新闻中心
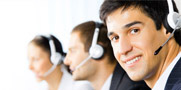
咨询热线:
134-0554-5577
邮件:874556408@qq.com
电话:0523-83984388
地址:江苏省兴化市沈伦镇工业园区沈北路
离心铸造高温稳定性好的硅凝胶组成
第二章第二章 熔模铸造 熔模铸造 概述 概述 熔模铸造的发 展史可以追溯 到0年前, 埃及、中国和 印度是早起 源的国家。 曾侯乙尊盘曾侯乙尊盘 ((战国早期 战国早期)) 曾侯乙尊盘 曾侯乙尊盘 ((战国早期 战国早期)) 概述 概述 概述概述 概述概述 概述概述 所谓熔模精密铸造工艺,简单说就是用易熔材料 (如蜡料或塑料)制成可熔性模型(简称熔模或模 型),在其上涂覆若干层特制的耐火涂料,经过硬 化形成整体型壳,熔掉模型,焙烧后浇入金属液而 得到铸件。 定义 2.1 概述:熔模铸造的原理及特点 2.1.1 原理:熔模铸造就是在蜡模(也可用 树脂模)表面涂覆多层耐火材料,待硬化 干燥后,加热将蜡模熔化,而获得具有与 蜡模形状相应形状的型壳,再经焙烧之后 进行浇注而获得铸件的一种方法,故又称 为失蜡铸造(Lost Wax Casting)。 随着生产技术水平不断提高。新的蜡模工艺不断 出现,以及可供制模材料的品种日益增多,现在去模的 方法己不再限于熔化,而且也不限于蜡模,也可用塑料 模,但因习惯的原因,离心铸造仍沿用原来名称。由于用这种方 法获得的铸件具有较高的尺寸精度和较低的表面粗糙度 值,故又称为熔模精密铸造(Investment Casting)。 概述 熔模铸造特别适合于生产尺寸精度要求高,表面粗糙度值低,形状复杂的铸件,合金材料不受限 典型的产品主要有:定向凝固和单晶铸件、整流器、汽轮机叶片、静叶片、热交换器等。 2.1.2熔模铸造的基本特点: 制壳时采用可熔化的一次模, 因无需起模,故型壳为整体而无分型面,且型壳是由高 温性能优良的耐火材料制成。 2.1.3 熔模铸造的主要优点如下:(与其它铸造方法相比) (1)铸件尺寸精度较高和表面粗糙度较低,可以浇注形 状复杂的铸件,一般精度可达CT5~7级,粗糙度可达 Ra2.5-6.3μ (2)可以铸造薄壁铸件以及重量很小的铸件,熔模铸件的小壁厚可达0.5mm,重量可以小到几克; (3)可以铸造花纹精细的图案、文字、带有细槽和弯曲 细孔的铸件; (4)熔模铸件的外形和内腔形状几乎不受限制,可以制造出 用砂型铸造、锻压、切削加工等方法难以制造的形状复杂 的零件,而且可以使有些组合件、焊接件在稍进行结构改 进后直接铸造成整体零件,从而减轻零件重量、降低生产 成本。 (5)铸造合金的类型几乎没有限制,常用来铸造合金钢件、 碳钢件和耐热合金铸件; (6)生产批量没有限制,可以从单件到成批大量生产。 2.1.4.熔模铸造方法的缺点是:工艺复杂,生产 周期长,不适用于生产轮廓尺寸很大的铸件。 2.1.5 熔模铸造工艺过程 2.2 熔模的制造 熔模是形成型腔的模型,它的尺寸 精度直接影响到成形铸件的尺寸精度 和表面质量。所以为获得高质量的熔 模,首先必须选择合适的熔模材料即 模料性能的基本要求对熔模模料性能的基本要求概括为: 热物理性能:主要指有合适的熔化温度和凝固区间、较小的热膨胀和收缩、较高的耐热 性(软化点)和模料在液态时应无析出物, 固态时无相变; 熔化温度和凝固温度区间模料熔化温度控制在 50~80之间,凝固温度区间则以6~10为宜。 2)热膨胀率和收缩率模料的收缩率是是模料的重要性 能指标之一,模料的热胀冷缩小,不仅可以提高熔模的 尺寸精度,也可减少脱蜡时胀裂型壳的可能性。模料的 线)软化点:模料开始软化变形的温度。
40。耐热 性是指温度升高时模料的抗软化变形的能力。模料的耐 热性高,抗软化变形的能力强,模样的尺寸精度越高。 4)强度熔模要有一定的强度,以保证在生产过程中不 致损坏。模料的强度多用抗弯强度表示,其值一般不得 低于2.0MPa,为5.0~8.0MPa。 5)硬度为保持熔模的表面质量,模料应有足够得硬度,以防摩 擦损伤。模料硬度通常以针入度表示。模料的针入度多在4~6度 (1度=0.1mm)。 6)流动性为了完满充填压型型腔并清晰复制出棱角及精细部位, 要求模料在压注时具有良好的流动性,但模料流动性过高,注入 型腔时容易形成紊流、飞溅,使熔模表面产生流线、气泡等缺陷, 所以压注时模料的流动性要适当,不宜过高或过低。模料的流动 性可通过温度和粘度控制,在90附近,模料粘度应为3.0X10- 2~3.0X10-1Pa 模料的涂挂性直接影响型壳的表面质量,可以用熔模与粘结剂之间的接触角来衡量。 8)灰分灰分是指模料经高温焙烧后的残灰。模料灰分含量高, 经高温焙烧后残留于型壳中的灰分多,势必对铸件内部和表面质 量产生不良影响。所以灰分也是模料重要的性能指标之一,应尽 量降低模料的灰分含量。一般而言,模料的灰分应低于0.05%。 模料的分类 随着熔模铸造工艺的发展,模料的种类日 益繁多,组成各不相同。 按组成模料的基体材料和性能的不同进行分类:可分为蜡基模料、树脂基模料、填料模料及水 .石蜡:饱和的固体碳氢化合物,含有20个以上碳原子烷烃的混合物。 2n+2,式中n=20-30。 晶态物质,冷却曲线有明显而确定的平台。耐热性较差,收缩率约为0.6—1.5%。针入度 15度,硬度较低,因此配以硬脂酸。化学性 质稳定,140以上分解碳化。 牌号:50,52…,70.(熔模铸造用58-64),对应其熔点。 35COOH,提高熔模的表面强度和涂料的涂 挂性(润湿能力) 与石蜡互溶,强度高,熔点高(2069),热稳定性好(工业用常含杂质油酸——易氧化,降低稳 定性),硬度大 石蜡与硬脂酸配合使用调整其比例来控制性能(软化点 强度等)(1:1) 硬脂酸含量增加,软化点、流动性、涂挂性提高,硬度提高,强度下降,凝固温度区间变窄 表2-2石蜡—硬脂酸(1:1)模料的主要性能 2.2.2.2 树脂基模料 兼顾蜡基的长处,表面光亮、针入度小,常用于精度要求很高的铸件生产中。 2.2.2.3 填料模料 常用四种:枝链型聚苯乙烯;XLPS冰烯醋酯;XLA 2.2.3.1模料的配制 配制工艺:是指按照模料的规定成分和 配比,将各种原料熔融成液态, 合并搅拌均匀,滤去杂质浇制成合乎要求的糊状模料直接使用,或浇注成锭 熔化方法水浴加热 旋转桨叶搅拌法 活塞搅拌法: 带孔活塞往复运动 注意:加料次序聚合物、蜡料、松香 模料配制工艺要点:模料配制过程中应该注意的三点: 严格控制温度的升限和在高温下停留的时间。避免模料的烧损和变质。(防止局部过热) 合理安排各组元的加热顺序原则:溶剂优先,互溶在前。 充分搅拌(互溶),滤去杂质(回收),保温静置(排气)2.2.3.2 模料的回收 概念去除模料中的杂质,恢复其性能的工艺过程 称之为模料的回收或复生。 模料变质的原因(皂化反应):置换反应(Al、Fe) 中和反应(氧化钠、氨水) 复分解反应(Ca、Mg盐) 皂化物不溶于水--不易去除,影响模料性能,进一步降低 铸件质量 使用松香基模料时,回收的模料用来制作浇 冒口熔模 使用蜡基模料,脱模后所获模料可回收,再用来 制造新的熔模 蜡基旧模料的性能变化 在循环使用时,模料的性能会变坏:脆性增 大,灰尘增多,流动性下降,收缩率增大,颜色由白 变褐,这些主要与模料中硬脂酸变质有关,也有其它 原因。 蜡基模料变质的原因 硬脂酸呈酸性,它能和化学活性比氢强的金属反应,如熔制熔模时,与一些铝、铁工具接触便发生以下置换反应: 2Fe +6C 17 35COOH 2Fe(C17 35COO) 2Al+6C 17 35COOH 2Al(C17 35COO) 用水玻璃作型壳黏结剂时,硬脂酸会与NaOH发生中和反应:NaOH 35COOH 35COONa 17H35COOH Ca(C17 H35COO)2 2H2O以上反应统称为皂化反应,所产生的硬脂酸盐称为皂盐或皂化物, 大都不溶于水,但却能与模料均匀混合使模料性能变坏。 (2)砂和涂料的污染 在制造熔模、制壳以及与蜡的熔失过程中,有时会受到砂和涂料等异物的污染。所以,制模车间 一定要注意工作场地的卫生。防止模料污染(一 般要白大衣、拖鞋、瓷地面、工作台洁净) (3)熔失熔模时过热,石蜡烧坏、氧化变 皂化物的去除方法:酸处理法电解处理法 活性白土 处理法 酸处理法Me(C17H35COO)2 +H2SO4=2(C17H35COOH)+MeSO4 不足:可逆,不能完全处理干净 电解处理法FeCl3 Cl2(有毒) 不足:设要求高,污 染环境 活性白土处理法吸附能力+Al3+与胶体杂质反应沉淀 补充使用 回收蜡基模料的处理方法 盐酸(硫酸)处理法具体方法为将水和旧模料放在不生锈的容器中(水占模料的25- 35%)加热至80-90,然后加入模料重3-5%的工业盐酸(或2-3% 的浓硫酸)继续加热,使酸与模料充分反应,经30-40分钟后,静置 使水与模料分离,然后过滤,浇成锭,由于硬脂酸铁与盐酸反应是 可逆的且很快达到平衡,因此模料中的硬脂酸铁难以去除干净。 盐酸和硫酸都可使除硬脂酸铁以外的硬脂酸盐还原为硬脂酸: Me(C 17 35COO)+ HCl 35COOH MeCl80-90 25-35%水(占模料比重)加3-5%盐酸(或2-5%硫酸) 加热 保温静置,使模料充分反应 30-40分 活性白土处理法活性白土是有一种经酸处理后的黏土,它的晶格由硅氧四面体 和铝氧八面体交叉成层构成,各层间有大量的孔隙。好的白土, 其孔隙率可达60-70%,有很大的比表面积。因而具有较高的吸附 能力,能吸附模料中硬脂酸盐。此外,活性白土中的阳离子(特 别是三价铝离子)还能和模料中的带负电荷的的胶状杂质结集成 中性质点,变成凝胶下沉。所以可用活性白土去除模料中的硬脂 酸盐。 生产中一般用此法作为盐酸处理的补充工序,即每隔一段时间 将用盐酸处理过的模料加热到120 左右,向模料中加入烘干的 活性白土(为模料重的10-15%)进行搅拌,半小时后,在120 下保温静置4-5小时,待活性白土与液态模料充分分离后即可处理 120+白土(10-15%) 搅拌半小时 120下静置4-5h 盐酸处理过 加热 烘干 电解法电解处理方法可去除模料中的硬脂酸铁。电解液浓度为2.8-3.5%, 温度为80-85的盐酸溶液,处理时向电解槽中加入经酸处理的熔融 模料,通电后当电压超过盐酸的电解电压(1.36v)时,在阳极碳棒 上析出活性极强的初生态氯,它有很强的氧化能力,能从硬脂酸铁 中夺取Fe +3 ,形成FeCl 反应如下:4Fe(C 17 35COO) 35COOH 而在阴极(铅板)上则析出还原能力极强的初生态氢,将Fe+3 还原成Fe +2 其反应如下: FeCl 在水中溶解度很大,能从模料进入盐酸中。因此,硬脂酸铁不断被还原为硬脂酸,使模料净化。 实际生产中,常用盐酸(硫酸)处理法,也用活性白土处理法,用 电解处理法因工艺复杂故很少采用。 判断一个铸造的水平,可根据3项指 石蜡的颜色:蜡越黄质量越差、越白、质量 越好 空调条件:空调条件好,蜡不易变形,精度高 车间内洁净程度:洁净、无污染、蜡的质量好 2.2.4. 熔模的压制和模组的制造 模料膏配制完毕即可压制熔模。压制熔模前,需先在压型表面涂薄层分型剂,以便从压型中取出熔模。 压制蜡基模料时,分型剂可为机油、松节油等;压制树脂基模料时,常用蓖麻油和酒精的混合液或硅油作分型 剂。分型剂层越薄越好,使熔模能更好地复制压型表面, 提高熔模的表面光洁度。 熔模的制即将模料注入压型的方法有自由浇注和压注两种。自由浇注法使用液态模料,用于制作浇冒口系统 的熔模和尿素型芯。压注法用于制造铸件熔模,可使用 液态、半液态(糊状)、半固态(膏状)及固态模料。 2.2.4.1 压注成形 压注成型的注蜡温度多在熔 点以下,此时模料是液、固两相共存的浆状或 糊状。呈浆状的模料中,液相量显著超过固相 量,所以仍保留着液体的流动性。在这种状态 下压注,熔模表面具有较低的粗糙度,而且不 易出现由于紊流、飞溅带来的表面缺陷。糊状 模料的温度比浆状模料更低,已失去流动性, 虽少有表面缺陷,但却具有较高的表面粗糙度。 图为几种常见的压注成形方法示意图柱塞加压法 活塞加压法与气压法压注 1)“液态压注模料”大多采用在熔点下呈糊状时压注(并 非真正的液态下压注) 收缩率降低。2.2.4.2 熔模表面质量的控制 合理确定工艺参数压蜡温度 压注压力 压型温度 压射速度 在压力下成型并在压力作用下凝固2.2.4.3 熔模尺寸精度的控制 压型温度其它:模型的壁厚 取模后停放时间 2.2.4.4 压注过程主要工艺参数的控制 压力+流速 压力和流速是压注过程中重要而又密切相关的两个参数,没 有足够的压力驱动,模料不能流动,但它们又是不同的两个概念: 驱动模料流动的压力取决于模料的粘稠度和充型过程中的阻力,而 流速则指模料进入压型型腔的速度。因此压蜡设可以划分为以下 四类: 1.只控制压力—受环境温度等因素影响。 2.同时控制压力和流速,无压力补偿—高压低流速,低压不能 获得高流速。 3.同时使用压力和流速控制,并有压力补偿—获得想要的流速。 4.流速控制和分段式压力控制—充型 保持3个阶段 2.2.5 熔模的组装 焊接法——应用广泛电烙铁 敷一层,利于取出熔模。要求越薄越好 蜡基:一般采用机油、松节油、硅油 树脂基:麻油与酒精混合物或者硅油 压缩空气起模 2.2.4.5 熔模的脱模 机械组装法——大批量、小铸件、高效率2.3 型壳的制造 型壳的质量直接关系到铸件的质量,为此,对型 壳的要求主要有以下四个方面: 1.强度——高的常温强度+ 高温强度(浇注、焙 +低的残留强度2.热震稳定性——抵抗急冷急热的性能或抗热冲 击性。它是指型壳抵抗因温度急剧变化而不开裂 的能力。 3.高温下化学稳定性——高温液态金属与之接触 时不发生相互化学作用的性能。 4.透气性——指气体通 过型壁的能力。 以免发生粘砂、麻点、氧化、脱碳 避免浇不足、气孔 HB5352.1-2004 熔模铸造型壳性能试验方法 部分:抗弯强度的测定 HB5352.2-2004 熔模铸造型壳性能试验方法 第2部分:高温自重变形的测定 HB5352.3-2004 熔模铸造型壳性能试验方法 第3部分:高温荷重变形的测定 HB5352.4-2004 熔模铸造型壳性能试验方法 第4部分:透气性的测定 型壳的制造工艺——涂挂法 熔模铸造型壳: 多层型壳:涂挂法制壳—(浸涂)常用 喷涂法 型壳的高温强度和高温软化点型壳的高温强度是型壳主要的基本性能,在制壳、 脱蜡、焙烧和浇注工艺过程中,型壳要承受各种应力的 作用,没有足够的强度就不可能达到铸造的目的。室温 强度固然重要,但高温强度更加重要。从浇注开始型壳 就开始承受高温液体金属的热冲击、机械冲击,金属又 要通过型壳散热而冷却凝固,从而型壳又将受到很大收 缩应力和热应力。 型壳的软化点是指型壳强度随温度升高而开始下降 的温度。不同型壳软化点不同。软化点高,高温强度下 降速度小,有利于提高铸件的尺寸精度。 型壳的热膨胀性型壳的热膨胀性是与铸件精度密切相关的重要性能。高温 金属液通过型壳放热、冷却、凝固中,温度的急剧变化,型壳的 线量也发生变化。 为获得尺寸的铸件型壳的膨胀率必须小而均匀。型壳小而均匀的热膨胀性是减少应力,使型壳具有良好 抵抗温度急剧变化能力的决定因素。(型壳温度变化,必然产生 内应力,当该内应力超过该温度下的强度时,型壳就会产生裂纹、 破损)。 .型壳的表面质量及化学稳定性型壳内表面层与高温液体金属直接接触,要想 获得表面光洁、轮廓清晰的铸件,型壳内表面层必 须光洁、致密、轮廓清晰。除此之外还应具有好的 化学稳定性,即浇注后,型壳内表层不与高温液体 金属及其氧化物相互发生化学作用。 上述条件将是实现高精度铸造的基本要求, 此外,还要有好的透气性、好的退让性、好的脱壳 清理性。但一种材料很难完全满足各种要求,因此 在选用制壳原材料时,应抓住无余量铸件表面光洁 度、尺寸精度要求高这个主要矛盾。 型壳的制造工艺:涂覆涂料撒砂干燥硬化 重复5-7次 涂料的组成:耐火材料粉 溶剂(水)2.3.1制造型壳用的材料 多层型壳是由耐火材、粘结剂料及附加物组成,其中 耐火材料占90%以上。所以耐火材料的选用对型壳的性能 影响很大。其次为粘结剂及附加物、工艺的影响 2.3.2.1 耐火材料 (石英 刚玉 1)面层粉料。与粘接剂配制成涂料的粉状料,直接与高温金属液接触,要能承受热冲击和热物理化学作用。 2)增强型壳的撒砂材料——粒度 3)制造陶瓷型芯的粉状料——具有一定的抗冲击性 对耐火材料的要求 耐火度和熔点——高温时不软化,变形(耐火度 :又称耐熔度。表征物体抵抗高温而不熔化的性能指标 573发生相变线时,离心铸造由β转变为α 膨胀大 应用:适用于碳钢、低合金钢、铜合金;不适于铝、钛、锰、铬合金钢 2)熔融石英 熔融石英熔化温度为1713,导热系数低,热膨胀系数几乎是所有耐火材料中小的,因而它具有极高的 热震稳定性。 应用:易被氢氟酸或碱侵蚀便于除芯,常用于作陶瓷型芯的基本材料 锆英砂又称硅酸锆,是天然存在的矿物材料。常含有少量的放射性的铀、TiO 和微量稀土氧化物。纯锆英石在1775能分解析出SiO 熔点2030密度大,结构致密,导 热性好,热膨胀系数小,高温化学稳定性好。 优点:熔点高,结构致密,导热好,热膨胀小而均匀,化学性能稳定,型壳尺寸稳定 莫来石又称高铝红柱石,分子式为3Al ,膨胀系数5410 -7 l/,离心铸造在1810开始出现液相。 莫来石很少以天然形式存在,多是人工合成(高温烧结)。 石英(硅石)SiO2 刚玉 (Al2O3) 锆英石其它 人造石墨 钨粉 氧化 优点来源广、价 廉、耐火度 高、残留强 熔点高、导热性好、 热膨胀小 均匀 价廉、来 定性提高传热系数 均匀、高耐火度 缺点 酸性易于在 高温下反应, 形成麻点、 来源缺、价高 SiO2易与 Al、Ti反 应、脱壳 矾土)价格较高、 分解出 SiO2 注 不能用来对 加固涂层面层使用, 提高质量 2.3.1.2 制壳用黏结剂 在高温及室温下形成的氧化物或与耐火材料形成的化合物,具有高温化学稳定性,不与所浇注的合金发生化学作用 目前熔模铸造及陶瓷型铸造使用的黏结剂包括水玻璃 硅溶胶 硅胶乙酯 从本质上来讲都是硅酸胶体,只不过其类型不同罢了,从终 形成的氧化物性质看都是二氧化硅,故都属酸性黏结剂。 3.胶凝过程 加热 溶胶 凝胶细微的二氧化硅结晶 溶剂挥发900-1000度 2.3.1.3 硅酸乙酯水解液(1)硅酸乙酯的物理性质 硅酸乙酯又称正硅酸乙酯。一般硅酸乙酯呈油性,为无色、透明或棕黄色液体(有杂质) 有醚味,对眼睛、呼吸道有刺激作用,应密封保存(2)硅酸乙酯的水解过程(硬化原理) 硅酸乙酯本身并不能作黏结剂,它必须经水解后成为水解液 才具有黏结力。因此,人们通常所说的硅酸乙酯黏结剂实际上是硅 酸乙酯水解液。 硅酸乙酯[(C Si]是由四氯化硅和乙醇作用而成:SiCl 4HCl生产中由于工业乙醇中含有水,且乙醇又极易吸水,且盐酸和乙醇 作用也生成水(HCl O),所以硅酸乙酯中总有水。水能使正硅酸乙酯水解而 形成不同聚合度的聚合物。 其反应如下: C2H5O C2H5O C2H5OSi C2H5OSi OH C2H5OC2H5O (乙氧基硅醇) 硅羟基 由于SiOH间脱水聚合倾向很强,故乙氧基硅醇极不稳定易发生 如下缩聚反应: 在熔模铸造过程中硅酸乙酯的水解是分两个阶段进行的。阶段:硅酸乙酯硅酸乙酯水解液 这时,我们需要的是具有一定聚合度的线型或枝型的聚合 物,即具有一定黏度和黏结力的黏结剂。故加水量应严格控制。 使硅酸乙酯的水解反应进行到一定程度为止。 第二阶段:干燥硬化 硅酸乙酯水解液配制成涂料, 制壳后,涂料层继续发生水解 反应,直至形成硅凝胶。制壳后,涂料层置于空气中,空气中 的水分可使硅酸乙酯继续进行水解—缩合反应,在线型或枝型 乙氧基硅酸结构间相互交联,后形成网状结构。在网状结构 间还含有一定的乙氧基,称为有机硅聚合物,其分子结构可表 随着胶凝过程进一步进行,乙氧基不断被羟基取代,水解作用趋于完全。网状的有机硅聚合物逐渐变为无机硅聚合物,其分子结 HOSi HOSi 这时型壳中的黏结剂薄膜由强度高,高温稳定性好的硅凝胶组成。 特点:强度高,高温稳定性好,价格贵 (3)酸乙酯水解时配料计算 因水和硅酸乙酯不能互溶,如单独把它们放在一起,水解反 应很难在整个体系内均匀进行,在硅酸乙酯不能和水充分接触的 地方,会形成不完全水解产物—有机硅聚合物。 水解时常用酒精或丙酮作媒介, 水解时加少量HCl或醋酸作催化剂(同时为加快反应速度). 例如:获得此种硅酸的正硅酸乙酯的水解反应式为: OH832 832 162 0.1943B‵即水解1kg(正)硅酸乙酯成为H (乙氧基硅醇)所需水量,此B‵可在各种书、手册中查到。 溶剂(乙醇或丙酮)及催化剂(HCl或醋酸)均可计算_略 硅酸乙酯的水解工艺一次水解法:先将水、溶剂和催化剂混匀,而后逐 渐加入硅酸乙酯并强烈搅拌。加完硅酸乙酯后,继续搅 拌30分钟,而后水解液存放16小时以上再使用。在使用 前需先测水解液中二氧化硅和HCl的含量及黏度。配料 时,只需向水解液中加入粉状耐火材料并充分搅拌 注意:水解时温度不得超过40-50度 (水+溶剂+催化剂) +硅酸乙酯 30分硅酸乙酯水解液 配制涂料 (静置16小时) 综合水解法:这种方法实质是使水解过程与耐火材料的混制同 时进行。具体工艺过程是先将硅酸乙酯与溶剂放在一起,搅拌2-3 分,再加粉状耐火材料搅拌5-10分。使硅酸乙酯溶液能很好润湿粉 粒表面。然后逐步加入酸化的水。在搅拌过程中,使水解反应在粉 粒表面进行。 硅酸乙酯+溶剂(酒精或丙酮) 搅拌2-3分+粉状耐火材料 搅拌5-10分所得涂料分散度高,均匀性好。型壳强度高,且节省硅酸 乙酯。但很难对涂料黏度进行调节。 硅酸乙酯水解液黏结剂特点硅酸乙酯是优质黏结剂,所以型壳性能好: 硅溶胶的物理特性:硅溶胶即胶体二氧化硅,是一类无定性二氧化硅粒子在水介质 中的分散体系。 硅溶胶是将水玻璃经过离子交换后去掉其中的钠离子和其它 杂质,再经浓缩制得的。它是硅酸的多分子聚合物,为较纯净的 硅酸水溶液,也称硅酸溶胶。为乳白色或青白色溶液。分子式为n 熔模铸造用硅溶胶要求:Na O小于等于0.5%,SiO 为24-30%,PH为8-10(为9.5) 黏度值为2-6厘泊 硅溶胶的处理工艺硅溶胶是一种水基黏结剂。用它配制耐火涂料涂挂性差,为 降低其表面张力,并使之具有适当的黏度,则在使用前需要进行 适当处理。 所谓处理就是在硅溶胶中加入一定量乙醇。这样配制成的 硅溶胶乙醇溶液就是硅溶胶黏结剂。 通常乙醇加入量为20-25%,比较合适,超过30%硅溶胶不
以上信息由江苏亚立特钢有限公司整理编辑,了解更多离心铸造信息请访问http://www.jsyltg.com