新闻中心
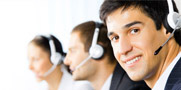
咨询热线:
134-0554-5577
邮件:874556408@qq.com
电话:0523-83984388
地址:江苏省兴化市沈伦镇工业园区沈北路
3铸型内的浇道应 能使金属液顺利流入型腔
卧式离心铸造机_化学_自然科学_专业资料。卧式离心铸造机 一、铸造的定义 铸造是熔炼金属,制造铸型,并将熔融金属浇入铸型,凝固后获得具有一定形状、尺 寸和性能金属零件毛坯的成型方法。铸造是将金属熔炼成符合一定要求的液体并浇进铸型 里,经冷却凝
卧式离心铸造机 一、铸造的定义 铸造是熔炼金属,制造铸型,并将熔融金属浇入铸型,凝固后获得具有一定形状、尺 寸和性能金属零件毛坯的成型方法。铸造是将金属熔炼成符合一定要求的液体并浇进铸型 里,经冷却凝固、清整处理后得到有预定形状、尺寸和性能的铸件的工艺过程。铸造毛坯因 近乎成形,而达到免机械加工或少量加工的目的降低了成本并在一定程度上减少了制作时 间。铸造是现代装置制造工业的基础工艺之一。 二、离心铸造的分类 为实现上述工艺过程,必须采用离心铸造机创造使铸旋转的条件。根据铸型旋转轴在空 间位置的不同,常用的有立式离心铸造机和卧式离心铸造机两种类型。 立式离心铸造机上的铸型是绕垂直轴旋转的(图 1),它主要用来生产高度小于直径的 圆环类铸件,有时也可用此种离心铸造机浇注异形铸件。 卧式离心铸造机的铸型是绕水平轴旋转的(图 2),它主要用来生产长度大于直径的套 类和管类铸件。 设计原则 设计离心铸管机时需要确定几项参数:浇注时管模的转速,浇注速度,浇注时间等,并 遵循以下四个原则。 1、离心机的下行速度应均匀,保证铸管壁厚均匀,不同规格的铸管下行速度不同。 2、浇注不同规格的铸管时,配用不同容量的扇形包。一套扇形包的倾动机构在一种倾 倒速度的条件下,可以倾倒出不同重量的铁水量。 3、管模的冷却水量采用闭环控制,根据水的出口和入口温度控制冷却水量。 4、离心铸管模的转速应保证液态金属进入管模后立刻成圆筒形,并能得到良好的铸管 内部组织,根据不同规格的铸管确定不同的转速。 三、卧式离心铸造特点 卧式离心铸造的特点是金属液在离心力的作用下充型和凝固,金属补缩效果好,铸件 外层组织致密,非金属夹杂物少,机械性能好。离心铸造不用造型、制芯,节省了相关材料 及设投入。铸造空心铸件不需浇冒口,金属利用率可大大提高。因此对某些特定形状的铸 件来说,离心铸造是一种节省材料、节省能耗、高效益的工艺,但须特别注意采取有效的安 全措施。 卧式离心铸造可以获得无缩孔、气孔、夹渣的铸件,而且组织细密、机械性能好。当铸 造圆形中空零件时,可以省去型芯。此外,离心铸造不需要浇注系统,减少了金属的消耗。 但离心铸造铸出的筒形零件内孔自由表面粗糙、尺寸误差大、质量差,有较多气孔、夹渣, 因此需增加加工余量,而且不适宜浇注容易产生比重偏析的合金及铝镁等合金。 四、发展史 1809 年,英国人埃尔恰尔特申请了有关卧式离心铸造和立式离心铸造的个专利。 1849 年,英国人安德鲁·逊克制作出台离心铸管机,而后生产了长达 3.6m、直径 为 75mm 的离心铸铁管。 1857 年德国人汉内·贝士麦提出用立式离心铸造生产轮圈。 1862 年英国人惠尔利和鲍韦尔制作出了铸造轮圈的立式离心铸造机。 1910 年德国人奥托·勃里代发明用移动浇注槽生产金属型离心铸管的方法。 1914 年巴西人代拉夫得和阿伦斯研究水冷型离心铸管法成功。1917 年美国人莫尔创造 了砂型离心铸管法,1920 年开始用于大量生产。 1950 年在瑞典开始用涂料金属型离心铸造法生产主要用于下水道的小口径铁管。 50 年代美国离心铸管建立了树脂砂型离心铸管法。 30 年代以后离心铸造法逐步推广应用于生产汽缸套、炮身、鼓轮等铸件。 在 20 世纪 40 年代出现了用离心铸造法生产双金属复合冶金轧辊的工艺。 五、铸造工艺 1、离心机的选择 如表 2-2 所示,根据零件尺寸选择 1 号卧式三级离心机。 表 2-2 离心机选择表 序号 规格(mm) 功率(KW) 车速(转/分) 形式 1 300? 4 1150 卧式三级 2 600? 800 10 900 卧式二级 3 700? 200 20 800 立式二级 4 1100? 600 40 700 立式二级 2、离心机转速的确定 离心机转速直接影响铸件质量,转速过低使铸件内圆产生金属堆积,合金液中的氧化夹 杂物不易离出,铸件产生类渣;转速过高铸件容易产生偏析,尤其是铸件壁厚较大,结晶温 度范围较宽的合金和合金中成分比重相差较大的元素。如锡、铅等。通常我们用如下经验方 法来确定。铸件的直径小,需要的离心力大,速度靠上限取,反之取较小的转速。此处铸件 的直径是指内孔而不是外圆,见表 2-3 所示。 表 2-3 离心机转速表 形式 直径(mm) 转速(r/min) 卧式 50~100 100~200 200~ ~600 800~1300 950~1100 750~950 600~750 立式 600~800 800~1100 600~700 500~600 零件内径是 130mm,选取转速 950~1100r/min。 3、浇注温度 浇注温度是保证合格铸件的主要参数之一。本次设计为管状零件,金属液充型时遇到阻 力较小,又有离心压力或离心力加强金属液的充型性,故离心铸造是的浇注温度可比重力浇 注低 5℃~10℃。浇注温度过高铸件外圆容易产生气孔,浇口部位将产生缩孔。浇注温度过 低铸件外圆产生冷隔、皱皮,铸件内部产生夹层、壁厚不均、内圆堆积金属等缺陷。45 钢 的熔化温度 1460℃~1467℃,出钢温度 1560℃~1580℃,浇注温度 1500℃~1550℃。 4、浇注速度 离心机因采用金属型模具,冷却速度较快,采用快速浇注能获得优质铸件。由零件 参数得质量为? (r2 ? r02 ) ? 4.4 kg。根据表 2-5,选取包孔直径 30mm,浇注时间 0.5s。 表 2-5 钢液浇注重量速度平均值 包孔直径 浇注重量速度 注 30 10 35 20 包 孔 直 径 :mm, 浇 注 重 量 速 40 27 度:kg/s 45 42 50 55 5、浇注系统 离心铸造浇注系统应满足下列要求:(1)浇注长度长、直径大的铸件时,浇注系统应使 金属液能较快的均匀的铺在铸型内表上。(2)尽可能减少金属液飞溅。(3)铸型内的浇道应 能使金属液顺利流入型腔。(4)浇注终了,浇杯和浇注槽内应不留金属和熔渣,如果有熔渣 也应该易于清理。 离心铸造的浇口没有手工铸造的要求严格,但浇口位置不当也会使铸件产生缺陷,突出 的缺陷有,纵向壁厚不均,浇口近的地方过厚,远离浇口的地方很薄,铸件两头产生氧化夹 杂物,特别是卧式离心机。因此对直径小而长的铸件,尽量将浇口伸进金属模 1/3~1/2 处较 为理想;直径大而短的铸件,浇口伸进金属模的深度约 1/3~1/2 处即可。浇口的深度确定之 后,还必须调整浇口方向,浇口方向不能朝上顺着离心机的旋转方向,也不能直顶着离心机 的旋转方向。合适的浇口方向始终与离心机的旋转方向形成一个 15°左右的夹角,不得 超过 30°,能有效地保证铸件质量。本次设计选择伸进金属模 1/3 处。选择管式浇注杯。 6、铸型转动时间 当金属液注入金属模后,要有足够的时间使液态金属转变为固态金属,整个转变过程是在离 心机旋转过程中进行的,不可以停机。若是过早停机,铸件将会产生凸瘤和不圆现象。简 单的办法是观察铸件颜色,呈暗红色时停机、取件。一般转动时间取 10s。 六、缺陷分析及注意事项 1、缺陷分析 离心铸造合金钢管常出现的缺陷有:充型不完整,表面气孔,钢管表层夹砂,裂纹, 试压渗漏,夹渣与渣痕,表面局部针刺。 1、裂纹。钢管裂纹有纵裂和横裂。纵裂纹主要是由于合金在凝固时转速过高,往往伴 随离心机振动较大时出现,生产中纵裂纹出现不多。 实际中横裂纹较多见,裂纹多靠管子一端,裂纹有时穿透管壁,严重者管子一出型就断 开了。 2、试压渗漏。钢管在试压时,在表面出现大面积渗漏,呈现一片片泅水现象,造成报 废。 3、充型不完整。在离心铸造钢管中充型不完整常有两种情况:一种是外型缺浇,管子 未达到足够的长度;另一种是管子壁厚不均,在管子浇注的彼端壁较薄。此缺陷常发生于壁 厚在 8mm 以下的薄壁钢管中,特别是长径比大的管子(L/D>15,L 管长;D 管径)。 4、表面气孔。在钢管表面局部存在气孔,直径为 0.2mm~2mm,深 0.5mm~2mm,气孔 分布的密度约为 2~12 个/cm?。呈现出很均匀的一片片的气孔。 5、钢管表层夹砂。在钢管表面局部出现粗糙麻面并稍有凸起,粗糙麻面有清晰的周边 轮廓。严重时成为环带状夹砂。当去掉粗糙的钢表层后可见存在其中的薄涂料层即夹砂。夹 砂部位经过 1mm~2mm 的加工即可去除。但它严重影响铸皮质量,如是非加工的钢管就很 可能报废。这种缺陷多出现于挂涂料的钢管。 6、夹渣与渣痕。 夹渣,有时管子表面并未见有夹渣,经试压发现局部小面积渗漏,经剖破检验发现在漏 水处管壁中存在夹渣,某生产镁罐筒曾出现过此现象。 渣痕,有时在钢管的内表面存在小凹陷,大小、深浅不等。在薄壁钢管中凹陷处使壁厚 减薄较多。由于钢管内表面存留较大块浮渣,待其脱落后便显出凹陷,所以是渣痕。渣物的 密度比钢液小时在离心力作用下浮到内表面,但由于渣物本身的重力使其沉入钢液一定深 度,从而形成渣痕。 7、表面局部针刺。在靠近钢管的一端有时会出现针刺。针刺的直径为 0.5mm~1mm, 高为 2mm~3mm,每平方厘米内 1 根左右。这种现象常发生在涂料层较厚的情况下。 2、注意事项: 生产离心铸件的生产操作控制工艺技术参数在设置时,特别要注意以下九个要点。 (1)对低碳钢铸件,浇注时要提高砂箱内的真空度 砂箱应采用双层箱壁真空室结构,浇注时抽真空能加速热分解物逸出涂层到型腔外,从而减 少模样热分解产物的浓度和与钢水的接触时间,降低或避免铸钢件出现渗碳、积碳现象。型 砂粒度在 20/40 目时,浇注铸钢件时负压以 0.03~0.06MPa 为宜。如果负压度过大,将会引 起铸件粘砂及其它缺陷发生。 (2)选择适宜的密度进行模样制作 在保证模样制作技术要求和铸件浇注时不出现因模样质量引起的其他缺陷的前提下,模样的 密度越小、泡沫塑料质量越少,对减少铸件的渗碳积碳现象就越好。 选择含碳量低的泡沫塑料或预发珠粒制作模样 (3)选用含碳量低或无碳粘接剂 应采用消失模铸造模样专用胶进行模样的粘接组合,不要使用含碳量高的低质普通胶粘接。 在模样粘接时,在保证胶的粘接温度及粘接强度的同时,要尽量减少粘接剂用量,从而降低 粘接剂的热分解产物。 (4)采用底注式浇注系统 对低碳钢铸件,浇注时应尽可能采用底注式浇注方式,使钢水充型流动平稳,模样热分解产 物能顺利进入集渣腔或冒口中,从而降低和减少模样热分解产物中液相和固相的接触反应时 间,降低和消除增碳机率。低碳钢铸件一般不宜使用雨淋式浇注系统,易使铸件增碳、渗碳、 积碳的工况和条件增大,导致铸件产生严重缺陷。 (5)中频炉熔炼,严格控制碳钢配料计算和实际配料、选料、投料操作 因配料计算是保证熔炼出成份合格的钢水及含有少气体与夹杂而铸出优质铸钢件产品的 关键所在。而配料、选料、投料的准确与否,是铸造出产品质量合格与否的根本保证。因此, 对回炉废钢必须建立严格的分检制度。特别是必须将合金钢废料和材质不清楚的废料挑除, 保证熔炼配料材质的成份符合铸造工艺技术参数的要求,是生产离心铸件操作控制中的 要务。 (6)选择确定合理的浇注系统 在进行浇注系统设计时,要尽可能在浇注过程中具有加速模样气化的作用,尽量减少及错开 其热分解产物中液相与固相接触和反应的时间,从而减少或避免铸件的渗碳现象发生。 (7)选择并确定铸件适宜的浇注温度和浇注速度 因相同的铸件如浇注工艺不同,在相同温度浇注钢液时,实际充型温度是完全不相同的。如 浇注温度提高,浇注速度也提高,将造成模样热分解加快而不易完全气化,使热分解产物在 液相中的含量增加,同时因钢液与模样的间隙较小,液相中的热分解物常被挤出间隙后,被 挤到模样涂料层和金属液之间,或钢液流动的冷角、死角,造成接触面增加,碳浓度增加, 渗碳量也将增大。同时特别要注意,如浇注工艺不合理,钢液浇注温度过高且浇注速度太快, 将会造成冒气、反喷等生产事故。 (8)目前国内生产的聚苯乙烯泡塑 EPS 含碳量为 92%;苯乙烯甲基丙烯酸甲酯共聚树脂 STMMAC 含碳量为 69.6%;可发性聚甲基丙烯酸甲酯 EPMMA 含碳量为 60.0%。用 EPS 材 质制作铸件模样将使铸件在浇注过程中,钢水的含碳量增加 0.1%~0.3%,而采用 EPMMA 或 STMMA 材料进行模样制作时,在浇注过程中因模样材质原因造成的铸件增碳量低于 0.05%。 (9)在模样上涂料过程中添加防渗碳材料 在涂料配制过程中加入某些抗增碳的催化剂,如碱金属盐、石灰石粉等,浇注后使涂料层中 能分解出足够量的 CO、CO2 气体进行吸碳,从而防止铸件渗碳;或在涂料中加入氧化剂, 促使模样热分解后的 C、H2 气体转变为中性气体,从而减少模样热分解后形成的 C 与 H 向 铸件内渗入,避免造成铸件增碳或氢脆现象。
以上信息由江苏亚立特钢有限公司整理编辑,了解更多离心铸造信息请访问http://www.jsyltg.com