新闻中心
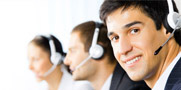
咨询热线:
134-0554-5577
邮件:874556408@qq.com
电话:0523-83984388
地址:江苏省兴化市沈伦镇工业园区沈北路
模架中的各个零件和确定零件是对应离心铸造
毕业设计论文 设计(论文) 题目: 端盖压力铸造工艺设计 下 达 日 期: 2008 年 12 月 08 日 开 始 日 期: 2009 年 04 月 28 日 完 成 日 期: 2009 年 06 月 25 日 指 导 教 师: 学 生 专 业: 材料成型与控制技术 班 级: 材料 0603 班 学 生 姓 名: 田育松 教 研室主任: 材 料 工 程 系 毕业论文 陕西工业职业技术学院毕业设计(论文) 任务书 一、 设计( ...
毕业设计论文 设计(论文) 题目: 端盖压力铸造工艺设计 下 达 日 期: 2008 年 12 月 08 日 开 始 日 期: 2009 年 04 月 28 日 完 成 日 期: 2009 年 06 月 25 日 指 导 教 师: 学 生 专 业: 材料成型与控制技术 班 级: 材料 0603 班 学 生 姓 名: 田育松 教 研室主任: 材 料 工 程 系 毕业论文 陕西工业职业技术学院毕业设计(论文) 任务书 一、 设计( 论文) 内 容及要求: ( 一) 设计( 论文) 内 容 1. 撰写压铸技术发展现状的研究文章; 2. 编制铸件( 附零件图) 铸造工艺规程, 绘制铸造工艺图, 填写铸造工艺过程卡片 ; 3. 绘制铸件图和压铸模具总装图; 4. 设计压铸模具, 绘制模具零件图; 5. 撰写设计说明书( 论文)。 ( 二) 要求 1. 通过理论学习 , 熟悉压铸工艺过程, 结合生产实际完成本次设计任务; 2. 工程图用 AutoCAD 软件绘制并打印; 3. 说明书( 论文) 按照学院统一格式, 使用 word 文档并打印。 4. 提交资料包括: ( 1) 毕业设计任务书; ( 2) 压力铸造技术发展现状的研究文章; ( 3)“四图一卡”, 即绘制铸造工艺图; 铸件图; 铸型装配图; ( 4) 设计说明书( 论文)。 所有提交的资料包括打印文件和电子文件。 二、 技术指标: 1. 生产类型: 大批大量生产 2. 生产及质量要求: 满足产品图纸的各项技术要求; 工艺出品率较高, 废品率 5% 以下; 生产效率高; 对工人技术水平要求较低, 操作简便。 3. 生产工艺要求: 压力铸造; 机械化生产; 所用 压铸模具自 行设计; 4. 技术水平要求: 尽量采用 先进技术, 创新项目 应符合国家环保及安全生产要求。 三、 主要参考资料: [1] 曹瑜强. 铸造工艺及设. 北京: 机械工业出版社, 2005 年 7 月 . [2] 林柏年. 特种铸造. 杭州: 浙江大学出版社, 2004 年 7 月 . [3] 模具实用 技术丛书编委会. 压铸模设计应用 实例. 北京: 2005 年 6 月 . [4] 潘宪曾. 压铸模设计手册. 北京: 机械工业出版社, 2006 年 7 月 [5] 中国机械工程学会铸造分会. 铸造非铁合金. 北京: 机械工业出版社, 2001 年 10 月 [6] 唐靖林 曾大本. 铸造非铁合金及其熔炼. 北京: 中国水利水电出版社, 2007 年 [7] 韩莉 邓杰. 机械设计课程设计. 重庆: 重庆大学出版社, 2004 年 7 月 陕西工业职业技术学院毕业设计(论文) 任务书 进 程 计 划 表 序号 起止日 期 计划完成内 容 实际完成情况 检查签名 4. 28-5. 5 设计前的准 1、 根据产品实样绘制零件图 2、 对压铸件进行结构工艺性析 3、 分型面的选择 4、 浇注系统的选择及设计 5、 绘制工艺图 5. 6-5. 10 压铸机的选用 1. 确定比压 2. 确定压铸机的锁模力 3. 确定压铸机的型号 4. 压铸机部分性能指标校核 5. 11-5. 15 压铸型设计 1、 成型零件的设计 2、 模架的设计及具体尺寸的确定 3、 抽芯机构的设计 4、 推出机构的设计 5、 排溢系统的设计 6、 压铸模具的校核 5. 16-5. 19 压铸常规工艺的确定以及工艺卡的制定 5. 20-5. 30 绘制模具总装图与零件图 5. 31-6. 5 熔炼工艺 1、 合金的选用 2、离心铸造 熔炼方法的选用 3、 配料计算 4、 熔炼、 浇注 5、 铸件的清理及检验 整理并编写设计说明书 摘要 对压力铸造基本知识、 压铸工艺、 及压铸设有了较为全面的掌握介绍了端盖的压铸工艺设计, 论述了压铸机的选用、 压型的设计、 铸件材料的选 用及熔炼和浇注、 铸件的清理及检测。 对 ZL102 的熔炼工艺流程, 以及铸件的浇注、 清理、 检验进行了详细的论证。 研究结果表明: 端盖的压力铸造工艺设计合理, 可以满足生产需要。 关键词: 压铸, 铝合金, 铝合金熔炼 ABSTRACT Basic knowledge of pressure casting, die-casting process, and die-casting equipment have introduced more comprehensive grasp of the cover design of the die-casting process, discusses the selection of die-casting machine, pressure type of design, casting and melting material selection and pouring, casting and testing of clean-up. The melting process of ZL102 and pouring the casting, cleaning, inspection carried out a detailed evaluation. The results show that: the pressure of end cover casting process designed to meet production needs. Keywords : Pressure casting , Aluminum Alloy , Aluminum Alloy Melting 目录 毕业设计任务书 中文摘要 英文摘要 目录 . . . . . . . . . . . . . . . . . . . . . . . . . . . . . . . . . . . . . . . . . . . . . . . . . . . . . . . . . . . . . . . . . . . . . . . . 6 一、 前言 . . . . . . . . . . . . . . . . . . . . . . . . . . . . . . . . . . . . . . . . . . . . . . . . . . . . . . . . . . . . . . . . . . . . 1 1、 压铸的基本概念 . . . . . . . . . . . . . . . . . . . . . . . . . . . . . . . . . . . . . . . . . . . . . . . . . . . . . . . 1 2、离心铸造 压铸生产的特点及应用范围 . . . . . . . . . . . . . . . . . . . . . . . . . . . . . . . . . . . . . . . . . . . . . 1 3、 铝合金压铸业的发展及现状 . . . . . . . . . . . . . . . . . . . . . . . . . . . . . . . . . . . . . . . . . . . . . 1 二、 压铸件工艺性分析及设计 . . . . . . . . . . . . . . . . . . . . . . . . . . . . . . . . . . . . . . . . . . . . . . . . . . 2 1、 零件图 . . . . . . . . . . . . . . . . . . . . . . . . . . . . . . . . . . . . . . . . . . . . . . . . . . . . . . . . . . . . . . . 2 2、 工艺性分析 . . . . . . . . . . . . . . . . . . . . . . . . . . . . . . . . . . . . . . . . . . . . . . . . . . . . . . . . . . . 3 3、 分型面的选择 . . . . . . . . . . . . . . . . . . . . . . . . . . . . . . . . . . . . . . . . . . . . . . . . . . . . . . . . . 3 3、 浇注系统的选择及设计 . . . . . . . . . . . . . . . . . . . . . . . . . . . . . . . . . . . . . . . . . . . . . . . . . 4 4、 铸造工艺图 . . . . . . . . . . . . . . . . . . . . . . . . . . . . . . . . . . . . . . . . . . . . . . . . . . . . . . . . . . . 7 三、 压铸机的选用 . . . . . . . . . . . . . . . . . . . . . . . . . . . . . . . . . . . . . . . . . . . . . . . . . . . . . . . . . . . . 8 1、 确定比压 . . . . . . . . . . . . . . . . . . . . . . . . . . . . . . . . . . . . . . . . . . . . . . . . . . . . . . . . . . . . . 8 2、 确定压铸机的锁模力 . . . . . . . . . . . . . . . . . . . . . . . . . . . . . . . . . . . . . . . . . . . . . . . . . . . 8 3、 确定压铸机型号 . . . . . . . . . . . . . . . . . . . . . . . . . . . . . . . . . . . . . . . . . . . . . . . . . . . . . . . 9 4、 压铸机部分性能指标校核 . . . . . . . . . . . . . . . . . . . . . . . . . . . . . . . . . . . . . . . . . . . . . . . 9 四、 压铸型设计 . . . . . . . . . . . . . . . . . . . . . . . . . . . . . . . . . . . . . . . . . . . . . . . . . . . . . . . . . . . . . 10 1、 成型零件的设计 . . . . . . . . . . . . . . . . . . . . . . . . . . . . . . . . . . . . . . . . . . . . . . . . . . . . . . 10 2、 模架的设计及具体尺寸的确定 . . . . . . . . . . . . . . . . . . . . . . . . . . . . . . . . . . . . . . . . . . 13 3、 抽芯机构的设计 . . . . . . . . . . . . . . . . . . . . . . . . . . . . . . . . . . . . . . . . . . . . . . . . . . . . . . 17 4、 推出机构的设计 . . . . . . . . . . . . . . . . . . . . . . . . . . . . . . . . . . . . . . . . . . . . . . . . . . . . . . 19 5、 排溢系统的设计 . . . . . . . . . . . . . . . . . . . . . . . . . . . . . . . . . . . . . . . . . . . . . . . . . . . . . . 21 6、 压铸模具的校核 . . . . . . . . . . . . . . . . . . . . . . . . . . . . . . . . . . . . . . . . . . . . . . . . . . . . . . 22 五、 压力铸造常规工艺的确定 . . . . . . . . . . . . . . . . . . . . . . . . . . . . . . . . . . . . . . . . . . . . . . . . . 23 1、 压力 . . . . . . . . . . . . . . . . . . . . . . . . . . . . . . . . . . . . . . . . . . . . . . . . . . . . . . . . . . . . . . . . 23 2、 速度 . . . . . . . . . . . . . . . . . . . . . . . . . . . . . . . . . . . . . . . . . . . . . . . . . . . . . . . . . . . . . . . . 23 3、 温度 . . . . . . . . . . . . . . . . . . . . . . . . . . . . . . . . . . . . . . . . . . . . . . . . . . . . . . . . . . . . . . . . 23 4、 时间 . . . . . . . . . . . . . . . . . . . . . . . . . . . . . . . . . . . . . . . . . . . . . . . . . . . . . . . . . . . . . . . . 24 5、 涂料 . . . . . . . . . . . . . . . . . . . . . . . . . . . . . . . . . . . . . . . . . . . . . . . . . . . . . . . . . . . . . . . . 25 6、 端盖铸造工艺卡片 . . . . . . . . . . . . . . . . . . . . . . . . . . . . . . . . . . . . . . . . . . . . . . . . . . . . 25 六、 熔炼工艺 . . . . . . . . . . . . . . . . . . . . . . . . . . . . . . . . . . . . . . . . . . . . . . . . . . . . . . . . . . . . . . . 26 1、 合金的选用 . . . . . . . . . . . . . . . . . . . . . . . . . . . . . . . . . . . . . . . . . . . . . . . . . . . . . . . . . . 26 2、 熔炼方法的选用 . . . . . . . . . . . . . . . . . . . . . . . . . . . . . . . . . . . . . . . . . . . . . . . . . . . . . . 27 3、 配料计算 . . . . . . . . . . . . . . . . . . . . . . . . . . . . . . . . . . . . . . . . . . . . . . . . . . . . . . . . . . . . 28 4、 熔炼 . . . . . . . . . . . . . . . . . . . . . . . . . . . . . . . . . . . . . . . . . . . . . . . . . . . . . . . . . . . . . . . . 29 5、 浇注 . . . . . . . . . . . . . . . . . . . . . . . . . . . . . . . . . . . . . . . . . . . . . . . . . . . . . . . . . . . . . . . . 33 6、 清理与检验 . . . . . . . . . . . . . . . . . . . . . . . . . . . . . . . . . . . . . . . . . . . . . . . . . . . . . . . . . . 35 参考文献 . . . . . . . . . . . . . . . . . . . . . . . . . . . . . . . . . . . . . . . . . . . . . . . . . . . . . . . . . . . . . . . . . . . 37 致 谢 . . . . . . . . . . . . . . . . . . . . . . . . . . . . . . . . . . . . . . . . . . . . . . . . . . . . . . . . . . . . . . . . . . . . . 38 1一、 前言 1、 压铸的基本概念 压铸是将熔融状态或半熔融状态合金浇入压铸机的压室, 在高压力的作用下,以极高的速度充填在压铸模(压铸型) 的型腔内, 并在高压下使熔融合金冷却凝固而形成的高效益、 高效率的精密铸造方法。 2、 压铸生产的特点及应用范围 (1) 压铸有如下的优点: 1) 铸件的尺寸精度和表面粗糙度要求很高 2) 铸件的强度和表面硬度较高 3) 可以压铸形状复杂的薄壁铸件 4) 生产率极高 5) 可省略装配操作和简化制造工序 (2) 压铸的应用范围 压铸是近代金属加工工艺中发展较快的一种高效率、 少无切削的金属成形精密铸造方法。 目前, 压铸广泛应用于制造非铁合金的压铸件。 由于压铸工艺的特点, 故使用的合金是结晶温度范围小、 热裂倾向小以及收缩系数小的压铸铝、 镁、 及部铜的合金。 在非铁合金的压铸中, 铝合金所占比例(约30%~60%) 。 3、 铝合金压铸业的发展及现状 压力铸造工艺的诸多特点, 使其在提高有色金属合金铸件的精度水平、 生产效率、 表面质量等方面显示出了巨大优势。 随着汽车、 摩托车等工业的发展, 以及提高压铸件质量、节省能耗、 降低污染等设计要求的实现, 有色金属合金压铸件、 特别是轻合金(铝及铝合金) 压铸件的应用范围在快速扩张。 有资料表明: 工业发达国家用铝合金及铝合金铸件代替钢铁铸件正在成为重要的发展趋势。 目前压铸已成为汽车用铝合金成形过程中应用广泛的工艺之一, 在各种汽车成型工艺方法中占 49%。 2二、 压铸件工艺性分析及设计 压铸件工艺设计是压铸型设计前必须做的工作, 此时应大致确定所使用的压铸机、 合适的压射压力和压射速度。 与此同时, 应地设计铸件的分型面、 浇注排气系统, 因为其对压铸件的生产和质量具有决定性的作用。 1、 零件图 图 2-1 为端盖零件图, 材料为 ZALSi12, 合金代号为 ZL102。 其作为承载件广泛应用于于大中型汽车配件。 图 2-1 端盖 32、 工艺性分析 由图2-1知端盖压铸件的小壁厚为2mm, 符合压铸铝合金压铸出的小壁厚0.7mm。铸造圆角R4.5均符合工艺要求。 该零件结构比较简单, 但在侧面有一圆柱孔, 因此, 压铸时要采用抽芯机构抽芯。 铸件壁厚基本均匀。 该零件全部尺寸均为标注公差。 按图中要求, 其公差按IT12级, 用压铸方法生产该零件完全能达到尺寸要求。 压铸材料为ZL102, 为压铸铝合金。 可以用作该零件的材料。 由查表知, 其平均收缩率为0.7%。 因此, 端盖符合压铸工艺要求。 初步确定选用卧式冷压室压铸机生产该铸件。 3、 分型面的选择 该铸件零件较复杂, 但形状较规范, 没有凸缘之类不便出模的部位, 分型面的布置使得铸件成型的型腔部位全部处于定模内。 该铸件只需用单分型面即可, 在单分型面上,考虑到零件较复杂, 不可能采用简单的直线分型面, 只能部分采用直线分型面, 部分采用曲线分型面。 该铸件一侧有轴孔, 此处采用抽芯机构; 外部轮廓较平整, 没有不易出模部分; 内部结构也较为简单, 采取一定的拔模角有利于脱模; 铸件冷却时收缩, 与内部接触的镶块受到包紧力要大于外部接触镶块, 所以分型面的布置要使得铸件成型的型腔部位全部处于定模内, 这样才能保证开模时铸件随动模移动方向移出定模。 通过综合考虑压铸模具分型面的设计要点, 选用部分直线分型面和部分曲线分型面,考虑到要有利于浇注系统和溢流系统的布置, 不影响铸件的精度, 开模时保持铸件随动模移动方向脱出定模, 决定选择铸件的 A 面也就是外表面为分型面, 可得到符合技术要求的铸件, 且操作方便, 分型面如图 2-2所示。 图 2-2分型面的位置 AA 43、 浇注系统的选择及设计 根据铝、 镁合金的浇注系统的特点及应用, 通过对比本设计选用底注式浇注系统, 其结构见图 2-3 所示。 其优点为: 合金液自下而上平稳的充填铸型, 充型效果好, 但不利于自下而上地定向凝固, 当铸件较高时, 可在冒口部分设置补充浇道或直接在冒口补浇, 以提高冒口的补缩作用。 (1) 直浇道的设计 在卧式冷压室压铸机的浇注系统中没有直浇道, 压射余料兼起直浇道的作用。 (2) 内浇口的设计 内浇口的设计主要是确定内浇口的位置、 形状和尺寸。 由于铸件的形状复杂多样, 涉及的因素很多, 设计时难以完全满足应遵循的原则, 内浇口的截面积目前尚无切实可行的计算方法, 因此进行内浇口的设计是, 经验是很重要的因素。 1) 充型速度和充填时间 考虑到该铸件的力学性能, 如抗拉强度和致密度要求较高, 根据表2-1 可以确定该铝合金压铸件充型速度为40m/s。 该铸件的平均壁厚为 3mm, 从表 2-2可以确定其充填时间为0. 05s。 1-直浇道; 2-横浇道、 3-内浇图 2-3 卧室压铸机用底注式浇注系统结构 5表2-1 充填速度推荐值 合金种类 铝合金 锌合金 铝合金 黄铜 充填速度/ (m/s) 20~60 30~50 40~90 20~50表2-2 充填时间推荐值 铸件平均壁厚 b/m型腔充填时间/ s铸件平均壁厚 b/m 型腔充填时间/ s 1. 5 0. 01~0. 03 3. 0 0. 05~0. 10 1. 8 0. 02~0. 04 3. 8 0. 05~0. 12 2. 0 0. 02~0. 06 5. 0 0. 06~0. 20 2. 3 0. 03~0. 07 6. 4 0. 08~0. 30 2. 5 0. 04~0. 09 2) 内浇口截面积的计算 内浇口截面积可通过流量计算法的下列公式得 Ag=G/ Vgt (2-1) 式中 Ag内浇口截面积(mm2) ; G通过内浇口的金属液质量(g) ; 液态金属的密度(g/ cm3) , 见表23; Vg充填速度(m/ s) , 见表21 t型腔的充填时间(s) , 见表22。 表2-3 液态金属的密度值 合金种类 铅合金 锌合金 铝合金 镁合金 铜合金 / (g/ ㎝3) 8~10 6. 4 2. 4 1. 65 7. 5 Ag=90g/2. 4×40×0. 05 =18. 75(mm内浇口的厚度参照经验数据内浇口厚度选1mm 内浇口宽度的经验数据 0. 48×64=30 mm 2) (3) 横浇道的设计 横浇道的结构形式, 主要取决于铸件的结构形式和尺寸大小, 内浇口的位置、 方向和流入口的宽度, 内浇口的结构以及型腔的分布状况等因素。 本文采用了分叉喇叭形扇形横浇道与闭合喇叭形扇形横浇道进行比较分析。 横浇道的截面形状, 根据铸件的结构特点而 6定, 一般以扁梯形为主, 特殊情况下, 采用双边梯形、 长梯形、 窄梯形、 圆形式半圆形。本文采用扁梯形。 扁梯形具有金属液热损失少, 模具型腔加工方便的特点。 1) 横浇道尺寸的选择 本文采用两种不同的喇叭形横浇道, 两种横浇道基本尺寸是一样的, 比如扇形浇道入口处截面积、 与内浇口连接处的截面积等, 只是形状上不同。 扇形浇道入口处的面积可如以下经验公式求得: Ar =( 1. 2-2. 0) Ag (2-2) 式中 Ar 扇形浇道入口处截面积(mm2) ; Ag 内浇口面积(mm2) 为了 避免金属液在流动过程中产生涡流, 一般采用收敛界面的形式, 取Ar与Ag的比例系数为1. 5, 所以Ar=1. 5×Ag=30mm2。 横浇道与内浇口接触处的宽度就是内浇口的宽度Wg=30mm。 横浇道的长度 L 要求大于内浇口的宽度Wg=30mm, 取L与Wg的比例系数为1. 34, 所以 L=1. 34×Wg=40mm 横浇道的深度可按以下经验公式求得: D=(5-8) T(卧室冷压室压铸机) (2-3) 式中 D横浇道深度(mm) T内浇口厚度(mm) 带入数据D=8×1=8mm 横浇道的宽度可按一下经验公式求得: W=Dtan+ Ar/D (2-4) 式中 W横浇道的宽度(mm) D横浇道的深度(mm) 脱模斜度( ) 带入数据有 W=30mm 2) 横浇道与内浇浇口和铸件之间的连接方式 横浇道与内浇口 和铸件之间的连接方式采用铸件横浇道和内浇口均设置在同一模面。 横浇道的截面形状及尺寸见图2-4 图2-4横浇道截面形状及尺寸 74、 铸造工艺图 铸造工艺图见图 2-5 图2-5 铸造工艺图 8三、 压铸机的选用 根据压铸件的结构、 材质、 技术要求及验收条件等采用合理的压铸工艺, 设计、 制造优良的压铸模并合理选用压铸机, 是生产合乎要求的优质压铸件的前提。 压铸机通常按压室的受热条件不同, 分为冷压室压铸机和热压室压铸机两大类, 又分卧式、 立式两种形式。 卧式应用多。 根据该铸件的结构及对压铸机的对比, 本设计选用卧式冷室压铸机, 其常用于压铸铝、 镁、 铜合金。 1、 确定比压 比压是确保压铸件质量的重要参数, 根据合金种类并按铸件特征及要求选择, 如表 3-1所示 表 3-1 压实压力推荐值(单位: MPa) 锌合金 铝合金 镁合金 铜合金 一般件 13~20 30~50 30~50 40~50 承载件 20~30 50~80 50~80 50~80 耐气密性件或大平面薄壁件 25~40 80~120 80~100 60~100 电镀件 20~30 该铸件为承载件, 所以压实压力选60。 2、 确定压铸机的锁模力 根据铸件结构特点、 合金及技术要求选用合适的比压, 结合模具结构的考虑, 估算的投影面积, 按公式(3-1) 求得胀型力后乘以安全系数 K, 便得到压铸该压铸件所需压铸机的锁模力: F 锁>k(F 主+F 分) (3-1) 式中 F 锁压铸机的锁模力(kN); F 主主胀型力(kN); F 分分胀型力 (kN); K 安全系数(一般取 k=1. 25) 主胀型力的确定: F 主=Ap/10 (3-2) =475kN 式中 F 主主胀型力(kN); A铸件在分型面上的投影面积, 多腔模则为各腔投影面之和, 一般另加 30%作为浇注系统与溢流排气系统的面积(cmp压实压力(MPa) 。 因本文模具的侧向活动型芯成型面积不大, 分胀型力忽略不计, 所以 F 锁>k*F 主=600 kN。 2) ; 93、 确定压铸机型号 为简化选用压铸机时的计算, 在已知模具分型面上压铸件总投影面积和所选比压后,可以从图 3-1 中直接查到所选用的压铸机的型号和压室直径。 考虑到实际模具的尺寸, 所以选用比计算求得的压铸机型号稍大一些的压铸机, 这样对实现压铸件的生产有较高的通用性。 再由图中可知选用 J116E 型卧式冷式压铸机合适。考虑到铸件体积较小, 选用压室直径为 40mm。 4、 压铸机部分性能指标校核 (1) 金属浇注量校核 J116E 型卧式冷室压铸机的铝金属浇注量为 0. 5kg, J116E 型卧式冷室压铸机的铝合金浇注量远远大于压铸件的质量 90g, 故满足要求。 (2) 压铸机投影面积校核 J116E 型卧式冷室压铸机的铸件投影面积为 67~110cm79cm2, 大于压铸件的投影面积2, 此项指标亦满足要求。 (3) 压铸机合模力的校核 J116E 型卧式冷室压铸机的合型力为 630kN, 大于压铸件所需的锁模力 600kN, 此项指标满足要求。 图 3-1 国产压铸机比压投影面积对照图 10四、 压铸型设计 压铸型主要由型架部分、 成形部分、 抽芯机构、 顶出铸件机构、 排溢系统、 导向零件组成, 本设计生产该铸件的压铸型结构总图见4-1。 模架设计首先根据成型零件的尺寸,直接从标准模架库中调用, 再根据具体的要求尺寸对每个模架中的零件进行进一步的设计, 设计后的零件还是继承原零件的装配特征。 辅助结构设计主要包括抽芯机构和推出机构。 压铸模具的每个部分都相互关联, 设计合理的配合是保证加工合格模具的关键。 该铸型的压铸过程为: 在铸型合拢锁紧后, 用浇勺经注口把合金液倒入横卧的压室中。压室的左端部分设在定型之中。 压室活塞向左移动, 把金属液压入压铸型。 动型左移, 打开铸型, 形成的铸件连同余料一起随动型左移, 完成一个压铸循环。 1、 成型零件的设计 成型零件主要是指型芯和镶块。 成型零件部分要承受高温、 高速金属液的冲击, 要求成型零件具有较高的耐蚀、 耐热、 抗疲劳断裂能力, 所以成型零件材质选用3Cr2W8V。 图4-1 压铸型结构总图 11(1) 镶块的设计 镶块的是型腔的基体。 在一般情况下凡金属液冲刷或流经的部位均采用热作模具钢制成, 以提高模具的使用寿命。 在成型加工结束经热处理后镶入套板中。 成型零件的结构形式分为整体式和镶拼式。 根据压铸件的结构特点, 镶块采用一摸一腔、 浇口与型腔一体、 一侧抽芯、 拔模角为1゜的矩形镶拼式结构。 镶拼式结构模具具有简化加工工艺, 提高模具制造质量, 容易满足组合镶块成形部位的精度要求; 合理使用热作模具钢, 降低成本; 易损件有利于更换和修理; 压铸件的局部结构改变时, 不至于整套模具报废; 拼合处的适当间隙有利于排除型腔内的气体; 采用合理的镶块结构可以减少热处理时的变形, 也便于在热处理后进行修理; 镶块的坯料比较容易锻造, 组织均匀, 质量较高的特点。 镶块装入模具的套板中加以固定, 构成动、 定模型腔, 其安装形式可分为不通孔和通孔两种。 本设计中采用通孔式。 对通孔的套板, 用台阶固定, 在动、 定模上镶块的安装孔尺寸和大小都应该一致, 容易保证同轴度。 定模镶块的结构和尺寸如图4-2所示。 动模镶块的结构及尺寸见图4-3所示。 图4-2 定模镶块的结构及尺寸 12 (2) 型芯的设计 型芯的形状取决于零件和镶块的结构。 根据零件和镶块的结构, 参考文献[4] 中的表6-25推荐尺寸, 本课题模具的型芯采用圆型型芯。 该模具的侧型芯见图4-4所示。 图4-4 侧型芯图4-3 动模镶块的结构及尺寸 132、 模架的设计及具体尺寸的确定 模架设计是根据成型零件的尺寸, 直接从标准模架库中调用, 再根据具体的尺寸进行结构的设计。 首先确定各个零件的主要尺寸。 (1) 套板的设计 套板一般受到拉伸、 弯曲、离心铸造 压缩三种应力, 变形后会影响型腔的尺寸精度。 因此, 在考虑套板尺寸时, 应兼顾模具结构与压铸生产中的工艺因素。 套板的边框厚度可由下式(4-1) 计算得出: (4-1) 式中 h套板边框厚度(mm); H 、 H1、 L1、 L2按铸件大小确定; P1、 P2边框侧面承受的总压力(N); [ ]钢材的许用弯曲强度(Mpa); p 压射比压(Mpa) 根据动、 定模镶块的厚度, 确定动、 定模套板的厚度分别为40mm和40mm, 满足上式的条件。 定模和动模套板加工后的边框尺寸根据镶块的尺寸和文献[4] 中表6-54推荐尺寸确定。 设计后的动、 定模套板长、 宽均为200mm。 (2) 支撑板的设计 动模支撑板厚度h可按公式(4-2) 计算。 h][2BPL (4-2) 式中 P 动模支撑板所受总压力(N) B 动模支撑板长度(mm); L 垫块间距(mm); [ ]钢材的许用弯曲强度(Mpa) 动模支撑板所受总压力等于压铸件在分型面上的投影面积与压射比压的乘积。 结合压铸件的尺寸和动模套板的尺寸求得: 支撑板的厚度为40mm, 支撑板的长、 宽均为200mm。 14(3) 座板的设计 1) 定模座板的设计 定模座板一般不作强度计算, 设计时主要考虑两点: 一是定模座板上要留出紧固螺钉或安装压板的位置, 借此使定模固定在压铸机定模安装板上; 二是浇口安装孔的位置与尺寸要与所用压铸机配合。 根据J116E型卧式冷室压铸机模板的尺寸为420×420(mm×mm) , 小尺寸为200× 200(mm× mm) , 结合定模座板的推荐尺寸, 确定定模座板的长、 宽分别为200mm、 200mm, 厚度为40mm。 2) 动模座板的设计 动模座板的尺寸与支撑板的投影面相同, 厚度不同, 有强度的要求。 动模座板的长、 宽分别为315mm、 200mm, 厚度 40mm。 (4) 导柱与导套的设计 导柱导套应具有一定的刚度, 以引导动模按一定的方向移动, 保证动定模在安装和合模时的正确位置。 在合模过程中应保持导柱导套首先起定向作用, 防止型腔型芯错位。 导柱导套需要有足够的刚性, 当导柱为四根, 一般都布置在模板的四个角上, 保持导柱之间有开档尺寸, 便于取出铸件。 选取导柱导滑段直径的经 验公式为: D= K F (4-3) 式中 D导柱导滑段直径(cm); F 模具分型面上的表面积(cm2); K 比例系数, 一般取0. 07~0. 09 (5) 基本模架的确定 根据已经确定模架中的各个零件, 从而在标准模架库中选用模架, 模架在总装图中的形状见图4-1。 模架中的各个零件和确定零件是对应, 零件的主要尺寸参照表4-5设计而定。 15表4-1 压铸模模架尺寸参考系列 主要尺寸 W L A B C D F 200 200 315 定模座板 定模套板 动模套板 支撑板 动模座板 25 25-160 25-160 35 25 垫块 W1 32 E W2 G W3 H 63-100 125 20 125 12 12 20 28 12 6XM10 6XM10 M8 推板 推杆固定板 复位杆直径 导柱导套 导向段直径 固定段直径 推板导柱 导向段直径 定模套板螺钉 动模套板螺钉 推板螺钉 (6) 模架具体尺寸的确定 模架设计主要是对已选用的基础模架, 根据抽芯机构和推出机构的具体尺寸以及对模架各个零件上孔类尺寸的要求, 确定模具零件终的尺寸。 定模座板根据所选压铸机的型号, 确定U型槽和浇口安装孔的位置和尺寸。 螺栓孔的数量、 位置及尺寸根据计算得出;动模座板根据压铸机型号确U型槽、 顶出杆孔的位置和尺寸螺栓孔的数量、 位置及尺寸根据计算得出。 定、 动模套板的导套孔和螺栓孔的尺寸、 位置由计算得出, 同时根据抽芯机构的尺寸确定动、 定模套板结构及尺寸如图4-11、 4-12所示。 支撑板的导柱孔的尺寸由计算得出, 位置根据推出机构确定; 推杆孔根据压铸件的 形状来定; 螺栓孔的位置、 尺寸与动模套板相对应。离心铸造 套板导柱采用半圆形润滑槽导柱。 套板导柱、 套板导套的尺寸由计算和动、 定模套板的尺寸共同确定。 16 图4-11 动模套板图4-12 定模套板 173、 抽芯机构的设计 抽芯机构的设计根据该铸件的结构特点, 模具应设有抽芯机构, 本文采用斜销式抽芯机构。 抽芯机构中的各个零件属于滑动配合件, 选用 T10A 为材料。 (1) 抽芯力 压铸时, 金属液充填型腔, 冷凝收缩后, 对被金属包围的型芯产生包紧力抽芯机构运动时有各种阻力即抽芯阻力, 两者的和即为抽芯开始瞬时所需的抽芯力。 继续抽时, 只需克服抽芯阻力。 抽芯力的查用图 按公式取挤压应力和摩擦系数的较大值作出锌、 铝、 铜合金压铸时的抽芯力查用图 (见图4-6) , 以简化设计时的计算。 1) 按图 4-6, 型芯直径为10mm, 查得型芯长度为10mm时, 铝合金压铸时的抽芯力为 0. 8KN即800N 2) 以查得数乘以成形长度得出: F=(800×500) N=2000N=2KN (2) 确定抽芯距离 1) 计算抽芯距离 抽芯后活动型芯应完全脱离铸件的成形表面, 并便铸件能顺利推出型腔。 抽芯距离的图4-6 抽芯力查用 18计算如下: S抽= S移十 K (4-4) 式中 S抽─抽芯距离(mm) ; S移─滑块型芯完全脱出成形处的移动距离(mm) ; K─安全值。 安全值 K按抽芯距离长短及抽芯机构选定(表4-2) . 各种侧向成形孔, 侧凹抽芯距离 S抽按下式 S抽 = h + K (4-5) 式中 h─抽芯处铸件壁厚或成形深度 (mm) ; K─安全值 (查表4-2) 。 对于同一滑块上抽出多个型芯时, 应取成形深度 h 表4-2 常用抽芯距离的安全值K (单位mm) S 移 抽芯机构 斜销、 弯销、 手动 齿轴齿条 斜 滑 块 液 压 10 3~5 5~10(取整齿) 2~3 ─ 10~30 3~5 30~80 5~8 80~l80 ─ 8~l0 180~ 360 8~l2 10~l5 15 注: 1. 所抽拔的型芯直径大于成型深度时, 安全值 K应接直径尺寸查取。 2. 同一抽芯滑块上有许多型芯时, 安全值 K应按型芯间距查取。 由于该铸件为侧向成形孔, 侧抽芯距离 S 抽按式(4-5) 计算 对于同一滑块上抽出多个型芯时, 应取成形深度 h 已知该铸件 h=25mm 所以 S 抽=25mm+5mm=30mm (4) 斜销的设计 斜销的形状及尺寸如图 4-7 所示 图 4-7 斜销 191) 斜销直径的估算 抽芯机构选用 T 型滑块结构。 斜销所受的力, 主要取决于抽芯时作用于斜销上的弯曲力, 斜销直径 d 的估算由公式(4-6)得到。 d 3cos3000ahF弯 (4-6) 式中 d斜销直径; F 弯斜销承受的弯曲力(10N) 。 许用抗弯强度取 300MPa; h滑块端面至受力点的垂直距离(cm) ; 斜销斜角 根据公式和推荐尺寸斜销直径取 d=12mm 2) 斜销长度的确定 斜销长度的计算是根据抽芯距离 S 抽、 固定端模套厚度 H、 斜销直径 d 以及所采用的斜角 的大小而定。 斜销总长度 L 的计算如公式(4-7) 所示。 L=L1+L2+L3 (4-7) 式中 L1斜销固定端尺寸(mm) ; L2斜销开作段尺寸(mm) ; L3斜销工作导引段尺寸(一般取 5~10 mm) 查表并计算得到斜销长度为 L=147mm。 4、 推出机构的设计 考虑到推杆推出方式的优点, 本文设计中推出机构选用推杆推出方式推出机构一般由推出元件(如推杆、 推管、 卸料板、 成型推块、 斜滑块等) 、 复位元件、 限位元件、 导向元件和结构元件等组成。 (1)、 推板及推杆固定板的设计推板的厚度按下式计算: (4-8) 式中 H推板厚度(cm); P推板负荷(N); C推杆孔在推板上分布的跨距(cm); B推板宽度(cm); K系数 推板与推杆固定板的标准尺寸参考文献[4]中表(6-50) , 推板与推杆固定板的厚度参考表(6-51) 中的推荐尺寸。 推板的长、 宽、 厚分别为 200mm、 150mm、 20mm; 推杆固定板 20的长、 宽、 厚分别为 240mm、 180mm、 16mm。 (2)、 推杆的设计 若每根推杆上的推出力超出压铸件被推出部位所能承受的许用应力, 推杆就会顶入压铸件内部, 顶坏压铸件。 推杆尺寸及形状见图6-8所示, 推杆的截面积可按公式(6-9) 计算。 又因为推杆均为细长的杆件, 因此还必须校核推杆的稳定性。 选择推杆的规格(直径)和数量, 主要依据是压铸件对模具的包紧力, 从而确定其作用在推杆端面的推力大小。 推杆截面积计算如下: A=][nF推 (4-9) 式中 A推杆推出段端部截面积(mm2); F推推杆承受的总推力(10N); n推杆数量; [ ]压铸件的许用强度(105Pa) 其中推杆的数量设计中考虑到铸件的形状特征定为4个。 推杆属于滑动配合件零件,所以材质选用T10A。 推杆的配合及参数见参考文献[4]《压铸模具设计手册》, 推杆与孔的配合精度为H7/e8。 (3)、 推板导柱与导套的设计 引导推板带动推出元件作往复运动的导柱通常称作推板导柱以区别定模套板上的导柱。 推板导柱和推板导套配合使用, 以减少滑动摩擦。 将推板导柱安装在动模套板上与动 模支撑板采用间隙配合。 或不伸入到支撑板内, 可以避免或减少因支撑板与推板温度差造 成热膨胀不一致的影响。 推出机构由推出元件、 复位元件、 限为元件等构成。 推板导柱和导套的主要尺寸参考文献[4]中表 6-5 和表 6-6, 其中导滑段长度 100mm,直径 20 mm, 固定端直径 12 mm。 二者形状及具体尺寸如图 4-9 和图 4-10 所示。 图4-8 推杆 21 5、 排溢系统的设计 压力铸造金属液充型时要求型腔中的气体和混有较多气泡和氧化碎渣的金属液排出型腔之外, 以保证铸件的内部质量, 故需在压型上设置排溢系统。 (1) 压铸型的排气 压铸型的排气可利用分型面的间隙、 各零件间的配合间隙排气, 由于该铸件体积较小,结构相对简单, 所以该铸型利用型芯与镶块的配合间隙、 顶杆与动模镶块的配合间隙排气。 (2) 压铸型的溢流槽 溢流槽时压铸型排溢系统中的溢流原件, 它设置在铸型一个半型(动型或顶型) 的分型面上, 沿型腔的边缘, 与型腔之间有溢流口相连。 该压型的溢流槽设置在动模镶块与铸件之间的分型面上。 图4-9 推板导柱 图4-10 推板导套 226、 压铸模具的校核 为了机器合模时能锁紧模具分型面, 开模后能方便地从分型面间取出铸 件, 需要对模具厚度和动模座板行程进行核算。 (1) 模具厚度校核 根据分型面在合模时必须贴紧的要求, 所设计的模具厚度, 不得小于机器说明书所给定的小模具厚度, 也不得大于所给定的模具厚度。 据此, 设计模具时, 按公式 (4-10)核算所设计的模具厚度 H min + 10 H设 Hmax-10 (4-10) 式中 H设设计模具厚度(mm) ; Hmin说明书中所给定的模具小厚度(mm) ; Hmax说明书中所给定的模具厚度(mm) 根据设计可知: H min =200 mm, Hmax=500 mm, 模具厚度则为定模套板、 定模座板、 动模套板、 支承板、 垫块以及动模座板的厚度之和, 即: H 设=70+30+40+30+90+30=290 mm 可见 H 设满足公式(4-10), 故设计中模具厚度符合要求。 (2) 动模座板行程核算 动模座板行程实际上就是压铸机开模后, 模具分型面之间的距离, 即压铸机型号所规定的动模座板行程。 设计模具时, 根据 压铸件的形状、 浇注系统和模具结构来核算是否满足取出铸件的要求, 具体见公式(4-11) L取 L行 (4-11) 式中 L取开模后分型面之间能取出铸件的小距离(mm); L行动模座板行程(mm), L行=350 mm 对于推杆推出机构 L取 L芯+L件+K (4-12) 式中 L芯型芯高出分型面尺寸(mm); L件包括浇注系统的铸件高度(mm); K 安全值(取10mm) 故 L 取=L 芯+L 件+K=24+34+10=68 mm, L 取L 行, 满足要求。 通过以上对模具厚度及动模座板行程的校核, 可以看出均满足模具结构要求, 加上对压铸机性能指标的校核, 可以得出: 所设计压铸模具结构合理, 满足。 23五、 压力铸造常规工艺的确定 正常生产过程中, 技术人员必须确定压铸时所采用的压铸压力, 金属经过内浇口进入型腔时的压铸线速度, 压铸时被压射金属的温度, 压射时压铸型的工作温度, 压射后铸件在型中的停留时间和为顺利自铸型中取出铸件所使用的压铸型涂料, 这些工艺因素是压铸每个铸件时都必须考虑的, 因此把它们称为常规工艺因素。 1、 压力 压力是使压铸件获得组织致密和轮廓清晰的重要因素, 又是压铸区别于其他铸造方法的主要特征, 其大小取决于压铸机的结构及功率。 在压铸中, 压力的表示形式有压射力和压射比压两种。 压射比压是液态金属在充填过程中各阶段实际得到的作用力大小的表示方法, 反映了液态金属在充填时的各个阶段以及金属液流经各个不同截面时的力的概念。 为了提高铸件的致密度,离心铸造 提高压射比压无疑是有效的。 但是,离心铸造 过高的压射比压会使铸型受到金属液的冲刷和增加粘模的可能性, 降低铸型的使用寿命。 压射比压过低会导致铸件组织不致密和轮廓不清晰。 因此, 应根据不同合金和不同结构特点的铸件选择合适的压射比压。 常用的压射比压为13~120MPa。 现有压铸机上改变压射比压的方法有两种: 调节压铸机压射力的大小和更换不同直径的压室。 2、 速度 压铸中速度的表示形式有压射速度和充填速度两种。 压力与速度对压铸件的内在质量、 表面质量及轮廓清晰度起着重要的作用。 充填速度的高低直接影响铸件的内部或外部质量。 充填速度的选择应视铸件大小、 铸件复杂程度、 铸件的要求、 合金种类、 压射比压高低而异。 对于简单厚壁或内部质量要求较高的铸件, 应选择低充填速度, 高比压, 大浇口; 而对于薄壁复杂或表面质量要求高的铸件, 应选择高充填速度, 高比压, 因为这时铸件成形是主要矛盾。 常用的充填速度为20~90m/ s。 3、 温度 金属液的浇注温度和模具的工作温度是压铸过程中的热因素。 为保证良好的充填条件, 控制和保持热因素的稳定性, 则要有一个相应的温度规范。 各种压铸合金的浇注温度, 随压铸件壁厚和结构的复杂程度而不同, 可参考下表选用。 24表5-1 合金的浇注温度 (℃) 合金 铸件壁厚3㎜ 结构复杂 420~440 铸件壁厚3㎜ 结构复杂 410~430 结构简单 结构简单 锌合金 430~450 420~440 铝合金 含硅 含铜 含铝 610~650 620~650 640~680 640~700 640~720 660~700 590~630 600~640 620~660 610~650 620~650 640~680 铝合金 普通黄铜 硅黄铜 640~680 660~700 620~660 640~80 铜合金 870~920 900~940 900~950 930~970 850~900 880~920 870~920 900~940 值得指出的是, 充填速度越大, 液态金属因摩擦作用而升温的数值越大, 当充填速度为40m/ s时, 铝合金进入型腔时的温度将增加8℃, 因此充填速度大时, 可适当降低浇注温度, 以保证铸件质量。 表 5-2 压铸模工作温度一般可按下式计算或根据下表查得。 (℃) 合金 铸件壁厚3㎜ 结构复杂 150~200 铸件壁厚3㎜ 结构复杂 120~150 结构简单 130~180 结构简单 110~140 锌合金 预热温度 连续工作保持温度 180~200 190~220 140~170 150~200 铝合金 预热温度 连续工作保持温度 150~180 180~200 200~230 250~280 120~150 150~180 150~180 180~200 铝铝合金 预热温度 连续工作保持温度 170~190 200~220 220~240 260~280 150~170 180~200 170~190 200~240 铝合金 预热温度 连续工作保持温度 150~180 180~240 200~230 230~280 120~150 150~180 150~180 180~220 铜合金 预热温度 连续工作保持温度 200~230 300~325 230~250 325~350 170~200 250~300 200~230 300~350 4、 时间 压铸时间包含充填、 持压及压铸件在压铸模中停留的时间。 它是压力、 速度、 温度这三个因素, 再加上液态金属的物理特性、 铸件结构(特别是壁厚) 、 模具结构(特别是浇注系统和排溢系统) 等各方面的综合结果。 压铸时液态金属从进入压铸模型腔开始到充满型腔为止所需的时间, 称为充填时间。充填时间大多在O. 01~0. 2s之间。 充填时间的长短取决于铸件的体积大小和复杂程度。 对大而简单的铸件, 充填时间要相对长些; 对复杂和薄壁铸件, 充填时间要短些。 实践证明,中小型铝合金压铸件的充填时间为0. 1s左右。 充填时间的调节方法与充填速度的调节方法相似。 持压时间的长短取决于铸件的材质和壁厚。 对熔点高、 结晶温度范围大和厚壁的铸件,持压时间要长些。 对结晶温度范围小而壁又薄的铸件, 持压时间可短些。 若持压时间不足,易造成缩松。 但持压时间过长, 起不到很大效果, 且易造成立式压铸机的切除余料困难。一般持压时间为l~2s, 对结晶温度范围大和厚壁的铸件, 持压时间为2~3S。 25铸件开裂, 同时也会降低压铸的生产率。 一般开型时间按每1㎜铸件壁厚为3s计算,然后经试压调整。 5、 涂料 压铸过程中, 为了避免铸件与压铸模焊合, 减少铸件顶出的摩擦阻力和避免压铸模过分受热而采用涂料。 压铸涂料指的是在压铸过程中, 使压铸模易磨损...
以上信息由江苏亚立特钢有限公司整理编辑,了解更多离心铸造信息请访问http://www.jsyltg.com