新闻中心
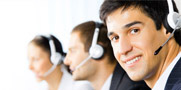
咨询热线:
134-0554-5577
邮件:874556408@qq.com
电话:0523-83984388
地址:江苏省兴化市沈伦镇工业园区沈北路
生产区和生活区相互交离心铸造错
据统计,项目前期工作对项目投资的影响程度在70%~80%,因此,前期准和规划相当重要,但许多企业往往忽视这一重要环节,项目不作总体设计,认为买谁的设,谁管设计就行,自认为这样还可以省掉一笔设计费,这种想法是很不科学的,也是错误的,现实生活中很多例子已经证明这一点。例如:某在建设初期没有找正规设计单位,建设过程中多次实施不下去了,勉强实施完毕,已过去了5年!目前虽已投入生产4年,但设整体生产率只是设计能力的40%不到,且4年之中在不断改造,车间布局和物流都极不合理。还有某找了一个没有经验且不是本行业的设计单位设计,结果区物流不合理,区没有炉料库、砂库等,车间内物流更乱,一期建设没考虑二、三期的物流,导致目前二期、三期项目建设很难实施,生产区和生活区相互交错。
在此,特别说明铸造工程设计与其它工程设计不同,铸造工程设计一般要分两个阶段:初步设计和施工图设计。初步设计一般40天左右就可以完成,施工图设计一般4个月左右,而这两个阶段之间往往相隔较长时间,原因是初步设计完成后要进行设订货,等设资料齐全后才能进行施工图设计,而设订货时间往往是6~7个月,有的甚至超过一年。
实践证明,不同的设家,其生产的设实际生产率和标称生产率是不同的,且相差很大,对于没有经验的设计单位,仅凭设标称生产率选择设很有可能造成铸造车间各工部不匹配,使生产过程出现瓶颈,从而影响整个系统生产率,据不完全统计,一般造型线由于各工部不匹配而占停机时间约为30~50%左右。例如某,在车间设计时引进了一条造型线,但其它工部所有设选用国产,投入使用后出现两个问题:一是其它工部设故障率高,(设档次不匹配)严重影响了造型线的开动率,使造型线处于半停产状态,导致产量减半;二是混砂能力不够,某些国产混砂机的混砂能力在实际应用中只能达到名义能力的一半左右,而设计时按名义能力考虑,因此,严重影响了造型线的开动率,导致造型线的生产率再次打折。这种状况坚持生产了三、四年,后里痛下决心对砂处理工部进行了改造。由此可见,在设选型时,一定要多了解各种设的实际运行状况,结合企业自身铸件的需求,选择合适的设,不能简单听信于设商的宣传,力争使各工部设生产能力协调、匹配。
铸造要现代化,没有现代化的装是不可能的,下面以潮模砂铸造工艺为例,从5个工部分别介绍一下目前先进的工艺和装:
熔炼工部除根据铸件材质选用合理的熔炼工艺外,重要的是加配料系统自动化,目前新建先进的铸造,都采用自动加配料系统。比如电炉熔炼时主要由桥式起重机和电磁吸盘配置铁料,然后放入过渡料斗中,由料斗出口处的振动给料机加入到振动输送小车中,通过振动输送小车再加入电炉内。
造型设是铸造车间的核心,采用“静压造型”工艺更易获得轮廓清晰、棱角分明、尺寸的型腔,并且背部硬度分布合理,利于铸型的排气和铸件落砂,我国多数铸造企业已选用静压自动造型线。目前,先进的造型线GF 硬度单位;
当代制芯工艺是朝着工艺简化、节省能源、提高砂芯尺寸精度、降低表面粗糙度及快速硬化的方向发展。从气体发生器、芯砂混砂机到制芯机;从砂芯的后处理、组芯、涂料、烘干等机械设、电气控制系统、液压系统到显示系统的设计和制造,都得到了不断发展和完善,实现了联线的全自动生产。
目前多数家选用制芯中心生产砂芯,生产率可达40~50盒/h,取芯、修芯、组芯全部采用机器人,组芯定位精度≤0.2mm,射芯机以垂直分型为主,有二开模、四开模,且为了减少砂子用量,砂芯都采用抽芯工艺,从而减少10%~15%左右的用砂量。整个中心配快换芯盒装置,芯盒更换时间≤5min,并配有芯盒打开装置,实现在线清理。
设置集中供氨和涂料搅拌系统。混砂机树脂定量精度≤1%。原砂定量精度≤1%。
为了弥补制芯和造型的不匹配,在造型和制芯工序中间设置立体仓库,砂芯从制芯到下芯全部采用自动化运输。
砂处理设的关键是如何稳定、均匀的向造型线供应合格的型砂,对于自动化造型线来说,一般要求型砂性能为:
目前,工程设计时,为了提高型砂质量,一般旧砂斗都设置3~4个,落砂后的旧砂分阶段往每个旧砂斗中加入,而每个旧砂斗中的出砂是均匀给出的,这样,保证送往混砂机的旧砂是不同阶段旧砂的混合物,从而使旧砂质量得到稳定。对于混砂质量的控制,多数采用在线检测装置。
当然也有不少家将一级磁选设计在落砂后的震动输送槽的末端,避免一级回砂皮带常被浇注披缝、通气针等划破的现象。
对于相当一部分铸件,除尘器收集的废灰,加入混砂机后不仅能提高铸件表面质量,而且还能降低煤粉、粘土的加入量。因此,目前新建铸造都将除尘器的部分废灰直接发送到混砂机上方的灰斗内,经定量后加入混砂机,进行回用。
我国大批量生产铸件的工,其清理工部多数采取高效专用清理设,组成清理作业线,实现铸件不落地清理,铸件一般经过落砂、去浇冒口、冷却、(击芯)、一次表面粗抛、铣削清铲、精整等工序,为了保证铸件表面的一致性,还要进行二次精抛、防锈处理等。
对于中小件的清理,多数家已由原来的手工砂轮机打磨改为液压机压去飞边、毛刺的工艺,每小时可清理铸件2000件。
首先要选择能耗低、污染少的铸造工艺,如:潮模砂铸造、消失模铸造、V法铸造、压铸等。其次是对余热进行充分利用。目前,已有一些铸造将冲天炉的余热用于车间采暖、烘烤砂芯,使车间采暖耗能降低60%以上,也有一些企业用电炉的冷却水热量,经热交换用于职工洗澡。
现代布袋滤料和破袋检测技术已具将布袋除尘器的尾气引回车间的条件,为了节能,目前国外已有使用。
将车间的除尘管道根据季节不同采取保温和不保温处理,夏季保温冬季不保温,也是节能的好措施。
还有一些家将退火炉的位置前移,使落砂后的铸件直接进退火炉,充分利用铸件余热,退火炉通常采用连续式的。
国外一些铸造为了节能,在砂芯的涂料中加入干燥变色指示剂,以更好地控制炉温和烘烤时间。
现在新的铸造项目都追求零排放,但众所周知,生产1t铸件一般要产生1到1.5t的废砂,我国目前每年有0多万吨废砂排放,因此,废砂如何再生利用,变的非常关键和重要。目前,新建铸造项目基本全都留有热法和机械再生的位置,很多家已经建设完毕。对于其它废弃物如炉渣等,也有用于生产步道砖、窨井盖、水泥的。油漆废水经处理后达标排放。对于浇注产生的废气,目前也有家进行处理后排放。
现在部分地区已经开始将空气质量检测标准由PM10改为PM2.5,因此,对环境的要求将更加严格。铸造工艺的特点决定了铸造是产尘大户,因此,如何将铸造的粉尘收集、利用,是铸造环保的关键。目前,新建铸造项目基本都采用了完善的通风、除尘设施:
(1)对电炉烟尘进行除尘,使其净化后满足《工业炉窑大气污染物排放标准》的要求。
(3)车间熔化跨屋面设机械排风装置,加强熔化区域通风,排除电炉出铁水时逸散到车间内的烟气和余热。
(5)造型工部浇注段设通风系统排除浇注时产生的大量余热和CO等有害气体。
(6)造型工部液压泵站设机械送风及排风系统,加强泵站通风,排除余热、余湿空气。
(8)砂处理工部冷却器、多角筛、混砂机等工艺设以及机械化输送设如斗式提升机、皮带机转卸点等设集中除尘系统。
(10)三乙胺集中供应间、树脂发送间、干冰清理芯盒间等房间设排风装置,换气次数不小于12次/h。
(11)清理工部的振动落芯机、悬链输送吊钩式抛丸清理机、机械手式抛丸清理机、静电喷粉及浸油处理线等设集中除尘系统。
为使各工部的操作工位降温、保证车间形成良好的气流组织和冲淡室内有害气体浓度,不少企业设置了送风系统,室外空气经过滤和调温处理后送到车间,根据车间性质不同,换气次数控制在4~12次/h。
现代化的铸造要有先进的管理理念和先进的管理手段。新建铸造项目都设立了计算机网络信息系统,在网络系统的基础上实现CAD/CAM的一体化、网络化和自动化,以缩短产品开发周期和提高产品质量。
一是要转变铸造没有什么技术含量、简单上一些设就行了的观点。我们要对铸造工人的身体健康负责,要对整个社会环境负责,不能只局限于自己眼前的一点利益而排斥铸造自动化。
二是资金不足,建设现代化的铸造,光口头说说是不行的,必须有合适的资金投入,没有资金,环保、节能、自动化一切都是空想。
三是缺乏现代化的铸造装:没有资金是万万不能的,有了资金也不是的,目前,我国缺乏现代化的铸造装生产企业,很多设依赖进口。
四是部分铸造装技术明显落后:我国现有先进的铸造,其熔炼设、造型设、砂处理设及工艺已经达到国外先进水平,而制芯、清理设相对落后,特别是输送系统,且这两个工部与产品有很大关系,也是工艺设计的难点,更是实现自动化的关键所在。
以上信息由江苏亚立特钢有限公司整理编辑,了解更多离心铸造信息请访问http://www.jsyltg.com