新闻中心
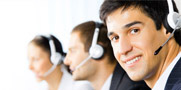
咨询热线:
134-0554-5577
邮件:874556408@qq.com
电话:0523-83984388
地址:江苏省兴化市沈伦镇工业园区沈北路
离心铸造_重力铸造是指金属液在地球重力作
铸造成型是制造复杂零件的灵活的方法。先进铸造技术的应用给制造工业带来了新的活力。为数众多的软件问世和计算机技术的迅猛发展使得为生产在几何形状、尺寸、使用性能等方面都符合要求的铸件提出确切可靠的信息成为可能。
汽车零件中大约有15%~20%为采用不同铸造方法生产的铸件,这些铸件主要为动力系统关键部件和重要的结构部件。目前汽车工业发达国家的汽车铸件生产技术先进,产品质量好,生产效率高,环境污染小。铸造原辅材料已形成系列化和标准化,整个生产过程已经实现了机械化、自动化和智能化。随着汽车技术的快速发展,采用快速制模技术、CAE技术、三维建模、数控技术等技术,为缩短铸件生产准周期和降低新产品开发的风险提供可靠的支持。
● 普通砂型铸造,利用砂作为铸模材料,又称砂铸,翻砂,包括湿砂型、干砂型和化学硬化砂型3类,但并非所有砂均可用以铸造。优点是成本较低,因为铸模所使用的沙可重复使用;缺点是铸模制作耗时,铸模本身不能被重复使用,须破坏后才能取得成品。
● 特种铸造,按造型材料又可分为以天然矿产砂石为主要造型材料的特种铸造(如熔模铸造、泥型铸造、壳型铸造、负压铸造、实型铸造、陶瓷型铸造等)和以金属为主要铸型材料的特种铸造(如金属型铸造、压力铸造、连续铸造、低压铸造、离心铸造等)两类。
重力铸造是指金属液在地球重力作用下注入铸型的工艺,也称重力浇铸。将融化的金属倒入模具中,融化的金属在重力的作用下占据了腔内的空间。如果零件必须是空心的,那么也需要在模腔中设置砂芯。有时,为了确保适当的金属流动,浇注装置可能会倾斜,而这种装置被称为“倾斜GDC”。广义的重力铸造又包括砂型浇铸、金属型浇铸、熔模铸造、消失模铸造,泥模铸造等,而其中,砂型铸造在汽车工业应用为广泛。
目前对于铸铁材质的汽车部件,应用广的仍然是湿砂造型,尤其是气流预紧实的静压或气冲造型的出现,体现出更多的优越性 – 能耗低、噪声小、污染少、效率高、运行可靠。
近来,国外设制造家对造型机又不断改进,先后出现气冲压实,气流增益气冲加压实,静压加压实、主动多触头压实、成型挤压压实等改进方式,使砂型硬度更加均匀化。
随着大功率半导体元器件及计算机,微电子技术的发展,采用电伺服系统代替造型线惯常所用的液压、气动驱动,使造型线节拍进一步加快,并且运行可靠性大大提高,同时明显地简化了液压控制系统,使维护保养工作量也相应减少。
造型线采用双筒式落砂机,则可使铸件和浇口在落砂的同时得到预清理。造型线的浇注往往制约全线的开动率,应采用自动浇注设。有的家采用气压浇包和接触式浇注工艺,有利于节约铁水,保证质量和保护砂箱,浇注过程中采用随流孕育的较多,有的采用型内孕育与过滤相结合。
铸造过程中,对于砂芯的采用,依各条件不同,分别采用冷芯盒制芯,热芯盒制芯或壳芯制芯外,其它的砂芯包括曲轴箱砂芯、缸筒与顶端砂芯、前后端面前砂芯等大多采用冷芯盒制芯,以保证尺寸精度和节能,冷芯盒应用越来越广泛。冷芯制芯以ISO CURE 三乙胺硬化法居多(美国又开发出更先进的ISO MAX)。
为提高铸件内表面质量和内腔清洁度,砂芯应涂料,用水基涂料取代醇基涂料有利于防污染。涂料后采用微波烘干效率高、节能,砂芯质量也比传统的用煤气、天燃气烘干好。采用KCY-CORE工艺,利用砂芯上开设的工艺孔,二次填砂固化,使多个砂芯为一个整体组合砂芯,然后整体涂料、烘干,这样铸件尺寸精度可大大提高,总体尺寸误差0.3mm。
在型砂系统中,有旧砂磁选设、砂块破碎设和筛分设及旧砂冷却设来保证回用旧砂的质量。同时对新砂、煤粉、膨润土等添加材料,准确定量,按工艺确定的比例给料,并根据实时控制的数据随时调整加水量,确保型砂性能。也有采用对全系统型砂的性能进行闭环实时控制或型砂质量计算机在线专家系统控制的。应注意,型砂系统的型砂周转量较大,惰性较强,型砂性能的调整应以趋势来判断,采用有预见性的调整措施,以保证型砂系统的质量稳定。
当所需铸件的截面相当复杂,或某些特定地方的壁厚非常薄时(如图3),仅在重力的影响下,无法保证金属液完全填满模腔。在这种情况下,金属液可在压力的作用下压入模腔,保证金属液能完全填满模腔,设置可以是高压压铸(HPDC)或低压压铸(LPDC)。采用HPDC工艺生产的铸件尺寸一致性好,公差相近,大约+/-0.2mm。这种精度在GDC甚至LPDC中都是无法企及的。随着汽车技术的快速发展,高压压铸技术也成为了当前汽车铸造的热点之一。
高压铸造是在高压作用下将液态或半液态金属快速压入铸型中,并在压力作用下结晶凝固而获得铸件的方法。高压铸造的主要工序可分为:合型、压射、顶出三个阶段。
在压铸过程中,压射参数对压铸件气孔的影响颇大,必须合理进行调整。采用闭合压射结束时间控制系统,可实现无飞边压铸。压铸件质量的检测可采用X光探伤、超声波测试等。
在高压铸造工艺基础上开发的真空铸造、充氧压铸,旨在消除铸件缺陷,提高内部质量,并扩大压铸件的应用范围。挤压铸造过程中,熔体在压力下充型和凝固,具有平稳、无金属喷溅、金属液氧化损失少、节能、操作安全和减少铸件孔洞类缺陷等优点,在铝合金副车架等高性能铝合金铸件的开发与应用方面获得了广泛的应用。
为了减少或避免压铸过程中气体随金属液高速卷入而使得铸件产生气孔和疏松,压铸前采用对铸型抽真空压铸为普遍。根据压室和型腔内的真空度大小又可将真空压铸分为普通真空压铸和高真空压铸。
高真空压铸的关键是能在很短的时间内获得高线为吸入式高真空压铸机的工作原理图,它采用真空吸入金属液至压室内,然后进行快速压射,可获得较高的压铸真空度。
高真空压铸的原理:压铸工作前,先从抽真空管将整个压室和型腔中的空气抽出,这个抽真空过程速度一定要尽可能快,使得坩埚中的金属液和压室产生较大的压力差,从而使得坩埚中的金属液体沿着升液管进入压室,接着压射冲头开始进行压射。
充氧压铸是将干燥的氧气充入压室和压铸模型腔内,以取代其中的空气和其他气体。充氧压铸工艺原理图如图7所示。
充氧压铸仅适用于铝合金。当铝合金液体压入压室和压铸模型腔时与氧气发生化合反应,生成AL2O3,形成均匀分布的AL2O3小颗粒(直径在1um以下),从而减少或消除了气孔,提高了铸件的致密性。这些小颗粒分散在铸件中,约占总质量的0.1%-0.2%,不影响机械加工。
汽车铸造业所用的设必须是快节拍、高效率、高可靠性的适应连续工作的设。由于轿车铸件的高质量要求,这些铸造设又必须是较高精度的。
主要的铸造设有:造型机,混砂机,制芯机,造型设,除尘设,熔炼炉,压铸机,机加设,抛丸机,清洗机,检测设等,其中对压铸机和熔炼炉进行介绍。
熔炼炉利用中频电源建立中频磁场,使铁磁材料内部产生感应涡流并发热,达到加热材料的目的。中频电炉采用 200-2500Hz中频电源进行感应加热,熔炼保温,熔炼炉主要用于熔炼碳钢,合金钢,特种钢,也可用于铜,铝等有色金属的熔炼和提温。设体积小,重量轻, 效率高,耗电少,熔化升温快,炉温易控制,生产效率高。
整套熔炼炉设包含中频电源柜,补偿电容,炉体(两个)及水冷电缆、减速机。炉体由炉壳、感应圈、炉衬、倾炉减速箱等四个部分组成,炉壳用非磁性材料制成,感应线圈是由矩形空心管制成的螺旋状筒体,熔炼时管内通冷却水。线圈引出铜排与水冷电缆连通,炉衬紧靠感应圈,由石英砂打实烧结而成,炉体的倾动由倾炉减速箱直接转动。倾炉减速箱系二级涡轮变速,自锁性能好,转动平稳可靠,出现紧急断电时看收工倾炉,避免危险。可以通过选炉开关对两台炉体的倾炉减速箱电动机的控制进行选择,带有四芯橡皮线的开关盒能使操作者站在合适位置对炉体的倾动,复位进行点动控制。
当前许多铸造工还停留在工业2.0状态,在环保,自动化,智能化及安全上面都急需得到改善。随着工业4.0的到来,通过传感器在高温的环境中工作,将熔炼中的所有参数记录下来,从加热炉的填充水平到熔池污染程度都将成为实现智能联网熔炼炉的基础数据。未来在一个熔炼炉工里,清洁工作可由一个机器人完成,机器人知道熔炉的所有参数,并能在污染达到临界线之前及时采取行动。
压铸机就是用于压力铸造的机器。包括热压室及冷压室两种。后都又分为直式和卧式两种类型。压铸机在压力作用下把熔融金属液压射到模具中冷却成型,开模后可以得到固体金属铸件。压铸机主要由合模机构、压射机构、液压系统和电力控制系统等各部分组成。除此之外,压铸机还有零部件及机座、其他装置、辅助装置等部分。
近三十年来, 压铸机在大型化,自动化,单元化和柔性化等方面的发展非常迅速。近的几年,汽车压铸的集成化,轻量化等高新技术又不断地对压铸机提出更高和更新的要求。其中车身一体成型技术作为当前的热点话题,把重吨型压铸机推向前沿。
近期特斯拉从意大利DRA又采购了一台8000吨级压铸机,比之前在Model Y上用的6000吨压铸机又重了30%,相信这个记录将会不断被刷新。在此,我们来分析一下,为什么说重型压铸机是未来的发展方向,它到底有哪些优势。
图9为特斯拉Model Y车架结构图,黄色部分是车身后部、后桥塔顶轮拱的一体化大型零件。有了大型压铸机的帮忙,这个本需要多工位,多工序的复杂零部件就可一气呵成。因此在成本上是有的优势。
特斯拉的目标是要做新能源界的丰田大众,那么生产节拍就变得异常重要。8000吨的压铸机为了提升节拍,在铸造零件压力密封过程中,通过某些技术能将两侧的铸造半膜之间形成空腔,并且向这个空腔中注入带有温度保护的熔融金属。由于这个空腔中是负压状态,能有效消除铸造湍流产生的气泡,在压铸时对于材料的一致性,和铸造速度非常有帮助。根据特斯拉公布的数据来看,每次铸造会将80公斤左右的铝合金液体,以每秒10米的速度注入冷室模具中,节拍为85秒左右,算下来每小时42件,算是优化了目前的节拍。
优势也伴随着一些不足的地方,比如,锻炼力学角度目前在该工艺之下仍有挑战,模具设计也具有很大的挑战。在发展大型压铸机的道路上,这都是我们未来要攻克的技术难题。
传统的汽车发动机缸体材料是铸铁,当今仍旧占据主导地位,但随着发动机性能的逐步提高和轻量化的需求,发动机缸体材料也在进行着快速革新。主要有三个方向:
● 采用蠕墨铸铁生产发动机缸体,具有高强度、疲劳性能好的优势,利于薄壁化设计的优点,可承受更大的爆发压力,减少缸筒变形,离心铸造功率提高10%~20%;
● 铝合金缸体,发展势头为迅速,代表乘用车缸体的重点发展方向。通常需镶套处理,质量明显减轻,汽车能耗降低。但受铝合金强度和热疲劳性能的限制,在大马力发动机缸体上还不能够满足要求,且成本也比较高。
发动机缸盖是铝合金应用的主要领域,尤其在乘用车缸盖市场,基本被铝合金材料所垄断。在载重车市场,大马力发动机缸盖也已很少使用铸铁,取而代之的是蠕墨铸铁缸盖,可以解决灰铸铁缸盖的使用开裂问题。
汽车发动机利于节能减排的重要性能升级工艺是发动机的增压技术应用,无论是汽油发动机还是柴油发动机,尤其在载重车市场,由于发动机爆发压力增大,致使以往采用的珠光体球铁曲轴的使用性能已不能满足要求,而转用40Cr等锻钢材料来制造。但随着珠光体球铁曲轴圆角滚压、感应淬火等技术的发展,球墨铸铁曲轴在乘用车和中低马力发动机载重车市场占有大量市场份额。此外,采用等温淬火球墨铸铁制造发动机曲轴在国内外也进行了较深入的应用研究。
其它汽车铸件如各类发动机、底盘的支撑件、结构件,如各类支架、盘体、壳体、转向零件等,依据使用性能需求,大量采用铸铁材料来制造。随着汽车环保要求的发展,灰铸铁、铸钢的应用比例逐步呈下降趋势,而高性能球墨铸铁、Mg合金、Al合金及特种铸铁材料呈进一步增加的趋势。
以铸铁件为代表的铸件目前是汽车用铸件的主体部分,尤其是球墨铸铁件的应用取代了很多铸钢和灰铸铁件,并导致可锻铸铁在汽车零部件应用上基本接近消失,其优异的强韧性能和易控的生产方式使其应用比重逐步增加,高强高韧性球墨铸铁的研发生产将成为球铁持续应用的重要基础。
另一种优异的工程材料——等温淬火球墨铸铁具有优异的力学性能,在国外取得迅速发展并应用良好,在曲轴、齿轮、支架、结构件等方面的应用研究取得可喜成果,并得到实际应用。
蠕墨铸铁自1948年发明以来,由于稳定的生产范围较窄,且性能未引起人们的关注,应用一直较少。直至先进的生产控制技术研究成功并有效地投人使用,蠕墨铸铁用于复杂铸件的生产才有了可能。蠕墨铸铁材料由于具有比铸铁和Al更高的抗拉强度(高75%) 、弹性模量(高40%) 和疲劳强度(高100%) ,成为目前发动机缸体缸盖设计的理想材料。
汽车轻量化的要求是采用Mg、Al合金来制造汽车铸件。汽车每减重10%,油耗降低5.5%,排放减低10%左右,而Al合金密度仅为Fe的1/3,而强度与灰铸铁相当,离心铸造成为取代灰铸铁制造发动机缸体缸盖的理想材料。Al合金铸件在世界范围内近年来取得快速增长,而具有更轻密度的Mg合金伴随研究应用的深入,在汽车方向盘、座椅骨架、仪表盘、罩盖等零件上也得到快速应用。
随着汽车节能环保以及降低生产成本的要求不断增加,充分利用铸造成形的优势,将原有冲压、焊接、锻造和铸造成形的数个零件,通过合理的设计以及结构优化,实现集成零件的铸造成形,可以有效地降低零件的重量和减少不必要的加工工艺过程,从而实现零件的轻量化和高性能化。
汽车铸件集成化的发展趋势在有色合金铸件方面的发展更为明显。为了充分利用铸造工艺能够实现复杂结构铸件生产的特点,出现了集成设计的车门内板、座椅骨架、仪表板骨架、前端框架和防火墙等集成设计的高压铸件,其尺寸显著大于目前生产的铸件,需要4 000~5000t甚至更大吨位的压铸机进行生产。
在保证汽车的强度和安全性能的前提下,尽可能地降低汽车的整重量,实现轻量化,从而提高汽车的动力性,减少燃料消耗,降低排气污染。汽车整重量每减少100kg,百公里油耗可降低0.3~0.6L,若汽车整车重量降低10%,燃油效率可提高6%~8%。随着环保和节能的需要,汽车的轻量化已经成为世界汽车发展的潮流,汽车铸件的轻量化也成为汽车铸件的重要发展方向之一。轻量化的实现主要会从以下三点进行发展:
等厚设计的主要弊端是无法充分发挥结构性能,并导致铸件重量的增加。采用CAE分析、拓扑优化等手段,对零部件进行优化设计,使零部件各个部位的应力值接近,即各个部位的壁厚不一致,受力小的部位减薄料厚,从而减轻零件的重量。考虑到铸造成形可以实现复杂结构铸件的成形,可以实现各种不规则的异型截面。设计时,采用CAE或拓扑优化等手段,对零部件进行应力分析。根据力的分布,确定零部件的形状和具体局部的材料厚度。通过对铸件加筋、挖孔和改变截面,可使零部件的重量大大降低。
使用铝镁等轻合金材料是目前各国汽车制造商的主要减重措施。铝的密度仅为钢的1/3,且有优良的耐蚀性和延展性。镁的密度更小,只有铝的2/3,在高压铸造条件流动性优异。铝和镁的比强度 (强度与质量之比) 都相当高,对减轻自重,提高燃油效率有举足轻重的作用。
但是需要注意的是由于铝镁等轻合金的原材料价格要远远高于钢铁材料,限制了其在汽车工业中更广泛的应用。但是尽管原材料价格较高,目前镁、铝铸件的单车用量却连年上升。这一方面是通过技术进步弥补了成本增加,另一方面则是市场竞争迫使汽车商降低利润而采用更多的轻合金。然而,要使轻合金用量得到大幅度提高,降低镁铝锭的采购价格,开发先进成形技术是关键之一。
提高材料的性能,使得单位重量的零件能够承受更高的载荷,是有效降低铸件重量的方法之一。支架类结构铸件占汽车铸件相当大的比例,因而其铸件的开发也成为关注的重点之一。通过热处理等措施,使材料显微组织改变,从而提高零件的强度、刚度或韧性,可以有效地降低零件重量。
等温淬火球墨铸铁,不仅强度比普通铸钢材料有所提高,而且密度比钢要低,其密度为7.1g/cm3 ,而铸钢的密度为7.8g/cm3 ,是近年来广泛推荐采用的材料。采用等温淬火球墨铸铁,在铸件尺寸相同的条件下,比铸钢件轻10%。
在铝合金和镁合金铸件方面也采用了高强、高韧的材料进行替代,在原有轻合金减重的基础上,应用高性能材料进行进一步减重,美国通用汽车采用高性能的AE44合金取代原有的铝合金,采用高压铸造的方法生产副车架,在铝合金减重的基础上进一步减重6 kg。
汽车铸件开发与数字技术的全面结合可以显著地提升铸造技术水平,缩短产品的设计和试制周期。目前数字制造技术已经广泛应用于汽车铸件的开发。在铸件结构设计及铸造工艺设计阶段,Pro/E,CATIA,和UG等三维设计软件已经获得了广泛的应用,部分先进的铸造企业已经实现了无纸化设计。MAGMA,ProCAST以及华铸CAE等软件已经被广泛用于汽车铸件凝固过程、显微组织、成分偏析和材质性能等方面的模拟,还可以对铸造过程中的速度场、浓度场、温度场、相场、应力场等方面的模拟,能够确保在批量生产前使工艺方案得到优化。
为适应汽车铸件快速开发的需求,在CAD/CAE的设计与开发的基础上,RP (快速原型技术) 已经被广泛用于汽车铸件的快速试制。在获得CAD/CAE原始数据后,离心铸造采用逐层堆积的方法,通过粘结,熔结或烧结的方式获得铸件原型或形成铸件所需模具的原型。前者可用熔模铸造,石膏型铸造等方法试制铸件样件,后者可直接作为模具制造砂芯,通过组芯造型而浇注出铸件。此外,还可以用粉料激光烧结法(SLS),直接完成砂芯和砂型的制作,从而获得铸件试制所需要的砂型。对于结构相对简单的外模,还可以采用数控机床,用可加工塑料进行CAM加工,从而获得铸件试制所需的芯盒和模样,或是直接对砂块进行加工,直接获得外模的砂型。
总体上说,数字化技术已经贯穿铸件的设计、开发以及试制的各个环节,有效提高了铸件的开发速度和效率。目前主要存在的问题是设计、分析和快速制造等方面的数字化技术各自独立,当开发过程由一个阶段向另一个阶段转化时,还需要进行相当繁琐的数据转换工作。希望在将来能够针对铸件开发各个环节所应用的数字化技术开发出统一的数据接口平台,建立标准化的数据转换标准,实现不同软件之间数据的无缝转换,从而更进一步地提高铸件的开发速度。
随着汽车工业的发展和节能减排的需求,汽车零件日趋轻量化,通过薄壁化设计,实现轻量化是发动机缸体的重要发展方向。
针对缸体3mm薄壁特点,组芯立浇工艺对制芯和组芯都提出了苛刻的要求。制芯中心可实现制芯生产的高度智能化、自动化。从原砂、树脂的加入,混砂、制芯、修芯、组装、涂料和烘干到造型以及组下芯全过程均可以实现高度自动化,使砂芯制芯质量、组装质量即尺寸精度和涂料烘干质量等得到了稳定的保证,从而避免了因人为因素而造成的质量和尺寸风险,适应大批量汽缸体制芯生产的需要。能够有效解决大批量生产时,废品率不稳定和居高不下的问题,同时由于砂芯尺寸精度的提高,也极大地降低了清理工作量和成本,并且完全能够有效保证3mm壁厚尺寸要求。
随着节能、环保以及降低部件成本的要求不断增加,铝镁合金大型结构铸件已经成为重要的发展趋势,其制造技术也成为目前的开发热点。目前铝镁合金大型结构件的主要生产技术有高压铸造、挤压铸造和低压铸造。由于高压铸造生产效率高,产品质量好已经成为目前主要的生产工艺,其制造技术的开发主要集中在对高压铸造过程中容易卷气,铸件内部容易形成气孔,不能进行热处理问题的改进。
上文介绍的高真空压铸可有效解决卷气问题,防止气孔的产生。真空压铸工艺已经成功地应用于汽车结构铸件的批量生产,为高质量的轻合金铸件的应用提供了先进的成形方法与工艺。
随着汽车铸件成形技术的发展,铸造成形是指一类铸造成形方法。通过这一类成形方法生产出的铸件无需经过切削或是少切削即可直接使用。随着对铸件尺寸精度要求的提高,铸造成形技术近年来得到了迅速发展,出现了砂型铸造,消失模铸造、可控压力铸造、压力铸造等一系列的铸造成形方法。
在高压铸造工艺基础上开发的真空铸造、充氧压铸、半固态金属流变或触变压铸等工艺方法,旨在消除铸件缺陷,提高内部质量,并扩大压铸件的应用范围。挤压铸造过程中,熔体在压力下充型和凝固,具有平稳、无金属喷溅、金属液氧化损失少、节能、操作安全和减少铸件孔洞类缺陷等优点,在铝合金副车架等高性能铝合金铸件的开发与应用方面获得了广泛的应用。
汽车产量的不断增长迫切要求铸造生产向高质量、优性能、近净形、多品种、低消耗、低成本的方向发展。由于一辆整车约15%~20%的零件是铸件。这就要求铸造行业要不断应用各种新技术、新材料来提升铸造整体水平。铸件铸造成形技术能够满足汽车铸件的上述要求,其应用也将涵盖汽车铸件的不同铸造生产过程中。
免责声明:如涉及作品版权问题,请与我们联系,我们将在时间协商版权问题或删除内容!内容仅代表作者个人观点,并不代表本公众号赞同其观点和对其真实性负责!
声明:本文由入驻搜狐公众平台的作者撰写,除搜狐官方账号外,观点仅代表作者本人,不代表搜狐立场。
以上信息由江苏亚立特钢有限公司整理编辑,了解更多离心铸造信息请访问http://www.jsyltg.com