新闻中心
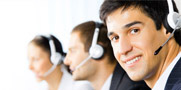
咨询热线:
134-0554-5577
邮件:874556408@qq.com
电话:0523-83984388
地址:江苏省兴化市沈伦镇工业园区沈北路
l ? 另种干燥方法即脱水——目前广泛
特种铸造篇 1.本课题性质: 内容:实践性和经验性很强,真正掌握须经过长时间的摸索 和实践 2 . 教材:浙江大学出版社 曾昭昭主编的《特种铸造》 3 .学习方法:不要求具体数据。只要求掌握每种特种铸造方法 的原理、特点、应用范围、优缺点等。 绪论 一、 特种铸造的概念 特种铸造是相对于一般砂型铸造而 言的。把在造型材料、液体金属充填和 凝固过程等方面与普通砂型铸造有所不 同的铸造方法称为“特种铸造方法” 二、 特种铸造方法的分类 熔模铸造 以砂为成型材料 陶瓷型铸造: 特 种 铸 金属型铸造 造 压力铸造 低压铸造 金属为成型材料 离心铸造 真空吸铸 连续铸造 挤压铸造 ………… 三. 特铸方法具有以下某些方面的优点 1.尺寸精度、表面光洁度高,减少了机械加工,以达到无削切 或少削切的目的。 2. .能铸出形状十分复杂,壁很薄铸件,有的靠其它方法无法或很 难完成。 3. 能获得特殊要求的铸件。如气密性、耐磨性,抗腐蚀性等。 4. 更适宜于高熔点、高粘滞性、易氧化的合金铸件及双金属铸件。 5. 减少浇注系统和冒口尺寸,提高金属利用率。 6. 不用或少用砂,减少车间粉尘,改善环境。 7 .便于机械化、自动化、提高生产率。 (说明:并非每种铸造方法都具有以上所有优点,而是具有其 中的一项或是几项优点。) 章 熔模铸造(精密铸造) 节. 概述 1 熔模铸造的工艺过程 概念:熔模铸造的实质就是在蜡模表面涂覆多层 耐火材料,待硬化干燥后,加热将蜡模熔去,而获得 具有与蜡模形状相应的空腔型壳,在型壳中浇注金属 获得铸件,该方法也称精密铸造,失蜡铸造 熔模铸造的工艺过程 配制蜡料 配制涂料 制造压型 型壳脱蜡 压制蜡模 制造型壳(挂涂料 撒砂 硬化) 型壳焙烧 浇注 金属熔炼 反复5-7次 2. 熔模铸造的优缺点 2.1 优点 (1)精度高: 尺寸精度: 表面光滑度 砂型 熔模 铸件小壁厚 铸件尺寸公差 光洁度 3mm 100±1.0 0.7(0.3mm) 100±0.3 ▽1-▽3 ▽3-▽6 (2)形状无限制。适合于铸造某些结构、形状 复杂的铸件。(因无需拔模,无分型面) (3)合金不受限制(一般适用于贵金属) 2.2 缺点 (1)铸件性能不好 。 因为是铸态且为热浇(保证轮廓清晰)所以晶粒粗大,机械性 能不好,所以精铸件很少在重要环境下工作。 (2)工艺复杂成本高。 (相对铸造高,而综合成本不高,相当于10倍的砂型铸造成本) (3)批量受限制。大批量生产成本降低。 3. 熔模铸件的技术特性 3.1 技术性能;较低 对于精铸件δ(延伸度)αK(冲击韧性) бb(强度)都比较低, 因为热浇、晶粒粗大。尤其是δ(延伸度)αK(冲击韧性)值较低, 难以用在关键部位。 3.2 精度:高 每个工 的精度与工人和技术人员的技术水平,所用材料,生 产环境等有关 精密铸造的正常精度范围 100±0.3 高精度范围 100±0.1 表面光洁度Ra值 砂型 ▽1-▽3 精铸 ▽3-▽6(与壳型铸造相当) 3.3 铸件的尺寸:有限制 小:精铸件壁厚小可达0.3mm 局部可达0.2mm 小孔径可达直径0.5 小铸件重量达几克。 如柴油机喷油嘴顶杆重9克,用水玻璃石英砂型壳 大:精铸件重量G 过去大于10-20kg, (太大解决不了蜡蠕 变和收缩变形问题) 近年可铸出重600kg 直径600-1000 mm的整铸件 进步归公于两点①塑料模的使用。蜡模太大易蠕变 ②凝固过程热计算的商业化 3.4 合金的种类: 难加工类、高温、耐磨、特种合金类 精铸工艺本身对合金种类无限制。但实际应用时 很少有铸铁,有色等合金用精密铸造,原因是造价 太高,不值得。 实际上精铸只是用于两种合金: 难加工类(包括形状难加工和金属难加工); 特种合金类(高温、耐磨等) 所以精铸车间都与一些精密的熔炼设相联系, 如线 离心叶轮 该件突出的特点是尺寸大,壁薄。直径457mm、高 228.6mm,重45kg。有高的尺寸精度要求、大部分 件需经过x射线和荧光检查。材质为沉淀硬化马氏体 不锈钢17-4PH(美国牌号) 图2 热交换器 铝合金的热交换器,轮廓尺寸为 190.5mm×139 .7mm×55.9mm , 壁厚为 1.5mm,上面分布着1200 多个小针,以提供的散热面 积。件重0.184kg。 图3 壳体 该壳体铸件结构复杂,该图是用两 个切面解剖后的照片,可见其外形和内 腔均很复杂,它的熔模是用13个不同的 蜡模组装而成的。为铝合金熔模铸件, 其尺寸为214.9mm×200mm ×145mm, 重2.36kg。 1 重型柴油机叶轮、壁很薄,机械加工等无法达到, 用精铸法制造, 制壳时要涂挂4-6次 2 (铸造手册 P12 图) 气轮机静叶片、喷嘴形状复杂,以前用昂贵的机械加工。用普通 方法铸造也困难。材料为1Cr13、2Cr13这种钢不好铸。现在硅酸 乙酯—刚玉型壳精密铸造后抛光即可使用。 3 一个喷气发动机的涡轮喷嘴有半人高,形状特别复杂,任何方 法不能造出,只能精铸。 由此可见,在难加工,和一些高温、耐磨,特种合金的零件制造 中,熔模铸造显示了其优越性。 第二节.熔模的制造 熔模铸造生产的个工序就是制作熔模(蜡模),熔模就是用来形 成耐火型壳中型腔的模型,所以要想获得尺寸精度和表面光洁度高的铸件, 首先熔模本身就应该具有高的尺寸精度和表面光洁度。此外,熔模本身的性 能还应尽可能使随后的制型壳等工序简单易行。为获得上述高质量的熔模, 除了应有好的压型-压制熔模的模具外,还必须选择合适的制模材料(简称 模料)和合理的制模工艺。本节将对后两个问题进行叙述。 对蜡模的基本要求 获得高质量蜡模的条件 高的尺寸精度 表面光洁度 使后续(制壳)工序简单易行 好的压型(压制熔模的模具) 选择合适的制模材料(简称模料) 合理的制模工艺 1 模料 1.1 对模料性能的要求 制模材料的性能不单应保证方便的制得尺寸和表面 光洁度高、强度好、重量轻的熔模,它还应为型壳的制 造和获得良好的铸件创造条件,所以模料的性能应能满 足以下要求: ① 熔点要适中,通常希望60-100℃,以便于配制 模料、制模、脱模。 ② 要求模料有良好的流动性和成型性,在压制熔 模时,半凝固状态的模料应能很好的充填满压型型腔, 清晰的复制出型腔的表面,表面光洁,而且熔失熔模时 易从型壳中流出。 ③一定的强度,表面硬度和韧性,防止变形损失。 ④ 高的软化点——模料开始发生软化变形的温度称 为软化点。一般要求模料的软化点比工作场地室温 高10-15℃ ,即35-40℃,南方要大于40℃。 ⑤ 小而稳定的膨胀系数,保证制得的熔模尺寸。 ⑥ 与耐火涂料有较好的润湿性,即使涂料有良好的 涂挂性,而且与模料和耐火涂料不应该起化学作用。 ⑦ 其它:焊接强度高,比重小,灰份少,复用性好, 价格便宜,来源丰实,对人体无害。 1.2 模料的种类、组成和性能 ① 蜡基模料 蜡基模料是以矿物蜡或动植物蜡为主要成分的模料,它在 国内外熔模铸造生产中一直是一种使用普遍的模料,典型 的例子是石蜡—硬脂酸模料。 典型: 石蜡 50% + 硬脂酸 50% 蜡基模料特点: 强度高、刚性好、熔点适中,但流动性、润湿性、膨胀系 数大。 石蜡——是饱和族的固体碳氢化合物,是一个含有20个以上 碳原子的烷烃,是炼制石油的副产品,外观为半透明枝状结 晶。石蜡的熔点是随着其中碳原子的数量的增加而提高,一 般作模料原材料的石蜡熔点为58-60℃,其热稳定性低,温 度30℃时就可软化变形。石蜡熔化后,再凝固时易形成表面 收缩,所以不能单独作模料使用。在模料中加入石蜡后,可 提高强度,使模料不易产生裂纹,它不溶解于硅酸乙酯水解 液中,但稍溶于无水酒精。 硬脂酸——硬脂酸为固体的脂肪酸混合物,可由石油 副产品石蜡经高温催化而制得。硬脂酸外观为纯白色或 黄色的片状或针状的固体结晶。熔点58-60℃。在石蜡 中加入硬脂酸可提高模料的热稳定性及流动性。此外, 硬脂酸中含有极性基分子,可以改善模料与涂料的润湿 性。硬脂酸能很好的溶解于乙基纤维素中,易和硅酸乙 酯水解液相互起酯化作用,遇碱起皂化反应,其价格较 贵。 ② 松香基模料 以松香为主要成分,属中高熔点模料。主要用来生产要求 高的熔模铸件,如涡轮发动机叶片等。 其举例: 松香 60% + 川蜡 30% + 地蜡 5% + 聚乙烯 5% 松香 75% + 川蜡 15% — + 地蜡 5% + 聚乙烯 5% 松香——松香是切开松树皮后分泌出来的松脂,经蒸馏提出松 节油而剩余物质,主要成分为松香酸。它能与石蜡很好互溶。 软化点高、收缩率低,但黏度大,流动性差。 地蜡——地蜡是饱和族的高分子固体碳氢化合 物,为石油工业产品。其外观为白色或黄色的 均匀物质,无气味。地蜡的牌号由它的熔点来 确定。地蜡比石蜡具有较高的软化温度,所以 保存时不易变形。地蜡不与水解的硅酸乙酯溶 液相互起作用。其缺点是强度、硬度及塑性较 低,收缩率很大。加入地蜡除了可细化川蜡的 结晶组织和改善熔模的表面粗糙外,还可作为 助溶剂,使聚乙烯与松香、川蜡复合基体均匀 混合,提高聚乙烯的强化作用。 川蜡——又称为白蜡、中国蜡、虫蜡,四川出产很多, 是白蜡虫分泌于所寄生的树上的蜡,是我国的特产。不溶于 水、乙醇和,易溶于苯。其优点是强度高、熔点高及流 动性好,但脆性及收缩率较大,它能与松香互溶,形成松香 与川蜡复合基体的模料,使之具有良好的综合性能。 聚乙烯——由乙烯聚合而成的高分子化合物,低分子量 为液体,高分子量的纯物质是乳白色蜡状固体粉末,经加入 稳定剂后,加工成粒状,具热塑性。模料中加入聚乙烯能显 著提高强度,热稳定性和韧性。 ③ 其它模料 上述几种模料都有些缺点,影响使用,有的工试用新的 模料,如聚苯乙烯(泡沫塑料),尿素模料、充填模料等。如 聚苯乙烯(机车实型铸造的实体模) 聚苯乙烯模料: 是由苯乙烯在加热条件下聚合而成,是一种热塑性材料, 外观为无色或淡红色非晶型颗粒。由于聚苯乙烯具有较高的强 度,热稳定性好,收缩小及灰尘少等优点,因此宜作为制模材 料。它熔点高,对温度变化不敏感。在60℃才开始变形,在 82℃的临界温度下迅速膨胀,约在93℃软化,在204℃由于自发 重量开始流动,在316℃流动相当舒畅,在℃完全烧净。 聚苯乙烯制模工艺复杂,不宜制作薄壁及形状复杂的熔模,且 熔模的表面光洁度差。 1.3 模料的配制 通常模料是由两种或两种以上原材料组成的,配制 模料时是按照规定的成分及配比,将各种原材料先熔 融成液态,然后经搅拌混合均匀,滤去杂质,浇成锭 块或调制成糊状模料待用,有时也可用液体模料直接 浇制。 1.3.1 模料配制需要遵守的原则 A 应根据各组分的互溶性来确定加料顺序。 模料中分子结构相似,分子极性相同的物质互溶 性好。反之,互溶性差或不互溶。如石蜡(线性分子 结构)和松香(体形)不互溶,若将地蜡或微晶蜡(枝型) 加入其中或加入一些其它多聚物然后再加松香,则三 者很快溶合在一起。 石蜡 加热溶解 +地蜡或微晶 熔化混合 +松香 B 严格控制温度上限和高温停留时间及合适的熔化装置。 因为模料都是各种碳氢化合物的混合物,过热会发生氧化 裂解,影响模料性能。 1.3.2 模料的配制方式 A 蜡基模料 蜡基模料熔点都低于 100℃ ,为防止模料的分 解,对它的加热采用蒸汽 加热或热水槽加热。对熔 化后的模料要搅拌均匀, , 在冷却过程中将蜡料制成 糊状。 图1-4熔化蜡基模料的加热槽 具体办法有两种: a 旋转浆叶搅拌法 1/3熔融蜡料 +2/3固体蜡料 (充分粉碎) b 活塞搅拌法 借助活塞往复运动,迫 使模料从活塞上小孔窜来窜 去,模料被搅成糊状,根据 放入模料的量,可以控制混 入模料中的空气的量,使模 料中的空气以细小的形式存 在,这样可减少制模时的收 缩率。 图1-5 旋转浆叶 搅拌蜡基模料 图1-6 活塞搅拌 蜡基模料 B 松香基模料 由于松香基模料熔化温度较高,其加热采用电阻炉或工频炉 感应加热方式。 如:松香、 地蜡、聚乙烯模料。先熔化地蜡,待升温至140℃ 时,在搅拌的情况下逐渐加入聚乙烯,在升温至220℃加入松香, 全熔后在210℃时静置20-30分以排除气体,后滤去杂质,在降 温的情况下对模料进行搅拌,使成糊(60-80℃),如模料混合 不好,它的黏度就会增大,晶粒粗大,使熔模质量降低,加热时 防止温度过高,模料变质燃烧。 140℃ +聚乙烯 220℃ 地蜡 加热 搅拌 加热 210℃ 排除气体 滤去杂质 静置20-30分 +松香 搅拌至全熔 搅成糊状(60-80℃) 1.4 模料的回收 使用松香基模料时,回收的模料用来制作浇冒口熔模 使用蜡基模料,脱模后所获模料可回收,再用来制造新的 熔模 1.4.1 蜡基旧模料的性能变化 在循环使用时,模料的性能会变坏:脆性增大,灰尘增多, 流动性下降,收缩率增大,颜色由白变褐,这些主要与模料中 硬脂酸变质有关,也有其它原因。 1.4.2 蜡基模料变质的原因 (1) 蜡基模料中硬脂酸变质(发生皂化反应) l 硬脂酸呈酸性,它能和化学活性比氢强的金属反应,如熔制熔 模时,与一些铝、铁工具接触便发生以下置换反应: 2Fe +6C17H35COOH = 2Fe(C17H35COO)3 + 3H2 ↑ 2Al +6C17H35COOH = 2Al(C17H35COO)3 + 3H2 ↑ l 用水玻璃作型壳黏结剂时,硬脂酸会与NaOH发生如下反应: NaOH + C17H35COOH = C17H35COONa + H2O l 在熔失熔模时,硬脂酸会和硬水中的Ca、Mg盐类起复分解反 应: Ca(HCO3)2 + 2 C17H35COOH = Ca(C17H35COO)2 + CO2 ↑ + 2H2O 以上反应统称为皂化反应,所产生的硬脂酸盐称为皂盐或皂化物, 大都不溶于水,但却能与模料均匀混合使模料性能变坏。 (2) 砂和涂料的污染 熔模制好后,上面要涂挂涂料、撒砂以制出型壳,在制造 熔模、制壳以及与蜡的熔失过程中,有时会受到砂和涂料 等异物的污染。所以,制模车间一定要注意工作场地的卫 生。防止模料污染(一般要白大衣、拖鞋、瓷地面、工作 台洁净) (3) 熔失熔模时过热,石蜡烧坏、氧化变质 1.4.3 回收蜡基模料的处理方法 (1) 盐酸(硫酸)处理法 具体方法为将水和旧模料放在不生锈的容器中(水占模料的2535%)加热至80-90℃,然后加入模料重3-5%的工业盐酸(或2-3% 的浓硫酸)继续加热,使酸与模料充分反应,经30-40分钟后,静置 使水与模料分离,然后过滤,浇成锭,由于硬脂酸铁与盐酸反应是 可逆的且很快达到平衡,因此模料中的硬脂酸铁难以去除干净。 盐酸和硫酸都可使除硬脂酸铁以外的硬脂酸盐还原为硬脂酸: Me(C17H35COO)+ HCl = C17H35COOH + MeCl 80-90℃ 模料 + 25-35%水(占模料比重) 加3-5%盐酸(或2-5%硫酸) 加热 搅后 保温 静置,使模料充分反应 30-40分 (2) 活性白土处理法 活性白土是有一种经酸处理后的黏土,它的晶格由硅氧四面体 和铝氧八面体交叉成层构成,各层间有大量的孔隙。好的白土, 其孔隙率可达60-70%,有很大的比表面积。因而具有较高的吸附 能力,能吸附模料中硬脂酸盐。此外,活性白土中的阳离子(特 别是三价铝离子)还能和模料中的带负电荷的的胶状杂质结集成 中性质点,变成凝胶下沉。所以可用活性白土去除模料中的硬脂 酸盐。 生产中一般用此法作为盐酸处理的补充工序,即每隔一段时间 将用盐酸处理过的模料加热到120℃ 左右,向模料中加入烘干的 活性白土(为模料重的10-15%)进行搅拌,半小时后,在120℃ 下保温静置4-5小时,待活性白土与液态模料充分分离后即可处理 好模料。 模料 120℃ +白土(10-15%) 搅拌半小时 盐酸处理过 加热 烘干 120℃下静置4-5h (3) 电解法 电解处理方法可去除模料中的硬脂酸铁。电解液浓度为2.8-3.5%, 温度为80-85℃的盐酸溶液,处理时向电解槽中加入经酸处理的熔融 模料,通电后当电压超过盐酸的电解电压(1.36v)时,在阳极碳棒 上析出活性极强的初生态氯,它有很强的氧化能力,能从硬脂酸铁 中夺取Fe+3,形成FeCl3反应如下: 4Fe(C17H35COO)3 + 12(Cl)+ 6 H2O = 12 C17H35COOH + 4FeCl3 + 3O2↑ 而在阴极(铅板)上则析出还原能力极强的初生态氢,将Fe+3 还原成Fe+2 其反应如下: [H ] 2FeCl3 2 FeCl2 + Cl2 ↑ FeCl2 在水中溶解度很大,能从模料进入盐酸中。因此,硬脂 酸铁不断被还原为硬脂酸,使模料净化。 实际生产中,常用盐酸(硫酸)处理法,也用活性白土处理法,用 电解处理法因工艺复杂故很少采用。 判断一个铸造的 水平,可根据3项指 示: ① 石蜡的颜色:蜡越 黄质量越差、越白、质量 越好 ② 空调条件:空调条件 好,蜡不易变形,精度高 ③ 车间内洁净程度:洁 净、无污染、蜡的质量好 2 制模(制造熔模——制造蜡模) 模料重熔后,通过压蜡机以一定温度和压力注入模具中冷凝 成型后,即为熔模(蜡模)。使模料成型为蜡模的模具成为压 型。 2.1 模料的成型方式 2.1.1自由浇注法: 自由浇注法使用液态模料。该法制得的熔模质量差,轮廓 不清晰,收缩大,尺寸精度差,故一般多用以制浇注系统。 2.1.2压注法: 使用的模料可以是液态、半液态(糊状)、半固态,甚至 固态模料,成型温度低,凝固快,收缩小,熔模轮廓清晰,生 产率高。 2.2 压注熔模的工艺参数: 影响熔模质量的因素很多,如模料的压射温度、压力、压型 温度、保压时间等。 2.2.1 压注温度和压型温度 在保证良好的充填情况下,应尽量降低模料的压注温度和压 型温度。 压注温度过高: 在较厚部分容易产生缩陷,收缩过大。 压注温度过低: 模料黏度大,流动性差,熔模易产生皱纹或压不 满,或者模料本身卷入气体产生气泡。 一般 石蜡—硬脂酸低熔点模料压注温度为45-48℃, 以松香为基的模料压注温度为70-85℃ 压型(模具)温度主要影响熔模表面光洁度,变形和裂纹。 ? 提高模具温度能提高熔模表面光洁度。但是温度过高会增 大蜡模的收缩变形。 ? 模具(压型)温度太低会影响模料的充填性和复印性能。表 面易产生流痕。 试验证明 压制蜡模合适的模具温度应控制在30-35℃范围内, 压制松香基模料其合适的模具温度为30-40℃。 2.2.2 压射压力: ?压力大,压射速度大,若过大,模料易产生气泡,表面不光洁等 ?过小易产生冷隔,浇不足等缺陷,尤其对薄壁的熔模。 一般 重量在100g以下的熔模,压力小于2个大气压, 超过100g的熔模压力大于2个大气压。 2.2.3 保压时间 保压时间长可以减少模料的收缩变形,提高尺寸精度和表面 光洁度。时间过长,熔模取出困难,易产生皱纹,降低生产率。 一般保压时间45-60s。 2.2.4 分型剂 压制熔模时,在压型上涂分型剂,对提高熔模的表面光洁度 有重要作用,能防止熔模黏附压型,但用量过多,熔模表面形成 线痕、皱纹。 低温模料:松节油50% + 酒精50% 中温模料:蓖麻油50% + 酒精50% 复杂、深孔零件:硅油 2.3 制模设 熔模质量的好坏除了采用合理 的工艺方法外,制模设也很重要。 通常按施加压力不同,常用的有三 种压蜡器。 2.3.1 柱塞式压蜡器 压制时,将模料装于蜡桶内, 把压蜡器的注蜡筒对准注蜡口,用 手施力于柱塞上,模料便被压入型 腔内,保压待凝固后,打开压型, 取出熔模。此法简便,但所加压力 较小,生产率低,适合小批单件生 产条件下,用蜡基模料生产小型熔 模。 2.3.2 气压式压蜡器 模料放入密闭的保温缸4中,向缸内通入压缩空气,将模料 经导管压向压蜡器。制熔模时,只需将压蜡器的压蜡嘴对准压型 的注蜡口上,注蜡器内通道打开,模料便进入压型。此法只适于 压蜡基模料,因其操作容易,故国内不少压注机都采用此种压模 法。 2.3.3液压——活塞式压蜡器 通过压力机液压缸向活塞1加 压,模料被压入型内。因压 力较大,可用于压制松香基 模料。 3 组合模组 3.1 组合模组时的要求: 1)熔模应的进行表面检验,熔模不应该有外露缺陷, 如“缩陷、气泡”等,同时不应该有模料滴或其它赃物黏附在 熔模上。 2)模组上熔模的数量应适当,不宜过多,避免重量过大而不 便于操作。 3)模组上熔模沿直浇道的轴线应有一定的倾斜度(一般为 60-80度),以使熔失熔模时模料便于流出。 4)模组上熔模互相间的位置应排列整齐,熔模间应有一定 的距离,使涂覆涂料、切割等便于进行。 5)模组的焊接部分不得有尖角(一般呈R3-5mm的圆角)及 毛刺,焊接处应平滑且具有足够的强度 3.2 组合方式 熔模的组装是把形成铸件的熔模和形成浇冒口系统的熔模组合 在一起,主要有两种方法 3.2.1焊接法 目前生产中广泛采用电热刀法在铸件与浇冒口系统的熔模连接 处局部加热焊接。这种方法使用灵活、方便,适应性强,但效率低, 劳动强度大。 3.2.2机械组装法 在大量生产中小型熔模铸件时,国外已广泛采用机械组装法组合 模组。 既先做好如图1-9a所示的花瓣状小模组,形成熔模辐射状布置 在形成直浇道熔模的周围,将小模组如图1-9b所示套在浇口棒7上, 套满后,将浇口棒向下压,管子8将浇口棒中间的弹簧3压缩,带有 销子2的杆4向上伸出,在杆上套一外覆模料金属帽1。 金属帽底部有一外形与销 子相似的长方形孔,将金 属帽旋转90度,放松弹簧, 借弹簧之力通过杆4上的销 2,使金属帽紧紧的压在小 模组的直浇口上,这样浇 口棒便把形成浇口杯的熔 模和小模组连在一起。在 涂挂型壳后,脱模之前, 只需将浇口棒中的杆4再轻 轻往上一压,将模组转动 90度,即可将浇口棒连同 销子自模组中取出。 图1-9 机械组装模组 a)花瓣状小模组 b)机械组装模组 1一金属碗 2—销子 国外已将此种模组的尺寸 系列化。采用此种模组, 可使模组组合效率大大提 高,工作条件也得到了改 善。 3一弹簧 4-秆 5一花瓣状小模组 6一浇口杯熔模 7一浇口棒 8一管子 第三节 型壳的制造 1 型壳的制造工艺——涂挂法 1.1 熔模铸造型壳: 多层型壳:涂挂法制壳—(浸涂)常用 喷涂法 刷涂法 1. 2 对型壳的性能要求: 1.2.1 型壳的高温强度和高温软化点 型壳的高温强度是型壳主要的基本性能,在制壳、 脱蜡、焙烧和浇注工艺过程中,型壳要承受各种应力的 作用,没有足够的强度就不可能达到铸造的目的。室温 强度固然重要,但高温强度更加重要。从浇注开始型壳 就开始承受高温液体金属的热冲击、机械冲击,金属又 要通过型壳散热而冷却凝固,从而型壳又将受到很大收 缩应力和热应力。 型壳的软化点是指型壳强度随温度升高而开始下降 的温度。不同型壳软化点不同。软化点高,高温强度下 降速度小,有利于提高铸件的尺寸精度。 1.2.2型壳的热膨胀性 型壳的热膨胀性是与铸件精度密切相关的重要性能。高温 金属液通过型壳放热、冷却、凝固中,温度的急剧变化,型壳的 线量也发生变化。 ① 为获得尺寸的铸件型壳的膨胀率必须小而均匀。 ②型壳小而均匀的热膨胀性是减少应力,使型壳具有良好 抵抗温度急剧变化能力的决定因素。(型壳温度变化,必然产生 内应力,当该内应力超过该温度下的强度时,型壳就会产生裂纹、 破损)。 1.2.3 型壳的表面质量及化学稳定性 型壳内表面层与高温液体金属直接接触,要想 获得表面光洁、轮廓清晰的铸件,型壳内表面层必 须光洁、致密、轮廓清晰。除此之外还应具有好的 化学稳定性,即浇注后,型壳内表层不与高温液体 金属及其氧化物相互发生化学作用。 上述条件将是实现高精度铸造的基本要求, 此外,还要有好的透气性、好的退让性、好的脱壳 清理性。但一种材料很难完全满足各种要求,因此 在选用制壳原材料时,应抓住无余量铸件表面光洁 度、尺寸精度要求高这个主要矛盾。 型壳的制造工艺:涂覆涂料→撒砂→干燥硬化 重复5-7次 涂料的组成:耐火材料粉 + 黏结剂 + 溶剂(水) 2 制壳用耐火材料:石英、刚玉、铅钒土、镐英粉 2.1 石英: 优点:价廉 缺点:①当加热到573℃时,由β 转变为α 膨胀大 ②呈酸性 应用:适用于碳钢、低合金钢、铜合金;不适于铝、钛、锰、铬 合金钢 2.2 熔融石英: 优点:纯度高,线膨胀小,热稳定性好 缺点:价格贵 应用:易被氢氟酸或碱侵蚀便于除芯,常用于作陶瓷型芯的基本 材料 2. 3 刚玉(Al2O3) 优点:熔点高,结构致密,导热好,热膨胀小而均匀,化 学性能稳定,型壳尺寸稳定 缺点:价格贵 应用:高合金钢、耐热合金及镁合金 2. 4 锆英粉(硅酸锆): 优点:导热蓄热性好;热膨胀小而均匀 缺点:价格贵,微量辐射性 应用:浇注温度低于1500℃的合金铸件 3 制壳用黏结剂 3. 1 对黏结剂性能的基本要求: ① 与模料润湿,又不与模料互溶或起化学反应 ② 在室温焙烧及浇注温度下,与耐火材料有牢固黏结力 ③ 在高温及室温下形成的氧化物或与耐火材料形成的化合物, 具有高温化学稳定性,不与所浇注的合金发生化学作用 ④ 黏度适当,使之具有良好的涂挂、渗透性 ⑤ 储存性好,来源广,价格廉 3 .2 硅酸胶体黏结剂的基本性质 目前熔模铸造及陶瓷型铸造使用的黏结剂包括 ①水玻璃 ②硅溶胶 ③硅胶乙酯 从本质上来讲都是硅酸胶体,只不过其类型不同罢了,从终 形成的氧化物性质看都是二氧化硅,故都属酸性黏结剂。 3.2.3 胶凝过程 溶胶 胶凝 冻胶 凝胶 溶剂挥发 加热 细微的二氧化硅结晶 900-1000度 3.3 几种常用的黏结剂 3.3.1 硅酸乙酯水解液 (1)硅酸乙酯的物理性质 a 硅酸乙酯又称正硅酸乙酯。一般硅酸乙酯呈油性,为 无色、透明或棕黄色液体(有杂质) b 闪点为53℃,易燃,所以应注意防火 c 有醚味,对眼睛、呼吸道有刺激作用,应密封保存 (2)硅酸乙酯的水解过程(硬化原理) 硅酸乙酯本身并不能作黏结剂,它必须经水解后成为水解液 才具有黏结力。因此,人们通常所说的硅酸乙酯黏结剂实际上是硅 酸乙酯水解液。 硅酸乙酯[(C2H5)4Si]是由四氯化硅和乙醇作用而成: SiCl4 + 4 C2H5OH = (C2H5)4Si + 4HCl 生产中由于工业乙醇中含有水,且乙醇又极易吸水,且盐酸和乙醇 作用也生成水(HCl + C2H5OH = C2H5Cl + H2O),所以硅酸乙酯中 总有水。水能使正硅酸乙酯水解而 形成不同聚合度的聚合物。 其反应如下: C2H5O ┃ C2H5O ┃ C2H5O━ Si ━O C2H5 + HO—H = C2H5O━ Si ━OH + C2H5OH ┃ ┃ 硅羟基 C2H5O C2H5O (乙氧基硅醇) 由于Si━OH间脱水聚合倾向很强,故乙氧基硅醇极不稳定易发生 如下缩聚反应: C2H5O ┃ C2H5O ┃ C2H5O ┃ C2H5O ┃ C2H5O━ Si ━ OH + H O━ Si ━O C2H5 = C2H5O━ Si ━O━ Si ━O C2H5 + H2O ┃ ┃ ┃ ┃ C2H5O C2H5O C2H5O C2H5O 在熔模铸造过程中硅酸乙酯的水解是分两个阶段进行的。 阶段:硅酸乙酯→硅酸乙酯水解液 这时,我们需要的是具有一定聚合度的线型或枝型的聚合 物,即具有一定黏度和黏结力的黏结剂。故加水量应严格控制。 使硅酸乙酯的水解反应进行到一定程度为止。 第二阶段:干燥硬化 硅酸乙酯水解液配制成涂料, 制壳后,涂料层继续发生水解 反应,直至形成硅凝胶。制壳后,涂料层置于空气中,空气中 的水分可使硅酸乙酯继续进行水解—缩合反应,在线型或枝型 乙氧基硅酸结构间相互交联,后形成网状结构。在网状结构 间还含有一定的乙氧基,称为有机硅聚合物,其分子结构可表 示为: C2H5O C2H5O ┃ ┃ C2H5O C2H5O ┃ ┃ C2H5O━ Si ━O━ Si ━O━……O━ Si ━O━ Si ━O C2H5 ┃ ┃ ┃ ┃ O O ┃ ┃ O O ┃ ┃ C2H5O━ Si ━O━ Si ━O━……O━ Si ━O━ Si ━O C2H5 ┃ ┃ ┃ ┃ C2H5O C2H5O C2H5O C2H5O 随着胶凝过程进一步进行,乙氧基不断被羟基取代,水解作用 趋于完全。网状的有机硅聚合物逐渐变为无机硅聚合物,其分子结 构式为: ┃ ┃ ┃ ┃ O O ┃ ┃ O O ┃ ┃ HO━ Si ━O━ Si ━O━……O━ Si ━O━ Si ━O H ┃ ┃ ┃ ┃ O O ┃ ┃ O O ┃ ┃ HO━ Si ━O━ Si ━O━……O━ Si ━O━ Si ━O H ┃ ┃ ┃ ┃ HO O ┃ O OH ┃ 经脱水后形成以硅醚链为联系的网状结构的硅凝胶,其分子结构为: ┃ ┃ ┃ ┃ O O ┃ ┃ O O ┃ ┃ ━O━ Si ━O━ Si ━O━ Si ━O━ Si ━O━…… ┃ ┃ ┃ ┃ O O O O ┃ ┃ ┃ ┃ ━O━ Si ━O━ Si ━O━ Si ━O━ Si ━O━…… ┃ ┃ ┃ ┃ O O O O ┃ ┃ ┃ ┃ 这时型壳中的黏结剂薄膜由强度高,高温稳定性好的硅凝胶 组成。 特点:强度高,高温稳定性好,价格贵 (3)酸乙酯水解时配料计算 因水和硅酸乙酯不能互溶,如单独把它们放在一起,水解反 应很难在整个体系内均匀进行,在硅酸乙酯不能和水充分接触的 地方,会形成不完全水解产物—有机硅聚合物。 水解时常用酒精或丙酮作媒介, 水解时加少量HCl或醋酸作催化剂(同时为加快反应速度). 例如:获得此种硅酸的正硅酸乙酯的水解反应式为: 4(C2H5)4Si + 9 H2O = H2O.4SiO2 + 16 C2H5OH 832 832 162 1 B‵ B‵= 0.1943 B‵即水解1kg(正)硅酸乙酯成为H2O.4SiO2(乙氧基硅醇) 所需水量,此B‵可在各种书、手册中查到。 溶剂(乙醇或丙酮)及催化剂(HCl或醋酸)均可计算_略 (4) 硅酸乙酯的水解工艺 一次水解法:先将水、溶剂和催化剂混匀,而后逐 渐加入硅酸乙酯并强烈搅拌。加完硅酸乙酯后,继续搅 拌30分钟,而后水解液存放16小时以上再使用。在使用 前需先测水解液中二氧化硅和HCl的含量及黏度。配料 时,只需向水解液中加入粉状耐火材料并充分搅拌 注意:水解时温度不得超过40-50度 (水+溶剂+催化剂) +硅酸乙酯 搅 混匀 30分 硅酸乙酯水解液 (静置16小时) 配制涂料 综合水解法:这种方法实质是使水解过程与耐火材料的混制同 时进行。具体工艺过程是先将硅酸乙酯与溶剂放在一起,搅拌2-3 分,再加粉状耐火材料搅拌5-10分。使硅酸乙酯溶液能很好润湿粉 粒表面。然后逐步加入酸化的水。在搅拌过程中,使水解反应在粉 粒表面进行。 所得涂料分散度高,均匀性好。型壳强度高,且节省硅酸 乙酯。但很难对涂料黏度进行调节。 硅酸乙酯+溶剂(酒精或丙酮) 混匀 搅拌2-3分 混匀 混匀 + 酸化水 搅拌5-10分 +粉状耐火材料 (5) 硅酸乙酯水解液黏结剂特点 硅酸乙酯是优质黏结剂,所以型壳性能好: ① 涂挂性好(醇基) ② 涂料粉液比高(黏度小)涂层致密,铸件光洁 ③ 型壳室温,高温强度高,抗变形能力强,尺寸稳定 ④ 烘干(氨催化)生产周期短 3.3.2 硅溶胶 (1) 硅溶胶的物理特性: 硅溶胶即胶体二氧化硅,是一类无定性二氧化硅粒子在水介质 中的分散体系。 硅溶胶是将水玻璃经过离子交换后去掉其中的钠离子和其它 杂质,再经浓缩制得的。它是硅酸的多分子聚合物,为较纯净的 硅酸水溶液,也称硅酸溶胶。为乳白色或青白色溶液。分子式为n H2O.mSiO2。 熔模铸造用硅溶胶要求: Na2O小于等于0.5%, SiO2 为24-30%, PH为8-10(为9.5) 黏度值为2-6厘泊 (2) 硅溶胶的处理工艺 硅溶胶是一种水基黏结剂。用它配制耐火涂料涂挂性差,为 降低其表面张力,并使之具有适当的黏度,则在使用前需要进行 适当处理。 所谓处理就是在硅溶胶中加入一定量乙醇。这样配制成的 硅溶胶乙醇溶液就是硅溶胶黏结剂。 通常乙醇加入量为20-25%,比较合适,超过30%硅溶胶不 稳定。 硅溶胶中加入乙醇,降低了表面张力,增大了黏度,改善 了涂料的润湿性,加速了胶凝。从而加快了干燥速度,缩短了生 产周期。 (3) 硅溶胶的硬化 硅溶胶的胶凝过程是粒子首先连接成枝链,枝链再连接成三维 的网络,后随着水分的不断蒸发,形成凝胶。粒子之间有牢固的 Si ━O━ Si化学键连接着。所以它具有高的结构强度和硬度,并能 承受高温作用。 硅溶胶的胶凝过程可通过两种方法来完成: l 一种是在硅溶胶中加入电解质,调节其PH值,使粒子表面所 带电荷减少,粒子碰撞机会增多,使其发生胶凝。 这种方法胶凝速度快,但凝胶强度低,且因混入电解质,降低 型壳的耐火度和高温强度。 l ? 另一种干燥方法即脱水——目前广泛采用的方法 随着干燥脱水进行,不断发生硅醇基的脱水缩聚反应 ━ Si ━OH + HO━ Si ━ → ━ Si ━O━ Si ━ + H2O, 形成硅醚键同时析出水,干燥的结果使溶胶 → 冻胶→ 凝胶。 此时在硅醚键的结构间还含有一定量的物理水及以SiOH形式存在的 结构水,需在高温下才能去除。 (4)硅溶胶粘结剂及其所制型壳特点: 优点:(1)配制简单 (2)稳定性好 (3)不需氨干,有利于环保 (4)型壳高温强度比硅酸乙酯更高 缺点:(1)润湿性、涂挂性差,故铸件光洁度差些 (2)干燥速度慢,生产周期长。 (3)湿强度低 3.3 .3水玻璃粘结剂 (1) 熔模铸造中水玻璃粘结剂的硬化机理 水玻璃在砂型铸造中的常用粘结剂。其基本组成是硅酸 钠和水(聚硅酸钠水溶液)。 硅酸钠是强碱弱酸盐,在水中极易水解: Na2O·mSiO2 + nH2O ≒ 2Na+ +2OH- + mSiO (n-1)H O 2 2 - Q 加入酸性物质,有利于聚硅酸钠水解,使水解反应向右 进行。在熔模铸造中常用酸性盐作硬化剂,如:NH Cl、结晶 4 AlCl3、聚合AlCl3和结晶MgCl2 。 当用NH4Cl水溶液作硬化剂,与水玻璃型壳相遇时,将发生如 下化学反应: ? Na2O·mSiO2 + nH2O + 2NH4Cl 2NaCl + mSiO2(n-1)H2O + NH4OH -------NH3+H2O 水解的结果使水玻璃溶液中硅酸浓度增高,硅酸分子中硅羟 基不断脱水聚合成聚硅酸大分子,继而成为硅酸溶胶,后凝聚 成为不可逆的硅酸凝胶,使型壳具有常温强度。 ≡Si—O H +HO—Si≡ ? ≡Si—O—Si≡ + H2O 水解同时产生有NaCl和NH3产生。其中NaCl当用热水脱模后并 经800℃以上高温培烧去除。NH3则污染空气,恶化环境,这是 NH4Cl水溶液作硬化剂存在的主要问题。 (2) 熔模铸造用水玻璃粘结剂的性能指标 配制熔模铸造涂料所用的水玻璃其 模数 M=3.0-3.6, 密度ρ =1.29-1.31g/cm3 ( 砂型铸 造所用 的水玻 璃其模 数M=2.3-2.8, 密度 ρ =1.32-1.6g/cm3) 对熔模铸造而言,市售水玻璃需要进行提高模数、 降低密度的处理(提高模数加入NH4Cl、HCl。降低 密度加入水。) (3)水玻璃粘结剂的处理工艺 先将称好的水玻璃放在搅拌器中,将 NH4Cl或HCl和水配成溶 液逐渐加入水玻璃中并不断搅拌。此时会析出白色凝胶物,它 是硅酸胶体和氯化钠的混合物。酸性溶液全部加完后,继续搅 拌半小时左右,白色胶状物迅速溶解。处理后的水玻璃静置一 段时间即可配置涂料。为提高水玻璃涂料的涂挂性,可向涂料 中加入0.05%非离子型或阳离子型表面活性剂,如农乳130# 水玻璃 + NH Cl(或HCl)水溶液 → 搅拌(析出白色胶状物)→ 4 水溶液加完后继续搅拌30分左右→至白色胶状物消失→静置→ 配制涂料. (4) 水玻璃作为型壳粘结剂的特点: 总而言之,比硅酸乙酯、硅溶胶所制型壳性能差。 优点:(1)来源广,价格廉。 缺点:(1)与蜡模润湿性差 (2)黏度大 (3)含Na2O →型壳高温强度低 →抗变形能力低→铸件精度低 涂料粉液比低 涂层致密性降低 铸件表面不光 Na O + SiO 2 2 (高温) Na2O·2SiO2(共晶物 熔点793℃) Na2O·2SiO2共晶物 在熔点793℃时出现液相,并使型壳软化变 形,因此,水玻璃作粘结剂的型壳所浇铸件尺寸精度、表面光洁 度都较差,用于一些要求不高的碳素钢件和有色金属铸件,对减 少机械加工和节约金属材料有利。 3.3.4 新型快干硅溶胶 概况 水基硅溶胶是一种绿色环保的粘结剂,在越来越重视环保 的今天,应大力加以推广。但普通硅溶胶型壳湿强度低,制壳周期 长已成为其推广使用中的主要问题。开发增强快干硅溶胶一直是各 国研究的课题。20世纪90年代研制成功的快干硅溶胶Ludox@SK系 列,制型壳时每制一层其干燥时间,即层间干燥时间仅1h,性能与 硅酸乙酯水解液粘结剂相当,于1997年已用于Rolls Royce大 量生产中。又如Remasol ADBOND系列,2001年推出的AD-BOND@ 3301制壳时每制一层,层间干燥时间也可达到1~2h,也已用于生 产。 国内在20世纪90年代中期清华大学和宇达化工合作开 发FS-Ⅰ快干硅溶胶,通过部级鉴定并用于生产。近年来又研制出 FS-Ⅱ型和FS- Ⅲ两种快干硅溶胶,通过省级鉴定,FS-Ⅲ在性 能上已接近Ludox@SK系列快干硅溶胶。 4.制壳工艺 型壳的质量与铸件的质量密切相关,因此制壳工艺也是熔模铸造 的关键一环。 制壳工艺包括: 除油和脱脂→在模组上涂挂涂料→撒砂→型壳的干燥和硬化 5-7次 →熔失熔模→培烧 4.1 模组的除油和脱脂 在采用蜡基模料和以水为溶 剂的粘结剂时,为提高涂料润湿模 组表面的能力,需要将模组表面的 油污去除掉。即在涂挂涂料之前, 先将模浸泡在中性肥皂片或表面活 性剂的水溶液中。 表面活性剂一端的亲水活性基 团易与涂料吸附,另一端的疏水 (亲油)基团易吸附在模组上. 4.2 涂挂涂料和撒砂 (1)涂挂涂料:先将涂料搅拌均匀,调整好涂料的黏度、比重。 若型壳上有小孔、槽,则内层涂料黏度、比重应小些,以使涂料能 很好地充填这些小孔、槽。 涂挂涂料时模组在涂料中上下左右晃动,使涂料能很好地润湿 模组,并均匀覆盖在模表面。不应有涂料局部堆积和缺料现象。且 不包裹气泡。 (2)撒砂 ? 撤砂的目的 1)迅速增厚型壳。 2)分散型壳在以后的干燥硬化中可能产生的应力 3)使外层表面粗糙,使下一层涂料与前一层很好的结合。 ?撒砂注意事项: 1)撒砂种类:应与该层涂料用耐火粉料一致,有相同的热膨 胀系数,以加强撒砂与涂层结合力。做一般钢件,如不锈钢、碳 钢件,面层用锆砂,背层用高岭石熟料。 2)不论用哪种砂子,都要严格控制其中的含水量,一般质 量分数均应小于0.3%。因为砂子湿度大极易产生浮砂堆积而导 致型壳分层。 3)砂子粒度也要合理选择,通常从面层到背层粒度逐渐加租。 面层撒砂不能过粗,否则会穿透涂层造成铸件表面凹凸不平,但 撒砂过细又不利于形成较粗糙的背层,不利于同下层牢固结合, 容易造成型壳分层。如用锆砂时面层撒砂应为100/120目。撒砂 逐渐变粗,过渡层撒30/60目、背层撒16/30目的高岭石熟料。 4)每次撒砂的粒度分布都不宜过于集中,这样才能使砂粒相 互镶嵌,提高型壳的致密度。 5)要严格限制砂中的粉尘含量,其质量分数应小于0.3%。 因为粉尘覆盖在涂料上就不易挂上砂粒。 ?撒砂方法: 1) 雨淋式:砂如雨点式撒在挂有涂料的模组上,模组不断旋转. 2) 流态式:砂存放于沸腾床中,底部送入压缩空气,将沸腾床上部 砂层均匀吹起,撒砂时只需将涂有涂料的模组往流态化的砂层中浸 一下,耐火材料就能均匀地粘在涂料表面。 图1-14 雨淋式撒砂机 4.3 型壳的干燥和硬化 每涂覆一层型壳之后,就要让它干燥、硬化,使涂料中的粘结 剂溶胶向冻胶、凝胶转变,把耐火材料连接在一起,根据所用的粘 结剂的不同,所用干燥、硬化方法也不同。 4.3.1 硅酸乙酯型壳的干燥和硬化 硅酸乙酯在干燥硬化时主要发生以下物理化学变化: (1) 涂料中溶剂(酒精或丙酮)的挥发: 挥发速度与溶剂分压有关,与湿度无关。 (2) 水解液的凝胶 型壳在干燥硬化时,硅酸乙酯水解液残留的不完全水解物会吸 收型壳中的水分继续水解,同时硅酸溶胶会在氨气的作用下进行凝 胶。因此 ,工业上使型壳在潮湿的氨气中硬化。 ?每制一层型壳需要五道工序: 上涂料 →撒砂 → 自干(或空气干燥)→ 氨干 → 去味 (强制通风柜中抽风除氨 ) 注意事项: 1)硬化时溶剂的挥发应比粘结剂的胶凝快,这时溶剂挥发产生 胶体收缩时,胶体尚处于弹、塑性状态,胶膜不易开裂。如果次序 相反,粘结剂固化后溶剂继续挥发,会出现脆性胶体的收缩,胶膜 易于开裂,型壳强度下降。为防止这一现象产生,通常将溶剂挥发 与胶体胶凝两个过程分开。 2)每层型壳硬化后须将氨气散发干净,再挂下一层。 3)有时为提高强度可在涂挂全部结束后,将带型壳的模组浸泡 在含SiO2较多的水解液中超过5分钟,使水解液渗入型壳中,而后在 风干、氨干过程中使粘结不好的耐火材料颗粒得到补充粘结。 4.3.2 硅溶胶型壳的干燥和硬化 硅溶胶中的溶剂是水和酒精,故硅溶胶的硬化过程主要是脱 水和酒精的挥发干燥过程。与此同时胶体进行凝聚。 将型壳放在温度较高的(25-35℃)的干燥空气中进行干燥 每层型壳的干燥时间约为2h,后一层涂料挂完后,型壳要自然 干燥一昼夜才能脱模。 (庆堂每层型壳的干燥时间约为8h,后一层涂料挂完后,型 壳要自然干燥一昼夜) 硅溶胶型壳的干燥和硬化 = 干燥的空气(25-35℃)中干燥硬化 4.3.3 水玻璃型壳的干燥和硬化 水玻璃型壳的干燥和硬化也是溶剂(水)的挥发和胶体的凝 聚过程。但水玻璃的脱水过程非常缓慢,而其硬化则由于电解质 的作用进行得很快。目前用的较多的硬化剂是NH4Cl、聚合AlCl3 结晶AlCl 。 3 硬化过程: (1)将型壳先放在空气中干燥一段时间(数分钟至一小时)。 其作用是去除模组表面和涂料层之间的水分、提高涂层中水玻璃 的浓度,减少型壳裂纹,改善型壳内表面质量。 (2)浸在浓度为25%左右的NH4Cl溶液中,此时发生反应 Na2O·mSiO2 + nH2O + 2NH4Cl≒ 2NaCl + mSiO2(n-1)H2O + → NH3↑+H2 析出的硅胶很快凝聚,使型壳硬化。 水玻璃型壳的干燥和硬化: 空气中干燥 浸在NH4Cl水溶液( 25%左右)中干燥硬化 注 意: 当型壳一浸入NH4Cl溶液中,在涂料层外表面上很快形成坚 硬的胶膜,影响NH4Cl溶液向型壳内层渗透。为加速NH4Cl溶液 向内层渗透,可在NH4Cl溶液中加入非离子型表面活性剂,可 使型壳的硬化时间由原来的15-20分缩短至2-3分钟。 图1-20 脉动式制壳机 4.4 脱模 型壳完全硬化后,需将型壳中的蜡模熔去,因模常为 蜡基模料制成,所以此工序称为脱蜡。根据加热方法不同, 有很多脱蜡方法,用的较多的方法有热水法和蒸汽法。 4.4.1 热水法 此方法适合于蜡基模料和水玻璃型壳。 用80-90℃的热水脱模。脱模时浇口杯朝上,使密度 小于水的蜡料易于上浮。 水 玻 璃 粘 结 壳 脱 蜡 时 热 水 中 通 常 加 入 少 量 NH4Cl 或 H3BO4,使型壳得到进一步硬化,且可除去型壳中残留的 Na2O和NaCl,提高型壳质量。(整个脱蜡过程在20-30分 钟内完成) 4)空气干燥及氨气硬化配合适当才能获得较高强度的型壳 并缩短制壳周期。 未经空气干燥而直接氨气固化的型壳,由于随后溶剂的挥 发使得涂层开裂,而强度较低。 如仅采用空气干燥固化,如每层干燥8~10h以上,型壳强 度,但生产效率低。 而将空气干燥与氨气硬化相结合就能获得较高强度的型壳, 其制壳周期也大为缩短。 硅酸硅酸乙酯型壳干燥硬化 空气中干燥硬化 潮湿的氨气中干燥硬化 特点 (1)简单易行,蜡料回收率高。 (2)若模组各部分厚薄不匀,或浇口杯厚大时,会 使先期熔化的模料难于排除,使型壳膨胀或破裂。 4.4.2 蒸汽法 用松香基模料制成的模组及采用硅酸乙酯水解液或硅溶 胶作粘结剂制壳时普遍采用蒸汽脱模。 将模组浇口杯朝下放在高压釜中,通入2-5个大气压的高 压蒸汽。模料受热熔失。 特点: (1)效率高(整个脱蜡过程在6-10分钟内完成),可提 高型壳强度。 (2)浇口杯直接受高压蒸汽作用,浇口处熔化快,型壳 膨胀可能性小 4.4.3 其它脱蜡方法 目前国外已经研究成功微波脱蜡、高温闪燃法脱蜡和预 熔法脱蜡。 4.5 型壳的培烧 脱模后,型壳在空气中经一段时间的自然干燥,在浇注 液体金属之前需将型壳经高温培烧。 目的: (1)去除型壳中的水分、残留模料、NH4Cl及盐分。避免 浇注时产生气孔、浇不足或恶化铸件表面等缺陷。 (2)进一步提高型壳强度 (3)提高金属的成型性。 普通型壳-装箱填砂培烧 高强型壳-直接装炉培烧。 硅酸乙酯、硅溶胶型壳-950℃,1-2h 水玻璃型壳-800-850℃,1-2h 型壳培烧后即可出炉浇注 5 熔模铸造型芯 一般情况下熔模铸造的内 腔是与外形一道通过涂挂涂料、 撤砂等工序形成的,不用专制 型芯。但当铸件内腔过于窄小 或形状复杂,常规的涂挂涂料、 撒砂等工序根本无法实施,或 内腔型壳无法干燥硬化时,就 必须使用预制的型芯来形成铸 件内腔。这些型芯要等铸件铸 成后再设法去除。 例如航空发动机空心涡轮 叶片,叶片的冷却通道迂回曲 折,形若迷宫,就必须采用陶 瓷型芯。图5-1是一些典型的 陶瓷型芯。 5.1 陶瓷型芯 陶瓷型芯是用粉状耐火材料(石英法粉或刚玉粉)和作为增剂 的蜡料(石蜡或蜂蜡等)以及一些其它其它附加物混成浆料物质, 在金属型中压制成型,后经高温烧结而成的陶瓷质型芯。 制熔模时,把陶瓷 型芯放在相应的位 置上,使陶瓷型芯 组成熔模上的小孔 洞,留在熔模中, 并露出型芯的芯头 部分。制壳时,陶 瓷型芯便借助芯头 与型壳组成一体, 成为型壳的一部分, 用它来形成铸件的 复杂内腔。 例如:铸件上的细长孔 直径在0.5-1mm 长30-60mm的 孔常可用石英玻璃管代替陶瓷型芯. 采用陶瓷型芯在熔模铸件上可铸出非常复杂的内腔,虽 然工艺复杂,但在一些重要零件的生产中,如航空发动机空 心涡轮叶片方面起了重要作用.( 叶片的冷却通道迂回曲折, 形若迷宫,必须采用陶瓷型芯铸造) 5.2 易溶型芯 若熔模的内腔是弯曲不平的,无法由压型压出,(无法 拔模),而是采用易溶型芯预先安放在压型内,压制时与蜡 模压成一体,取出蜡模后放于冷水中溶去,使熔模上形成 弯曲的内腔(然后内腔挂砂)常用材料为尿素(熔点130133℃)例如耐酸泵叶轮用此工艺。 5.3 其它型芯 (1)水玻璃型芯 (2)树脂型芯 (3)树脂砂替换拈结剂型芯 这是近年来国外提出来的一种低成本型芯。它是将传统的 树脂砂芯渗人一种“替换粘结剂”,干后就作为熔模铸造型芯 使用。这种型芯与陶瓷型芯相比,成本低,工艺简便,浇注后 型壳溃散性好,脱芯容易。很适合用于汽车行业和商业机械等 行业的价位不高的熔模铸件。图5-14替换粘结剂应用的一些 实例。 第四节 熔模铸造的浇注与清理 1.熔模铸造的浇注 1.1 热型重力浇注 这是目前使用广泛的一种浇注形式,即型壳从培烧炉中 取出后,立即在高温进行自由浇注。 优 点:流动性好,轮廓清晰,尺寸精度高。 缺 点:(1)晶粒粗大,机械性能低 (2)铸件表面脱碳、氧化 热型浇注碳钢时,冷却较慢,铸件表面易脱碳、氧化,从 而降低了铸件表面的硬度、光洁度、和尺寸精度。 改善措施: (1)细化晶粒 ※ 表面孕育的方法 如生产镍基、铁基合金时,较普遍的使 用混有表面孕育剂的涂料作为面层涂料制造型壳,浇入型壳中的金 属液在凝固时与型壳面层中的表面孕育剂(铝酸钴)作用,使铸件 晶粒变细。 ※ 加速冷却也可在一定程度上细化晶粒。 (2)控制浇注气氛为还原性 盖罩法:简单的方法是将刚浇注完的型壳用罩盖住,并向罩内 滴煤油。煤油在高温下分解为活性炭和氢,使罩内气氛呈还原性, 防止铸件表面脱碳、氧化 加还原物质:造型浇注时,可在填砂中加一些碳质物质,如: 石墨、无烟煤、沥青等,可使铸件在还原气氛中凝固。防止脱炭、 氧化。 1.2 真空吸铸 将型壳(如图所示)放在真空浇 注箱中,浇口向下,下降吸铸室, 使直浇口浸在液体金属中,同时抽 真空,利用型壳本身具有一定透气 性的特点,通过型壳中微小的孔隙 吸走型腔中的气体,并将金属吸入 型腔,完成充型过程。 精铸中工艺复杂、机械性能低、 成本高三大缺点中后两点可以在此 得到缓解。因为用真空吸铸代替了 热浇,另外计算好凝固时间,件凝 但浇注系统未凝时停止负压,使浇 注系统中的液体金属流回到熔池中, 提高了金属的收得率,降低了成本。 图1-21 真空吸气浇注装置 示意图 抽 真 空 真空吸铸过程示意图 线)在一定真空度下充型和凝固,改善充填条件,可复制 复杂薄壁铸件。 (2)充型平稳,可避免卷入气体和熔渣。 (3)可以降低浇注温度,节省能源。晶粒细、组织致密、 性能提高。 (4)直浇口向下,未凝金属回流,提高金属利用率,降低 成本。 线)要求型壳有更高的强度和透气性。 (2)加压停压时间难以控制。 (3)对耐火材料要求高(型壳吸铸口处长时间被熔融金属 浸泡) 1.3定向凝固 一些溶模铸件,如涡轮机叶片、 磁钢片等,如果结晶组织是按一定 方向排列的柱状晶,它们的工作性 能将有很大提高(蠕变和抗疲劳性 能明显提高,工作温度和寿命都得 到提高)。 如图,浇注前,先将型壳放在感应 加热的石墨套筒中的水冷底版上,, 先加热型壳,使其温度高于合金的 熔点,然后向型壳内浇入金属,通 过铜底版内的循环水,带走结晶时 放出的热量,晶体依温度梯度,按 垂直于铜板的方向向上生长。与此 同时,自下向上依次切断感应线圈 电源,使结晶前沿保持一定的温度 梯度,保证柱状晶顺利发展。 图⒈22 定向结晶示意图 l一石墨套 2一感应圈 3一型壳 4—水冷铜底版 1.4 压力下结晶 压力下结晶是将形壳放在压力罐内,当浇注完毕后,即封闭压 力罐,并向其中通入高压气体(惰性气体),使铸件在压力下凝 固,提高铸件的致密性。目前国外所用压力达15.2Mpa 1.5 细晶铸造 细晶铸造技术的实质就是控制铸件凝固时形核和晶粒长大的条 件,使铸件获得相当或接近于锻件的细小晶粒(0.1~0.5mm)组 织,从而提高铸件的抗疲劳性能,特别是低于760℃温度下低周 疲劳性能。并减小力学性能的分散性,使铸件的可靠性提高。普 通铸造和细晶铸造IN713C合金整铸涡轮晶粒度的对比如图7-25 所示,疲劳寿命及疲劳试验结果重现性(标准差)的对比见表7 -5。 1,细晶铸造常用的方法: 熔模铸件中需要采用细晶铸造 的并不只是整体铸造涡轮,还有其它许多场合,例如某些导向 和涡轮叶片等,所以细晶铸造也有多种方法。 熔模铸造高温合金细晶铸造常用的方法有化学法(含表面 孕育法和整体孕育法)、热控制法、动力学法(含代动力 学 法 Grainex 法 —— 机 械 搅 动 法 和 第 二 代 动 力 学 法 —— Microcast法,简称Mx法)。这些方法的基本原理及应用见表7 -6。 1.6 定向凝固加细晶铸造(DS/GX法) 1一合金液 2一铸型 3一型腔 4一水冷铜结晶器 5一冷却水管 ‘一隔热挡板 7一加热器 8一结晶起始块 p一振动器 20世纪90年代以 来,在美国宇航 工业技术发展计 划安排下,由 NASA(美国国家 航空航天局)发 起开展用于小型 航空发动机的更 先进的整铸涡轮 的研究。目标是 在保证轮毂部分 保持较好的低周 疲劳性能的前提 下,使叶片具有 更高的抗蠕变断 裂性能。 美国Howmet和英国Rol1s Royce Allison合作,论证了一种 能同时满足上述二方面性能要求的新的铸造工艺方法,称之 为DS/GX法,即所得铸件的叶片是定向柱晶,而轮缘和轮毂 是细等轴晶,铸后再辅以热等静压和其它热处理,使涡轮整 体综合性能显著改善。 为了获得这种在同一个铸件上具有双重组织和性能的整铸 涡轮,曾经进行过许多尝试和努力,但大多收效甚微。其原 因主要是实际生产中控制从叶片部位定向柱晶适时地转变为 等轴细晶十分困难。过程的再现性很差。 后采用将计算机模拟技术和铸造实际试验相结合的方 法大大缩短了DS/GX新工艺开发的时间并节省了费用。 1.试验装置(图7-26) 操作时先将隔热挡板6打开,启 动加热器7,将铸型2加热到预定温度,然后将合金液1浇 人铸型型腔3。与水冷铜结晶器4接触的合金液首先凝固, 形成许多任意取向的细小等轴晶粒。随后,合金的结晶进 人受控阶段。此时,先令隔热挡板6缓慢闭合,并将加热 器7外围的加热元件断电,同时调节结晶器4内的冷却水 流,使之与轮盘之间形成有效的径向温度梯度。铸造合全 凝固时产生的热量不断通过结晶器冷却水管5中的水流导 出,晶体便通过结晶起始块8向轮盘中心定向生长,从而 得到定向柱晶叶片。当凝固前沿到达轮毂部分时,关闭加 热器电源,将隔热挡板完全打开,并开动振动器9,使轮 盘部分快速结晶,形成细小的等轴晶组织。于是铸成叶片 部分为定向柱晶,而轮毂部分为细小等轴晶的整体涡轮。 从铸件相应部位切取试棒测定力学性能,试验项目包括 高温拉伸、应力断裂、低周疲劳、疲劳裂纹扩展速率等。 结果表明叶片部分高温断裂性能比单纯细晶铸造(GX法) 有较大改善, 从总体看达到了预期研究目标。 2 熔摸铸件的清理 清理的内容包括:(1)从铸件上清除型壳, (2)从铸件上切除浇冒口 (3)去除铸件上所粘附的型壳耐火材料。 (4)铸件热处理后的清理。如去氧化皮等。 在熔模铸造中,第2、4项外,其余都有自己的特点。 2.1从铸件上清除型壳 (1)锤击法:少量生产时,用锤击 浇冒口系统,产生震动,使型壳脱落。 (2) 震击式脱壳机脱壳:产量较大 时,用震击式脱壳机脱壳。 优点:效率高。 缺点:噪音灰尘大,清理后,铸件仍残 留一些耐火材料。 图⒈23 震击式脱壳机 1一气缸 2一弹簧 3一导柱 4一风锤 5一铸件组 (3)电液压清理:它利用水中电极与铸件间的高压放电而 产生的冲击波和冲击压力进行清理。 优点: 铸件清理干净、工作 时无灰尘 缺点: 噪音大,还能放出有 害气体(NO、 NO2)和 有害辐射。 图1-24 电液压清理装置示意图 2.2铸件表面清理 残留在铸件表面上,尤其是内腔、深槽及盲孔等部位的耐火 材料,需要进一步清除干净。 清理方法包括: (1) 机械清理:滚筒、喷丸或喷砂(铸件表面被硬化) (2) 化学清理: 1)碱煮清理:将带有残留石英砂的铸件放在苛性钠(浓度 20-30%)或苛性钾(浓度40-50%)的溶液中,加热煮沸,发生如 下化学反应: 2NaOH + SiO2= Na2SiO3 +H2O 2KOH + SiO2= K2SiO3 +H2O 生成的硅酸钠和硅酸钾是一种粘稠状液体,可以用热水冲洗 干净(此方法不能用于铝合金铸件,以免腐蚀)。还可将铸件置 于滚筒一起浸入碱液中,边转动边清洗。 2)碱爆清理:清除深孔、槽中的残砂效果好。 A. 碱煮:浓度为90-95%的苛性钠加热至500-520℃的熔融 状态,将装着铸件的吊筐浸入其中,加热25-60min B.水爆:将加热的铸件移至水槽中进行水爆,然后置于70- 90℃的热水中清洗。 3)电化学清理: 将铸件放在处理溶液中,通以直流电,通过化学反应和电解还 原将粘砂层清理干净。 处理溶液:NaOH(85-90%)+NaCl(10-15%)(-500℃)。 粘砂层与NaOH反应生成Na2SiO3。通入3-6V直流电,粘砂层接 阴极,钠离子在其上面得到电子而还原为金属钠,它有很强的还 原性,能把铸件表面和内腔的氧化物还原干净。
以上信息由江苏亚立特钢有限公司整理编辑,了解更多离心铸造信息请访问http://www.jsyltg.com