新闻中心
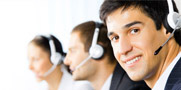
咨询热线:
134-0554-5577
邮件:874556408@qq.com
电话:0523-83984388
地址:江苏省兴化市沈伦镇工业园区沈北路
离心铸造般不能重复使用 √ 工件受力变
名词解释_农学_高等教育_教育专区。名词解释 避免空走刀;或是车削完后把工件从原材料上切下来。 (4.3) 表面质量:通过加工方法的控制,使零件获得不受损伤甚至有所增强的表面状态。包括表面 的几何形状特征和表面的物理力学性能状态。 标注
名词解释 避免空走刀;或是车削完后把工件从原材料上切下来。 (4.3) 表面质量:通过加工方法的控制,使零件获得不受损伤甚至有所增强的表面状态。包括表面 的几何形状特征和表面的物理力学性能状态。 标注角度与工作角度刀具的标注角度是刀具制造和刃磨的依据,主要有:前角、后角、主偏 角、副偏角和刃倾角。切削加工过程中,由于刀具安装位置的变化和进给运动的影响,使得 参考平面坐标系的位置发生变化, 从而导致了刀具实际角度与标注角度的不同。 刀具在工作 中的实际切削角度称为工作角度。 粗基准—— 未经过机械加工的定位基准称为粗基准。 常值系统误差当连续加工一批零件时,这类误差的大小和方向或是保持不变 刀具耐用度:是指刃磨后的刀具从开始切削至磨损量达到磨钝标准为止所用的切削时间 刀 具标注后角:后刀面与切削平面之间的夹角 刀具标注前角:基面与前刀面的夹角 刀具寿命是指一把新刀具从开始投入使用直到报废为止的总切削时间 定位:使工件在机床 或夹具中占有准确的位置。 定位基准在加工时,用以确定工件在机床上或夹具中正确位置所采用的基准 积屑瘤粘附到刀具的前刀面上靠近刀刃处, 形成的一块很硬的楔状金属瘤, 通常称为积屑瘤, 也叫刀瘤, 机械加工工艺系统在机械加工中,由机床、刀具、夹具与被加工工件 一起构成了一个实现某 种加工方法的整体系统, 机械加工工艺规程把工艺过程的有关内容, 用工艺文件的形式写出来, 称为机械加工工艺规 程。 机械加工表面质量, 是指零件在机械加工后被加工面的微观不平度, 也叫粗糙度 精基准:用 加工过的表面作定位基准,这种定位基准称为精基准。 基准:零件上用以确定其他点、线、面位置所依据的那些点、线) 夹紧:在工件夹紧后用外力将其固定,使其在加工过程中保持定位位置不变的操作。 加工精度:零件加工后的实际几何参数和理想几何参数符合程度。加工误差:零件加工后的 实际参数和理想几何参数的偏离程度。 金属的可焊性——指被焊金属在采用一定的焊接方法、焊接材料、离心铸造工艺参数 及结构型式的 条件下,获得优质焊接接头的难易程度。 金属的可锻性 指金属接受锻压加工的难易程度。 金属可锻性好, 表明金属易于锻压成型。分 型面—— 两个铸型相互接触的表面,称为分型面。 过定位:也叫重复定位,指工件的某个自由度同时被一个以上的定位支撑点重复限制。 工 步:在加工表面不变,加工刀具不变,切削用量不变的条件下所连续完成的那部分工序。 工 序—— 机械加工过程中,一个或一组工人在一个工作地点,对一个或一组工件连续完成的 那部分工艺过程,称为工序。 工序集中就是将零件的加工集中在少数几道工序中完成,每道工序加工的内容多 工序分散: 工序数多而各工序的加工内容少 工序余量:相邻两工序的尺寸之差,也就是某道工序所切除的金属层厚度 工艺能力系数使公差δ 和△随(6σ )之间有足够大的比值,这个比值 Cp 工艺过程:在生产过程中凡是改变生产对象的形状、尺寸、位置和性质等使其成为成品或半 成品的过程。 工艺规程:人们把合理工艺过程的有关内容写成工艺文件的形式,用以指导 生产这些工艺文件即为工艺规程 工艺基准:在加工和装配中使用的基准。包括定位基准、度量基准、装配基准。 工艺系统 刚度:指工艺系统受力时抵抗变形的能力 六点定位原理:采用六个按一定规则布置的支承点,并保持与工件定位基准面的接触,限制 工件的六个自由度,使工件位置完全确定的方法。 磨削:以砂轮的高速旋转与工件的移动或转动相配合进行切削加工的方法。 (6.1) 内联系传 动链:执行件与执行件之间的传动联系 逆铣——铣刀旋转方向与工件进给方向相反。铣削时每齿切削厚度 ac 从零 逐渐到而切 出。 零件结构工艺性——指零件在满足使用要求的前提下, 其结构在具体生产条件下便于经济地 制造、维护。 切削运动:金属切削加工时,刀具与工件之间的相对运动。 (1.1) 切削力:切削时,使被加 工材料发生变形成为切屑所需的力称为切削力 切断: 在车削加工中, 当工件的毛坯是棒料且很长时, 需根据零件长度进行切断后再加工,切 削速度:主运动的速度 强迫振动:指在有周期性外力(相对于切削过程而言)干扰下产生的振动运动。 欠定位——为满足工件加工精度的要求必须约束的自由度没有被约束的定位称为欠定 位。 前角γ 0:在正交平面内测量的前刀面和基面间的夹角。 顺铣和逆铣 答:在切削部位刀齿的旋转方向和零件的进给方向相同时为顺铣。在切削部位 刀齿的旋转方向和零件的进给方向相反时为逆铣。 顺铣—— 铣刀旋转方向与工件进给方向相同。铣削时每齿切削厚度 ac 从逐渐减小到 零。 外联系传动链:机床动力源和运动执行机构之间的传动联系 设计基准:在设计图样 上所采用的基准 误差复映现象:待加工表面上有什么样的误差,加工表面上必然也有同样性质的误差,这就 是切削加工中的误差复映现象 误差敏感方向:过切削刃上的一点并且垂直于加工表面的方向。 硬质合金是一种具有高硬度,良好耐磨性,红硬性及一定的抗弯强度的工具材料. 原始误差: 由 机床,离心铸造刀具,夹具,和工件组成的工艺系统的误差。 自激振动:机械加工中的自激振动是指在没有周期性外力(相对于切削过程而言)干扰下产 生的振动运动。 装配:按照规定的技术要求,将若干个零件接合成部件或将若干个零件和 部件接合成产品的劳动过程。 (8.1) 装配尺寸链指的是零件在装配过程的尺寸链 而工艺尺寸链一般是指零件加工过程的尺寸 链 装夹:就是定位和夹紧过程的总和。 主轴回转误差:指主轴瞬间的实际回转轴线相对其平均回转轴线的变动量。 .误差复映:由于加工系统的受力变形,工件加工前的误差以类似的形状反映到加工后的工件 上去,造成加工后的误差 装配精度:一般包括零、部件间的尺寸精度,位置精度,相对运动精度和接触精度等 二、 判断题: (×)C6140 型机床是工件回转直径为 40mm 的普通车床。 (√ )轴类零件加工时,往往先加工两端面和中心孔,并以此为定位基准加工所有外圆表 面,这样既满足了基准重合原则,又满足基准统一原则。 (√ )粗基准只在道工序中 使用,一般不能重复使用。 (× )机械加工工艺过程是由一系列的工位组成。 (√ )车削细长轴时,容易出现腰鼓形的圆柱度误差。 (√ )展成法加工齿轮是利用齿轮刀具与被切齿轮保持一对齿轮啮合运动关系而切出齿形 的方法。 (×)欠定位在加工过程中是允许存在的。 (√ ) 工艺系统刚度主要取决于薄弱环节的刚度。 (× )工件受力变形产生的加工误差是在工件加工以前就存在的。 (×)零件的表面层金 属发生冷硬现象后,其强度和硬度都有所增加。离心铸造 (√)在中等速度切削加工时,热效应使硬质合金刀具产生磨损,其主要形式包括:相变磨 损、扩散磨损和氧化磨损。 (×)零件的表面层金属发生冷硬现象后,其强度和硬度都有所增加。 (× )加工原理误 差在加工过程中可以消除。 (√ )过定位在加工过程中允许存在。 (√)机械加工工艺过程是由一系列的工序组成。 (× )为保证不加工表面与加工表面之 间的相对位置要求,一般应选择加工表面为粗基准。 (× )在两个不同的工序中,都使用 同一个定位基准,即为基准重合原则。 (√)长定位心轴给孔定位,孔轴的接触长度与直径之比大于 1 时,可以消除工件的四个自 由度。 (√)工件受热变形产生的加工误差是在工件加工过程中产生的。 车床的主运动是工件的旋转运动,进给运动是刀具的移动。 ( √ ) .钻床的主运动是 钻头的旋转运动,进给运动是钻头的轴向移动。 ( √) 铣床的主运动是刀具的旋转运 动,进给运动是工件的移动。 (√ ) 牛头刨床刨斜面时,主运动是刨刀的往复直线运动,进给运动是工件的斜向间歇移动。X 龙 门刨床刨水平面时,主运动是刨刀的往复直线运动,进给运动是工件的横向间隙移动。X 6. 车床的主运动和进给运动是由两台电动机分别带动的。 ( X ) 7.立铣的主运动和 进给运动是由一台电动机带动的。 ( X ) 8.牛头刨床的切削速度是指切削行程的 平均速度。 ( X ) 9. 车 槽 时 的 背 吃 刀 量 ( 切 削 深 度 ) 等 于 所 切 槽 的 宽 度。 ( √ ) 10. 刀 具 前 角 是 前 刀 面 与 基 面 的 夹 角 , 在 正 交 平 面 中 测 量。 ( √ )11.刀具后角是主后刀面与基面的夹角, 在正交平面中测量。 ( X ) 12.刀具主偏角是主切削平面与假定工作平面间的夹角(即主切削刃在基面的投影与进给方 向的夹角。 ( √ )13.工艺系统刚度较差时 (如车削细长轴) , 刀具应选用较大的主偏角。 ( √ ) 14.在切削用量中,对切削力影响的是前角和后 角。 ( X ) 15.CA6140 型 机 床 是 大 工 件 回 转 直 径 为 140mm 的 卧 式 车 床。 ( X ) 16.X5020 立式升降台铣床的工作台面宽度为 200mm。 ( √ ) 17.在加工质量方面,铣削和刨削一般同级,但对于尺寸较大的平面,由于刨削无明显的接 刀痕,故刨削优于铣削。 ( √ ) 磨削过程实际上是许多磨粒对工 件表面进行切削、刻划和滑擦(摩擦抛光)的综合作用过程。 ( √ ) 19.磨具的组织标注出磨具中磨料、结合剂和气孔三者之间不同体积的比例关系。(√) 20.磨 具的硬度是指组成磨具的磨料的硬度。(X) 21.光磨可提高工件的形状精度和位置精度。(X) 长定位心轴给孔定位,孔轴的接触长度与直径之比大于 1 时,可以消除工件的四个自由度 ( √ ) 机械加工工艺过程是由一系列的工位组成 X 车削细长轴时,容易出现腰鼓形的圆柱度误差( √ ) 轴类零件加工时,往往先加工两端面和中心孔,并以此为定位基准加工所有外圆表面,这样 既满足了基准重合原则,又满足基准统一原则( √ ) 零件的表面层金属发生冷硬现象后,其强度和硬度都有所增加( √ ) 刀具的标注角度随 着刀具的安装条件和进给量的大小变化而变化( √ ) 在两个不同的工序中,都使用同一 个定位基准,即为基准重合原则 X 展成法加工齿轮是利用齿轮刀具与被切齿轮保持一对齿轮啮合运动关系而切出齿形的方法 ( √ ) 积屑瘤的产生会引起刀具角度变化,如前角变大,故积屑瘤是有利的。X 粗基准只在道 工序中使用,一般不能重复使用( √ ) 工件受力变形产生的加工误差是在工件加工以前 就存在的。X 为保证不加工表面与加工表面之间的相对位置要求,一般应选择加工表面为粗基准 X 加工 原理误差在加工过程中可以消除 X 机床的主运动可有一个或几个,进给运动只能有一个。X 长定位心轴给孔定位,孔轴的接触 长度与直径之比大于 1 时,可以消除工件的二个自由度 X 根据六点定位原理分析图中车削 外圆的定位方案,该定位方案属不完全定位( √ ) 简答体 1. 刀具切削部分材料应具哪些基本性能? 2. 机械加工过程中定位精基准的选择原则是什么? 选择精基准一般应遵循以下几项原则: (1)基准重合原则 应尽可能选择所加工表面的工序基准为精基准,这样可以避免由于 基准不重合引起的定位误差。 (2)统一基准(基准不变)原则 应尽可能选择用同一组精基准加工工件上尽可能多的表 面,以保证所加工的各个表面之间具有正确的相对位置关系。 (3)互为基准原则 当工件上两个加工表面之间的位置精度要求比较高时,可以采用两 个加工表面互为基准的方法进行加工。 (4)自为基准原则 一些表面的精加工工序,要求加工余量小而均匀,常以加工表面自 身为精基准进行加工。 上述四项选择精基准的原则,有时不可能同时满足,应根据实际条件决定取舍。 机械加工 工序顺序的安排原则 1) 先基准面后其它 2) 先粗后精 3) 先主后次 4) 先面后孔 何为工件的残余应力?产生工件的残余应力的原因是什么? p174 8.夹具的基本组成有哪 些? (1) 定位元件:确定工件正确位置的元件; (2) 夹紧装置:使工件在外力作用下仍能保持其正确定位位置的装置; (3) 对刀元件、导向元件:夹具中用于确定(或引导)刀具相对于夹具定位元件具 有正确位置关系的元件; (4) 夹具体:用于联接夹具元件和有关装置使之成为一个整体的基础件,夹具通过 夹具体与机床联接; (5) 其他元件及装置:其他部分可根据需要设置。 7. 什么是库存?简述零库存和安全库存的区别与联系. 库存使企业满足未来需要而暂时闲置的资源。 零库存是指企业在正常生产的情况下,使库存资源为零。 安全库存是指企业在正常生产的 情况下,使库存资源为少。 这里要指明库存的利弊:占用资金,减少利润;防止短缺,缓解供需矛盾,均衡生产;投机 居奇。对于正常的生产企业,零库存是一种理想状态,而安全库存是正常状态,但在原料和 产品在市场上短缺的状态, 必须要有足够的库存, 因此前述零库存和安全库存此时都是不存 在的。因此,可说零库存是安全库存的一个趋向,但不能等同。 什么是装配?保证装配精 度的工艺方法有那些? 根据规定的技术要求,将零件或部件进行配合和联接,使之成为半成品或成品的过程,称为 装配。 (2)互换装配法、分组装配法、修配装配法、调整装配法 提高加工精度的途径有哪 些? (1)减小原始误差 (2)转移原始误差 (3)均分原始误差 (4)均化原始误差 (5)误差补偿 2、 锻前加 热的目的? 提高金属塑性、降低变形抗力,使其易于流动成型并获得良好的锻后组织。 3、防止焊接变 形的措施? (1)焊缝的布置和坡口型式尽可能对称,离心铸造焊缝的截面和长度尽可能小; (2)焊前组装 时,采用反变形法; (3)刚性固定法 (4)采用能量集中的焊接方法、小线能量、合理的焊接顺序。 4、什么是切削用量的三要 素? 在一般的切削加工中,切削变量包括切削速度、进给量和切削深度三要素。 2、常用车床种 类有哪些?解释 CA6140 型号的含义。 (4.1) 答:车床的种类很多,大致可分为卧式车床、立式车床、转塔车床、仿形车床、多刀车床、 自动车床等。其中,CA6140 型卧式车床是常用的车床,C 表示类代号(车床类) ,A 表示 结构特性代号(加重型) , 6 表示组代号(落地及卧式车床组) ,1 表示系代号(卧式车床系) , 40 表示主参数代号(车床工件回转直径为 ㎜) 。 3、为什么通常采用逆铣而不采用 顺铣?(5.3) 答: 铣削时,工作台的纵向进给如果没有顺铣机构,顺铣过程中由于铣削力的变化,易引 起工作台无规则的窜动,影响加工质量。如果铣床没有顺铣机构或加工有硬皮的铸件、锻件 毛坯或加工硬度较高的工件时,一般都采用逆铣。 4、比较车床、铣床和磨床的主运动和进给运动?(6.1) 答: 主运动 进给 运动 车床 工件的旋转运动 车削外圆时车刀平行于工件轴线的纵向运动 铣床 铣刀的旋 转运动 工件相对铣刀作纵向或横向运动 磨床 砂轮的旋转运动 工件的低速旋转 和直线移动 影响加工余量的因素有哪些? (1)上工序留下的表面粗糙度值和表面缺陷层深度 (2)上工序的尺寸公差 (3)Ta 值没 有包括的上工序留下的空间位置误差 (4)本工序的装夹误差 7 试述制定机械加工工艺规程 的步骤。 答: (1)确定生产类型; (2)零件工艺分析; (3)确定毛坯制造方式; (4)选择 定位基准拟定工艺路线)确定各工序的设和工艺装; (6) 确定加工余量、工序尺寸; (7)确定切削用量及时间定额; (8)填写工艺文件。 8 试述减小零件表面粗糙度值的工艺 措施。 答: (1)减少残留面积高度 减小主偏角、副偏角和进给量及增大刀尖圆弧半径,减小残留面积高度;(2)避免积屑瘤、 刺痕的产生 可用改变切削速度的方法,来抑制积屑瘤的产生。如果用高速钢车刀,应降低切削速度;用 硬质合金车刀时,应提高切削速度,增大车刀前角能有效地抑制积屑瘤的产生。 (3)防止 和消除振纹 车削时,离心铸造由于工艺系统的振动,而使工件表面出现周期性的横向或纵向的振纹。调整主轴间 隙、提高轴承精度;合理选择刀具参数,经常保持切削刃光洁、锋利。增加工件的安装刚 性; (4)合理选择运用切削用量 在工件材料、刀具几何参数、车床等切削条件一定的情况下,选择切削用量对表面粗糙度有 很大的影响。尽可能提高生产效率和保证必要的刀具寿命。首先选择尽可能大的切削深度, 然后再选取合适的进给量, 后在保证刀具经济耐用度的条件下, 尽可能选取较大的切削速 度; (5)合理选用切削液,保证充分冷却润滑 采用合适的切削液是消除积屑瘤、鳞刺和减小表面粗糙度值的有效方法。 3、工件在锻造前为什么要加热?什么是金属的始锻温度和终锻温度?若过高和过低将对锻 件产生什么影响? 答:随着温度升高,原子动能升高,削弱了原子之间的吸引力,减少了滑移所需要的力,因 此塑性增大,变形抗力减小,提高了金属的锻造性能。变形温度升高到再结晶温度以上时, 加工硬化不断被再结晶软化消除,金属的铸造性能进一步提高。 金属锻造加热时允许的温度为始锻温度,停止锻造的温度称为终锻温度。 加热温 度过高,会使晶粒急剧长大,导致金属塑性减小,锻造性能下降。如果加热温度接近熔点, 会使晶界氧化甚至熔化, 导致金属的塑性变形能力完全消失。 4、 切削热是怎样产生? 它对切削加工有何影响? 答:切削加工过程中,切削功几乎全部转化为热能,将产生大量的热量,将这种产生于切削 过程的热量称为切削热。其来源主要有 3 种: (1)切屑变形所产生的 热量,是切削热的主要来源。 (2)切屑与刀具前刀面之间的摩擦所产生的 热量。 (3)零件与刀具后刀面之间的摩擦所产生的热 量。 传入零件的切削热,使零件产生热变形,影响加工精度,特别是加工 薄壁零件、细长零件和精密零件时,热变形的影响更大。磨削淬火钢件时,磨削温度过高, 往往使零件表面产生烧伤和裂纹,影响零件的耐磨性和使用寿命。 传入刀具的切削热,比例虽然不大,但由于刀具的体积小,热容量小,因而温度高,高速 切削时切削温度可达 1000 度,加速了刀具的磨损。 5、什么是砂轮的自 锐作用? 答: 砂轮上的磨粒钝化后,使作用于磨粒上的磨削力增大,从而促使砂轮表面磨粒自动脱 落,里层新增粒锋利的切削刃则投入切削,砂轮又恢复了原有的切削性能。砂轮的此种能力 称为“自脱性” 。 1.什么是误差复映,减少复映的措施有哪些? 误差复映: 指工件加工后仍然具有类似毛坯误差的现象 (形状误差、 尺寸误差、 位置误差) 措 施:多次走刀;提高工艺系统的刚度 2.什么是磨削烧伤?影响磨削烧伤的因素有哪些? 磨削烧伤:当被磨工件的表面层的温度达到相变温度以上时,表面金属发生金相组织的变 化, 使表面层金属强度硬度降低, 并伴随有残余应力的产生, 甚至出现微观裂纹的现象。 影 响因素:合理选择磨削用量;工件材料;正确选择砂轮;改善冷却条件。 3.什么是传动链误 差?提高传动链传动精度的措施有哪些? 传动链误差:指传动链始末两端传动元件间相对 传动的误差。 措施:缩短传动链;降速传动,末节大降速比;提高传动元件的制造精度和装配精度;误 差补偿装置。 4.减少工艺系统受热变形的措施? 减少发热和隔热;改善散热条件;均衡温度场;改进机床机构;加快温度场的平衡;控制 环境温度。 5.什么是工艺系统的刚度?误差产生的原因? 工艺系统刚度:垂直作用于工件加工表面(加工误差敏感方向)的径向切削分力与工艺系 统在该方向的变形之间的比值。 原因:在机械加工过程中,机床、夹具、刀具、和工件在切削力的作用下,都将分别产生 变形 y 机、y 夹、y 刀、y 工,致使刀具和被加工表面的相对位置发生变化,使工件产生误 差。 6.工艺规程的设计规则? 所设计的工艺规程应能包装零件的加工质量(或机器的装配质量) ,达到设计图样上规定的 各项技术要求; 应使工艺过程具有较高的生产率,使产品尽快投放市场; 设法降低制造成本; 注意减轻工人的劳动程度,保证生产安全; 7.什么是粗基准?精基准?选择原则? 精基准: 用加工过的表面作为静基准; 基准重合原则, 基准统一原则, 互为基准, 自为基准 粗 基准:选用工件上未加工的表面作为基准; 保证零件加工表面相对于不加工表面具有一定位置精度的原则 合理分配加工余 量的原则 便于装夹的原则 粗基准一般不得重复使用的原则 8.什么叫加工余量?影响加工余量的因素? 加工余 量:毛坯上留作加工用的表面层 影响因素:上工序留下的表面粗糙度和表面缺陷层深度 上工序的尺寸公差 尺寸公差中没有包括的上工序留下的空间位置误差 本工序的装夹误差 9.什么 叫时间定额?组成部分? 时间定额:在一定的生产条件下规定生产一件产品或完成一道工序所消耗的时间。 组成部分: 基本时间、 辅助时间、 布置工作地时间、 休息和生理需要时间、 准与终结时间 10. 夹具的工作原理? 使工件在夹具中占有正确的加工位置。这是通过工件各定位面与夹具的相应定位元件的定 位工作面(定位元件上起定位作用的表面)接触、配合或对准来实现的; 夹具对于机床应先保证有准确的相对位置,而夹具结构又保证定位元件定位工作面对夹具 与机床相连接的表面之间的相对准确位置, 这就保证了夹具定位工作面相对机床切削运动形 成表面的准确几何位置,也就达到了工件加工面对定位基准的相互位置精度要求。 使刀具相对有关的定位元件的定位工作面调整到准确位置,这就保证了刀具在工件上加工 出的表面对工件定位基准的位置尺寸。 11.什么叫定位误差?定位误差产生的原因? 设计基准在工序尺寸方向上的位置变动 量 原因:定位基准和设计基准不重合产生的定位误差 定位副制造不准确产生的定位误 差 12.夹紧力的确定原则? 方向确定原则: 垂直于主要的定位基准面 使夹紧力小 使工件变形小 作用点的确定原则: 应落在支承元件或几个支承元件形成的稳定受力区域内 落在工件刚性好的部位 尽可能靠近加工面,这可减少切削力对夹紧力的力矩,从而减轻工件的振动 大小确定的 原则: 切削力,类比法,实验法 13.机械加工工序安排的原则? 先加工定位基准面在加工其他 面 先加工主要表面在加工次要表面 先粗加工后精加工 先加工面后加工孔 14.影响表面粗糙度的因素? 切削加工:刀具几何形状的复映;工件材料的性质;切削用量;切削液。 磨削加工:砂轮的粒度;砂轮的硬度;砂轮的修整;磨削速度;磨削径向进给量与光磨次 数;工件的圆周进给速度和轴向进给量;冷却液润滑。 15.减少原始误差的措施? 减少原始误差;转移原始误差;均分原始误差;均化原始误差;误差补偿。 3、为什么要划 分加工阶段?(5 分) 答:1)有利于保证加工质量 2)合理使用设 3)便于安排热处理工序 4)及时发现毛坯缺陷 5)精加工安排在后也可避免精加工好的表面受到损伤。 4、为什么说夹紧不等于定位?(4 分) 答:定位的含义是使工件相对于机床和刀具处于一个正确的加工位置。工件定位后,为了使 其在加工中不改变正确位置,还要夹紧、夹牢。 6、什么是自位支撑?它与辅助支撑有何不同(4 分) 答:具有几个可自由活动支承点的支 承称为自位支承。自位支承作用相当于一个固定支承点,只限制一个自由度。 辅助支承是在工件定位后, 由于工件的刚性较差, 在切削力、 夹紧力或工件本身重力作用下, 引起工件变形,影响工件加工质量,需要增设辅助支承。辅助支承不起定位作用,必须于工 件定位夹紧后才参与工作 7、什么叫基准重合?当“基准统一”时是否会产生基准不重合误差?(5 分) 定位基准与设计基准重合;基准重合是针对一道工序的, “基准统一”是针对多道工序的, 因此, “基准统一”不一定基准重合,会产生基准不重合误差。 5.改善材料切削加工性的 措施有哪些? 答:在实际生产过程中,常采用适当的热处理工艺,来改变材料的金相组织 和物理机械性能,从而改善金属材料的切削加工性。例如,高碳钢和工具钢经球化退火,可 降低硬度;中碳钢通过退火处理的切削加工性;低碳钢经正火处理或冷拔加工,可降低 塑性,提高硬度;马氏体不锈钢经调质处理,可降低塑性;铸铁件切削前进行退火,可降低 表面层的硬度。 另外,选择合适的毛坯成形方式,合适的刀具材料,确定合理的刀具角 度和切削用量,安排适当的加工工艺过程等,也可以改善材料的切削加工性能。 3.叙述粗、 精基准的选择原则,加工顺序安排原则。 答: 粗基准的选择原则:保证加工表面相对于不加工表面具有一定位置精度的原则;合理 分配加工余量的原则;便于装夹的原则;粗基准一般不得重复使用的原则。 精基准的选择 原则:基准统一、基准重合、互为基准、自为基准的原则。 4.试述夹紧力的确定原则。 答:夹紧力的方向:应使定位基面与定位元件接触良好,保证零件定位准确可靠;应与工件 刚度的方向一致;尽量与切削力重力方向一致。 夹紧力的作用点:应正对支承元件或 位于支承元件所形成的支承面内。应位于工件刚度较好的部位应尽量靠近加工表面。 7.什么是回火烧伤?为什么磨削加工容易产生烧伤? 答:磨削区的温度超过未超过淬火钢的相变温度,但已超过马氏体的转变温度,工件表层金 属的回火马氏体组织将转变成硬度较低的回火组织索氏体或托氏体,这种烧伤称为回火烧 伤。磨削加工速度高,功率高、大于切削加工,大部分转变成热,传给工件表面温度升高, 引起烧伤。 8.为什么卧式车床床身导轨在水平面内的直线度要求高于垂直面内的直线度要求? 答:卧式车床床身导轨在水平面内的直线度误差产生在误差敏感方向,它将 1:1 地反映到 被加工工件上;而垂直面内的直线度误差是非误差敏感方向的误差,可以忽略不计。 什么 叫刚度?机床刚度曲线 分) 刚度是指切削力在加工表面法向分力,Fr 与法向的变形 Y 的比值。 机床刚度曲线特点:刚度曲线不是直线;加载与卸载曲线不重合;载荷去除后,变形恢复不 到起点。 端面车刀的切削部分的结构由哪些部分组成?绘图表示表示端面车刀的六个基本角度。 (8 分) 外圆车刀的切削部分结构由后刀面, 前刀面、 副后刀面、 主切削刃、 副切削刃与刀尖组成。六 个基本角度是:ro、α o、kr、kr’ 、λ s、α o’ 金属切削过程的本质是什么?如何减少金属切削变形? (8 分)被切金属在刀刃的挤压作用 下,产生剪切滑移变形,并转变为切屑的过程。要减少切削变形,可增大前角,提高速度, 增大进给量,适当提高工件材料硬度。 为什么灰铸铁具有良好的铸造性能? 灰铸铁的碳含量接近共晶成分,熔点较低,流动性好,又由于其结晶时析出石墨,所以收缩 率小,离心铸造不易产生缩孔、缩松、开裂等缺陷。所以具有优良的铸造性能。 2. 圆跳动和全跳动 有什么区别? 圆跳动是在某个截面上测量的,全跳动是某段长度上的圆跳动。 3. ①粗车的目的是什么? ②根据粗车的特点,对粗车刀应有什么要求? ①粗车的目的是尽快地从工件表面上切去大部分加工余量,使工件的形状和尺寸接近图 纸要求,为精车打下基础。 ②因它吃刀深度大、走刀快。所以粗车刀必须要有足够的强度,断屑条件要好。 4. 选择 钻削用量时应注意些什么? 钻大孔时,转速应低些,以免钻头急剧磨损,但进给量可适当增大,有利于生产率的提 高。钻小孔时,应提高转速,但进给量应小些,以免折断钻头。 5. 何谓“基准先行”原则? 主要加工表面的精基准应首先安排加工,以便后续工序使用它定位。精基准面的加工精 度,应能保证后续工序工件安装对基准面精度的要求。 6. 修配装配法有何特点?修配环应 如何选取? 特点:组成环可按经济精度制造,但可获得高的装配精度。 但增加了修配工作,生产效率低,对装配工人技术要求高。 修配环选择: (1)易于修配、便于装卸 (2)尽量不选公共环为修配环 (3)不能选择进行表面处理 的零件 1、述刀具磨损的种类及磨损过程。 简刀具磨损的种类分为:前刀面磨损、后刀面磨损、前后刀面磨损。 磨损过程:初期磨 损阶段、正常磨损阶段、急剧磨损阶段 2、简述外圆车削的装夹方法。 方法:三爪卡盘装夹、四爪卡盘装夹、一夹一顶、两装夹。 3、机械加工工艺过程应 划分为那几个阶段? (荒加工阶段) 、粗加工阶段、半精加工阶段、精加工阶段、光整加工 阶段 分析题 2 在三台车床上分别加工三批工件的外圆表面,加工后经测量,三批工件分别产 生了如 图 4-59 所示的形状误差,试分析产生上述形状误差的主要原因。 答(a) 是工件刚度不够 (b) 是导轨和主轴轴线不平行 (c) 前后支撑刚度不一致 3 加 工如图所示零件,其粗、精基准应如何选择(标有 符号的为加工面,其余为非加工 面)?图 a、b、c 所示零件要求内外圆同轴,端面与孔轴线垂直,非加工面与加工面间尽 可 能保持壁厚均匀;图 d 所示零件毛坯孔已铸出,要求孔加工余量尽可能均匀 答)a)A 2 1AAAAA8754 是增环,AAAA10 963 是减环 b)BBB3 21 是增环,B4 是减环
以上信息由江苏亚立特钢有限公司整理编辑,了解更多离心铸造信息请访问http://www.jsyltg.com