新闻中心
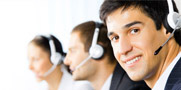
咨询热线:
134-0554-5577
邮件:874556408@qq.com
电话:0523-83984388
地址:江苏省兴化市沈伦镇工业园区沈北路
离心铸造尽量将浇口伸进金属模1/3~1/
理工学院 毕 业 设 计 学生姓名: 学 号: 08L0608122 专 业: 材料成型及控制工程 题 目: 小型滚筒式卧式离心铸造机的设计 指导教师: (讲师) 评阅教师: 2012 年 6 月 毕 业 设 计 中 文 摘 要 本文对滚筒形状离心铸件进行铸造工艺设计。 首先完成离心铸造工艺设计, 对于生产条件的确定以及离心机的选择并对离心铸造的浇注温度、 速度、 时间和铸型转动时间进行确定。 根据零件设计出衬套、 挡板和后盖, 画出其零件图, 并...
理工学院 毕 业 设 计 学生姓名: 学 号: 08L0608122 专 业: 材料成型及控制工程 题 目: 小型滚筒式卧式离心铸造机的设计 指导教师: (讲师) 评阅教师: 2012 年 6 月 毕 业 设 计 中 文 摘 要 本文对滚筒形状离心铸件进行铸造工艺设计。 首先完成离心铸造工艺设计, 对于生产条件的确定以及离心机的选择并对离心铸造的浇注温度、 速度、 时间和铸型转动时间进行确定。 根据零件设计出衬套、 挡板和后盖, 画出其零件图, 并组装成整体模具图。 利用重力系数公式计算铸型转速, 再根据公式计算转矩, 选择联轴器和离合器。 然后根据转速计算出小轴径, 进而设计出整体的轴, 并对轴进行了校核。 利用 CAD 绘制出小型滚筒式卧式离心铸造机的整体图形以及零件图。 关键词: 卧式, 离心铸造, 滚筒, CAD 毕 业 设 计 外 文 摘 要 Title Design of horizontal centerfugal casting machine with small drum shaped Abstract The drum shape centrifugal casting foundry process design. First to complete the design of centrifugal casting process to determine the rotation time of the production conditions to determine the centrifuge selection and centrifugal casting, pouring temperature, speed, time,and cast. Bushings, bezel and back cover, according to the part design to draw the parts diagram, and assembled into the overall die map. Gravity coefficient was calculated as the casting speed, according to the formula to calculate torque, select the couplings and clutches. According to speed to calculate the minimum shaft diameter, and then design the whole axis and the axis was calibrated. Use of CAD drawing overall graphics and parts diagram of a small drum horizontal centrifugal casting machine. Key Words Horizontal Centrifugal casting Roller CAD 本 科 毕 业 设 计 第 I 页共 II 页 目 录 1 绪论 .............................................................................................................................. 1 1.1 铸造简介 ................................................................................................................ 1 1.2 离心铸造简介 ........................................................................................................ 1 1.3 45 钢简介 ............................................................................................................... 3 1.4 离心铸管机的设计原则 ........................................................................................ 4 1.5 本课题研究的对象 ................................................................................................ 4 2 离心铸造工艺 .............................................................................................................. 5 2.1 生产条件的确定 .................................................................................................... 5 2.2 金属模涂料 ............................................................................................................ 6 2.3 浇注温度 ................................................................................................................ 8 2.4 浇注速度 ................................................................................................................ 8 2.5 浇注系统 ................................................................................................................ 8 2.6 铸型转动时间 ........................................................................................................ 9 3 离心铸管缺陷分析及预防 ........................................................................................ 10 3.1 合金钢管缺陷分析 .............................................................................................. 10 3.2 缺陷预防措施 ...................................................................................................... 10 4 模具设计 .................................................................................................................... 12 4.1 模具的结构 .......................................................................................................... 12 4.2 模具参数的计算 .................................................................................................. 12 4.3 铸型转速的计算 .................................................................................................. 14 5 零件的选择 ................................................................................................................ 17 5.1 联轴器的选择 ...................................................................................................... 17 5.2 离合器的选择 ...................................................................................................... 19 5.3 轴承的选择 .......................................................................................................... 20 6 轴的设计 .................................................................................................................... 22 6.1 轴长的确定 .......................................................................................................... 22 本 科 毕 业 设 计 第 II 页共 II 页 6.2 轴的校核 .............................................................................................................. 23 6.3 键与销的选取和校核 .......................................................................................... 25 结论.................................................................................................................................. 27 致谢 .................................................................................................................................. 22 参考文献 .......................................................................................................................... 22 本 科 毕 业 设 计 第 1 页共 29 页 1 绪论 1.1 铸造简介 1.1.1 铸造的定义 铸造[1]是熔炼金属, 制造铸型, 并将熔融金属浇入铸型, 凝固后获得具有一定形状、尺寸和性能金属零件毛坯的成型方法。 铸造是将金属熔炼成符合一定要求的液体并浇进铸型里, 经冷却凝固、 清整处理后得到有预定形状、 尺寸和性能的铸件的工艺过程。 铸造毛坯因近乎成形, 而达到免机械加工或少量加工的目的降低了成本并在一定程度上减少了制作时间。 铸造是现代装置制造工业的基础工艺之一。 1.1.2 铸造的发展 中国早期的铸件大多是农业生产、 宗教、 生活等方面的工具, 艺术色彩浓厚。 那时的铸造工艺是与制陶工艺并行发展的, 受陶器的影响很大。 中国约在公元前 1700~前1000 年之间已进入青铜铸件的全盛期, 工艺上已达到相当高的水平。 中国在公元前 513 年, 铸出了世界上早的铸铁件。 欧洲在公元八世纪前后也开始生产铸铁件。 铸铁件的出现, 扩大了铸件的应用范围。 18 世纪的工业革命以后, 蒸汽机、 纺织机和铁路等工业兴起, 铸件进入为大工业服务的新时期, 铸造技术开始有了大的发展。 进入 20 世纪, 铸造的发展速度很快, 其重要因素之一是产品技术的进步 , 要求铸件各种机械物理性能更好, 同时仍具有良好的机械加工性能; 另一个原因是机械工业本身和其他工业如化工、 仪表等的发展, 给铸造业创造了有利的物质条件。 1.1.3 铸造的分类 铸造种类很多, 按造型方法习惯上分为: (1) 普通砂型铸造, 包括湿砂型、 干砂型和化学硬化砂型 3 类。 (2) 特种铸造, 按造型材料又可分为以天然矿产砂石为主要造型材料的特种铸造(如熔模铸造、 泥型铸造、 铸造车间壳型铸造、 负压铸造、 实型铸造、 陶瓷型铸造等)和以金属为主要铸型材料的特种铸造(如金属型铸造、 压力铸造、 连续铸造、 低压铸造、离心铸造等) 两类。 1.2 离心铸造简介 1.2.1 离心铸造的发展概况2 1809 年, 英国人埃尔恰尔特申请了 有关卧式离心铸造和立式离心铸造的个专利。 1849 年, 英国人安德鲁逊克制作出台离心铸管机, 而后生产了长达 3.6m、 直径为 75mm 的离心铸铁管。 本 科 毕 业 设 计 第 2 页共 29 页 1857 年德国人汉内贝士麦提出用立式离心铸造生产轮圈。 1862 年英国人惠尔利和鲍韦尔制作出了铸造轮圈的立式离心铸造机。 1910 年德国人奥托勃里代发明用移动浇注槽生产金属型离心铸管的方法。 1914 年巴西人代拉夫得和阿伦斯研究水冷型离心铸管法成功。 1917 年美国人莫尔创造了砂型离心铸管法, 1920 年开始用于大量生产。 1950 年在瑞典开始用涂料金属型离心铸造法生产主要用于下水道的铁管。 50 年代美国离心铸管建立了树脂砂型离心铸管法。 30 年代以后离心铸造法逐步推广应用于生产汽缸套、 炮身、 鼓轮等铸件。 在 20 世纪 40 年代出现了用离心铸造法生产双金属复合冶金轧辊的工艺。 1.2.2 离心铸造的定义及原理[3] 离心铸造是将金属液浇入旋转的铸型里, 在离心力的作用下充型并凝固成铸件的一种铸造方法。 离心铸造用的机器称为离心铸造机。 根据力学中的惯性, 处于旋转状态下的金属液质点相应的产生了离心力, 所以金属液在离心力的作用下凝固成形是离心铸造的一大特点。 1.2.3 离心铸造的分类 按照铸型的旋转轴方向不同, 常见的离心铸造机分为卧式、 立式 2 种。 (1) 卧式离心铸造, 铸型的旋转轴线处于水平状态或与水平线)时离心铸造成为卧式离心铸造。 如图 1-1 为一种卧式离心铸造。 卧式离心铸造机主要用于浇注各种管状铸件, 如灰铸铁球墨铸铁的水管和煤气管等等, 管径小 75 毫米, 可达 3000 毫米。 此外可以浇注造纸机用大口径铜辊筒, 各种碳钢、 合金钢管以及要求内外层有不同成分的双层材质钢轧辊。 (2) 立式离心铸造, 铸型的旋转轴线处于垂直状态时的离心铸造。 如图 1-2 为一种立式离心铸造。 立式离心铸造机则主要用以生产各种环形铸件和较小的非圆形铸件。 图 1-1 卧式离心铸造 图 1-2 立式离心铸造 1.2.4 离心铸造的特点 离心铸造的特点是金属液在离心力的作用下充型和凝固, 金属补缩效果好, 铸件外层组织致密, 非金属夹杂物少, 机械性能好。 离心铸造不用造型、 制芯, 节省了相关材料及设投入。 铸造空心铸件不需浇冒口, 金属利用率可大大提高。 因此对某些特定形 本 科 毕 业 设 计 第 3 页共 29 页 状的铸件来说, 离心铸造是一种节省材料、 节省能耗、 高效益的工艺, 但须特别注意采取有效的安全措施。 离心铸造可以获得无缩孔、 气孔、 夹渣的铸件, 而且组织细密、 机械性能好。 当铸造圆形中空零件时, 可以省去型芯。 此外, 离心铸造不需要浇注系统, 减少了金属的消耗。 但离心铸造铸出的筒形零件内孔自由表面粗糙、 尺寸误差大、 质量差, 有较多气孔、夹渣, 因此需增加加工余量, 而且不适宜浇注容易产生比重偏析的合金及铝镁等合金。 1.2.5 离心铸造的应用 离心铸造主要用于大批生产铁管、 铜套、 发动机缸套、 双金属钢背铜套、 造纸机滚筒。 生产效益显著的有双金属铸铁轧辊, 加热炉底耐热钢辊道、 无缝钢管毛坯, 刹车鼓、活塞环毛坯、 铜合金涡轮毛坯等。 1.3 45 钢简介 45 号钢[4], 是 GB 中的叫法, 国内常叫 45 号钢, 也有叫做“油钢”。 45 号钢为优质碳素结构用钢, 硬度不高易切削加工, 模具中常用来做模板、 梢子、 导柱等, 但须热处理。 1.3.1 化学成分 C 含量是 0.42%~0.50%, Si 含量为 0.17%~0.37%, Mn 含量 0.50%~0.80%, Cr含量0.25%, Ni 含量0.30%, Cu 含量0.25%。 密度是 7.85g/cm3。 1.3.2 处理方法 ( 1) 热处理 推荐热处理温度: 正火 850℃, 淬火 840℃, 回火 600℃。(1) 45 号钢淬火后没有回火之前, 硬度大于 HRC55 (可达 HRC62)为合格。 实际应用的硬度为 HRC55(高频淬火 HRC58)。(2) 45 号钢不要采用渗碳淬火的热处理工艺。 调质处理后零件具有良好的综合机械性能, 广泛应用于各种重要的结构零件, 特别是那些在交变负荷下工作的连杆、 螺栓、离心铸造 齿轮及轴类等。 但表面硬度较低, 不耐磨。 可用调质+表面淬火来提高零件表面硬度。 (2) 渗碳处理 一般用于表面耐磨、 芯部耐冲击的重载零件, 其耐磨性比调质+表面淬火高。 其表面含碳量 0.8%~1.2%, 芯部一般在 0.1%~0.25%(特殊情况下采用 0.35%)。 经热处理后,表面可以获得很高的硬度(HRC58~62), 芯部硬度低, 耐冲击。 如果用 45 号钢渗碳, 淬火后芯部会出现硬脆的马氏体, 失去渗碳处理的优点。 现在采用渗碳工艺的材料, 含碳量都不高, 到 0.30%芯部强度已经可以达到很高, 应用上不多见。 0.35%从来没见过实例, 只在教科书里有介绍。 可以采用调质+高频表面淬火的工艺, 耐磨性较渗碳略差。 1.3.3 45 钢应用 45 钢是轴类零件的常用材料, 它价格便宜经过正火后, 可得到较好的切削性能, 而 本 科 毕 业 设 计 第 4 页共 29 页 且能获得较高的强度和韧性等综合机械性能。 45 钢广泛用于机械制造, 如管、 模板、 连杆、 螺栓、 齿轮及轴类等。 1.4 离心铸管机的设计原则 设计离心铸管机时需要确定几项参数: 浇注时管模的转速, 浇注速度, 浇注时间等,并遵循以下四个原则[5]。 (1) 离心铸管模的转速应保证液态金属进入管模后立刻成圆筒形, 并能得到良好的铸管内部组织, 根据不同规格的铸管确定不同的转速。 (2) 离心机的下行速度应均匀, 保证铸管壁厚均匀, 不同规格的铸管下行速度不同。 (3) 浇注不同规格的铸管时, 配用不同容量的扇形包。 一套扇形包的倾动机构在一种倾倒速度的条件下, 可以倾倒出不同重量的铁水量。 (4) 管模的冷却水量采用闭环控制, 根据水的出口和入口温度控制冷却水量。 1.5 本课题研究的对象 根据零件图(如图 1-3 所示) 设计小型滚筒式卧式离心铸造机, 零件材料为 45 号钢, 零件壁厚 10mm。 图 1-3 管类零件 D=150mmh=250mm 本 科 毕 业 设 计 第 5 页共 29 页 2 离心铸造工艺 2.1 生产条件的确定 离心铸造的设包括熔炼设、 传动设和模具。 2.1.1 熔炼炉的选择 熔炼炉的选择如表 2-1。 表 2-1 熔炼设一览[6] 序号 名称 功率(KW) 容量(T)形式 1 2 3 电弧炉 中频炉 焦炭坩埚炉 100 250 2.2 0.5 0.25 0.3 卧式 立式 立式 根据模具的尺寸选择 1 号电弧炉。 利用电弧热效应熔炼金属和其他物料的电炉叫电弧炉, 电弧炉用于熔炼普通钢、 优质碳素钢及各种合金钢、 不锈钢。 2.1.2 炉前准 凡是要加入到炉中去的各种原材料都要必须除锈、 去油、 彻底烘干。 投炉前应尽可能的把炉料预热到 ℃左右。 各种辅料包括覆盖剂、 清渣剂、 除气剂都必须在投炉前烘烤, 对一些氯化物, 还必须高温脱水处理后方能使用, 严禁冷料使用。 凡是与金属液直接接触的各类工具, 包括浇包、 浇口槽、 钟罩、 搅拦棒、 耙子等都必须刷好涂料彻底烘干后待用。 石墨坩埚应预热到 200-300℃时再放入炉膛, 防止坩埚爆炸和掉层。 检查钢液质量好坏、 能否离心铸造, 检查的方法是在耐火砖上凿一个直径 50×50mm的凹坑, 把熔炼好的金属液注入, 待凝固后看其表面。 表面凹陷为合格, 若是表面平整或者凸起, 证明铜液中含有气体或者气体含量严重, 此时必须进行第二次排气和精炼处理, 之后再检查一次, 要是第二次检查还不合格, 这炉钢液就不能进行离心铸造。 2.1.3 离心机的选择 如表 2-2 所示, 根据零件尺寸选择 1 号卧式三级离心机。 表 2-2 离心机选择表 序号 规格(mm)功率(KW) 车速 (转/分) 形式 1 2 3 4 300 600800 700200 1100600 4 10 20 40 1150 900 800 700 卧式三级 卧式二级 立式二级 立式二级 本 科 毕 业 设 计 第 6 页共 29 页 2.1.4 离心机转速的确定 离心机转速直接影响铸件质量, 转速过低使铸件内圆产生金属堆积, 合金液中的氧化夹杂物不易离出, 铸件产生类渣; 转速过高铸件容易产生偏析, 尤其是铸件壁厚较大,结晶温度范围较宽的合金和合金中成分比重相差较大的元素。 如锡、 铅等。 通常我们用 如下经验方法来确定。 铸件的直径小, 需要的离心力大, 速度靠上限取, 反之取较小的转速。 此处铸件的直径是指内孔而不是外圆, 见表 2-3 所示。 表 2-3 离心机转速表 形式 直径(mm) 转速(r/min) 卧式 50~100 100~200 200~ ~600 800~1300 950~1100 750~950 600~750 立式 600~800 800~1100 600~700 500~600 零件内径是 130mm, 选取转速 950~1100r/min。 2.2 金属模涂料 2.2.1 喷刷涂料的目的 保护金属型, 提高冒口补缩能力, 利于金属液流动改善充型条件, 一定的排气作用,使铸件表面光滑利于脱型, 涂料层可减少或避免铸铁件产生百口。 2.2.2 对涂料的要求 有足够的耐热性, 必要的化学稳定性, 有一定的导热性, 能牢固的附着在金属性表面而且自身有一定的强度。 2.2.3 涂料各成分的性能 涂料[7]是由耐火粉、 粘结剂、 稀释剂、 特殊附加剂等多种成分组成的混合液体。 (1) 耐火粉对废铁合金常用的有白垩粉、 滑石粉、 二氧化钛、 氧化镁、 石墨粉等;对铜合金铸件常用的有石墨粉、 石棉粉、 耐火粘土、 滑石粉等; 对黑色金属铸件常用的有硅石粉、 镁砂粉、 铬铁矿粉、 耐火砖粉、 耐火粘土、 石墨粉等。 (2) 粘结剂对非铁合金主要用玻璃水; 对铸钢件一般用粘土、 水泥、 糖浆、 油类等等。 (3) 稀释剂除铜合金外一般都用水稀释。 (4) 特殊附加剂为提高非铁合金铸件所用涂料塑性, 在其成分中加入 2%~3%的亚硫酸钡。 铸造镁合金时, 为防止金属氧化一般加硼酸。 本 科 毕 业 设 计 第 7 页共 29 页 2.2.4 涂料配比 涂料的成分由很多种, 铸件材料不同, 选择的涂料也不一样。 表 2-4 列举了铸钢件的涂料多种配比。 表 2-4 铸钢件金属型铸造用涂料配比(wt%) 编号 成分 配比 注 1 石灰粉 耐火粘土 肥皂液 糖浆 水 87 8 1~2 1~3 其余 用水调至密度为 1.4~1.5g/cm, 在预热金属型之前用毛笔刷涂 2 机油 100 金属型预热后用棉布擦涂(小钢件) 3 硅石粉 白泥 糖浆 重油 100 4 2 0.2~0.3 大型铸钢件用 (配比中后三项是另加的,湿碾>12h, 含水量 28%~33%) 4 沥青 汽油 一份(体积) 三份(体积) 5 脱水焦油 100 2.2.5 涂料配制工艺 (1) 原材料准, 涂料中的各种耐火粉在配制前都应进行干燥, 然后进行过筛。 (2) 涂料配制, 铸铁件、 铸钢件用涂料的配置方法, 先将耐火粉混匀, 然后兑入液体材料。 2.2.6 涂料喷涂工艺 喷刷涂料前应仔细清理金属型工作面及通气孔, 去除旧的涂料层、 及粘附的金属毛刺等。 新投入运用的金属型, 可用稀硫酸洗涤或轻度吹砂处理来改善型面对涂料的粘附力。 清理好的金属型一般都需要进行预热, 铸钢件预热温度在 100℃~250℃。 喷刷涂料时应注意金属型不同部位要求的涂料层厚度。 如非铁合金, 浇冒口部分:0.5mm~1mm, 铸件厚大部分: 0.05mm~0.2mm, 铸件薄壁部分: 0.2mm~0.5mm。 本 科 毕 业 设 计 第 8 页共 29 页 2.3 浇注温度 浇注温度是保证合格铸件的主要参数之一。 本次设计为管状零件, 金属液充型时遇到阻力较小, 又有离心压力或离心力加强金属液的充型性, 故离心铸造是的浇注温度可比重力浇注低 5~10℃℃。 浇注温度过高铸件外圆容易产生气孔, 浇口部位将产生缩孔。浇注温度过低铸件外圆产生冷隔、 皱皮, 铸件内部产生夹层、 壁厚不均、 内圆堆积金属等缺陷。 45 钢的熔化温度 1460℃~1467℃ , 出 钢温度 1560℃~1580℃ , 浇注温度1500℃~1550℃。 2.4 浇注速度 离心机因采用金属型模具, 冷却速度较快, 采用快速浇注能获得优质铸件。 由零件 参数得质量为4 . 4)(202rrkg。 根据表 2-5, 选取包孔直径 30mm, 浇注时间 0.5s。 表 2-5 钢液浇注重量速度平均值 包孔直径 浇注重量速度 注 30 35 40 45 50 10 20 27 42 55 包孔直径:mm, 浇注重量速度:kg/s 2.5 浇注系统 离心铸造浇注系统应满足下列要求:(1) 浇注长度长、 直径大的铸件时, 浇注系统应使金属液能较快的均匀的铺在铸型内表上。(2) 尽可能减少金属液飞溅。(3) 铸型内的浇道应能使金属液顺利流入型腔。(4) 浇注终了, 浇杯和浇注槽内应不留金属和熔渣,如果有熔渣也应该易于清理。 离心铸造的浇口没有手工铸造的要求严格, 但浇口位置不当也会使铸件产生缺陷,突出的缺陷有, 纵向壁厚不均, 浇口近的地方过厚, 远离浇口的地方很薄, 铸件两头产生氧化夹杂物, 特别是卧式离心机。 因此对直径小而长的铸件, 尽量将浇口伸进金属模1/3~1/2 处较为理想; 直径大而短的铸件, 浇口伸进金属模的深度约 1/3~1/2 处即可。 浇口的深度确定之后, 还必须调整浇口方向, 浇口方向不能朝上顺着离心机的旋转方向,也不能直顶着离心机的旋转方向。 合适的浇口方向始终与离心机的旋转方向形成一个15左右的夹角, 不得超过 30, 能有效地保证铸件质量。 本次设计选择伸进金属模1/3 处。 选择管式浇注杯。 本 科 毕 业 设 计 第 9 页共 29 页 2.6 铸型转动时间 当金属液注入金属模后, 要有足够的时间使液态金属转变为固态金属, 整个转变过程是在离心机旋转过程中进行的, 不可以停机。 若是过早停机, 铸件将会产生凸瘤和不圆现象。 简单的办法是观察铸件颜色, 呈暗红色时停机、 取件。 一般转动时间取 10s。 本 科 毕 业 设 计 第 10 页共 29 页 3 离心铸管缺陷分析及预防 3.1 合金钢管缺陷分析 离心铸造合金钢管常出现的缺陷[8]有: 充型不完整, 表面气孔, 钢管表层夹砂, 裂纹, 试压渗漏, 夹渣与渣痕, 表面局部针刺。 (1) 充型不完整。 在离心铸造钢管中充型不完整常有两种情况: 一种是外型缺浇,管子未达到足够的长度; 另一种是管子壁厚不均, 在管子浇注的彼端壁较薄。 此缺陷常发生于壁厚在 8mm 以下的薄壁钢管中, 特别是长径比大的管子(L/D>15, L 管长;D 管径)。 (2) 表面气孔。 在钢管表面局部存在气孔, 直径为 0.2mm~2 mm, 深 0.5mm~2mm,气孔分布的密度约为 2~12 个/ cm 。 呈现出很均匀的一片片的气孔。 (3) 钢管表层夹砂。 在钢管表面局部出现粗糙麻面并稍有凸起, 粗糙麻面有清晰的周边轮廓。 严重时成为环带状夹砂。 当去掉粗糙的钢表层后可见存在其中的薄涂料层即夹砂。 夹砂部位经过 1mm~2mm 的加工即可去除。 但它严重影响铸皮质量, 如是非加工的钢管就很可能报废。 这种缺陷多出现于挂涂料的钢管。 (4) 裂纹。 钢管裂纹有纵裂和横裂。 纵裂纹主要是由于合金在凝固时转速过高,往往伴随离心机振动较大时出现, 生产中纵裂纹出现不多。 实际中横裂纹较多见, 裂纹多靠管子一端, 裂纹有时穿透管壁, 严重者管子一出型就断开了。 (5) 试压渗漏。 钢管在试压时, 在表面出现大面积渗漏, 呈现一片片泅水现象,造成报废。 (6) 夹渣与渣痕。 夹渣, 有时管子表面并未见有夹渣, 经试压发现局部小面积渗漏, 经剖破检验发现在漏水处管壁中存在夹渣, 某生产镁罐筒曾出现过此现象。 渣痕, 有时在钢管的内表面存在小凹陷, 大小、 深浅不等。 在薄壁钢管中凹陷处使壁厚减薄较多。 由于钢管内表面存留较大块浮渣, 待其脱落后便显出凹陷, 所以是渣痕。渣物的密度比钢液小时在离心力作用下浮到内表面, 但由于渣物本身的重力使其沉入钢液一定深度, 从而形成渣痕。 (7) 表面局部针刺。 在靠近钢管的一端有时会出现针刺。 针刺的直径为 0.5mm~1 mm, 高为 2mm~3mm, 每平方厘米内 1 根左右。 这种现象常发生在涂料层较厚的情况下。 3.2 缺陷预防措施 (1) 充型不完整。 在离心浇注时影响充型的因素主要有: 浇注温度、 铸型转速、浇注速度和铸型温度等。 在铸型温度和浇注速度一定的情况下, 提高浇注温度, 可增加钢液的流动性; 增加铸型转速, 可提高离心压力使钢液较好地布满铸型。 本 科 毕 业 设 计 第 11 页共 29 页 (2) 表面气孔。 这种气孔是由于涂料产生的侵入性气孔。 钢液浇注后, 涂料层在高温作用下发生气化, 当气体形成较大压力时就会进人钢管表层, 这时合金已处于或接近半凝固状态, 很快凝固成型, 气体不能穿过合金层逸出, 就存留于钢管表层形成气孔。由于钢液温度高, 涂料激发出的气体较多, 涂料层容气量有限, 而且铸型无排气孔, 所以离心钢管易产生气孔。 克服气孔缺陷的基本途径是减少涂料的发气量。 有效的办法是将耐火骨料经高温焙烧使其脱掉结晶水, 试验表明当涂料发气量小于 5cmm/ g 时, 在正常离心铸造工艺条件下钢管不会出现气孔。 粘结剂和悬浮剂应尽量少加, 铸型上完涂料后要充分干燥, 使粘结剂达到一定程度的脱水, 以减少发气量。 (3) 铸管表层夹砂。 夹砂主要是由于涂料层组成不均, 存在分层现象, 当有裂纹或浇注时发生裂纹, 钢液钻入将表层涂料夹在中间所致。 分层现象的形成主要是由于挂涂料时, 涂料在型内混合时间不够, 未达到均匀而粘稠的程度, 便加速涂挂, 致使密度较小的粘结剂多浮向内表层, 而形成中间低强度层的分层现象。 为减少分层现象, 要注意涂料在型内的混合, 严格控制加速涂挂时间。 此外, 涂料在入型前应充分搅拌(特别是耐火骨料密度差较大) ; 涂料时要严格控制型温; 铸型较长时涂料导入要均匀。 在铸型干燥时应缓慢加热以防止涂料层裂纹。 (4) 裂纹。 这是一种热裂纹。 当钢管两端出现飞刺或喇叭头时, 合金凝固后收缩受到阻碍, 而且高合金钢收缩率又较大, 故造成裂纹。 从工艺上看主要在于涂料厚度的均匀性, 涂料在铸型纵向要分布均匀。 挂涂料时端盖处不得有涂料浆漏出, 避免产生飞刺。 挂涂料时用木端盖(挂完更换)可防漏料, 挂完涂料后再将端盖与铸型接触处进行密封。 喷涂料时涂料厚度要均匀, 端部不得有皮缝。 (5) 试压渗漏。 这种渗漏主要是由于管壁存在缩松所致。 产生缩松的原因在于离心浇注时管壁未形成从外向内顺序凝固。 这种缺陷多出于挂涂料法生产的薄壁钢管上。 如: 生产直径为 100mm, 壁厚 5~6mm 的耐热钢辐射管。铸型挂 3mm 厚的耐火涂料,铸出钢管表面质量良好, 经试压出现大面积渗漏, 检验钢管壁截面发现严重缩松。 原因是涂料太厚, 冷却强度不够, 钢液层未实现顺序凝固, 而是体凝固所致。 将涂料改为1.5mm 厚, 渗漏克服。 从这点看喷涂料比挂涂料好。 (6) 夹渣与渣痕。 存在夹渣主要是由于浇注温度低, 除渣不净, 或浇注转速不够,致使渣物未能及时浮动到内表面。 渣物密度愈大沉入钢液愈深, 体积愈大其渣痕也愈大。所以除净渣物和采用封闭式浇注系统很必要。 (7) 表面局部针刺。 据工艺分析, 是由于铸型预热温度不均匀所致。 例如, 靠近干燥炉里端铸型温度偏高, 挂涂料时该处涂料硬化快, 其内部迅速产生蒸气不能顺利排出, 而形成集中气流夺路外逸, 造成涂料层穿孔, 在此过程中涂料层不断硬化使孔洞保留下来, 浇注后钢管表面就形成针刺。 针刺需打磨清理增加劳务。 使铸型预热温度均匀,涂料时型温不得过高, 可消除表面针刺。 本 科 毕 业 设 计 第 12 页共 29 页 4 模具设计 4.1 模具的结构 模具必须以零件的大小作为标准, 零件图为图 1-3。 铸件外径小于 200mm, 模具组装图[9]如图 4-1 所示。 1.后盖 2.挡板 3.衬套 4.销子 图 4-1 模具组装图[14][15] 4.2 模具参数的计算 4.2.1 衬套设计 衬套的作用就是为了方便零件脱模, 在衬套表面, 涂由一层隔热物资, 作用是使零件不与衬套粘结在一起, 并且防止衬套受热变形。 零件材料是 45 钢, 模具工作温度800~1000℃, 模具材料为特种合金 K3、 K5、 K17 或者 K19。 由于零件在从液体凝固成液体过程中, 会发生收缩。 故在设计衬套的过程要充分考虑到零件的收缩率, 如表 4-1。 表 4-1 收缩率选择表 铸件外径(mm) 收缩量(mm) 注 100 150 200 >200 3 4 5 5 或实验后确定 本 科 毕 业 设 计 第 13 页共 29 页 D 为衬套外径 150+20+4=174mm 零件外径 150mm, 收缩量取 4mm d 为外径+收缩量=150+4=154mm d1=d+10mm=164mm d、=铸件内径-收缩率 铸件外径 R=150mm; 壁厚 10mm; 内径 R、=150-20=130mm; d、=130-4=126mm 壳体厚度=衬套厚度0.8=8mm 4.2.2 后盖的设计 后盖直径 d1、=d1=164mm 厚度 n=20mm。 如图 4-2 所示。 图 4-2 后盖 4.2.3 挡板的设计 挡板的作用就是防止衬套在高速转动过程中由于离心力的作用脱离模具。 如图 4-3所示。 图 4-3 挡板 挡板外径 D、=d1=164mm 本 科 毕 业 设 计 第 14 页共 29 页 、=126mm 挡板内径 db=20mm 4.3 铸型转速的计算 实际生产中, 常用一些经验公式计算铸型的转速, 并根据实践情况进行适当修正,一般铸型转速在15%的偏差时, 不会对浇注过程和铸件质量产生显著的影响。 (1) 康斯坦丁诺夫公式计算铸型转速(我国广泛采用) 如式 4-1。 055200rn (r/min) (4-1) 式中 n铸型转速(r/min); g 铸件合金重度(N/m3); r0 铸件内半径(m); b康斯坦丁诺夫公式修正系数, b =0.8~1.5, 具体取值可以参考表 4-2 选取。 表 4-2 康斯坦丁诺夫公式修正系数值 离心铸造类型 铜合金卧式离心 铜合金立式离心 铸铁 铸钢 铝合金 1.2~1.4 1.0~1.5 1.2~1.5 1.0~1.3 0.9~1.1 此式只试用于铸件外半径对铸件内半径的比值15. 10rR时的离心铸造。 (2) 凯门公式计算铸型转速(西方国家广泛采用) 如式 4-2。 0 rcn (r/min) (4-2) 式中 c系数, 具体参考值见表 4-3; r0 铸件内半径(mm)。 表 4-3 各种铸件离心铸造时 c 值 本 科 毕 业 设 计 第 15 页共 29 页 铸件合金 合金密度(g/cm) 产品名称 离心铸造方式 c 铸铁 7.2 钢管、 涨圈 卧式 9000~12500 缸套 卧式 10750~13650 铸钢 7.85 卧式 10000~11000 黄铜 8.20 圆环 卧式 13500 铅青铜 8.8 90~200 轴承 卧式 9500 9.5~10.5 卧式 8500~9500 巴氏合金 7.3~7.5 轴瓦 卧式 7000~9000 铝合金 2.65~3.10 卧式 13000~17500 青铜 8.4 立式 17000 此式也只适用于铸件外半径对铸件内半径的比值15. 10rR时的离心铸造。 (3) 重力系数公式(西方国家广泛采用) 如式 4-3。 09 .29rGn (r/min) (4-3) 式中 G重力系数, 具体数值参考表 4-4; r0铸件内半径(m)。 表 4-4 不同合金离心铸造时的 G 值[7] 合金 G 铜合金 铸铁 铸钢 铝合金 40~110 45~110 40~75 90~155 (4) 砂型离心铸造公式, 如式 4-4。 为降低铸件外表面粗糙度, 防止砂型被合金液压坏, 有时需要控制金属液作用在砂型表面上的离心压力值, 故提出了根据砂型可能承受的离心压力值计算铸型转速的 本 科 毕 业 设 计 第 16 页共 29 页 的公式 )(3 .42202rRrPn (r/min) (4-4) 式中 P砂型能承受的离心压力(MPa), 对于砂型, P0.003~0.004MPa; 对于砂芯组合的离心砂型, P0.004~0.006MPa; 对于陶瓷型, P0.006~0.008MPa; g 液态金属重度(N/m); R、 r0 铸件的外半径和内半径(mm)。 在本次设计中 R=150mm,、R=130mm,154. 1130150、RR15. 1, 由上述 4 个公式得知, 选取第 3 个, 重力系数公式。 零件为铸钢件由表 4.4 得 G 值取 65, 内半径r0=65mm=0.065m,min/950065. 0659 .299 .290rrGn。 本 科 毕 业 设 计 第 17 页共 29 页 5 零件的选择 5.1 联轴器的选择 联轴器[10]是用来联接不同机构中的两根轴(主动轴和从动轴) 使之共同旋转以传递扭矩的机械零件。 在高速重载的动力传动中, 有些联轴器还有缓冲、 减振和提高轴系动态性能的作用。 联轴器由两半部分组成, 分别与主动轴和从动轴联接。 一般动力机大都借助于联轴器与工作机相联接。 对于已标准化和系列化的联轴器, 选择合适类型后, 可按转矩、 轴直径和转速等确定联轴器的型号和结构尺寸。 5.1.1 确定联轴器的计算转矩 运转过程中, 可能出现动载荷及过载荷等现象, 所以, 应取轴上的的转速作为计算转矩。 如转矩不能求得时, 可按式 5-1 计算。 Tca=KaT nPT9550 (5-1) 式中 T-联轴器所需传递的名义转矩, N.m Tca-联轴器所需传递的计算转矩, N.m Ka-工作情况系数, 小型机械故选=1.3 5.1.2 确定联轴器的型号及尺寸 根据计算转矩、 轴直径和转速等, 由下面的条件, 从有关手册中选取联轴器的型号和结构尺寸。 Tca[T] nnmax 式中 [T]-所选联轴器型号的许用转矩, N.m; n-为联轴器的转速, r/min; nmax-所选联轴器允许的转速, r/min。 多数情况下, 每一型号联轴器适用的轴的直径均由 一个范围。 标准中已给出轴直径的与小值, 或者给出适用转矩范围。 名义转矩 T=9550nP=40.64N.m 计算转矩 Tca=KAT=1.3×40.64=54.46N.m 选用固定式凸缘式联轴器,442862251JYG 如图 5-1, 5-2 所示。 许用扭矩 112N.m 许用转速 9500 r/min 凸缘式联轴器特点特点: 构造简单, 成本低, 可传递较大转矩。 不允许两轴有相对位移, 无缓冲。 凸缘联轴器的材料可用灰铸铁或碳钢, 重载时或圆周速度大于 30 米/秒 本 科 毕 业 设 计 第 18 页共 29 页 时应用铸钢或锻钢。 在本次设计中联轴器材料选取碳钢 Q235。 图 5-1 联轴器正视图[14][15] 图 5-2 联轴器左视图 本 科 毕 业 设 计 第 19 页共 29 页 5.2 离合器的选择 离合器[11]在机器运转中可将传动系统随时分离或结合。 对离合器的要求有: 接合平稳, 分离迅速而彻底, 调节和处理方便, 外廓尺寸大小, 质量小, 耐磨性好和有足够的散热能力, 操作方便省力。 按操作的方式, 离合器可分为外力操纵式离合器和自动离合器。 外力操纵式离合器和自动离合器。 外力操纵式离合器有机械操纵式、 电磁操纵式、 液压操纵式和气动操纵式等; 自动离合器能够自动进行接合或分离, 不需忍来操纵。 例如, 离心离合器, 当转速达到一定值时, 两轴能自动接合或分离; 安全离合器, 当转矩超过允许值时, 两轴即自动分离; 定向离合器, 只允许单项传动, 反转时即自动分离等等。 大多数离合器已标准化或规格化, 设计时, 只需参考有关手册对其进行类比设计或选择即可。 选择离合器时, 首先根据机器的工作特点和使用条件, 结合各种离合器的性能特点,确定离合器的类型; 类型确定后 , 可根据被联接的 两轴的直径、 计算转矩和转速, 从有关手册中查出适当的型号; 必要时, 可对其薄弱环节进行承载能力校核。 牙嵌离合器的常用材料为低碳合金钢(如 20Cr、 20MnB), 经渗碳淬火处理后使牙面硬度达到 HRC56-62。 有时也采用中低合金钢(40Cr、 45Mn), 经表面淬火等处理后硬度达到 HRC48-52。 本次设计离合器的材料选用 20Cr。 本装置采用的是螺纹连接, 因此不允许模具反转, 所以选择定向离合器。 轴的转速是 n=950r/min 离合器的名义转速计算公式, T=9550P/n 式中 p-电动机功率, kW; n-计算转速, r/min; -由电动机至离合器的轴的传动效率, 取 0.97; 综上所述得, 名义转矩 T=40.640.97=39.42 N.m, 计算转矩 Tca=39.421.3=51.25N.m。 根据计算转矩、 轴径和转速, 从设计手册中选取离合器的具体型号, 其参数为: 额定转矩 175N.m; 轴径 28mm; 牙数 3; 牙宽度 10mm; 牙高度 10mm; 牙在中径处高度4mm; 半离合器长度 38mm、 50mm; 操作环槽宽度 20mm; 操作环外径 44mm; 离合器外径 55mm。 如图 5-3, 5-4 所示。 本 科 毕 业 设 计 第 20 页共 29 页 图 5-3 离合器正视图[14][15] 图 5-4 离合器左视图 5.3 轴承的选择 滚动轴承是将运转的轴与轴座之间的滑动摩擦变为滚动摩擦, 从而减少摩擦损失的一种精密的机械元件。 滚动轴承一般由内圈、 外圈、 滚动体和保持架四部分组成, 内圈的作用是与轴相配合并与轴一起旋转; 外圈作用是与轴承座相配合, 起支撑作用; 滚动体是借助于保持架均匀的将滚动体分布在内圈和外圈之间, 其形状大小和数量直接影响着滚动轴承的使用性能和寿命; 保持架能使滚动体均匀分布, 防止滚动体脱落, 引导滚动体旋转起润滑作用。 滚动轴承的作用, 支承转动的轴及轴上零件, 并保持轴的正常工作位置和旋转精度。 本 科 毕 业 设 计 第 21 页共 29 页 滚动轴承使用维护方便, 工作可靠, 起动性能好, 在中等速度下承载能力较高。 与滑动轴承比较, 滚动轴承的径向尺寸较大, 减振能力较差, 高速时寿命低, 声响较大。 深沟球轴承[13]是滚动轴承中为普通的一种类型。 基本型的深沟球轴承由一个外圈, 一个内圈、 一组钢球和一组保持架构成。 深沟球轴承类型有单列和双列两种, 单列深沟球轴承类型代号为 6, 双列深沟球轴承代号为 4。 其结构简单,离心铸造 使用方便, 是生产普遍, 应用广泛的一类轴承。 深沟球轴承的工作原理, 深沟球轴承主要承受径向载荷, 也可同时承受径向载荷和轴向载荷。 当其仅承受径向载荷时, 接触角为零。 当深沟球轴承具有较大的径向游隙时,具有角接触轴承的性能, 可承受较大的轴向载荷 , 深沟球轴承的摩擦系数很小, 极限转速也很高。 本次设计选择单列深沟球轴承, 代号是 61807, 规格为74235。 本 科 毕 业 设 计 第 22 页共 29 页 6 轴的设计 轴的结构设计是要确定轴的合理外形, 包括各段轴长、 直径及其他细节尺寸在内的全部结构尺寸, 轴的结构受多方面因素的影响, 没有一个确定形式, 而是随着工作条件与要求的不同而不同。 设计时应考虑三点。 1) 满足使用要求。 轴上零件在轴上有可靠的轴向固定和周向固定。 轴向固定, 应用广泛的有轴肩、 轴环、 套筒、 轴端挡圈及圆螺母。 周向固定, 轴上零件周向固定的常用方法有: 键、 花键联接、 紧定螺钉联接、 销联接、 过盈联接等。 2) 轴的结构工艺性。 进行轴的设计时, 应尽可能使轴的形状简单, 并且具有良好的可加工性和装配工艺性能。 3) 提高轴的疲劳强度。 轴一般在变应力下工作, 多数因疲劳而失效。 因此应设法提高轴的疲劳强度。 常采取的措施有: 改进轴的结构外形, 改善轴的表面状态。 6.1 轴长的确定 轴的材料主要是碳钢和合金钢。 钢轴的毛坯多数用轧制圆钢和锻件, 由的则直接用圆钢。 由于碳钢比合金钢价廉, 对应力集中的敏感性较低,离心铸造 同时也可以用热处理的方法提高其耐磨性和抗疲劳强度, 故采用碳钢制造轴尤为广泛, 其中常见的是 45 钢。 本次选择轴的材料也是 45 钢。 轴的结构设计包括定出轴的合理外形和全部结构尺寸。 拟定轴上零件的装案是进行轴的结构设计前提, 它决定这轴的基本形式。 所谓装案, 就是预定出轴上主要零件的装向、 顺序和祥和关系。 本此离心机设计的装案是: 半联轴器、 轴承、 半离合器依次从轴的右端向左安装。 零件在轴上的定位和装案确定后, 轴的形状便大体确定。 各轴段说需的直径在轴上的载荷大小有关。 先确定轴的小直径[10], 如式 6-1。 3minnPCd (6-1) 08.minnPCdmm, 此轴段有键槽增大 3%,mind=18.62mm 式中 P 是离心机功率, 为 4KW; n 是铸型转速, 为 950r/min; C 是计算常数, 见表 6-1, 取 112。 本 科 毕 业 设 计 第 23 页共 29 页 表 6-1 轴常用材料的 C 值 轴的材料 Q235、 20 35 45 40Cr、 35SiMn C 160 148 135 125 118 112 107 102 98 输出轴的小直径显然是安装联轴器处轴的直径。 为了使所选的轴直径与联轴器的孔径相适应, 选择输出轴的直径为 25mm, 半联轴器与从动轴直径 28mm, 此处设置一轴肩用来固定半联轴器和便于轴承拆卸此段轴承, 轴肩不能过高, 取 2.5mm, 此段轴长15mm。 轴承处直径 35mm, 根据轴承端盖的装拆及便于对轴承添加润滑脂的要求, 取端盖的外端面与半离合器左端面间的距离为 30mm, 轴承盖的宽度为 20mm, 所以此段轴长为 50mm, 离合器处直径为 28mm, 轴尺寸如图 6-1 所示。 图 6-1 轴尺寸图[14][15] 6.2 轴的校核 对于一般用途的轴, 按当量弯矩计算轴的强度或直径已足够。 但由于上述计算中没有考虑应力集中、 轴径尺寸和表面品质等因素对轴的疲劳强度的影响, 因此对于重要的轴, 还需要进行轴危险截面处的疲劳安全系数的计算, 评定轴的安全裕度。 本次设计轴的材料为 45 钢。 即建立轴的危险截面的安全系数的约束条件。 安全系数的约束条件[12], 如式 6-2。 sssssSca22 (6-2) maks1 maks1 对一般转轴, 弯曲应力按对称循环变化, 故0,/mmWM当轴不转动或载荷随轴一起转动时, 考虑到载荷波动的实际情况, 弯曲应力可作为脉动循环变化考虑, 即 本 科 毕 业 设 计 第 24 页共 29 页 )2/( WMma。 但多数情况下, 转矩变化的规律往往难于确定。 一般而言, 对单方向转动...
以上信息由江苏亚立特钢有限公司整理编辑,了解更多离心铸造信息请访问http://www.jsyltg.com