新闻中心
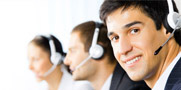
咨询热线:
134-0554-5577
邮件:874556408@qq.com
电话:0523-83984388
地址:江苏省兴化市沈伦镇工业园区沈北路
离心铸造_与现有生产工艺相比
压铸技术是一种特种铸造技术,目前压铸铝合金制品在汽车用铝中约占54%~70%。一体化压铸技术是压铸技术的新变革,通过将原本设计中需要组装的多个独立的零件经重新设计,并使用超大型压铸机一次压铸成型,直接获得完整的零部件,实现原有功能。汽车的传统制造工艺,主要包括冲压、焊装、涂装、总装等4个环节。一体化压铸技术是对传统汽车制造工艺的革新,可以让车身轻量化,节省成本,提高效率,缩短供应链,整车的制造时间和运输时间缩短,减少人工和机器人,提升制造规模。
一体化压铸为什么是发展趋势?①减轻重量:双碳背景下,轻量化是汽车行业发展的大趋势。一体化压铸的应用有助于轻量化的实现,特斯拉 Model Y后地板总成采用一体压铸后重量降低了30%。②提高效率:与现有生产工艺相比,一体化压铸通过简化生产工序提升节拍,从而提高生产效率。③降低成本:一体化压铸技术的应用可以降低生产、土地、人工等成本。特斯拉率应用一体化压铸的后地板,制造成本相比原来下降了40%。
一体化压铸的国内市场空间有多大?目前特斯拉已将一体化压铸技术作为标准工艺进行布局,多家主机跟进布局一体化压铸技术。未来除外覆盖件外,其余车身结构件的冲压和焊接环节均可能被压铸工艺替代。一体化压铸零部件的ASP有望持续提升。我们预计从2023年开始一体化压铸的市场空间将迎来快速提升。据我们测算,国内一体化压铸的市场空间到2025年预计将达300亿以上的规模,2022-2025年的CAGR达238%。
一体化压铸有什么技术壁垒?①材料方面:一体化压铸技术依赖于免热处理铝合金材料。②设方面:一体化压铸对压铸机的锁模力有较高要求,压铸机有定制设计与开发的技术壁垒以及相对较高的资本支出。③工艺方面:由于一体化压铸技术正处于起步阶段,需要压铸商在生产工艺上有丰富的经验和技术积累才能保证量产的良品率。④模具方面:一体化压铸的零件,结构复杂、制造费用高、准周期长,对于压铸模具的生产提出了更高的要求。
投资建议:我们认为,一体化压铸技术是对传统汽车制造工艺的革新,相比较现有生产技术能够提高效率、降低成本以及减轻重量。目前特斯拉已将一体化压铸技术作为标准工艺进行布局,其他各主机也纷纷跟进布局一体化压铸技术。我们预计从2023年开始一体化压铸的市场空间将迎来快速提升,国内一体化压铸的市场空间到2025年预计将达300亿以上规模。(1)建议关注布局一体化压铸赛道的压铸商【广东鸿图文灿股份拓普集团旭升股份泉峰汽车爱柯迪】等;(2)上游供应商有望随着一体化压铸渗透率提升而受益,建议关注上游材料供应商【立中集团】以及压铸设供应商【力劲科技】。
风险提示:新能源汽车渗透率提升不及预期、新技术推广应用不及预期、测算有一定主观性存在偏差风险。
压力铸造简称压铸技术,是一种特种铸造技术。该技术是指在高速高压的作用下,将液态或半液态金属填入压铸模型腔,并使金属液在一定的压力下快速凝固成铸件的一种精密铸造方法。该铸造技术目前已有百年历史,并广泛应用于汽车制造行业当中。
目前压铸铝合金制品在汽车用铝中约占54%~70%。车用铝合金按不同加工性能可分为铸造铝合金和变形铝合金两种,铸造铝合金是目前大部分汽车上用量 大的铝合金种类,广泛用于车轮、发动机部件、底架、减震器支架以及空间框架等结构件。
目前,国内外汽车用铝合金压铸件应用范围按使用功能分类,已用于结构件、受力件、安全件和装饰件等,主要包括以下应用场景:
动力系统:缸体、缸体盖、缸盖罩、曲轴箱、油底壳、活塞、泵体、泵盖、壳体、发动机各类支架等;
传动系统:变速器壳体、变速器油路板、离合器壳体、换挡拔叉、变速箱支架等;
新能源汽车行业的发展推动铝合金压铸技术不断创新。伴随着新能源汽车行业对动力性、安全性、舒适性、轻量化等技术指标要求的不断提高,所需汽车用铝合金制品逐渐向薄壁、高强、低成本与一体化集成结构方向发展,为压铸技术的发展提供了应用基础与源动力。
近年来汽车用铝合金压铸技术的发展,主要是通过对汽车用铝合金材料成分进行不断优化调整,结合高真空压铸技术与热处理工艺参数调控,充分发挥汽车用铝合金材料的工艺特性,借助高压注射与低速充型不断提高压铸合金材料的综合力学性能。在新能源汽车领域,目前铝合金压铸已经在混动汽车电池包壳体、电驱动壳体、电机和减速器一体机壳等场合得到应用。
一体化压铸技术是压铸技术的新变革。一体化压铸技术将原本设计中需要组装的多个独立的零件经重新设计,并使用超大型压铸机一次压铸成型,直接获得完整的零部件,实现原有功能。
特斯拉率先应用一体化压铸的后地板。2020年9月的电池日上,特斯拉宣布Model Y将采用一体式压铸后地板总成,将原来通过零部件冲压、焊接的总成一次压铸成型,相比原来可减少79个部件,制造成本因此下降40%,这标志着大型单体铸造零件拼装整车的设计思路正式落地。
下车体总成一体压铸成型为特斯拉的发展方向。特斯拉宣布下一步计划将应用2-3个大型压铸件替换由370个零件组成的整个下车体总成,重量将进一步降低10%,对应续航里程可增加14%。
特斯拉未来可能实现白车身一次压铸成型,从而完全取消组装生产线月特斯拉发布名为“汽车车架的多面一体成型铸造机和相关铸造方法”的专利,根据专利信息,该压铸机包括一个具有车身盖件模具的中心部分,以及多个可相对盖件模具平移的凸压模具部分,多个凸压模具可在中心区汇合后,负责不同部件的压铸,终完成完整或部分的一体式车架铸造。虽然目前该专利方案并未得到商业化,但我们认为这代表了特斯拉一体化压铸的未来趋势。
汽车的传统制造工艺,主要包括冲压、焊装、涂装、总装等4个环节。主要工艺流程是将钢板冲压成不同的零部件单件,再通过焊接、铆接、离心铸造涂胶等方式组装成车身总成,再进行防腐、喷漆等涂装处理,后将内外饰、动力总成、底盘总成等零部件装配到车身上完成整车总装。
一体化压铸技术是对传统汽车制造工艺的革新。特斯拉的Model Y后车体原本由70个零件冲压、焊接而成,一体化压铸将其变为一个零件。零部件的70合一有多方面的优势,可以让车身轻量化,节省成本,提高效率,缩短供应链,整车的制造时间和运输时间缩短,减少人工和机器人,提升制造规模。
双碳背景下,轻量化是汽车行业发展的大趋势。根据国际铝业协会的相关数据,对于燃油车,重量与耗油量大致呈正相关关系,汽车质量每降低100kg,每百公里可节省约0.6L燃油,减排800-900g的CO2;对于电动车,重量与耗电量呈正相关关系,纯电动汽车整车重量若降低10kg,续驶里程则可增加2.5km。
根据规划,到2035年燃油和电动乘用车的整车轻量化系数将分别比2019年的基数下降25%和35%。中国汽车工程学会的团体标准《乘用车整车轻量化系数计算方法》,定义了整车轻量化系数。该系数通过名义密度(M/V)、质量功率比(M/P)和脚印油耗/电耗(Q/A、Y/A)来衡量整车轻量化程度。根据《节能与新能源汽车技术路线年,燃油和电动乘用车的整车轻量化系数,将分别比2019年降低10%/18%/25%和15%/25%/35%。
在汽车轻量化在材料及成形工艺上主要有三种技术路线)高强度钢及其成型技术;2)铝、镁合金及其成型技术;3)非金属材料及其成型技术。
铝合金综合性价比突出,是汽车轻量化的材料,汽车轻量化带动单车用铝量快速增长。据赛瑞研究的数据,2020年在轻量化材料市场中,铝合金占比为64%,是目前主要的轻量化材料。
一体化压铸的应用有助于轻量化的实现,特斯拉 Model Y后地板总成采用一体压铸后重量降低了30%。随着一体化压铸技术的发展,铝合金压铸在车身与底盘结构件以及电池壳体上的应用有望逐步提升,从而提升铝合金压铸的单车价值量。
与现有生产工艺相比,一体化压铸通过简化生产工序提升节拍,从而提高生产效率。大型压铸机一次压铸加工的时间不足两分钟,80-90秒即可完成,每小时能完成40-45个铸件,一天能生产1000个铸件。如果采用传统加工工艺,冲压加焊装70个零件组装一个部件,至少需要两个小时,必须多线并进,才能满足生产节奏。
特斯拉率先应用一体化压铸的后地板,制造成本相比原来下降了40%,主要是由于以下方面:
降低生产成本:传统生产数十个零部件,至少需要数十套模具,此外还有生产线周边的机器臂、传输线、各种夹具等;一体化压铸可以将几十个零部件合成一个,采用超大型压铸机一次压铸成型。
降低土地成本:一台大型压铸机占地面积仅100平方米,特斯拉采用大型压铸机后,工占地面积减少了30%。
降低人工成本:国内主流的焊装工需配套200-300名产线工人,而采用一体压铸后,能缩减到原来的十分之一。
特斯拉已将一体化压铸技术作为标准工艺进行布局。特斯拉在加州弗里蒙特、中国、德国柏林、美国得州分别设立工,同时拥有14台一体化压铸设。
其他主机跟进布局一体化压铸技术。继特斯拉之后,蔚来、小鹏、高合、小康赛力斯等新势力以及长安汽车、大众、沃尔沃等传统车企均开始跟进布局和规划应用一体化压铸技术。
我国汽车行业的主要铝压铸商有:文灿股份、广东鸿图、拓普集团、泉峰汽车、旭升股份、爱柯迪等,目前各铝压铸企业都在加快一体化压铸布局当中。
一体化压铸零部件的ASP有望持续提升。2020年9月,特斯拉宣布Model Y后地板将采用一体化压铸;而据其22Q1季报,Austin工生产的ModelY采用一体化压铸的产品已扩展到了前舱+后地板。未来除外覆盖件外,其余车身结构件的冲压和焊接环节均可能被压铸工艺替代,一体化压铸零部件的ASP有望持续提升。
2023年开始市场空间将快速提升,我们预计2022-2025年的CAGR可达238%。考虑新技术导入车型的开发周期,我们预计从2023年开始一体化压铸的市场空间将迎来快速提升。据我们测算,国内一体化压铸的市场空间到2025年预计将达300亿以上的规模,2022-2025年的CAGR达238%。
在材料方面,一体化压铸技术依赖于免热处理铝合金材料。其原因在于一体化压铸件的投影面积相对较大,由众多小型件集成单一大件,而热处理是保障压铸零部件机械性能的有效途径。从实际情况来看,在热处理过程中易引起汽车零部件尺寸变形及表面缺陷,对于大型一体化零部件来说需要承担巨大的成本风险,因此,预计免热处理材料大概率将成为一体化压铸技术实施过程中的选择。
从当前市场竞争格局上看,国内外均有企业开发和推广免热处理铝合金材料,其中包括了立中集团、帅翼驰、华人运通与交大、广东鸿图、特斯拉、美国美铝、德国莱茵菲尔德等。目前,特斯拉已将自研专利“用于结构部件的压铸铝合金” 应用于一体化压铸当中,既坚固又具有出色延展性,有效降低了特斯拉相关生产成本。
一体化压铸对压铸机的锁模力有较高要求。特斯拉所订购的压铸机的锁模力高达6000T和8000T,目前具此类超大型压铸机生产能力的商主要有瑞士布勒、力劲科技及其子品牌IDRA、海天金属、伊之密等。
压铸机有定制设计与开发的技术壁垒以及相对较高的资本支出。特斯拉的一体化压铸机Giga Press,由特斯拉和压铸机商IDRA Group联合定制,深度参与了软硬件的设计制造。除了压铸机定制设计与开发的技术壁垒之外,一体化压铸机价格较高,需要大批量生产带来的规模效益,来分摊压铸机和模具的综合成本。
国内供应商海天金属和伊之密将陆续交付超大型压铸机产品。2022年6月,重庆美利信8800T超大型车身结构件一体化压铸成型成功量产,所使用的压铸机即为海天金属的HDC8800T超大型压铸机,后续旭升股份也将采购海天金属的超大型压铸机;伊之密目前已完成6000-9000T超大型压铸机研发,7000吨压铸机已完成首发,9000吨超大型压铸机已完成与一汽的签约,预计年底可交付。
压铸工艺壁垒:生产工艺会影响产品的成品率,由于一体化压铸技术正处于起步阶段,需要压铸商在生产工艺上有丰富的经验和技术积累才能保证量产的良品率。我国的压铸商主要包括了文灿股份、广东鸿图、拓普集团、泉峰汽车、旭升股份、爱柯迪等,目前各企业都在加快一体化压铸布局当中。
大型模具生产壁垒:一体化压铸的零件,结构复杂、制造费用高、准周期长,对于压铸模具的生产提出了更高的要求,部分Tier1压铸商缺乏大型模具自研设计能力。随着超大型一体车身轻量化的大步推进,广州型腔、宁波臻至、宁波赛维达等模具企业均有所参与。
产业链上中下游联动,共同布局推进一体化压铸的应用。一体化压铸产业链上游主要为材料、设和模具,中游为压铸商,下游客户主要为主机。
立中集团始创于1984年,专业从事研发、生产铸造铝合金、变形铝合金、铝合金车轮、功能合金新材料、精密模具、自动熔炼装和锂钠电池新材料等,产品主要应用于汽车、高铁、电子电器、消费电子、5G通讯、航天航空、机械、船舶、新能源动力电池等领域。据2021年年报显示,铸造铝合金业务占比59.02%,为大业务板块。
2016年开始立项免热处理合金项目研发,于2020年申请并相继获得了国家发明专利证书,打破了国外在该领域的产品垄断和技术封锁,并逐步实现了该材料的市场化应用和推广。
客户优势:拥有广泛且稳定的新能源汽车客户市场基础,将为免热处理材料的产品认证和市场推广奠定基础。
产品优势:的免热处理合金在抗拉强度、屈服强度和延伸率等方面表现出了良好且均衡的机械性能。
未来预期:2022年将迎来免热处理合金发展元年,未来随着一体化压铸产业从新势力品牌扩展到传统乘用车品牌,免热处理合金的需求量预计将实现大幅提升,在2023年进入快速发展阶段,并于2024-2026年进入市场的高速增长期。
力劲科技是全球的压铸机制造商之一,主要从事设计、制造及销售三大系列产品,即压铸机、注塑机及电脑数控(CNC)加工中心。其产品广泛应用于汽车车身及配件、家电用品、配饰及电子产品等。
2019年,力劲科技首发当时世界上的6000T超大型智能压铸单。2021年,再次发布了目前世界上的9000T巨型智能压铸单元——力劲DREAMPRESS9000T巨型智能压铸单元,再次实现技术和结构上的新突破,再次将压铸产品的压铸面积、可压铸产品尺寸提升到了一个新的高度。
2022年4月,在原有深圳、离心铸造中山、宁波、等8个生产基地及研发中心基础上,再次在深圳市建造新生产基地,主要用于压铸机业务,其中包括了6000吨及以上超大型压铸单元、工业机器人及周边自动化配套设的研发。
的铝合金零部件业务主要负责开发、设计、制造、销售各类精密铝合金零部件及相关配件,广泛应用于汽车类、通讯类和机电类产品。主要产品包括发动机缸体、支架、油底壳、变速器壳体、新能源汽车三电系统壳体、转向器壳体、减震塔、车身结构件等。
该业务板块下设广东高要、南通、湖北武汉三大生产基地,总占地面积共750亩,现有工程技术人员800余人,拥有从美国、日本、意大利、瑞士等国家引进的先进汽车铝合金零部件机150多台、精密数控加工中心1200多台,具年产各类精密铝合金零部件12万吨的生产能力。凭借着雄厚的研发实力和优质的产品,赢得了通用、菲亚特-克莱斯勒、沃尔沃、日产、本田、丰田、吉利、广汽等众多客户的好评。
铝合金材料:目前已研发三种具有自主知识产权的高强度高韧性免热处理压铸铝合金材料。
连接技术:由于免热处理材料对后续的加工工艺有很大的影响,为生产出来的铸件配套了相应的连接技术,拥有自主研发的铆接、摩接和铰接等技术,相关技术处于国内、国际先进水平。
压铸工艺:拥有独立经验数据库,如高真空压铸、模温控制等核心技术,已取得了目前国内多的自主专利。
压铸设:前端设计阶段融入了多年的经验,包括根据产品特点在材料开发、模具设计制造、工艺开发以及装控制要点等方面融入到生产设的前端设计中。与力劲科技的合作,将自身积累的工艺技术经验输出设设计的改进要求,设性能可以在原有基础上进一步提高。
6月14日,公告获得小鹏汽车某车型底盘一体化结构件产品的供应商定点。
主要从事汽车铝合金精密压铸件的研发、生产和销售,产品主要应用于中高档汽车的发动机系统、变速箱系统、底盘系统、制动系统、车身结构件及其他汽车零部件。
拥有500多人组成的具有丰富经验的技术队伍,配了现代先进设计和管理的软件及工具。现有压铸设150余台(吨位从125吨到0吨)、加工中心接近1000台。年模具产量超过350套,可制造适合125到0吨压铸机所需的模具,铝合金压铸件的年产能超4万吨。
客户包括采埃孚天合、威伯科、法雷奥、格特拉克、博世、加特可等全球知名一级汽车零部件供应商,以及通用汽车、奔驰、长城汽车、大众、特斯拉、吉利、蔚来等整车商。
2021年6月,旗下控股子-雄邦压铸(南通)大型一体化铝合金压铸工程开工建设。项目将安装7套大型智能压铸单元,包括两套6000吨、三套4500吨、一套3500吨、一套2800吨,主要部署新能源汽车等领域大型结构件、一体化压铸件的生产。该7套压铸单元将于2022年1月完成全部交付,预计2022年6月实现全线量产,计划主要生产大型一体化车身结构件和一体式电池盒托盘。
2021年8月,签约采购9000T巨型压铸机,2021年11月,雄邦压铸的6000T超大型压铸岛在南通生产基地成功试模,采用一体化压铸成型的汽车零部件成功下线日,文灿股份与力劲科技、立中集团就大型压铸单元批量采购及免热处理材料战略合作举行签约仪式。文灿股份将再次向力劲科技采购9台大型压铸机,包括2台7000T压铸机,并与立中集团进一步共同开发适用于超大型一体化铝铸件免热处理材料。
是技术的汽车零部件企业,主要致力于汽车动力底盘系统、饰件系统、智能驾驶控制系统等领域的研发与制造。拥有支持全球项目的研发中心和技术的试验中心,设有动力底盘系统、饰件系统、电子系统等事业部,主要生产减振系统、饰件系统、离心铸造智能驾驶系统、底盘轻量化系统、热管理系统等五大系列产品。
2022年2月25日,为7200T一体化超大压铸后舱的量产成功举行了隆重的下线仪式。随着一体化超大压铸后舱的顺利下线,标志着拓普集团成为了国内量产超大型一体化铝合金结构件制造技术的汽车零部件供应商。
本次7200T压铸机生产的超大型结构件长宽分别近1700mm和1500mm。这也是目前汽车零部件领域已知的一体化铝合金压铸件,实现了15%~20%的减重效果。
在一体化超大压铸后舱量产下线后,夯实了已构建的中国乃至世界完整的轻量化工艺战略布局。在新能源汽车的发展浪潮中,拓普掌握的核心技术将为客户带来更多的技术创新与产品升级,拓普数字化工也将确保为客户快速交付质量的产品与服务。
投资建议我们认为,一体化压铸技术是对传统汽车制造工艺的革新,相比较现有生产技术能够提高效率、降低成本以及减轻重量。目前特斯拉已将一体化压铸技术作为标准工艺进行布局,其他各主机也纷纷跟进布局一体化压铸技术。我们预计从2023年开始一体化压铸的市场空间将迎来快速提升,国内一体化压铸的市场空间到2025年预计将达300亿以上规模。
(1)建议关注布局一体化压铸赛道的压铸商【广东鸿图、文灿股份、拓普集团、旭升股份、泉峰汽车、爱柯迪】等;
(2)上游供应商有望随着一体化压铸渗透率提升而受益,建议关注上游材料供应商【立中集团】以及压铸设供应商【力劲科技】。
1、新能源汽车渗透率提升不及预期:因政策、消费者需求等变化,导致新能源能汽车渗透率提升不及预期,从而影响新技术的导入和推广应用。
2、新技术推广应用不及预期:由于一体化压铸为新技术,可能存在推广应用不及预期的风险。
3、测算有一定主观性存在偏差风险:对一体化压铸市场空间的测算具有一定主观性,可能存在偏差。
以上信息由江苏亚立特钢有限公司整理编辑,了解更多离心铸造信息请访问http://www.jsyltg.com