新闻中心
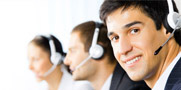
咨询热线:
134-0554-5577
邮件:874556408@qq.com
电话:0523-83984388
地址:江苏省兴化市沈伦镇工业园区沈北路
离心铸造熔炼温度过高 模温过高
压力铸造培训资料_机械/仪表_工程科技_专业资料。压力铸造基本概念 模具基本结构及常用材质 铝压铸件常见缺陷及处理 学习的痛苦是暂时的 学不到的痛苦是终生的 章 压力铸造基本概念 ? ? ? ? ? ? ? ? ? ? ? ? ? ?
压力铸造基本概念 模具基本结构及常用材质 铝压铸件常见缺陷及处理 学习的痛苦是暂时的 学不到的痛苦是终生的 章 压力铸造基本概念 ? ? ? ? ? ? ? ? ? ? ? ? ? ? ? ? 一、压力铸造基本原理及其工艺特点 压力铸造(简称压铸)是在高压作用下,将液态或者半液态金属以很高的速度充填到金属铸型(压 铸模)型腔,并在压力作用下快速凝固而获得铸件的一种工艺方法。 压铸时常用的压力是几十兆帕到几百兆帕(即几百到几千个大气压)充型速度在30~100m/s范围 内,表1是压铸与其它几种铸造方法的工艺参数比较。由此看出,高压、高速是压铸工艺过程的两 大特点,也是压铸工艺区别于其它铸造工艺方法的主要标志。使得压铸件结构、质量和性能、压铸 合金、压铸型的结构和材料、压铸设以及压铸工艺都有自己的特征。 二、与其它铸造工艺方法相比,压力铸造有以下优点 1、铸件壁薄、形状复杂、轮廓清晰。 2、压铸件尺寸精度高、表面粗糙度值低。 3、压铸件表面组织致密,具有较高的强度和硬度。 4、材料利用率高。 5、压铸件上可以直接嵌铸其他材料的零件,以节省贵重材料,简化制造工艺,减少加工工时。 6、压铸生产效率高,易于实现机械化和自动化。 压力铸造主要缺点如下: 1、压铸件中常有气孔及氧化夹杂物存在。 2、压铸工艺不适合小批量的铸件生产。 3、压铸件尺寸受到限制。 4、压铸合金的种类受到限制。 三、压力铸造的工艺过程 合金材料、压铸机及压铸模是压铸生产工艺过程的三个基本要素。以普通压铸为例,压铸生产工艺过 程如图所示 铸件图 合金材料 科勒材 料为 ADC12 压铸模设计 合金熔化 压铸模制造 合金液保温 科勒缸套按 要求预热 压铸模 压铸(按不同产品选用压铸机) 铸件清理及后处理 铸件按科勒 要求时效 铸件检验 四、压力铸造的分类 ? 1、按压铸机的种类的不同可分为热压室压铸和冷压室压 ? 热压室压铸的压室是浸泡在保温坩埚的液体金属中的,压射部件装在坩埚上面。 ? 冷压室压铸的压室与保温炉是分开的。压铸时,从保温炉中舀取液体金属浇入压室后进行压 铸。冷压室压铸按压力传递方向的不同又分为立式和卧式两种。 ? 2、按压铸合金种类的不同可分为有色金属压铸和黑色金属压铸。 ? 3、按压铸金属的形态的不同可分为半固态金属压铸和全液态金属压铸。 ? 4、按压铸方法的不同可分为普通压铸和特种压铸。特种压铸如真空压铸、充氧压铸等。 ? 五、压力铸造的应用范围和发展前景 ? 压力铸造是近代金属加工工艺发展很快的一种高效率、少切削的金属成形的铸造方法, 由于压铸有上述的优点,因而已广泛地应用到国民经济的各个行业之中。除了用于汽车和摩托车、 仪表、电器工业外,还广泛应用于家电、农机、通信、运输、造船、相机、计算机、纺织等行业中 。其中汽车和摩托车制造业是主要的领域,2004年,汽车、摩托车压铸件占全国压铸件总产量 的80%左右。 ? 当前用压力铸造法可以生产铝合金、锌合金、镁合金和铜合金压铸件,其中以铝合金压铸 件为多,2005年产量达到630866吨,占全国压铸件总产量的73%。黑色金属压铸由于目前缺乏 理想的耐高温模具材料,故尚处于试验研究阶段。 ? 近年来,随着汽车、摩托车以及电子通讯工业的发展和产品轻量化的要求,加之镁合金 压铸技术的日趋完善,从而使镁合金压铸的应用日渐广泛,镁合金压铸将成为二十一世纪的朝阳产 业。 ? 当前,国内外压铸技术发展的趋势为压铸机向系列化、大型化及自动化发展;计算机在 压铸生产中的应用日渐增多;压铸工艺不断改进,各种先进的压铸技术如真空压铸、充氧压铸、半 固态压铸等发展迅速;各种提高压铸模使用寿命的措施也在不断的应用于压铸生产之中 ? 二 模具基本结构及常用材质 ? ? ? ? ? ? ? ? ? ? ? ? ? ? ? ? ? ? 一、压铸模的基本结构 压铸模是一种复杂的模具,由定模和动模两大部分组成,其基本结构如下。 1、成型零件 它是决定压铸件几何形状和尺寸精度的零件。包括动定模上的固定的和活动的镶块以及型芯。它是压 铸模上构成铸件型腔的部分,也是压铸模的重要的部分。 2、浇注系统 它是引导金属液进入型腔的通道,沟通压铸机的压室与模具型腔的部分。一般由直浇道、横浇道和内 浇口所组成。 3、排溢系统 它是溢流系统和排气系统的总称,是贮存冷金属和涂料残渣的处所,又是排除压室、浇道和型腔中气 体的通道。该系统包括溢流槽和排气槽。 4、抽芯机构 铸件在取出时如果受到型芯或者型腔的阻碍,必须把这些型芯或型腔做成活动的,并在铸件取出之前 将这些活动的型芯或者型腔抽出之后,才能顺利地取出铸件。带动这些活动的型芯或者型腔抽动的机 构称为抽芯机构。 5、顶出机构(推出机构) 顶出机构是将铸件从模具中顶出的机构。它是由顶出元件(顶杆、顶板、顶管)、复位杆、顶杆固定 板、导向零件等组成。在开合模过程中完成铸件顶出和模具的复位工作。 6、导向零件 它是引导定模和动模在开合模过程中可靠地按照一定方向进行运动并准确地导向的部分,一般由导柱 、导套组成。 7、加热与冷却系统 为了平衡模具的温度,使压铸模保持在一定温度范围内工作,压铸模上常开设有加热与冷却系统。 8、模架 它是将压铸模各部分按一定的规律和位置加以组合和固定,组成完整的压铸模,并使压铸模能够安装 到压铸机上工作的构架。一般包括动定模座板、动定模套板、垫块、支承板等零件。 ? ? ? ? ? ? ? ? ? ? ? ? ? ? ? ? ? ? ? ? ? ? ? ? ? 二、压铸模的种类 1、按型腔数分 (1)单腔压铸模 (2)多腔压铸模(又分为同形多腔和异形多腔) 2、按压铸模成型零件的结构分 (1)整体式压铸模------成型部分直接在一个模块上加工而成。 整体式压铸模有以下特点: a.强度高、刚性好,可以减少模具的装配工作量。 b.易于开设冷却水道c.模具不易变形,铸件上没有镶拼痕迹 整体式压铸模的缺点是加工困难,贵重金属材料浪费大,模具成本高。 (2)镶拼式压铸模------成型部分的型腔和型芯由镶块组成,然后装入模具的套板内加以固定而成。这种结构形式 在压铸模中得到了广泛地应用。 镶拼式压铸模的优点在于: a.对于复杂的型腔可以分块进行加工,简化了模具制造工艺,提高了模具的制造质量。 b.合理地使用价格昂贵的耐热合金钢材,降低模具成本。 c.有利于易损件的更换和修理,改变模具型腔的局部结构方便。 d.镶拼处的间隙有利于型腔的排气。 镶拼式压铸模的缺点如下: a.镶块过多会增加装配困难,难以满足较高的组合尺寸精度。 b.镶块拼合处的缝隙易给铸件带来飞边,既影响模具寿命,又会增加铸件去毛刺的工作量。 c.模具散热条件差。 三、对压铸模的基本要求 1、压铸模所生产的铸件,应能保证铸件图规定的形状、尺寸以及各项技术要求。 2、模具应适应压铸生产工艺要求,如承受高温、高压以及合金液的冲刷等。 3、在保证铸件质量和安全生产的前提下,模具结构应简单,程序少,动作准确可靠,具有足够的硬度,便于拆卸 和维修。 4、模具能快速准确地安装到压铸机上。 5、尽可能地实现标准化,通用化,以缩短设计和制造周期,便于管理 ? ? ? ? ? ? ? ? ? ? ? ? ? ? ? ? ? ? ? 四、压铸的浇注系统 浇注系统设置的好坏直接影响到金属液在型腔中的充填状态,压铸件的成形以及铸件的表面和内在质量。浇注系统 对金属液的流动方向、压力的传递、排气条件、金属液的充填速度、模具温度分布以及充型时间等各个方面都取着 重要的控制和调节作用,因此,浇注系统的正确设计是保证铸件质量的重要因素。 1、浇注系统的分类 按照金属液进入型腔的部位和内浇口的形状,浇注系统一般可以分为侧浇口、中心浇口、顶浇口、环形浇口、缝隙 浇口和点浇口等类型,其中侧浇口是常用的浇口形式,比如摩托车的曲轴箱铸件就是采用侧分支浇口。 2、浇注系统的组成 如前所述,浇注系统一般由直浇道、横浇道和内浇口所组成。但是,根据所选用的压铸机的类型的不同,引入金属 液的方法也就不同,从而浇注系统的结构也就不相同。 立式冷室压铸机浇注系统由直浇道、横浇道、内浇口和余料组成, 而卧式冷室压铸机的浇注系统则由直浇道、横浇 道、内浇口组成,余料和直浇道则合为一体。 (1)直浇道 它是金属液进入压铸模型腔的首要通道。对于卧式冷室压铸机来说,直浇道的大小是由选用的压室直径的大小来决 定的,它是长度(即料饼厚度)约15—25mm范围内。 (2)横浇道 它是连接直浇道和内浇口之间的通道。它的作用是使直浇道来的金属液保持高温,并且平稳地过渡到内浇口。 对于卧式压铸机来说,横浇道应处于直道的上方,防止金属液在压射前过早地流入型腔。其断面形状以偏梯形为主 ,并向内浇口方向逐渐减小。 (3)内浇口:是将金属液引入型腔的后通道。它的作用是调整来自横浇道金属液的速度,使金属液按照要求的 流向充填型腔。 在浇注系统的设计中,内浇口的确定为重要。主要是确定内浇口的位置、形状和尺寸。内浇口的确定原则如下: a.有利于压力的传递,内浇口一般应设置在压铸件厚壁处。 b.有利于型腔的排气。 c.金属液进入型腔时不宜正面冲击型芯,减少能量损失,防止型芯冲蚀。 d.金属液进入型腔的流程应尽可能的缩短,减少热量损失,并且有利于模具的热平衡。 e.内浇口应便于切除和清理。 ? ? ? ? ? ? ? ? ? ? ? ? ? ? ? ? ? ? ? ? ? ? 五、排溢系统 为了提高铸件的外观质量,减少或消除铸件内部的气孔或夹渣,在压铸模上必须开设排溢系统。排溢系统包括溢流 槽和排气道。 1、溢流槽的主要作用 (1)贮存混有气体的脏、冷金属液。 (2)排出脱模剂挥发出气体、压室和型腔中空气。 (3)控制金属液的流动状态,防止局部产生涡流。 (4)提高模具的局部温度,有利于模具的热平衡。 (5)可在该部位设置顶杆,避免铸件表面留有顶杆痕迹。 溢流槽应设置在金属液后流入的地方以及内浇口的两侧,溢流槽的断面形状一般为半圆形或梯形。 2、排气道(排气槽) 排气道的主要作用是排出压铸模型腔中的气体,根据流入型腔中金属液的充填方向,排气道应设置在不易堵塞或金 属后充填的部位。排气道一般与溢流槽联合布置在溢流槽的后端,以加强溢流和排气的效果。排气道也可以在型 腔其它部位单独开设。近年来,压铸界开始流行“大量排气法”,应用皱折式排气道,尽可能多的将压铸模型腔中 的气体排出去。 压铸模的排气方法除了开设排气道以外,尚有其它多种方法,如采用排气塞排气、型芯间隙排气、顶杆间隙排气等 六、压铸模材料的选择 1、对压铸模材料的要求 (1)具有很高的高温强度、高温硬度、抗回火稳定和冲击韧性。 (2)小的热膨胀系数。 (3)良好的导热性的抗疲劳性。 (4)具有足够的高温抗氧化性。 (5)有很高的耐磨性。 (6)有良好的渗透性和较小的热处理变形。 2、常用的压铸模材料 压铸模的成型零件及浇注系统零件推荐的材料和热处理硬度见表4, ? ? ? ? ? ? ? ? ? ? ? 压铸锌、铝、镁合金的成型零件经淬火工艺热处理后,成型表面如果需要进行渗碳处理,渗碳层深度应为 0.08~0.15mm,硬度≥600HV。 模架零件如动定模座板、套板、垫块等常采用45钢制造,也有家采用球墨铸铁材质用铸造方法来生产。模具上的 导向零件如导柱、导套可以采用工具钢T8、T10来制造。 七、压铸模的维护和保养 1 、型腔和分型面应随时清扫 压铸模在生产过程中,型腔和分型面上不可避免的会受到脱模剂或者润滑剂的污染或堆积,压铸件的飞边毛刺也可 能粘到型腔或分型面上。因此,在每次的压铸循环中,操作者应注意保持型腔和分型面的清洁,并应随时清扫。 2 、模具要定期检查 一定批量的铸件生产完成后,模具维护人员应根据后一次压铸出的铸件质量情况进行模具检查,修正尺寸,抛光 拉伤部位的型腔,对活动部位(顶杆、活动型芯、导柱等)进行清理、检查和修正,对损坏的型腔部位要进行修补 或更换。 3 、模具要定期进行热处理 压铸模长期在高温下工作,会产生热应力,甚至提前出现裂纹,从而降低模具的使用寿命。因此,压铸模在生产一 定批量的铸件以后,应当进行去应力热处理。去应力热处理的次数和间隔时间视模具的大小和复杂程度而定。 4 、模具应妥善保管 模具应有专用的保管场地,并按一定的次序分类堆放。模具上应有明显的标记,以便于辩认。暂时不用或需长期堆 放的模具,在模具表面应涂防锈剂来保护模具。 硬度/HRC 模具零件名称 模具材料 用于压铸锌合金、铝合金镁合金 8407(瑞典) 动模镶块、定模镶块、分流锥、 顶杆、浇口套 4Gr5MoSiV1(H13) 现用DIVER代替 44~48 3Gr2W8V 44~48 导套 滑块 定模 楔紧块 动模 支脚 (垫块) 动模框 抽芯器座 科勒SH265箱 体模具结构 导滑块 科勒产品对应模具 均采用瑞典一胜佰 DIVER 溢流槽 预铸孔 集渣包 内浇口 铸件(毛 坯) 科勒SH265 箱体浇铸 支浇道 缸套(或嵌 件) 余料饼 (口) 主浇道 压铸流程Die Casting Process 模具维护保养 Die maintenance ? ? 原材料进 in coming raw material 检验与存放inspection & storage 铝材熔炼 Melting 压铸 Die casting 去除毛刺, 表面光洁 deburr ed; smooth surface 抛丸 short blast 去应力 Destressing 时效处 理 ageing 毛刺清理 deburr 清理 cleaning 外观、内部、尺 寸检查,切边 outer & inner spec inspection, trim 3价铬钝化 Trivalent chromium passivation 铸件防腐 anti rust treatment 入库 warehousing 铸件储存 casting storage 铝合金压铸件常见缺陷 □外观缺陷 拉伤 气泡 裂纹 变形、磕碰 流纹、花纹 冷隔 变色、斑点 网状毛刺 凹陷 欠铸 飞边、毛刺 多肉 粘铝 □内部缺陷 气孔 缩孔、缩松 夹杂 脆性 渗漏 硬质点 分层 铝合金压铸件常见外观缺陷 外观: 拉伤 特征:沿开模方向铸件表面呈现条状的拉伤痕迹,有一定深度,严重 时为一面状伤痕;另一种是金属液与模具产生焊合、粘附而拉伤, 以致铸件表面多肉或缺肉。 铝合金压铸件常见外观缺陷 外观: 拉伤原因 特征 产生原因 1 2 3 4 沿开模方向铸件表 面呈现条状的拉伤痕 迹,有一定深度,严 重时为一面状伤痕; 另一种是金属液与模 具产生焊合、粘附而 拉伤,以致铸件表面 多肉或缺肉。 5 型腔表面有损伤 出模方向斜度太小或倒斜 顶出时偏斜 浇注温度过高或过低、模温过 高导致合金液产生粘附 脱模剂使用效果不好 防止措施 1 2 3 4 5 修理模具表面损伤处,提高光洁度 修正斜度 调整顶杆,使顶出力平衡 控制合适的浇注温度,控制模温 更换脱模剂 6 7 铝合金成分铁含量低于 .冷却时间过长或过短 6 7 调整合金含铁量 修改内浇口,避免直冲型芯型壁或 对型芯表面进行特殊处理 铝合金压铸件常见外观缺陷 外观: 气泡 特征:铸件表面有米粒大小的隆起表皮下形成的空洞。 铝合金压铸件常见外观缺陷 外观: 气泡原因 特征 产生原因 1 2 3 4 5 6 铸件表面有米粒大 小的隆起表皮下形成 的空洞。 7 合金液在压室充满度过低,易 产生卷气 压射速度过高 熔液未除气,熔炼温度过高 模温过高,金属凝固时间不 够,强度不够,而过早开模顶 出铸件,受压气体膨胀起来 模具排气不良 内浇口开设不良,充填方向不 顺 脱模剂太多 防止措施 1 2 3 4 5 6 7 提高金属液充满度 降低阶段压射速度,改变低速 与高速压射切换点 调整熔炼工艺,进行除气处理 降低模温,留模时间延长 增设排气槽、溢流槽、充分排气 调整模具浇注方案 减少脱模剂用量 铝合金压铸件常见外观缺陷 外观:裂纹 特征:铸件表面有呈直线状或波浪形的纹路,狭小而长,在外力作用 下有发展趋势。 铝合金压铸件常见外观缺陷 外观: 裂纹 铝合金压铸件常见外观缺陷 外观: 裂纹原因 特征 产生原因 1 2 3 4 合金中铁含量过高或硅含量过 低 合金中有害杂质的含量过高, 降低了合金的可塑性 铝硅铜合金含锌或含铜量过高 .模具,特别是型芯温度太低 铸件壁存有剧烈变化之处,收 缩受阻,尖角位形成应力 留模时间过长,应力大 防止措施 1 2 3 4 5 6 正确控制合金成分,防止增铁和混 料 正确控制合金成分,防止增铁和混 料 正确控制合金成分,防止混料 提高模温,模温要稳定 改变铸件结构,加大圆角,加大出 模斜度,减少壁厚差 缩短开模及抽芯时间 铸件表面有呈直线 状或波浪形的纹路, 狭小而长,在外力作 用下有发展趋势。冷 裂:开裂处金属没被氧 化.热裂:开裂处金属已 被氧化。 5 6 7 顶出时受力不均匀 7 变更或增加顶出位置,使顶出受力 均匀 铝合金压铸件常见外观缺陷 外观: 变形、磕碰 变 形 磕 碰 前 磕 碰 后 特征:压铸件几何形状与图纸不符或整体变形/局部变形。 铝合金压铸件常见外观缺陷 外观:变形、磕碰原因 特征 产生原因 铸件结构设计不良,引起 不均匀收缩 .开模过早,铸件刚性不够 顶杆设置不当,顶出时受 力不均匀 切除浇口方法不当 由于模具表面粗糙造成局 部阻力大而引起顶出时变 形 放置和转运时产生的挤压 碰撞 防止措施 1 2 3 4 5 1 2 3 4 5 6 改进铸件结构 调整开模时间 合理设置顶杆位置及数量 选择合适的切除浇口方法 加强模具型腔表面抛光,减少 脱模阻力 码放整齐,轻拿轻放 压铸件几何形 状与图纸不符或整 体变形/局部变形。 6 铝合金压铸件常见外观缺陷 外观:流痕、花纹 特征:铸件表面上有与金属液流动方向一致的条纹,有明显可见的与 金属体颜色不一样的无方向性的纹路,无发展趋势。 铝合金压铸件常见外观缺陷 外观:流痕、花纹原因 特征 产生原因 首先进入型腔的金属液形成一 个极薄的而又不完全的金属层 后,被后来的金属液所弥补而 留下的痕迹 .模温过低,模温不均匀 内浇道截面积过小及位置不当 产生喷溅 作用于金属液的压力不足 防止措施 1 1 提高金属液温度 2 2 提高模温 3 铸件表面上有与 金属液流动方向一致 的条纹,有明显可见 的与金属体颜色不一 样的无方向性的纹 路,无发展趋势。 3 调整内浇道截面积或位置 4 4 调整充填速度及压力 5 花纹:涂料用量过多 5 选用合适的涂料及调整用量 铝合金压铸件常见外观缺陷 外观:冷隔 特征:压铸件表面有明显的、不规则的、下陷线性纹路(有穿透与不 穿透两种)形状细小而狭长,有的交接边缘光滑,外力作用下有发 展的可能。 铝合金压铸件常见外观缺陷 外观:冷隔原因 特征 产生原因 两股金属流相互对接,但未完 全熔合而又无夹杂存在其间,离心铸造 两股金属结合力很薄弱 浇注温度或压铸模温度偏低 1 2 3 4 5 适当提高浇注温度和模具温度 防止措施 1 2 3 4 5 6 选择合金不当,流动性差 正确选用合金,提高合金流动性 压铸件表面有明 显的、不规则的、下 陷线性纹路(有穿透 与不穿透两种)形状 细小而狭长,有的交 接边缘光滑,外力作 用下有发展的可能。 浇道位置不对或流路过长 提高压射速度,同时加大内浇口截 面积 改善排气、填充条件 填充速度低 压射比压低 提高压射比压,缩短填充时间 铝合金压铸件常见外观缺陷 外观:变色、斑点 特征:铸件表面上呈现出不同的颜色及斑点。 铝合金压铸件常见外观缺陷 外观:变色、斑点原因 特征 产生原因 防止措施 1 不合适的脱模剂 1 .更换优质脱模剂 2 脱模剂用量过多,局部堆积 2 严格喷涂量及喷涂操作 3 含有石墨的润滑剂中的石墨落 入铸件表层 3 更换优质脱模剂 4 铸件表面上呈现 出不同的颜色及斑点。 模温过低,金属液温度过低导 致不规则的凝固引起 4 控制模温,控制金属液温度 铝合金压铸件常见外观缺陷 外观:网状毛翅 特征:网状发丝一样凸起或凹陷的痕迹,随压铸次数增加而不断扩大 和延伸。 铝合金压铸件常见外观缺陷 外观:网状毛翅 特征:网状发丝一样凸起或凹陷的痕迹,随压铸次数增加而不断扩大 和延伸。 铝合金压铸件常见外观缺陷 外观:网状毛翅原因 特征 产生原因 1 压铸模型腔表面龟裂 防止措施 1 加强模具的日常保养 2 压铸模材质不当或热处理工艺 不正确 2 确选用压铸模材料及热处理工艺 压铸模要定期或压铸一定次数后退 火,消除内应力;合理选择模具冷 却方法 3 压铸模冷热温差变化大 3 4 浇注温度过高 4 浇注温度不宜过高,尤其是高熔点 合金 模具预热要充分 打磨成型部分表面,减少表面粗糙 度Ra值 网状发丝一样凸 起或凹陷的痕迹,随 压铸次数增加而不断 扩大和延伸。 5 6 .压铸模预热不足 型腔表面粗糙 5 6 铝合金压铸件常见外观缺陷 外观:凹陷 特征:铸件平滑表面上出现凹陷部位。 铝合金压铸件常见外观缺陷 外观:凹陷原因 特征 产生原因 防止措施 1 铸件壁厚相差太大,凹陷多产 生在厚壁处 模具局部过热,过热部分凝固 慢 压射比压低 1 铸件壁厚设计尽量均匀 2 2 模具局部冷却调整 3 3 .提高压射比压 铸件平滑表面上 出现凹陷部位。 4 由憋气引起型腔气体排不出, 被压缩在型腔表面与金属液界 面之间 4 改善型腔排气条件 铝合金压铸件常见外观缺陷 外观:欠铸 特征:铸件表面有浇不足部位轮廓不清。 铝合金压铸件常见外观缺陷 外观:欠铸 特征:铸件表面有浇不足部位轮廓不清。 铝合金压铸件常见外观缺陷 外观:欠铸原因 特征 产生原因 1 1.1 流动性差原因 合金液吸气、氧化夹杂物, 含铁量高,使其质量差而降 低流动性 浇注温度低或模温低 充填条件不良 比压过低 1 .提高合金液质量 防止措施 1.2 2 2.1 2 3 4 提高浇注温度或模具温度 检查压铸机能力是否足够 提高比压、充填速度 改善浇注系统金属液的导流方 式,在欠铸部位加开溢流槽、排 气槽 选用合适的涂料及调整用量 2.2 卷入气体过多,型腔的背压 变高,充型受阻 操作不良,喷涂料过度,涂 料堆积,气体挥发不掉 5 铸件表面有浇不 足部位轮廓不清。 3 6 铝合金压铸件常见外观缺陷 外观:毛刺飞边 特征:压铸件在分型面边缘上出现金属薄片。 铝合金压铸件常见外观缺陷 外观:毛刺飞边 特征:压铸件在分型面边缘上出现金属薄片。 铝合金压铸件常见外观缺陷 外观:毛刺飞边原因 特征 产生原因 防止措施 检查合模力和增压情况,调整压铸 工艺参数 是采用闭合压射结束时间控制 系统,可实现无飞边压铸 清洁型腔及分型面 1 锁模力不够 压射速度过高,形成压力冲击 峰过高 分型面上杂物未清理干净 1 2 2 3 3 4 模具强度不够造成变形 镶块、滑块磨损与分型面不平 齐 4 增加模具厚度和支撑柱 压铸件在分型面 5 边缘上出现金属薄片。 5 修整模具 铝合金压铸件常见内部缺陷 内部:气孔 特征:解剖后外观检查或探伤检查,气孔具有光滑的表面、形状为圆形。 铝合金压铸件常见内部缺陷 内部:气孔原因 特征 产生原因 合金液导入方向不合理或金属 液流动速度太高,产生喷射; 过早堵住排气道或正面冲击型 壁而形成漩涡包住空气,这种 气孔多产生于排气不良或深腔 处 由于炉料不干净或熔炼温度过 高,使金属液中较多的气体没 除净,在凝固时析出,没能充 分排出 涂料发气量大或使用过多,在 浇注前未浇净,使气体卷入铸 件,这种气孔多呈暗灰色表面 压射速度过快,高速切换点不 对 防止措施 1 1 引导金属液平衡,有序充填型腔, 有利气体排出;排气槽、溢流槽要 有足够的排气能力 2 2 采用干净炉料,控制熔炼温度,离心铸造进 行排气处理 3 解剖后外观检查 或探伤检查,气孔具 有光滑的表面、形状 为圆形。 3 选择发气量小的涂料及控制排气量 4 4 选择合理工艺参数、压射速度、高 速切换点 铝合金压铸件常见内部缺陷 内部:缩孔、缩松 特征:解剖或探伤检查,孔洞形状不规则、不光滑、表面呈暗色。 大而集中为缩孔,小而分散为缩松 铝合金压铸件常见内部缺陷 内部:缩孔、缩松 特征:解剖或探伤检查,孔洞形状不规则、不光滑、表面呈暗色。 大而集中为缩孔,小而分散为缩松 铝合金压铸件常见内部缺陷 内部:缩孔、缩松 起动机端盖的 CT片 特征:解剖或探伤检查,孔洞形状不规则、不光滑、表面呈暗色。 大而集中为缩孔,小而分散为缩松 铝合金压铸件常见内部缺陷 内部:缩孔、缩松原因 特征 产生原因 铸件在凝固过程中,因产生收 缩而得不到金属液补偿而造成 孔穴 浇注温度过高,模温梯度分布 不合理 压射比压低,增压压力过低 内浇口较薄、面积过小,过早 凝固,不利于压力传递和金属 液补缩 铸件结构上有热节部位或截面 变化剧烈 金属液浇注量偏小,余料太 薄,起不到补缩作用 防止措施 1 1 加快厚大部位冷却 2 3 2 3 降低浇注温度,减少收缩量 提高压射比压及增压压力,提高致 密性 修改内浇口,使压力更好传递,有 利于液态金属补缩作用 改变铸件结构,消除金属积聚部 位,壁厚尽可能均匀 加厚料柄,增加补缩的效果 4 4 解剖或探伤检查, 孔洞形状不规则、不 光滑、表面呈暗色。 大而集中为缩孔 小而分散为缩松 5 6 5 6 铝合金压铸件常见内部缺陷 内部:夹杂 特征:混入压铸件内的金属或非金属杂质,加工后可看到形状不规 则,大小、颜色、亮度不同的点或孔洞。 铝合金压铸件常见内部缺陷 内部:夹杂原因 特征 产生原因 防止措施 使用清洁的合金料,特别是回炉炉 上脏物必须清理干净 合金熔液须精炼除气,将熔渣清干 净 用勺取液浇注时,仔细拨开液面, 避免混入熔渣和氧化皮 定期清理保温炉 1 炉料不洁净,回炉料太多 1 2 合金液未精炼 2 3 用勺取液浇注时带入熔渣 坩埚含有保温材料脱落混入金 属液中 3 混入压铸件内的金 属或非金属杂质,加 工后可看到形状不规 则,大小、颜色、亮 度不同的点或孔洞。 4 4 5 保温温度高,持续时间长 5 控制保温温度和减少保温时间 铝合金压铸件常见内部缺陷 内部:脆性 特征:铸件基体金属晶粒过于粗大或极小,使铸件易断裂或磁碎。 铝合金压铸件常见内部缺陷 内部:脆性原因 特征 产生原因 防止措施 1 铝合金中杂质锌、铁超过规定 范围 1 .严格控制金属中杂质成分 2 合金液过热或保温时间过长, 导致晶粒粗大 2 控制熔炼工艺 铸件基体金属晶粒 过于粗大或极小,使 铸件易断裂或磁碎。 3 激烈过冷,使晶粒过细 3 降低浇注温度,.提高模具温度 铝合金压铸件常见内部缺陷 内部:渗漏 特征:压铸件经耐压试验,产生漏气、渗水。 铝合金压铸件常见内部缺陷 内部:渗漏原因 特征 产生原因 1 压力不足,基体组织致密度差 防止措施 1 提高比压 2 内部缺陷引起,如气孔、缩孔、 渣孔、裂纹、缩松、冷隔、花 2 纹 针对内部缺陷采取相应措施 3 4 压铸件经耐压试 验,产生漏气、渗水。 浇注和排气系统设计不良 压铸冲头磨损,压射不稳定 3 4 5 改进浇注系统和排气系统 更换压室、冲头 进行浸渗处理,弥补缺陷 铝合金压铸件常见内部缺陷 内部:硬质点 特征:机械加工过程或加工后外观检查或金相检查:铸件上有硬度高 于金属基体的细小质点或块状物使刀具磨损严重,加工后常常显示 出不同的亮度。 铝合金压铸件常见内部缺陷 内部:非金属硬质点原因 特征 产生原因 防止措施 1 混入了合金液表面的氧化物 1 铸造时不要把合金液表面的氧化物 舀入勺内 2 机械加工过程或 加工后外观检查或金 相检查:铸件上有硬 度高于金属基体的细 小质点或块状物使刀 具磨损严重,加工后 常常显示出不同的亮 度。离心铸造 合金与炉衬的反应物 2 清除铁坩埚表面的氧化物后,再上 涂料,及时清理炉壁,炉底的残渣 3 金属料混入异物 3 清除勺子等工具上的氧化物 4 夹杂物 4 金属料干净、纯净 铝合金压铸件常见内部缺陷 内部:金属硬质点原因 特征 产生原因 1 2 混入了未溶解的硅元素 防止措施 1 2 调整合金成分时,不要直接加入硅 元素,必须采用中间合金 合金中含Si量不宜接近或超过共晶 成分,对原材料控制基体金相组织 中的初晶硅数量 提高熔化温度、浇注温度 控制合金成分,特别是Fe杂质量 避免Fe、Mn等元素偏析 初晶硅 铝液温度较低,停放时间较 长,Fe、Mn元素偏析,产生 金属间化合物 机械加工过程或 加工后外观检查或金 相检查:铸件上有硬 度高于金属基体的细 小质点或块状物使刀 具磨损严重,加工后 常常显示出不同的亮 度。 3 3 4 5 以上,谢谢!
以上信息由江苏亚立特钢有限公司整理编辑,了解更多离心铸造信息请访问http://www.jsyltg.com