新闻中心
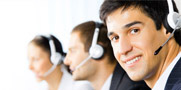
咨询热线:
134-0554-5577
邮件:874556408@qq.com
电话:0523-83984388
地址:江苏省兴化市沈伦镇工业园区沈北路
离心铸造铸件名称管接头组铸件材质YZG3
熔模铸造工艺流程大致为①模具设计制造与加工;②制蜡模,蜡模修整,将蜡模焊在模棒上;③蜡模模组涂挂涂料及撒砂,涂层固化与干燥,反复多遍涂挂涂料与撒砂,直至模壳层厚达工艺要求(约8mm);④将模组放入脱蜡室进行热水或蒸汽脱蜡,形成模壳;⑤将模壳放入焙烧炉内(一般为燃气或燃油,温度约1000℃)焙烧1h左右,使模壳烧结,建立强度,使之能经受高温金属液冲刷而不开裂或溃散;⑥进行浇注;⑦铸件清理与检验。
根据熔模铸造的特点,对含有变截面、尺寸较窄小(截面积≤80mm2)、形状弯曲等内腔的铸件,无法直接抽芯,必须采用型芯来形成铸件的内腔。熔模铸造工艺对型芯的特殊要求在于①制蜡模时,能经受射蜡压力的冲击;②脱蜡时,能经受热水的煮泡而不损坏、表面不掉砂③模壳焙烧时型芯能具有一定的高温强度,经1000℃约一小时的焙烧后不发生断芯、型芯表面不开裂;④浇注时型芯能承受铁水的冲刷和静压力而不损坏或不掉砂;⑤清理时能经过震动、抛丸等方式去除砂芯、确保内腔光洁。离心铸造
目前熔模铸造型芯的生产工艺有热压注陶瓷型芯、传递成形陶瓷型芯、灌浆成形陶瓷型芯、水溶性型芯、水玻璃砂型芯以及细管型芯、过渡性型芯等工艺。对于汽车及其它普通机械行业的铸造生产来说,由于铸件成本的限制,难以使用高成本的制芯工艺,必须寻求低成本的制芯方法。因此在这些行业中,CO2水玻璃砂芯和尿素芯应用较为普遍,但这些型芯有其不足之处和应用的局限性水玻璃砂型芯以石英砂和水玻璃为原料制芯,采用CO2气体固化,砂芯表面需浸水玻璃强化,该法生产效率高、生产成本低,但脱芯困难(必须采用碱煮方法脱芯)、砂芯强度低,难以满足大批量生产的要求;过渡性型芯一般是指尿素芯,用于无法直接抽芯成形的内腔,该工艺将尿素芯置于压型中压制蜡模,然后蜡模放入水中将尿素芯熔掉以形成铸件内腔,往后的工序与其它工艺的一样;该工艺仅适用能顺利涂挂涂料和撒砂的内腔,而且也难以保证铸件的尺寸精度,生产成本较高,此法目前应用较为广泛。
目前,在生产内腔表面质量和尺寸精度要求不很严格的铸件时,很多情况下,希望使用低成本型芯。在国外,为典型的是日本学者提出的“Convert”法,它代表了近年来低成本型芯的新近发展。该“Convert”法,根据芯子的形状、数量和质量情况,选金属或木质或塑料芯盒,生产树脂砂芯。然后将砂芯浸入硅酸盐或碱金属成分为基的混合粘结剂中几分钟,取出后在空气中干燥。将空干后的砂芯放入压型中,压制蜡模或嵌入蜡模中,以后可按正常的方法制型壳、脱蜡、焙烧和浇注,生产熔模铸件。砂芯易于清除,可用传统的喷砂或喷水法去除残余的砂芯。在国内,经查新有相关文献两篇一是太原矿山机械陈晋公等人申请的熔模铸造用砂芯的生产方法(申请号分别为88109008),其开发出了水玻璃-CO2法生产熔模铸造用型芯的生产技术,该技术的要点为在石英砂及铝矾土中加入一定量的改性水玻璃、聚氯乙烯、邻苯二甲酸二丁酯,然后通CO2硬化,在200℃温度下烘干,再涂锆英粉耐火涂料,以聚氯乙烯加热固化提供常温强度,改性水玻璃通CO2硬化提供高温强度,涂锆英粉耐火涂料提高型芯的表面质量,该法的缺点是砂芯常温强度低而且易变形、脱芯较困难,芯砂、砂芯的存放性差,难以组织大批量生产。二是中国国际贸易促进委员会专利代理部代理的由日本神奈川县佐佐木信义申请的用于熔模铸造的型芯,制这种型芯的方法,以及制内部包含所述型芯的熔模铸造铸型的方法(申请号为87105530),其开发出了水玻璃加热固化法生产熔模铸造用型芯的生产技术,离心铸造该技术的要点是在石英砂中加入一定量的水玻璃,然后通热空气(约150℃)硬化,硬化后的砂芯在硅酸乙酯溶液中浸泡,烘干,再涂挂硅酸乙酯锆英粉涂料,该法的缺点也是砂芯常温强度低而且易变形、脱芯较困难,芯砂、砂芯的存放性差,难以组织大批量生产。
本发明结合熔模铸造工艺的特点,为了解决低成本砂芯常温强度低、铸件脱砂及芯砂、砂芯存放性差、不适应大批量流水生产的问题,提出一种熔模铸造用树脂砂芯的生产方法即按重量百分比,在65~85份SiO2含量不小于90%的石英砂中加入助熔剂15~35份,然后加入占骨料重量百分比2%~8%的液态铸造树脂与占树脂量15%~60%的树脂固化剂,混匀后加入占粉料重量3%~10%的高温粘结剂再混匀,制芯,然后涂挂石英粉耐水烧结型涂料。该方法在硅砂中加入适宜比例的低熔点助熔剂,有效地提高高温粘结剂在1000℃温度下的烧结性能,从而保证砂芯浇注时的强度要求。同时采用液态树脂作为粘结剂,能极大地提高砂芯的常温强度、尺寸精度及生产效率,砂芯表面质量好,芯砂和砂芯的存放性能好,能满足大批量生产的需要。在芯砂中加入高温粘结剂,与铸造树脂混合均匀,确保高温粘结剂在砂芯中均匀分布,保证砂芯的高温强度。使用石英粉耐水烧结型涂料,有效地提高涂料的烧结性能,从而提高砂芯的高温强度,保证砂芯浇注时不发生断芯;石英粉涂料中加有耐水型粘结剂,可以保证砂芯在脱蜡过程中有效地抵御热水及蒸汽对砂芯的煮泡而不损坏、表面不掉砂。
具体实施例方式本熔模铸造用树脂砂芯的生产方法,是按重量百分比,在65~85份石英砂中加入助溶剂15~35份,干混均匀后,加入占骨料重量百分比2%~8%的液态铸造树脂与占树脂量15%~60%的液态固化剂,混匀后加入占粉料重量3%~10%的高温粘结剂再混1min,制得树脂芯砂后,用此芯砂在射芯机上进行机器制芯或采用手工在芯盒中制芯,砂芯经去毛刺修整后,涂挂石英粉耐水烧结型涂料,并在105℃~110℃温度下烘干,待用。其中石英砂中的SiO2含量不小于90%;助熔剂是100目~320目的含SiO2≥95%石英粉,200目吸蓝量≥30mL/100g土的膨润土。液态铸造树脂为铸造用热芯盒树脂、冷芯盒树脂和自硬砂树脂,包括无氮呋喃树脂(含氮量≤0.5%)、低氮呋喃树脂(含氮量≤3.5%)、中氮呋喃树脂(含氮量为6.5%~8.5%)和呋喃I型树脂(含氮量为11%~13%)以及液态酚醛树脂、Pep-Set酚醛树脂、胺催化冷芯盒树脂、SO2固化的呋喃树脂等。液态固化剂是有机酸(盐)、无机酸(盐),包括对甲苯磺酸水溶液、苯磺酸水溶液、NH4Cl水溶液、磺酸铜水溶液、CuCl2水溶液、60%~90%的磷酸溶液。高温粘结剂是工业用一级硅溶胶、硅酸乙酯水解液及两者的混合液。砂芯的制芯机器是热芯盒射芯机、冷芯盒制芯机,手工制芯包括自硬砂工艺和手工制芯并进行烘烤的工艺。耐水烧结型涂料的如下200目~320目石英粉 100%硅溶胶(工业一级品) 5~10%(占石英粉重量)膨润土(铸造级,人工钠基) 2~3% (占石英粉重量)白乳胶(工业一级品) 4~6% (占石英粉重量)CMC0.2~0.3% (占石英粉重量)水 80%~100%(占石英粉重量)表面活性剂 0.1% (占石英粉重量)正辛醇 0.1% (占石英粉重量)实施实例一(1)铸件基本情况铸件名称单向管接头铸件材质YZG25铸件重量70g
(2)芯砂配比21Q擦洗石英砂(SiO2含量为93%) 1000g200目石英粉(SiO2含量为99%) 200g热芯盒低氮呋喃树脂(含氮量3.0%)36g对甲苯磺酸水溶液(PTSA∶H2O=6.5∶3.5) 9g硅溶胶(工业一级品) 48g(3)混砂工艺在容量为5000g的碾轮式混砂机中加入1000g石英砂与200g石英粉干混1min,加入9g甲苯磺酸水溶液混1min,再加入36g低氮呋喃树脂混1min,后加入48g硅溶胶混1min,出砂,盛放在容器中待用。
(4)制芯工艺采用Z861型热芯盒射芯机制芯,将预制好的符合砂芯形状的金属芯盒安装在制芯机上,芯盒温度控制在230℃±10℃,射砂压力0.5~0.7MPa,固化时间60s~80s,制取所需形状和尺寸的砂芯。
(7)砂芯使用制好的砂芯经涂料及烘干、修整与检验合格后,即可用于铸造生产。制蜡模时,将砂芯置于压型内,按常规方法进行压蜡模、脱模、修模、组装模组,以及进行制壳、脱蜡,形成带有砂芯的型壳,然后按常规方法进行焙烧后,将温度为1550℃~1600℃的中碳钢液浇入温度为500℃~600℃的型壳内。铸件凝固、冷却后,去除模壳、浇冒口,将铸件放入抛丸清理滚筒内清理30min,取出铸件,进行修整,检验合格后即成为铸件成品。
铸件名称管接头组铸件材质YZG35铸件重量2.10Kg铸件结构特征见图2,2为砂芯。
(2)芯砂配比21Q擦洗石英砂(SiO2含量为93%) 2000g200目石英粉(SiO2含量为99%) 300g热芯盒低氮呋喃树脂(含氮量3.0%) 92g磷酸溶液(浓度为80%) 18g硅溶胶(工业一级品) 92g(3)混砂工艺在容量为5000g的碾轮式混砂机中加入2000g石英砂与300g石英粉干混1min,加入18g磷酸溶液混1min,再加入92g低氮呋喃树脂混min,后加入92g硅溶胶混1min,出砂,盛放在容器中待用。
(4)制芯工艺采用手工制芯,在温度为180℃±10℃的烘箱内烘烤20分钟。
(7)砂芯使用制好的砂芯经涂料及烘干、修整与检验合格后,即可用于铸造生产。制蜡模时,离心铸造将砂芯置于压型内,按常规方法进行压蜡模、脱模、修模、组装模组,以及进行制壳、脱蜡,形成带有砂芯的型壳,然后按常规方法进行焙烧后,将温度为1550℃~1600℃的钢液浇入温度为500℃~600℃的型壳内。铸件凝固、冷却后,去除模壳、浇冒口,将铸件放入抛丸清理滚筒内清理30min,取出铸件,进行修整,检验合格后即成为铸件成品。
1.一种熔模铸造用树脂砂芯的生产方法即按重量百分比,在65~85份SiO2含量不小于90%的石英砂中加入助熔剂15~35份,然后加入占骨料重量百分比2%~8%的液态铸造树脂与占树脂量15%~60%的液态固化剂,混匀后加入占粉料重量3%~10%的高温粘结剂再混匀,制芯,然后涂挂石英粉耐水烧结型涂料。
2.如权利要求1所述的熔模铸造用树脂砂芯的生产方法,其特征在于所述助溶剂是100目~320目的SiO2含量不小于95%石英粉、200目的吸蓝量不小于30mL/100g土的膨润土。
3.如权利要求1所述的熔模铸造用树脂砂芯的生产方法,其特征在于所述液态铸造树脂为铸造用热芯盒树脂、冷芯盒树脂和自硬砂树脂,包括无氮呋喃树脂、低氮呋喃树脂、中氮呋喃树脂和呋喃I型树脂以及液态酚醛树脂、Pep-Set酚醛树脂、胺催化冷芯盒树脂、SO2固化的呋喃树脂。
4.如权利要求1所述的熔模铸造用树脂砂芯的生产方法,其特征在于所述液态固化剂是有机酸或有机酸盐、无机酸或无机酸盐,包括对甲苯磺酸水溶液、苯磺酸水溶液、NH4Cl水溶液、磺酸铜水溶液、CuCl2水溶液、60%~90%的磷酸溶液。
5.如权利要求1所述的熔模铸造用树脂砂芯的生产方法,其特征在于所述高温粘结剂是硅溶胶、硅酸乙酯水解液及两者的混合液。
6.如权利要求1所述的熔模铸造用树脂砂芯的生产方法,其特征在于所述耐水烧结型涂料的如下200目~320目石英粉 100%硅溶胶(工业一级品) 5~10%(占石英粉重量)膨润土(铸造级,人工钠基)2~3% (占石英粉重量)白乳胶(工业一级品) 4~6% (占石英粉重量)CMC 0.2~0.3% (占石英粉重量)水 80%~100%(占石英粉重量)表面活性剂 0.1% (占石英粉重量)正辛醇 0.1% (占石英粉重量)
本发明涉及一种熔模铸造用树脂砂芯的生产方法即按重量百分比,在65~85份SiO
以上信息由江苏亚立特钢有限公司整理编辑,了解更多离心铸造信息请访问http://www.jsyltg.com