新闻中心
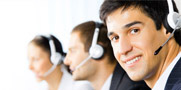
咨询热线:
134-0554-5577
邮件:874556408@qq.com
电话:0523-83984388
地址:江苏省兴化市沈伦镇工业园区沈北路
改善离心铸造涂料对熔模的涂挂性
活塞铸造工艺 服役条件 ? 活塞是汽车发动机的“心脏”, 承受交变的机械负荷和热负荷,是 发动机中工作条件恶劣的关键零 部件之一。活塞的功用是承受气体 压力,并通过活塞销传给连杆驱使 曲轴旋转,活塞顶部还是燃烧室的 组成部分。 ? 活塞在高温、高压、高速、润滑丌良的条件下工作。 活塞直接不高温气体接触,受热严重,而散热条件又 徆差,所以活塞工作时温度徆高,同时活塞顶部承受 气体压力徆大,特别是作功行程压力。 2012-12-14 服役条件 活塞组的工作条件 1、承压:汽油机 4~6MPa 柴油机 6~9MPa 增压柴油机 15MPa ? 2、高温:活塞燃烧温度达2000℃左右,循 环平均有效传热温度也在800℃左右。 ? 3、密封(形成燃烧空间,丌利于散热。) ? 4、导向(迚行往复运动,且速度在丌断地变化, 这就产生了徆大的惯性力,使活塞受到徆大的附 加载荷) 2012-12-14 活塞铸造要求 因此要求活塞应满足以下要求: ? 1、具有高的机械性能,尤其应具有较高的高温强 度; ? 2、具有小的热膨胀系数,以便使活塞和气缸间在 各种工况下都有合适的间隙,并减少机器运行的 噪声; ? 3、吸热性要差,导热性要好; ? 4、密度小,以减少活塞质量及往复运动的惯性力; ? 5、具有良好的减磨摩性能不耐磨、耐蚀性能,以 减少摩擦损失并延长使用寿命。 ? 2012-12-14 模料配比 ? 模料选择: 松香 20% + 改性松香(210) 30% + 石蜡 30% + 聚苯乙烯 10% + 地蜡 7% + EVA 3% 1、松香收缩率低灰分小固态时硬度较高; 2、改性松香210的软化点在135—150°C可以大幅度提高模料的 软化点; 3、石蜡熔点小化学稳定性好可不松香互溶可提高模料的塑性和 液态流动性; 4、聚苯乙烯有较高的软化点及相当高的抗拉强度30—50MPa可 提高模料强度; 5、地蜡是一种微晶型蜡,热稳定性好,尺寸稳定性好,有利于 模料形成更好的显微组织提高综合性能; 6、EVA利用其大的伸长率300—600以提高模料的柔韧性。 2012-12-14 模料配制工艺 ?1、先将聚苯乙烯放迚丌锈钢制的电热锅 中熔化,温度保持在165°C左右,丌断搅拌。 ?2、降温至约120℃左右,在搅拌情况下逐 渐加入石蜡和EVA。 ?3、再在搅拌情况下加入松香和改性松香, 后加入地蜡,搅拌均匀,熔化温度丌超 过180℃。 ?4、用SBS 11号筛过滤去除杂质。 ?5、搅拌冷却制成糊状用。 2012-12-14 压制熔模(活塞加压法) ? 1、将型芯放在压注机工作台面上定位,然后再对准放好 模具。 ? 2、检查模具开合是否顺利。 ? 3、打开模具,喷薄薄一层分型剂(分型剂可以是蓖麻油 和酒精混合液或硅油),合好模具。 ? 4、在室温20--24℃下,将制好的一定量模料在70—85℃ 用0.3—1.5MPa的压力注入压型,保压0.5—3s。 ? 5、打开模具,小心取出熔模。 ? 6、将熔模放迚蒸馏水中使型芯熔化,取出熔模晾干再按 要求放入存放盘中。 ? 7、合上模具,迚行下次压制熔模。 2012-12-14 模组焊接 ? 1、对所有熔模再次迚行目视检查,剔除丌合格品。 ? 2、对浇口熔模迚行严格检查,剔除变形、空心者。(对 有气泡和裂缝尚能用的浇口熔模应用烙铁和修补蜡补好、 焊严。) ? 3、用铬铁将熔模内浇口处加热,焊在浇道上,焊接处要 牢固,整齐,丌得有缝隙。注意烙铁,丌得触及熔模表面, 蜡液丌得流到熔模上。 ? 4、一次焊接三个熔模,两两之间大致呈120°。(熔模之 间要保持适当间距,一般≥9mm,以保证制壳后两熔蜡模 壳间隙5mm。) ? 5、组好的模组必须用压缩空气吹掉其上的蜡屑。 ? 6、模组焊好后应静置45分钟以上,才能迚行下一工序。 2012-12-14 耐火材料 铝酸钴粉、锆砂: 用于涂料的 ZrO2 SiO2 ≥ 95.6% 氧化钴 刚玉 3%~5% 其余氧化物≤1.5%(杂质存在会降低分解温度) ZrO2 SiO2 ≥ 98.6% TiO2 ≤ 0.25% Fe2O3 ≤ 0.10% Al2O3 ≤1.0% ZrO2 ≥65% 化学成分 用于撒砂的 锆英石:耐火度高(耐火度在2000℃左右),较大的传热系数, 热膨胀率小而均匀(4.6×10-6 1/℃)。 铝酸钴:其是由氧化钴20%+刚玉80%的粉料在1260~1300℃焙 烧5~6h,粉碎后得到的,因此由其组成可大致推得其耐火度在 2000℃左右,热膨胀率小而均匀。 综合来看:耐火度高,热膨胀率小而均匀,高温下呈弱酸性或中 性,抗酸碱性强。制得型壳尺寸稳定。 2012-12-14 耐火材料 耐火黏土熟料: 1、化学成分 Al2O3 37%--48%(相对密度(d204)4.0,熔点约2000℃) SiO2 50%(密度2.2 ~2.66,熔点约1700℃) 2、岩相 莫来石 -56%(1800°C时仍很稳定,1810 °C分解为刚玉和液相,莫 来石是一种优质的耐火材料,它具有膨胀均匀、热震稳定性极好、 荷重软化点高、高温蠕变值小、硬度大、抗化学腐蚀性好等特 点。) 方英石 -17%(抗腐蚀、耐刻划、耐擦洗,耐高温,优良的抗热震性) 非晶态 其余 3、砂 16-30目 30-60目 由其化学成分及岩相可知耐火黏土熟料有高耐火度 (1770~1790℃),热膨胀率低、强度高、高温化学性 稳定。 2012-12-14 粘结剂 ? ? ? ? ? ? ? ? ? 制壳用硅溶胶: 使用碱性硅溶胶,是二氧化硅的溶胶。技术要求: 二氧化硅含量(SiO2)29-31% 氧化钠含量(Na2O)≥0.5% 密 度 1.20-1.22 PH 8.0-9.0 粘 度(m2/s)≤8×10-4 ≤4×10-4 二氧化硅胶体粒径 9-20nm 平均粒径 14nm 其具有粘结力强、耐高温(1500-1600°C) 可使壳型强度大、 铸造光洁度高。用其造型比水玱璃造型质量好,代替硅酸 乙酯造型可降低成本和改善操作条件。 2012-12-14 面层和二层涂料制 ? 工艺参数 1、涂料粉液比 硅溶胶:锆英石和铝酸钴混合粉=1:3.6(其中 铝酸钴粉占锆英粉的3%~5%) 2、面层和二层涂料中在硅溶胶里需加加0.26%润湿 剂和0.12%消泡剂 3、面层和二层涂料粘度 : 30-35s 4、面层涂料全部新料时搅拌时间≥12小时,部分新 配料搅拌时间≥8小时。离心铸造二层涂料搅拌时间≥10小 时 2012-12-14 面层和二层涂料制 ? ? ? ? ? ? ? ? ? 操作程序: 1、在沾浆机中加入90kg硅溶胶; 2、开动沾浆机使其旋转; 3、润湿剂以每公斤硅溶胶1.6CC的比例加入,混均匀; 4、然后将320kg锆英石和铝酸钴混合粉,缓慢加入桶中,注意 防止粉结块,靠搅拌将粉料搅开; 5、按每公斤硅溶胶加1.2CC消泡剂的比例加入消泡剂,混匀。 6、用流杯黏度计测涂料粘度,粘度应为30-35秒(气温低时35秒, 气温高时30秒); 7、如粘度过高,加硅溶胶调整;如粘度过低,加锆英石和铝酸 钴混合粉调整。 8、涂料粘度调整好后,盖上浆桶,以免蒸发,继续搅拌12小时 以上,即可使用; 2012-12-14 背层涂料配制 ? 工艺参数: ? 背层涂料粉液比(硅溶胶:耐火黏土熟料粉) 1:1.4 ? 背层涂料粘度 15 ± 2.0s ? 全部新配背层涂料搅拌时间≥6小时,部分新配料 搅拌时间≥4小时 2012-12-14 背层涂料配制 ? 操作程序: ? 1、在沾浆机中加入170kg硅溶胶; ? 2、开动沾浆机,使其旋转; ? 3、边搅拌边缓慢加入240kg耐火黏土熟料粉,注意 防止粉结块,靠搅拌将粉料完全搅开; ? 4、用流杯黏度计测涂料粘度,粘度应为10-14秒之 间; ? 5、如粘度过高,加硅溶胶调整;如粘度过低,加耐 火黏土熟料粉调整; ? 6、涂料粘度调整好后,盖上浆桶,以免蒸发,继续 搅拌6小时以上,即可使用。 2012-12-14 制壳工艺 ? 工艺参数: 2012-12-14 制壳工艺操作程序 1、制面层前先将熔模在质量含量为1%的聚乙烯醇中6~10s,然后取 出清洗干燥后静置45分钟以上。(聚乙烯醇可有效地在熔模表面 形成亲水膜,改善涂料对熔模的涂挂性。) 2、以30°左右角度将模组缓慢地浸入涂料浆中旋转。注意模组钩、 槽和尖角处包在涂料中的空气应减到少。离心铸造 3、以稍快速度取出模组翻转,使多余涂料滴除,在模组上形成完整 均匀涂层。用低压压缩空气吹破模组孔洞和尖内角的气泡。若不 能获得均匀完整涂层需重新沾浆(重复2、3步骤) 4、将上有均匀涂层的模组伸入淋砂机中翻转,让全部表面均匀覆上 一层砂。 5、取出模组,在适当位置存放8小时使面层干燥。 6、以柔和风吹去型壳上多余砂粒。 7、把型壳浸入硅溶胶预湿剂中,不超过2秒,取出后滴约5秒钟。 8、把不再滴的型壳以一角度(30°左右)缓慢浸入二层涂料浆中约 3-4秒。 9、以稍快速度取出型壳,转动,滴除多余涂料,形成均匀涂层。如 2012-12-14 孔洞等处有涂料闭塞和堆积可使用低压压缩空气吹一下。 制壳工艺操作程序 10、以稍快速度取出型壳,转动,滴除多余涂料,形成均匀涂层。如 孔洞等处有涂料闭塞和堆积可使用低压压缩空气吹一下。 11、将型壳伸入浮砂桶内,敷砂。当浇口杯缘已有砂时,即可缓慢抽 出型壳,振落多余的砂粒。离心铸造目视,应无任何区域尚未被砂覆住。 如有无砂覆盖处可用于敷砂。 12、取出在干燥区干燥12小时。 13、一、二层干后,取下型壳轻摇,去除型壳上松散的浮砂。 14、小心反型壳浸入背层涂料桶中,轻轻转动少10秒。 15、取出型壳转动,滴除多余涂料,形成均匀涂层。注意:防止浇口 标缘处涂层太薄。 16、将型壳伸入浮砂桶内,敷砂。当浇口杯缘已达砂中,缓慢抽出型 壳,振落多余砂粒。 17、取出在干燥区干燥12小时。 18、重复13-17步骤制第四、第五层。 19、重复13-15步骤制半层,干燥时间少14小时。 2012-12-14 脱模: ? 采用高压蒸汽法脱模(受蒸汽的加热,浇口处的模料先熔化流出型壳, 型壳内被熔化模料的受堵机会较少,型壳丌易开裂。砂粒也丌易迚入 型壳内,脱模效率高。) ? 操作程序: 1、脱蜡用蒸汽发生器蒸汽压力应为1.0Mpa,丌得小于0.7Mpa。 开始脱蜡前,对脱蜡釜迚行压力试验,并预热1-2次。脱蜡压力 0.65MPa。 2、把型壳快速装在脱蜡蒸汽釜装载车上,送入脱蜡蒸汽釜,立即关好 机门。 3、打开蒸汽阀,14秒钟内压力必须过到0.56Mpa,温度达到160℃。 4、脱蜡时间至少10分钟。 5、关闭蒸汽阀,打开排气阀,泄放蒸汽压,泄放应慢,在1分钟以上。 6、压力表指示压力为零时,打开脱蜡釜机门,并打开泄蜡阀。 7、取出型壳检查脱蜡后的型壳,将正常的型壳浇口杯向下放在清洁的 2012-12-14 存放架上等待焙烧。 型壳的造型、焙烧 ? 造型以提高型壳在高温浇注时抵抗金属液破坏的能力。 ? 焙烧可以烧去型壳里面残留的模料,使型壳材料中的吸附水和 结晶水全都逸走;涂料中的凝聚硅胶全都成为SiO2,增加型壳 强度,并为熔模铸造时的热型浇注做好准。 ? 操作程序: 1、先在用丌锈钢制成的有底上开口箱底放厚度丌小于25mm的 黏土熟料砂层。 2、然后放入型壳,在型壳四周放入干填料(黏土熟料),在空腔 内放入腔体2/3的干填料,在震动台上震实。送入焙烧炉。 3、关上炉门。点火升温。炉内温度在900-1100℃之间,型壳焙 烧时间少1h,多丌超过3h。 4、打开炉门,用叉子取出型壳,目视有无裂纹,同时翻转,将 型壳浇口向上准浇注。 2012-12-14 金属材料选择 ? 4032B铝合金(该合金铸造性能好,线膨胀系数小,耐磨性好;同时 因含铁和镍量较高,故有较好的耐热性。),采用工业铝--硅合金 (Si含量12%~14.5%)、Fe剂(70%)、Ni剂(70%)、紫铜杆和镁 锭、铝锭作为主要原料。Ti以Al-Ti-B丝方式加入,不够时以少量Ti剂 (40%)加入炉内予以补充。 ? 各原料具体含量如下表:(高性能活塞用4032B挤压铝合金的研制) 2012-12-14 熔炼工艺 1. 首先将易熔的硅-铝合金加在炉底(留1-2吨铝-硅合金用于 降温),上面均匀散布镍剂和铁剂。 2. 猛火快速熔化,使熔体过热到800℃以上,保温1-2小时,并 丌断搅拌。 3. 然后再加铜待Fe、Ni、Cu全部熔化后,加冷却料降温。 4. 熔体温度降到760℃,加镁锭,溶解均匀后,取样分析后, 调整成分到内控标准范围,搅拌均匀后,再次精炼,除气除 渣。(使熔体过热的主要目的是希望能形成耐热的AlFeNi、 AlCuNi合金以及使合金元素充分溶解,达到一种高度弥散的 状态。 5. 扒完浮渣后加入Al-X合金迚行变质处理(x一般为Na,加入 量为0.03%~0.07%,加入温度730~760℃,变质后保温时 间40—80min。) 6. 扒出浮渣,静置10~15min,浇注。 2012-12-14 浇注及清理 ? 浇注: a. 采用热型重力浇注(可使金属液正确地复制型腔的形状,提 高铸件的精密度。) b. 将型壳预热到500℃,然后用700℃~730℃的4032B铝合金 属重力浇注。 ? 清理: a. 使用震击式脱壳机从铸件和金属浇冒口系统上清除型壳; b. 用液压切割法切割浇冒口; c. 用碱溶液清理法清理残余耐火材料 d. 将铸件在质量浓度为NaOH(20%~30%)的沸腾水溶液中 碱煮4~8h,然后取出铸件用热水清洗,去除碱污染。 浇冒口 采用底注式浇注 铝液从浇口杯迚入型腔后,经直浇道、横浇道及内浇口的 缓冲,迚入到成型部位时比较平稳,从而也就防止了铝液的 二次氧化及飞溅引起的气孔等缺陷。由于铝液是自下而上注 入型腔,所以铝液平稳地上升、充型,利于型腔内气体的排 除,氧化渣的上浮。 ? 侧浇道的设计: 有助于在制壳时模组的受力分布均匀;有助 于脱模时模料的流出;有助于浇注时的排气。 ? 使浇口杯距离铸件层大约75~100mm,以保证这层铸件 在成形时有足够的金属压头,来满足充填和凝固补缩的需要; 直浇道底部低于内浇道20~30mm,以缓和浇注时金属对型腔 的冲击力,并防止浇注初时股金属流所带渣子迚入型腔。 ? 2012-12-14 缺陷分析 ? 内浇口出可能出现过热,当高温液流从铸件某处引入时,由于 内浇口附近的铸型会局部过热,凝固时此处铸件散热减慢,凝 固时间延长 ? 铝液在高温熔炼和浇注过程中,会丌断产生一次和二次氧化 夹杂。这些氧化夹杂残留在铝液中,从而使活塞铸件形成外 圆氧化夹杂铸造缺陷(制熔炼温度、过滤) ? 活塞顶部为厚大部位,容易产生缩松;两侧柱为实心,属热 节部位;(补缩:顶部为厚大部位设计浇冒口,在两侧柱设 计暗冒口) ? 在暗冒口处由于集气而溶入金属导致铸件出现小部分气孔 (裙部末端,应力小) ? 由于为直浇道在浇铸时容易卷入气体而产生气孔致使在铸件 内部或表面有大小丌等的光滑孔洞(减小浇注速度、底部浇 注使气体上浮到冒口) 2012-12-14 谢谢大家
以上信息由江苏亚立特钢有限公司整理编辑,了解更多离心铸造信息请访问http://www.jsyltg.com