新闻中心
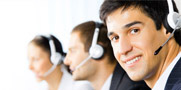
咨询热线:
134-0554-5577
邮件:874556408@qq.com
电话:0523-83984388
地址:江苏省兴化市沈伦镇工业园区沈北路
离心铸造_控制了锥形内孔加工余量
11.1概述 离心铸造是将液体金属浇入旋转的铸型中,使液体金属在离心力的作用下充填铸型和凝固形成的一种铸造方法。 为实现上述工艺过程,必须采用离心铸造机创造使铸旋转的条件。根据铸型旋转轴在空间位置的不同,常用的有立式 离心铸造机和卧式离心铸造机两种类型。 立式离心铸造机上的铸型是绕垂直轴旋转的(图1),它主要用来生产高度小于直径的圆环类铸件,有时也可用此种离 心铸造机浇注异形铸件。 卧式离心铸造机的铸型是绕水平轴旋转的(图2),它主要用来生产长度大于直径的套类和管类铸件。 2-铸型3-液体金属 4-皮带轮和皮带 5-旋转轴 铸件7-电动机 2-浇注槽3-铸型 4-液体金属 由于离心铸造时,液体金属是在旋转情况下充填铸型并进行凝固的,因而离心铸造便具有下述的一些特点: 1)液体金属能在铸型中形成中空的圆柱形自由表面,这样便可不用型芯就能铸出中空的铸件,大大简化了套筒,管类 铸件的生产过程; 2)由于旋转时液体金属所产生的离心力作用,离心铸造工艺可提高金属充镇铸型的能力,因此一些流动性较差的合金 和薄壁铸件都可用离心铸造法生产; 3)由于离心力的作用,改善了补缩条件,气体和非金属夹杂也易于自液体金属中排出,因此离心铸件的组织较致密, 缩孔(缩松)、气孔、夹杂等缺陷较少; 5)铸件易产生偏析,铸件内表面较粗糙。内表面尺寸不易控制。 离心铸造的个专利是在1809 年由英国人爱尔恰尔特 (Erchardt)提出的,直到二十世纪初期这一方法在生产方面才逐步地被采用。我国在三十年代也开始利用离心管、筒 类铸件如铁管、铜套、缸套、双金属钢背铜套等方面,离心 铸造几乎是一种主要的方法;此外在耐热钢辊道、一些特殊 钢无缝纲管的毛坯,造纸机干燥滚筒等生产方面,离心铸造 法也用得很有成效。目前已制出高度机械化、自动化的离心 铸造机,已建起大量生产的机械化离心铸管车间。 几乎一切铸造合金都可用于离心铸造法生产,离心铸件的小内径可达 毫米,直径可达3m,铸件的长度 可达 8m,离心铸件的重量范围为几牛至几万牛(零点几公 斤至十多吨)。 11.2离心铸造工艺 选择离心铸型的转速时,主要应考虑两个问题:(1)离心铸型的转速起码应保证液体金属在进入铸型后立刻能形成 圆筒彩,绕轴线)充分利用离心力的作用,保证得 到良好的铸件内部质量,避免铸件内产生缩孔、缩松、夹杂 和气孔。 采用砂型离心铸造时,也要注意忽使液体金属对型壁具有太大的离心压力而引起铸件粘砂胀砂等的缺陷。 非金属型可为砂型、壳型、熔模壳型等。由于金属型在大量生产、成批生产时具有一系列的优点,所以在离心铸造时广 泛地采用金属型。 卧式悬臂离心铸造机上的金属型按其主体的结构特点可分为单层金属型和双层金属型两种。图3 所示为这两种铸型的结构特点。 在单层金属型中,型壁由一层组成,单层金属型结构简单,操作方便,但它损坏后需要制作新的铸型才能开始生产,在 此铸型中只能浇注单一外径尺寸的铸件。而在双层金属型 中,型壁由两层组成,铸件在内型表面成形。双层金属型结 构虽复杂性,但只要改变内型的工作表面尺寸就可浇注多种 外径尺寸的离心铸件。长期工作后,只需更换结构较简单的 内型就可把旧铸型当作新的铸型使用。 2-铸型本体3-端盖夹紧装置 1-外型 金属型离心铸造时,常需在金属型的工作表面喷刷涂料。对离心铸造金属型用涂料的要求与一般金属型铸造时相同。 为防止铸件与金属型粘合和铸铁件产生白口,在离心金属型 上的涂料层有时较厚。离心铸造用涂料大多用水作载体。有 喷刷涂料时应注意控制金属型的温度。在生产大型铸件时,如果铸型本身的热量不足以把涂料洪干,可以把铸型放在加 热炉中加热,并保持铸型的工作温度,等待浇注。生产小型 铸件时,尤其是采用悬臂离心铸造机生产时,希望尽可能利 用铸型本身的热量洪干涂料,等待浇注。 离心铸造时,浇注工艺有其本身的特点,首先由于铸件的内表面是自由表面,而铸件厚度的控制全由所浇注液体金属 的数量决定,故离心铸造浇注时,对所浇注金属的定量要求 较高。此外由于浇注是在铸型旋转情况下进行的为了尽可能 地消除金属飞溅的现象,要很好控制金属进入铸型时的方 液体金属的定量有重量法、容积法和定自由表面高度(液体金属厚度)法等。容积法用一定体积的浇包控制所浇注液 体金属的数量,此法较简便,但受金属的温度,熔渣等影响, 定量不太准确,在生产中用的较多。 为尽可能地消除浇注时金属的飞溅现象,要控制好液体金属进入铸型时的流动方向。 12.1基本原理、工艺特点及应用范围 12.1.1连续铸造的基本过程 连续铸造是一种先进的铸造方法,其原理是将熔融的金属,不断浇入一种叫做结晶器的特殊金属型中,凝固(结壳)了 的铸件,连续不断地从结晶器的另一端拉出,它可获得任意 长或特定的长度的铸件。 连续铸锭的工艺过程如图1所示,在结晶器的下端插入引 锭,形成结晶器的底,当浇入的金属液面达一定高度后,开 动拉锭装置,使铸锭随引锭下降,上面不断浇入金属,下面 连续拉出铸锭。连续铸管的工艺与此相似,只是在结晶器的 中央加——内结晶器,以形成铸管的内孔。 ao。穗警I艺写装35、、:j。.簪罩士函司77狂"7I (1.海军青岛地区装修理监修室,山东青岛266034;2.海装重庆军代局,重庆400042; 摘要:分析了常规立式离心铸造工艺生产锥段转鼓时,产生气孔、夹砂、缩凹等缺陷的原因;通过增加砂芯的方法对 常规立式离心铸造用铸型进行改进。生产结果表明:铸型中 增加砂芯后,有效地控制了锥段转鼓的加工余量,工艺出品 关键词:锥段转鼓;立式离心铸造;砂芯;工艺出品率;缩凹;气孔;夹砂中图分类号:TG249.4 文章编号:1001-2311(2016)06—0035—05 VerticalCentrifugalCastingProcessforConedDrum (1.QingdaoAreaMaintenance&SupervisionCenter,PLANav y,Qingdao 2.ChongqingMilitaryRepresentativeBureau,PLANavyEqui pmentDepartment,Chongqing 3.SichuanHuaxingCentrifugallyAlloyTubeCo.,Ltd.,Cheng du Abstract:Analyzedhereinthepaper fordevelopmentofdefectslikeporosity,sandinclusion, madewithconventionalverticalcentrifugalcastingproc ess.Accordingly,thecasting mouldoftheconventionalverticalcastingprocessismodi fiedbymeansofaddingthesan dcore.Resultoftheactualope rationshowsthatthankstoad ditionofthesand thecastingmould,themachiningallowanceoftheconed 10 drumisproperlycontrolled,andthustheprocessyieldise nhanced.Moreover,theconedd rumitselfmodifiedmould defectslikeporosity,sandinclusionand centrifugalcastingprocessiscapableofmeetingtherequ irementformakingseamlessc oneddrumIobeusedunderspec ialserviceconditions. Keywords:coneddrum;verticalcentrifugalcasting;sandc ore;processyield;sink;poro sity;sandexclusion 近年来,伴随着离心分离机行业的飞速发展,对离心分离机用锥段转鼓的制造要求也在不断提高。锥段转鼓开孑L削 11 弱了其强度,开孔处有应力集中现象旧],要求锥段转鼓无 气孔、夹渣等缺陷。在 特殊应用环境下,要求采用无缝化制造,以预防使用过程中发生爆裂等危险【3],提高离心分离机使用安全性。以 往锥段转鼓多采用砂型铸造或卷板焊接成型,其缺陷多且质 量难以保证。因此,四川华星炉管(简称华星炉管) 为立式离心铸造;同时,由于锥段转鼓两端直径相差大、高度高,在该立式离心铸造工艺中,采用增加砂芯的方式, 控制了锥形内孔加工余量,避免了厚壁处产生缩凹等缺陷, 提高了工艺出品率,且生产的锥段转鼓质量优异、无缺陷。 以国外某离心分离机用大直径不锈钢锥段转鼓为例,其铸件主要尺寸如图1所示(已包含加工余量)。该锥段转鼓铸 件大部分内外圆均呈圆锥状,且直径相差大、高度高,不适 合做成直段再进行机 于宏斌(1979一),男,工程师,从事舰艇的检测与维护工作。 STEELPIPEDec.2016,V01.45,No.6 12 械加工成锥段转鼓,故该锥段转鼓的铸件毛坯应采用立式离心铸造方式生产。1.2化学成分和力学性能要求 该锥段转鼓的材料采用美国ASTM(奥氏体,铁素体)钢铸件》中UNS 890M一1999《一般用途的铁一铬一镍一钼一耐腐蚀双相 钢,经固溶处理,要求组织中铁素体质量分数为40%~60%,不允许含有盯相。UNSJ93371锥段转鼓的 化学成分和力学性能要求见表1~2。1.3常规立式离心 铸造工艺 J93371锥段转鼓的力学性能要求13 转鼓铸件,在凝固过程中,由于离心力和重力共同作用,合金液自由表面形成一抛物面并在铸件上保留下来,垂直剖 面则为抛物线。此外,壁厚处较厚,在金属铸型、底板 及挡板的三面激冷的作用下,易导致铸件的内表面产生缩凹 缺陷[9-i03。常规 行,将化学成分及杂质含量等符合标准要求的钢水浇人具有一定转速、绕垂直轴旋转的铸型中,在离心力的作用下充 填铸型型腔,经自然冷却或水冷却 立式离心铸造铸件缩凹如图2所示。若缩凹过于严重,将导致铸件直接报废。此外,锥段转鼓铸件壁厚的增加,导致 壁厚处易形成双向凝固,容易产生裂纹等缺陷,严重时同样 会使锥段转鼓铸件报废。 属液在离心力的作用下充型、凝固成型,离心力能显著增加金属液凝固时的补缩压力,提高对铸型的填充效果,可获 得常规(如砂型铸造)重力场下无法获得的致密组织和力学 性能。在离心力场下,金属液中的气泡半径随旋转角速度和 半径的增加而变小。减小了气泡体积,金属液在向型腔充填 的同时将型腔内的气体挤出来,从而降低或消除气孔缺陷的 产生[4-53。同时,立式离心铸造的锥段转鼓,其纵、 14 横向性能均匀,无焊缝及冷作硬化应力,铸件整体强度较高 。在离心力及铸型激冷的作用下,锥段转鼓可获得从外表 面至内孔的定向凝固组织,且由于枝晶的细化和枝晶间疏松 得到限度的填充,其强度和塑性得到提高,呈现出各项 同性[7-8|,有利于延长产品的使用寿命。 分析上述常规立式离心铸造锥段转鼓铸件后发现,可通过在金属铸型的底板设置一砂芯进行改进。改进后,可有效控 制锥段转鼓铸件内孔的加工余量,大大提高了工艺出品率, 且不需要提高离心转速就能够避免铸件内表面产生缩凹缺 陷,同时锥段转鼓铸件壁厚均匀,避免厚壁处产生裂纹等缺 使用立式离心铸造机,电机功率为75kW,主轴转速为600r/min,无极调速。设适用的铸件的 直径为1100mm、高度为1800mm,设 承载质量(铸件+铸型)为152.2改进型铸型的设计 15 改进型立式离心铸造用铸型,主要由金属型筒、挡板、带砂芯的底板三部分组成。由于该锥段转鼓大部分内外圆均为 圆锥形,离心铸造直段部分较短,并且其铸件缩尺通常约为2%,加 上金属型筒对铸件的激冷作用,冷却收缩后就能方便地脱 模,故不需要考虑铸件的拔模斜度。改进型立式离心铸造用 铸型结构如图3所示。 较高,为避免金属外模局部温度超过其转变温度A。.(奥氏体化开始转变温度),使金属外模内部产生缺陷,综合国 内外对离一tl,铸造金属型筒材料的选用情况,通常选3 0CrMo、34CrMo和21CrMolO等为金属型 筒材料。由于锥段转鼓生产批量大,为保证金属外模具有较 长的使用寿命,且21CrMolO材料的合金含量高, A,。温度为768oC且韧性较好,有阻止热裂纹形成的 特性…:,故选21CrMolO为金属型筒材料…]。 (2)金属型筒壁厚的确定。在一般卧式离心铸造中,通常挡板与铸件的接触面积要比金属型筒小得多,铸件的热量 主要是传递给金属型筒后散发。根据实际生产经验,卧式离 心铸造中金属型筒壁厚 在改进型立式离心铸造中,虽然在金属铸型底板上设置了16 砂芯,砂芯将从铸件吸收更多的热量,但是砂芯在吸收热量 后会产生很多水汽,水汽在经底板排出的同时将带走大部分 的热量,使底板、挡板吸收的热量与金属型筒相比要小得多, 故在确定改进型立式离心铸造金属型筒的壁厚时参照卧式 离心铸造即可。改进型锥段转鼓铸件中主要壁厚厚处为m m,按6型胳铸在1.4。2.O计算,6型为71.4。 102.0mm,考虑到锥段转鼓铸件壁厚有的地方变大, 1一销子2一挡板3一金属型筒4一耐火砖5一芯骨6一砂芯7一底板图3改进型立式离心铸造用铸型结构示意 定金属型筒的壁厚为90mm,此时6型胚铸=1.7。2.3铸型首次使用前内表面的处理 首次使用的金属型筒工作表面,在机械加工后比较光洁、存在油污等,喷涂涂料后会出现涂料容易脱落的现象,使铸 件产生夹渣等有害缺陷。因此,金属型筒在首次使用前,通 常要求喷涂涂料后用适当温度的金属液清洗型筒一次。生产 实践发现,金属型筒工作表面在首次使用前,提前在喷涂的 涂料中加入少量的盐,然后喷涂到金属型筒工作表面并存放 5。7天,之后将金属型筒工作表面用清水清洗干净,清洗 干净后即可投入使用,且加人的少量的盐并不会对金属型筒 产生任何危害,并可以大大减少资源的浪费、提高生产效率 17 等。2.4铸型加工余量的确定 采用离心铸造时,金属液在离心力的作用下进行补缩,一般无气孔、夹渣等有害缺陷,杂质主要聚集在锥段转鼓铸件 内表面和两端面,故铸件内表面加工余量要大于外表面。同 时,在改进型立式离心铸造工艺中,由于增加了砂芯,避免 了铸件内表面产生缩凹;因此,设计加工余量时不需要考虑 在改进型立式离心铸造用铸型中,金属型筒与底板、底板与立式离心机采用止口定位,尽量使金属型筒、砂芯、底板 三者同心,保证锥段转鼓铸件的同心度。整个铸型中,砂芯 内芯骨采用无缝钢管,在钢管长度方向上钻有许多小孑L, 用以引导砂芯内的水汽从底板孑L中排出,防止浇注时砂芯 内的气体将砂芯胀坏,使锥段转鼓铸件产生气孔、夹渣等缺 陷。砂芯顶部设有耐火砖,用以缓冲浇入模具型腔的熔融金 属液,避免砂芯被冲坏。底部沿圆周布置有耐火砖,通过外 模将其压紧在底板上,使熔融金属液与底板隔开,尽可能减 少热量传输到底板上,由于底板与立式离心机连接板直接接 触,热量传输的减少对立式离心机也有一定的保护作用。同 时,金属将耐火砖压紧在底板上,也起到了密封作用,可防 止熔融金属液从金属型筒与底板间流出。 于宏斌等:锥段转鼓的立式离心铸造工艺18 凹对铸件壁厚的影响。故其单面加工余量:锥段转鼓上端(小直径端)面为20mm,锥段转鼓下端(大直径端)面 为16mm,锥段转鼓外圆加工余量为6mm,锥段转鼓内 孔加工余量为102.5铸型转速的确定 700左右时,离心力基本上已不起作用,可停机将铸型从立式离心机上吊走,以保护立式离心机。为便于操作, 待铸件自然冷却至300左右脱模。 离心铸造工艺后是否产生气孑L、夹渣等有害缺陷,对机械加工成型后的锥段转鼓进行了化学成分、机械性能、液体 渗透检测。立式离心铸造锥段转鼓实物如图4所示。液体渗 透检测执行英国BSEN 对于国外某离心分离机用大直径不锈钢锥段转鼓,其材质为UNS 砂铸、重力压模铸和低压模铸法》中的SP2、CP2、LP2和AP2规范,检测区域包括锥段转鼓外表面及可探 内表面等。结果显示:采用改进型立式离心铸造工艺,其双 相不锈钢锥段转鼓质量满足液体渗透检测标准要求。锥段转 鼓的化学成分和机械性能也都满足ASTM N/m3。由于锥段部分增加了砂芯,0可按直段部分的选取,即E0=137.5mm。因此,由公式(1)可 计算出铸型所需的离心转速为533.0~692.9r/ min。 铸型的离心转速凡取560r/min,此时口=1.05。2.6金属型筒的涂料 金属型筒的涂料采用硅石粉水基涂料,喷涂的涂料厚度为1.2.1.5mm,喷涂涂料时应均匀、平整。金属型筒、 20 砂芯预热后喷涂涂料,喷涂后不需再次预热。 金属型筒的预热温度为180~240。首次使用时,先预热至300,然后自然冷却至180~240进 行涂料的喷涂,喷涂涂料后即可用于浇 砂芯采用树脂砂造型,预热温度为120~150,预热时间不宜过长,一般为1h左右,以避免出现松垮,滞留 的水汽在浇注时可以将热量从底板孔中带出。预热后进行涂 料的喷涂,涂料喷涂完毕后即可用于浇注。2.8浇注温度 的确定 对双相不锈钢来说,其熔点约为l基础上上升120~230,即1 为进一步检测锥段转鼓内部是否含有夹渣等,补充进行了21 超声波检测,按照NB/T47013.3—2015(承 压设无损检测第3部分:超声检测》进行检测,采用CS K—IIA一2标准试块,检测区域包括锥段转鼓所有可探 区域。结果显示:采用改进型立式离心铸造工艺,其双相不 锈钢锥段转鼓的超声波检测结果满足NB/T4701 3.3—2015标准要求。 cc。采目前,华星炉管生产的所有双相不锈钢锥段转鼓已交付用户复检,结果满足要求,且使用后质量良好,现已 批量出口。 浇注温度过高则不利于保护铸型,且为保证铸型型腔内的气体能充分排出,故取浇注温度为1 (1)在常规立式离心铸造的基础上,通过增加砂芯改进铸型,使生产的锥段转鼓无气孑L、夹渣等有害缺陷。 STEELPIPEDec.2016,V01.45,No.6 22 『5]隋艳伟,李邦盛,刘爱辉,等.立式离心铸造液态金属 中气泡的长大规律[J].特种铸造及有色合金,2009,29 (3)铸型中增加的砂芯有效地控制了锥段转鼓内孑L的加工余量,大大提高了工艺出品率。 [6]王小军,张应龙.双相不锈钢转鼓用管的离心铸造生产 (5)金属型筒首次使用前,在涂料中加入少量盐,喷涂到金属型筒的工作表面存放5—7天,清洗干净后可直接投 入使用,提高了生产效率。 艺及铸型强度校核[J].铸造,2016,65(5):459—462.『10]杨为勤,党旭亮.大型锡青铜厚 壁蜗轮的离心铸造工艺 『1]龚俊,张凯,辛舟.离心分离机开孑L转鼓的设计计算 研究[J1.特种铸造及有色合金,2012,32(10):975— f12]王伟,张国利,姜福顺.管模用钢21CrNol0材料的研 [2]李文辉,龚俊,刘永平.离心卸料离心机锥形转鼓24 简体 [13]张伯明.离心铸造[M].北京:机械工业出版社,2004. [3]汤新文,陈海辉.离心机转鼓爆裂事故分析[J].机电工 计及充型凝固模拟[J].热加工工艺,2012,14(7):66— 中国钢结构协会钢管分会七届二次理事(扩大)会议暨2016钢管产业链发展与应用大会在市召开 2016年11月l一3日,中国钢结构协会钢管分会(简称钢管分会)七届二次理事(扩大)会议暨2016钢管产 业链发展与应用大会在市召开。来自国内80余家钢管 生产企业、贸易和行业协会的140余人参加了会议。 25 市经信委新材料处副处长李慧民、中国钢结构协会常务副会长刘毅、钢管分会理事长朱学强到会并致辞。 会议听取了国务院钢铁专家、“一带一路”研究院常务副院长、国资委大型企业监事会原主席、原国家冶金局副局长赵 喜子作的《民营钢铁企业发展新趋势》报告;钢管分会顾问 庄钢作的《十三五期间中国钢管行业发展前景和机会》报告; 国家电网北京国网富达科技发展有限责任副总经理徐 德录作的《钢管塔原材料需求与市场供应现状分析》报告; 中油管道物资装LNG项目经理、高级工程师吕 志刚作的《管道工程项目中品种钢管的应用及项目介绍》报 告;海油石油工程股份海洋工程技术中心副主任兼 设计首席工程师赵冬岩作的《海底管道用管现状及展 望》报告;中国广核集团核安全技术中心那福利作 的《核电机组用管的准人标准及采购模式》报告;大唐华东 电力试验研究所总工程师王家庆作的《十三五期间燃煤电 发展动态展望》报告等。 会议讨论通过了钢管分会理事长、副理事长人事变动的议案;通过了9家企业的人会申请;听取了钢管分会秘书处《钢 管行业“十三五”发展规划纲要指导意见(讨论稿)》编制说 明,并决定将于2016年底前下发正式稿。 会议对钢管行业协会为本次会议提供的周到服务表示衷心地感谢。 26 安装好型筒涂刷好锆英粉醇基涂料的前后端盖,预热型筒。预热温度一般在 180-220范围之间,此时,涂料中的水分 可以充分蒸发,减少气孔的产生,使涂料中粘胶剂充分发挥 作用,可以防止涂料被冲刷,出现粘型筒、端盖现象。 2.1喷涂 喷涂压力0.45-0.55MPa,喷涂小车行走速度7m/s, 喷涂料速度及喷涂量 250g/20s ,涂层厚度:小管径 0.2-0.3mm,大管径0.3-0.5mm,型筒转速600-800 槽伸入铸型的轴线左右的铸型转动,倾 型槽,将覆膜砂或石英砂均匀地铺在铸型的工作面上,利用铸型热量硬化覆膜砂,覆膜砂在铸型上的厚度为 2-4.5mm。 3.1铸型转速的选择,过低的铸型转速,会出现钢液雨淋现 象,也会使铸管内出现疏松、夹渣,内表面凹凸不平等缺陷; 27 过高的铸型转速,铸管上易出现裂纹、偏析等缺陷,也会使 机器出现大的震动,磨损加剧,功率消耗过大。2-4 吋转速 为850 转/s,4-8 吋转速为750 3.2浇注定量 由离心铸管的内径、外径、长度、比重,确 定浇注重量。 3.3浇注 浇注温度、化学成分要合格后,在浇包中按浇注 定量承接浇注一根铸管的钢液,把浇注槽伸入型筒内,快速 把钢液倾入浇注槽,让浇注槽出口的钢液均匀地铺在铸型的 内表面上,不得有断流现象。要求在2-5s 内完成浇注,以提 供足够的钢液流速。 要严格控制拔管时间、温度,拔管太早,铸管温度高,会出现弯曲和断裂现象;拔管太晚,型筒温度升高,不利于喷 涂工艺进行,且降低了生产效率,同时铸管在型筒中收缩受 阻,易引起裂纹。拔管温度应在500-700之间。 5.1经常检查型筒,有无裂纹、变形、损伤等。 离心铸造工艺将金属液浇入旋转的铸型中,使之在离心力 作用下充填铸型并凝固成形的铸造方法,称为离心铸造。 根据铸型旋转空间位置的不同,常用的离心铸造机有立式和卧式两类。铸型绕垂直轴旋转的称为立式离心铸造,铸型 绕水平轴旋转的称为卧式离心铸造。 将液态金属浇入旋转的铸型里,在离心力作用下充型并凝固成铸件的铸造方法。离心铸造用的机器称为离心铸造机。 按照铸型的旋转轴方向不同,离心铸造机分为卧式立式和倾 种。卧式离心铸造机主要用于浇注各种管状铸件,如灰铸铁球墨铸铁的水管和煤气管,管径小 75 毫米,可达 3000 毫米此外可浇注造纸机用大口径铜辊筒,各种碳钢、合 金钢管以及要求内外层有不同成分的双层材质钢轧辊。立式 离心铸造机则主要用以生产各种环形铸件和较小的非圆形 铸件。 离心铸造所用的铸型,根据铸件形状、尺寸和生产批量不同,可选用非金属型(如砂型、壳型或熔模壳型)、金属型或 在金属型内敷以涂料层或树脂砂层的铸型。铸型的转数是离 心铸造的重要参数,既要有足够的离心力以增加铸件金属的 致密性,离心力又不能太大,以免阻碍金属的收缩。尤其是 对于铅青铜,过大的离心力会在铸件内外壁间产生成分偏 析。一般转速在每分钟几十转到1500 转左右。 离心铸造的 特点是金属液在离心力作用下充型和凝固,金属补缩效果 29 好,铸件组织致密,机械性能好;铸造空心铸件不需浇冒口, 金属利用率可大大提高。因此对某些特定形状的铸件来说, 离心铸造是一种节省材料、节省能耗、高效益的工艺,但须 特别注意采取有效的安全措施。 离心铸造既是传统、又是一种现代的铸造方法。我国铸件的年产量在1500 是用离心铸造方法生产的,占 15%。其中球墨铸铁管125 t,内燃机缸套35 t。随着人民生活水平的提高,国家在城镇化建设、离心铸造西气东输、南水北调 等项目上的大力投资,以及汽车作为支柱产业的兴起,预计 2010年,用离心铸造生产的铸件,每年可达到 320 以上。不言而喻,在生产铸件的各种方法中离心铸造方法将仅次于砂型的铸造方法,具有举足轻重的地位。 人们提出对输水工具的需要要早于工业革命时期。我国在明洪武年代(1368—1399 年),就生产了铸管,用在南京武庙 闸渠;德国根铸管是在 1455 年生产的,用在迪伦堡宫 殿(Schloss Dillenburg);法国则是在1644 年生产的铸管,用 在塞纳河至凡尔赛宫 34hn 长的管线上。由于输水线路—般 较长,如何提高铸管的生产效率和质量,在当时成为批量生 产的关键。于是英国人埃尔恰尔特(Emhart)在 1809 年提出 了世界上个离心铸造法的专利,名称为“用铁液生产更 好、更纯净的金属制品”。它要比德国人贝士麦(Bessmmer) 30 提出的连续铸管的方法早 d8 年(1857 年)。随后,离心铸造 方法在和连续铸造、砂型铸造的竞争中不断发展,并逐渐推 广到其他环形铸件(例如气缸套、轴瓦)的生产中。但真正使 离心铸造发展成第二大类的铸造工艺方法,还要归功于巴西 人代—拉沃德的水冷金属型离心铸造机的发明与 20 世纪中 球墨铸铁在铸管卜的应用,从而开始了用离心铸造工艺 替代连续铸造工艺、用球墨铸铁替代灰铸铁在生产压力铸管方面的过渡。 因此,大都认为离心铸造法是环绕铸管生产的发展而开发并推广到其他铸件生产的方法。 离心铸造属于特种铸造。其特点就在于金属液浇人旋转的铸型小,在离心力的作用下成形、凝固而获得铸件。 根据离心铸造的不同形式可对其进行分类,见表2—1。按离心力应用情况的分类法,首先是由美国和德国提出的,我 国在CB/T5611—1998《铸造术语》标准中也规定了相应的 概念。美国按表2—1 分为三类,德国则只分为1、3 两类。 不用砂芯,纯粹用旋转产生的离心力使金属液紧贴型壁而形 成空腔铸件的方法称为线)。作为真 正离心铸造的典型产品,如不同长度的铸管、不同直径的缸 套。旋转轴可以处于任意角度,如管于等长件—般用水平旋 转轴;缸套、轴套等短件可使用垂直旋转轴,其共同特点是 铸件轴线与旋转轴线重合。图 为半线 铸型形状仍是轴对称的,但较上述的管子与缸套等铸件要复 杂得多。中心孔可用砂芯做出。铸型旋转速度远比前者要低, 离心力有助于充型与凝固,但不起成形的作用。非真离心铸 造如图 所示,零件形状可随意,仅利用离心力增加金属液凝固时的压力,铸型旋转速度也更低,铸件中心线也不 和旋转轴线重合。 我国习惯上常用的分类方法是按旋转轴位置分类,因它和离心机的分类相同,即分为水平(或卧式)离心铸造(如图 2-1 所示)和立式离心铸造,如图 2-2、2 所示。为获得更好的铸件,在水平离心铸造中,水平旋转轴并非完全水平,而 是和水平有很小的倾角,它仍归于水平离心铸造范围内,在 倾角较大时也称为倾斜离心铸造,常用在轧辊铸造上。 离心铸造用铸型可用不同材料制成,按其分类有:金属型、带耐火层。 LED贴片机 贴片机 国产贴片机 砂型铸造所用铸型一般由外砂型和型芯组合而成。为了提高铸件的表面质量,常在砂型和型芯表面刷一层涂料。涂料 的主要成分是耐火度高、高温化学稳定性好的粉状材料和粘 结剂,另外还加有便于施涂的载体(水或其他溶剂)和各种附 加物。[编辑本段]原料及工艺砂型制造砂型的基本原材料是 铸造砂和型砂粘结剂。常用的铸造砂是硅质砂。硅砂的高 温性能不能满足使用要求时则使用锆英砂、铬铁矿砂、刚玉 砂等特种砂。为使制成的砂型和型芯具有一定的强度,在搬 运、合型及浇注液态金属时不致变形或损坏,一般要在铸造 中加入型砂粘结剂,将松散的砂粒粘结起来成为型砂。应用 广的型砂粘结剂是粘土,也可采用各种干性油或半干性 油、水溶性硅酸盐或磷酸盐和各种合成树脂作型砂粘结剂。 砂型铸造中所用的外砂型按型砂所用的粘结剂及其建立强 度的方式不同分为粘土湿砂型、粘土干砂型和化学硬化砂型 粘土湿砂型以粘土和适量的水为型砂的主要粘结剂,制成砂型后直接在湿态下合型和浇注。湿型铸造历史悠久,应用 较广。湿型砂的强度取决于粘土和水按一定比例混合而成的 33 粘土浆。型砂一经混好即具有一定的强度,经舂实制成砂型 后,即可满足合型和浇注的要求。因此型砂中的粘土量和水 分是十分重要的工艺因素。 粘土湿砂型铸造的优点是:?粘土的资源丰富、价格便宜。?使用过的粘土湿砂经适当的砂处理后,绝大部分均可回收再 用。?制造铸型的周期短、工效高。?混好的型砂可使用的时 间长。?砂型舂实以后仍可容受少量变形而不致破坏,对拔 模和下芯都非常有利。缺点是:?混砂时要将粘稠的粘土浆涂 布在砂粒表面上,需要使用有搓揉作用的高功率混砂设, 否则不可能得到质量良好的型砂。?由于型砂混好后即具有 相当高的强度,造型时型砂不易流动,难以舂实,手工造型时 既费力又需一定的技巧,用机器造型时则设复杂而庞大。? 铸型的刚度不高,铸件的尺寸精度较差。?铸件易于产生冲 砂、夹砂、离心铸造气孔等缺陷。 20 世纪初铸造业开始采用辗轮式 混砂机混砂,使粘土湿型砂的质量大为改善。新型大功率混 砂机可使混砂工作达到高效率、高质量。以震实为主的震击 压实式造型机的出现,又显著提高了铸型的紧实度和均匀 性。随着对铸件尺寸精度和表面质量要求的提高,又出现了 以压实为主的高压造型机。用高压造型机制造粘土湿砂型, 不但可使铸件尺寸精度提高,表面质量改善,而且使紧实铸 型的动作简化、周期缩短,使造型、合型全工序实现高速化 和自动化。气体冲击加压的新型造型机,利用粘土浆的触变 34 性,可由瞬时施以0.5 兆帕的压力而得到非常紧密的铸型。这 些进展是粘土湿砂型铸造能适应现代工业要求的重要条件。 因而这种传统的工艺方法一直被用来生产大量优质铸件。 粘土干砂型制造这种砂型用的型砂湿态水分略高于湿型用的型砂。砂型制好以后,型腔表面要涂以耐火涂料,再置于 烘炉中烘干,待其冷却后即可合型和浇注。烘干粘土砂型需 很长时间,要耗用大量燃料,而且砂型在烘干过程中易产生 变形,使铸件精度受到影响。粘土干砂型一般用于制造铸钢 件和较大的铸铁件。自化学硬化砂得到广泛采用后,干砂型 已趋于淘汰。 ?气雾硬化:混砂时加入粘结剂和其他辅加物, 先不加硬化剂。造型或制芯后,吹入气态硬化剂或吹入在气 态载体中雾化了的液态硬化剂,使其弥散于砂型或型芯中, 导致砂型硬化。气雾硬化法主要用于制芯,有时也用于制造 小型砂型。 ?加热硬化:混砂时加入粘结剂和常温下不起作用的潜硬化剂。制成砂型或型芯后,将其加热,这时潜硬化剂和粘结剂 中的某些成分发生反应,生成能使粘结剂硬化的有效硬化 剂,从而使砂型或型芯硬化。加热硬化法除用于制造小型薄 壳砂型外,主要用于制芯。 化学硬化砂型铸造工艺的特点
以上信息由江苏亚立特钢有限公司整理编辑,了解更多离心铸造信息请访问http://www.jsyltg.com