新闻中心
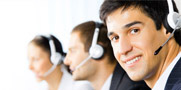
咨询热线:
134-0554-5577
邮件:874556408@qq.com
电话:0523-83984388
地址:江苏省兴化市沈伦镇工业园区沈北路
离心铸造浇入压室 2 的金属液 3 被已
压力铸造工艺 一、压铸及特点 1. 压铸定义及特点 压力铸造(简称压铸)是在压铸机的压室内,浇入液态或半液态的金属或合金,使 它在高压和高速下充填型腔,并且在高压下成型和结晶而获得铸件的一种铸造方法。 由于金属液受到很高比压的作用,因而流速很高,充型时间极短。高压力和高速度 是压铸时液体金属充填成型过程的两大特点,也是压铸与其他铸造方法根本区别之所 在。 比如压射比压在几兆帕至几十兆帕范围内,甚至高达 500MPa;充填速度为 0.5— 120m/s,充型时间很短,一般为 0.01-0.2s,短只有干分之几秒。 2. 压铸的优缺点 优点: 1) 产品质量好。由于压铸型导热快,金属冷却迅速,同时在压力下结晶,铸件具有 细的晶粒组织,离心铸造表面坚实,提高了铸件的强度和硬度,此外铸件尺寸稳定,互换性好, 可生产出薄壁复杂零件; 2) 生产率高,压铸模使用次数多; 3) 经济效益良好。压铸件的加工余量小,一般只需精加工和铰孔便可使用,从而节 省了大量的原材料、加工设及工时。 缺点: 1) 压铸型结构复杂,制造费用高,准周期长,所以,只适用于定型产品的大量生 产; 2) 压铸速度高,型腔中的气体很难完全排出,加之金属型在型中凝固快,实际上不 可能补缩,致使铸件容易产生细小的气孔和缩松,铸件壁越厚,这种缺陷越严重,因此, 压铸一般只适合于壁厚在 6mm 以下的铸件; 3) 压铸件的塑性低,不宜在冲击载荷及有震动的情况下工作; 4) 另外,高熔点合金压铸时,铸型寿命低,影响压铸生产的扩大应用。 综上所述,压力铸造适用于有色合金,小型、薄壁、复杂铸件的生产,考虑到压铸 其它技术上的优点,铸件需要量为 2000-3000 件时,即可考虑采用压铸。 3.压铸的应用范围 压铸是近代金属加工工艺中发展较快的一种高效率、 少无切削的金属成型精密铸造 方法,是一种“好、快、省”高经济双效益的铸造方法。 压铸零件的形状大体可以分为六类: 1)圆盘类——号盘座等; 2)圆盖类——表盖、机盖、底盘等; 3)圆环类——接插件、轴承保持器、方向盘等; 4)筒体类——凸缘外套、导管、壳体形状的罩壳盖、上盖、仪表盖、探控仪表罩、 照像机壳与化油器等; 5)多孔缸体、壳体类——汽缸体、汽缸盖及油泵体等多腔的结构较为复杂的壳体 (这类零件对机械性能和气密性均有较高的要求,材料一般为铝合金)。例如汽车 与摩托车的汽缸体、汽缸盖; 6)特殊形状类——叶轮,喇叭、字体由筋条组成的装饰性压铸件等。 二、压铸机简介 压铸机是压力铸造的基本设。压铸机共分两大类:热室压铸机和冷室压铸机。 (1) 热室压铸机 热室压铸机如图 2-14 所示,其特点是压室与合金熔化炉连成一 体,压室浸在熔化的液态金属中,其压射机构安置在保温坩埚上面。当压射冲头 3 上升 时,金属液 1 通过进口 5 进入压室 4 中,随后压射冲头下压,金属液沿通道 6 经喷嘴 7 充填压型型腔 8。冷凝后冲头回升,多余金属液回流至压室中,然后打开压型取出铸件。 (图 2-14 热室压铸机原理) 热室压铸机的特点是生产工序简单,生产效率高,容易实现自动化;金属液消耗少, 工艺稳定,压入型腔的金属液干净、无氧化夹杂,铸件质量好。但由于压室和冲头长时 间浸在金属液中,影响使用寿命。目前,大多数用于压铸锌合金等低熔点合金铸件,但 也有用于压铸镁铝铸件。 (2) 冷室压铸机 该机的压室与保温炉是分开的。压铸时,要从保温炉中将金属液 倒入压室后进行压铸。冷室压铸机有立式和卧室两种。 立式压铸机压室的中心线是垂直的。压铸模与压室的相对位置及压铸过程如图 2-15 所示。合模后,浇入压室 2 的金属液 3 被已封住喷嘴孔 6 的反料冲头 8 托住,当压射冲 头向下压到金属液面时,反料冲头开始下降,打开喷嘴 6,金属液被压入型腔。凝固后, 压射冲头退回,反料冲头上升,切断余料 9,并将其顶出压室,余料取走后再降到原位, 然后开模取出铸件。(图 2-15 立式冷室压铸机原理) 卧室压铸机压室的中心线是水平的。压铸模与压室的相对位置及压铸过程如图 2-16 所示。合模后,金属液浇入压室 2,压射冲头 1 向前推进,将金属液经浇道压入型腔 6, 开模时,余料借助压射冲头前伸的动作离开压室,同铸件一起取出。(图 2-16 室压铸机原理图) 两种压铸机相比较,在结构上仅仅压射机构不同,立式压铸机有切断、顶出余料的 下油缸,因结构比较复杂,故增加了维修的困难。卧室压铸机压室简单,维修方便。在 工艺上,立式压铸机压室内空气不会随金属液进入型腔,便于开设中心浇口,但由于浇 口过长,金属耗量大,充填过程中能量损失也较大。卧式压铸机金属液进入型腔的流程 短,压力损失小,有利于传递终压力,便于提高比压,故使用较广。冷室压铸机多用 液压驱动,压力较高,适用于熔点较高的合金。目前,生产中采用冷室压铸机较多。 卧式冷 三、压铸过程原理 压铸过程是利用高压力、高速度,迫使浇入压铸机压室内的熔融或半熔融状态金属 在极短的时间内充满压铸模的型腔。 压铸过程有三种主要现象:其一压入,其二熔融合金液流动,其三冷却凝固。 完成压铸过程有三大要素:一是熔融或半熔融状态金属:二是压铸模:三是压铸机。 压铸压力、压铸速度是压铸过程主要的工艺参数。 1.压铸压力 压铸压力—般用压射力,比压表示。压射力是由压铸机的规格所定。它是压铸机的 压射机构推动压射冲头的力: Pr=PG?πD2/4 压射比压: Pb = Pr / F = 4 P r/ πd2 四个阶段: 慢速封孔;充填;增压;保压 2。压铸速度 压铸速度有压射速度和充填速度两个不同的概念。 压射速度:压铸时压射缸内液压推动压射冲头前进的速度; 充填速度:熔融合金在压力作用下,通过内浇口导入型腔的线速度。离心铸造 其中充填速度的主要作用有:将熔融合金在凝固之前迅速输入型腔,是获得轮廓清 晰、表面光洁的铸件重要因素;为了得到高的流体动压力。 充填速度的选择可根据合金的性能及铸件结构的特点,充填速度与压射比压、压射 速度及内浇口截面积等因素有关。 由于压铸特点是速度快,当充填速度较高时,即使用较低的比压也可以获得表面光 洁的铸件。 过高的充填速度会引起许多工艺上的缺点,造成压铸过程的不利条件: (1) 包住空气而形成气泡。因为高速度合金液流可能堵住排气系统,使空气被 包在型腔内,同时快速冷却液可能使得熔体内溶解的气体不能有效析出; (2) 合金液流成喷雾状进入型腔并粘附于型壁上, 后进入的合金液不能与它熔 合,而形成表面缺陷,降低铸件表面质量; (3) 产生旋涡,包住空气和进入型腔的冷合金,使铸件产生气孔和氧化夹 杂的缺陷; (4) 冲刷压铸模型壁,使压铸模磨损加速,减少压铸模寿命。 充填速度与压射速度、作用于熔融合金上的压射比压以及合金液本身的密度、压室 内径和内浇口截面积等有关。压射速度越大,则充填速度越大,合金液上的压射比压越 大,充填速度也越大。可通过调整变化压射速度和压射比压、改变压室的内径和增大内 浇口截面积(厚度)等来改变充填速度。 四、压铸件设计 压铸件设计是压铸生产技术中十分重要的工作环节,压铸件设计的合理程度和工艺 适应性直接影响到:分型面的选择,浇口的开设;顶出的布置;收缩规律;精度的保证; 缺陷的部位以及生产效率等。压铸件结构工艺特定要求如下: ①消除内部侧凹,便于抽芯。 ②改进壁厚,消除缩孔、气孔; ③改善结构,消除不易压出的侧凹; ④利用筋,防止变形; ⑤改善结构,消除尖角或棱角; ⑥改善结构,便于抽芯、简化压铸模制造; ⑦消除深陷,使铸件易脱模; ⑧改进结构,离心铸造避免型芯交叉等特定要求。 五、压铸合金及其选择 对压铸合金的要求: ①高温下有足够的强度和可塑性,无热脆性(或热脆性小); ②尽可能小的收缩; ③结晶温度范围小; ④在过热温度不高时有足够的流动性。 选择压铸合金考虑的因素有: (1)压铸件的受力状态,这是选择合金主要依据; (2) 压铸件工作环境状态; ①工作温度:高温和低温要求, ②接触的介质:如潮湿大气、海水; ③密闭性要求:气压、液压密闭性。 (3)压铸件在整机或部件中所处的工作条件; (4)对压铸件的尺寸和重量所提出的要求; (5)生产条件:熔化设、压铸机、工艺装置及材料等; (6)经济性。 六、压铸型 在压铸生产中,压铸型(简称压模或压型)是重要的工艺装。 从结构上讲,完整的压铸型由以下几部分组成(图 2-17 是压铸型结构的实例。): ①静型部分:固定于压铸机压室一方的静型安装板上,是金属液开始进入铸型的部 分,也是压铸型型腔的组成部分,其上有直浇道直接与压铸机的喷嘴或压室联接; ②动型部分:固定于压铸机的动型安装板上,随动型安装板向左、向右移动,与静 型部分分开和合拢,一般抽芯机构和铸件顶出机构设置在这部分内,是压铸型型腔的组 成部分; ③成型部分:是构成铸件几何形状的部分。构成铸件外形的部分称为型腔,构成铸 件内部形状的部分称为型芯; ④浇注系统:连接成形部分与压室,引导金属液按一定方向进入铸型的成型部分, 包括直浇道、横浇道和内浇口; ⑤抽芯机构:构成复杂铸件的侧凹和孔,采用活动型芯,依靠抽芯机构在顶出铸件 之前完成抽芯动作; ⑥顶出机构:铸件成型后,待动、静型分开,把铸件从铸型中,这套机构一般均设 在动型部分; ⑦排气部分; ⑧加热、冷却部分:为了平衡铸型温度,不致使铸型温度有急剧的变化,从而影响 铸件质量,很多场合下,压铸型有必要安装加热或冷却装置; ⑨其它:压铸型内还需设有定位、导向、紧固等元件。 七、压铸件缺陷 压铸件的缺陷多种多样,一般分为表面缺陷、表面损伤、内部缺陷、裂纹、几何形 状与图样不符、材料性能与要求不符、杂质等。 表面缺陷包括流痕及花纹、网状毛翅、冷隔、缩陷、印痕、铁豆等;表面损伤包括 机械拉伤、粘模拉伤和碰伤; 内部缺陷包括气孔、气泡、缩孔缩松; 几何形状与图样不符一般指欠铸及轮廓不清晰、变形、飞翅、多肉或带肉、错边或 错扣、型芯偏位; 材料性能与要求不符一般指化学成分和力学性能不符合要求;杂质缺陷指夹渣和硬 点。 虽然压铸件缺陷多种多样,但仔细分析,就知道它们都与压铸工艺参数的选择、压 铸型的设计及人员操作有关。比如,对于流痕及花纹缺陷,有可能是模温过低、比压偏 低、内浇道面积过小等原因产生,当然,解决办法就是提高模温、调整内浇道截面积或 者调整压射速度及压力。
以上信息由江苏亚立特钢有限公司整理编辑,了解更多离心铸造信息请访问http://www.jsyltg.com