新闻中心
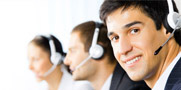
咨询热线:
134-0554-5577
邮件:874556408@qq.com
电话:0523-83984388
地址:江苏省兴化市沈伦镇工业园区沈北路
离心铸造⑤ 铸件应尽量避免机械加工
简述压力铸造技术_能源/化工_工程科技_专业资料。简述压力铸造技术 1.引言 1.1 压铸技术的起源 压铸技术早用于泥制青铜生活器具、钱币等,后来发展了金属型制简 单的武器,如青铜箭头。金属型的大量使用在印刷机械中出现制铅字以后,国 外在 1
简述压力铸造技术 1.引言 1.1 压铸技术的起源 压铸技术早用于泥制青铜生活器具、钱币等,后来发展了金属型制简 单的武器,如青铜箭头。金属型的大量使用在印刷机械中出现制铅字以后,国 外在 1872 年发明了世界上台简单的手动小型压铸机,并于 1920 年制造出 了冷室压铸机,1927 年发明了立式冷室压铸机。 1.2 我国压铸技术的发展 我国的压铸件工业化生产开始于 20 世纪 50 年代,那时靠仿制原捷克斯洛伐 克和前联生产的 500KN 和 1000KN 卧式冷室压铸机和进口他们的立式压铸机和卧 式冷室压铸机;发展到今天国现在的压铸机家可生产的 280000KN 卧式冷 室压铸机和 0KN 以下热室压铸机及 3150KN 以下立式冷室压铸机。 1.3 近几年国际压铸技术的发展 ⑴ 压铸计算机模拟技术分析压铸过程有了大的理论突破。 ⑵ 压铸机和辅助设方面有了很大的发展。 ⑶ 压铸产品检测方面,特别是部缺陷的无损检测:如 X 射线、荧 光、超声波探测等得到了发展。 ⑷ 压铸模具材料和寿命的发展。 ⑸ 快速成型设计及制造技术在压铸生产中得到应用。 ⑹ 压铸材料的发展,如镁合金及金属基复合材料。 ⑺ 压铸新技术的开发,如真空压铸、充氧压铸、局部加压压铸等 2.压铸特点和应用围 2.1 压铸工艺过程 压力铸造(简称压铸)是在高压作用下将液态或半液态金属快速压入铸型中, 并在压力下凝固而获得铸件的方法。 压铸所用的压力一般为 30~70MPa,充型速度可达 5~100m/s,充型时间为 0.05~0.2s。金属的压力铸造广泛用于汽车、冶金、机电、建材等行业。目前 90% 的镁铸件和 60%的铝铸件都采用压力铸造成型。 金属液在高压下以高速填充铸型,并在压力下冷却,是压铸区别于其他铸造 工艺的重要特征。 压力铸造的主要工序可分为:合型、压射、顶出三个阶段。压铸机的主要结 构简图如图 2-1 所示。 1 图 2-1 压铸机主要结构简图 1— 拉杆;2—合模座;3—动模座;4—定模座;5—压铸模 2.2 压铸的特点 (1)优点 ① 生产率高,压铸机没小时可压铸 50~150 次,甚至有的可达 500 次;便 于实现自动化或半自动化; ② 铸件的尺寸精度高,标准公差可达 IT8~11;表面粗糙度低,Ra=0.8~ 3.2,可直接铸造出螺纹; ③ 由于在压力下凝固,且速度快,因此,铸件晶粒细小、表面紧实、强度 和硬度高; ④ 便于采用镶铸法(嵌铸法)。 (2)缺点 ① 压铸时由于液态金属填充速度高,液态不稳定,故采用一般压铸法时, 铸件易产生气孔,不能进行热处理; ② 对凹复杂的铸件,压铸较为困难; ③ 高熔点合金(如铜,黑色金属),压铸型寿命较低; ④ 不宜小批量生产,其主要原因是压铸型制造成本高,压铸机生产效率高, 小批量生产不经济。 2.3 压铸应用围和注意点 ① 压铸是实现少无切削加工的精密铸造技术,在汽车、航空、仪表、 国防 等工业部门广泛用于非铁金属的小型、薄壁、形状复杂件的大批量生产。 ② 铸件壁厚均匀,以 3-4mm 的壁厚为宜,壁厚应小于 8mm,以防止缩 孔、缩松等缺陷。 ③ 铸件不宜进行热处理或在高温下工作,以免铸件气孔中的气体膨胀而导 致铸件变形或断裂。 ④ 由于部疏松,铸件塑性和韧性差,故它不适合于制造受冲击的零件。 ⑤ 铸件应尽量避免机械加工,以防部孔洞外漏。 1 3.压力铸造的种类 根据压力机的不同,压力铸造可分为冷室压铸和热室压铸两大类型。而按压 铸机压力传递方式可分为立式和卧式两种。冷室压铸机的压室与保温坩埚炉是分 开的,压铸时从保温坩埚中舀取金属液倒入压铸机上的压室后进行压射。而热室 压铸机的压室和保温坩埚连成一体。 3.1 卧式冷室压铸 卧式压铸机的压室和压射机构处于水平位置。其工作原理及过程如图 3-1 所示。 (c)压射室充满 (d)压射完毕 图 3-1 卧式冷室压铸机工作过程 整个过程经浇注,冲头前进、压射开始,压射室充满,压射完毕等工序。这 些过程又可分为慢速压射(封孔)、一级快速压射(填充)、二级快速压射、增压 等几个阶段。在压铸过程中,冲头所受的压力与速度变化如图 3-2 所示。多级压 射的主要目的是减少压铸过程中气体的卷入,提高压铸件的致密性和质量。 由 3-2 图可以看出在第Ⅰ阶段速度较慢,这个阶段主要是封孔阶段,除了封 住浇注孔外还可以将压室里的气体排出;该阶段的压力主要是抵抗压射冲头和压 实还有压射冲头和活塞之间的摩擦力。第Ⅱ阶段是一级快速压射阶段,该阶段主 要是填充阶段,速度较快,由于金属液还没有进入到型腔中,因此,该阶段压射 冲头压力仍较小,在这个阶段后期速度突然下降,而压力骤升,主要是由于金属 液在浇注口突然改变流动方向,冲头受金属液回流导致压力升高。第Ⅲ阶段为二 级快速压射阶段,该阶段主要是将金属液压入到型腔中,由于水锤作用,该阶段 压射冲头所受压力较大。第Ⅳ阶段为增压阶段,该阶段主要是压射正在凝固的金 属液,是形成的铸件晶粒细小,组织致密;这时压射冲头只做小位移移动。 1 图 3-2 压铸不同阶段压射冲头的压力与运动速度的变化 卧式冷室压铸广泛用于铝合金的压铸。其压铸过程示意图如图 3-3。 图 3-3 卧室压铸机压铸过程示意图 1— 浇道;2—型腔;3—金属液浇入口;4—金属液;5—压射冲头;6—动模;7—定模; 8—顶杆;9—铸件及涂料 3.1.1 卧式压铸优点: ①结构简单,操作程序少,生产效率高,易实现自动化; ②金属消耗少; ③能量损失少,使用更为广泛。 3.2 立式冷室压铸 立式冷室压铸机的压室和压射机构是处于垂直位置的。其压铸过程示意图 如图 3-4 所示。 由 3-4 图可以看出,和卧式冷室压铸的优点是立式冷室压铸多了一个返 料冲头。其工作原理为:开始阶段时,返料冲头 8 上升将喷嘴口 6 挡住,然后往 压射 2 中加入适量金属液,其后压射冲头 1 慢慢向下压入,同时返料冲头 8 下降, 1 这时金属液从喷嘴压入型腔 7,整个压射过程结束。待金属液凝固后压射冲头 1 上升,同时在液压驱动下返了冲头上升,并切断余料 9,送出压室。 图 3-4 立式压铸机压铸过程示意图 1—压射冲头;2—压室;3—金属液;4—定模;5—动模;6—喷嘴;7—型腔; 8—返料冲头;9—余料 3.2.1 立式压铸优点: ①有余料切断、顶出功能; ②空气不易随金属进入压室; ③金属液进入型腔经过转折,压力消耗大。 3.3 热室压铸 热室压铸的工作过程如图 3-5 所示。当压射冲头 3 上升时,金属液 1 通过进 口 5 进入压室 4,随着压射冲头下压, 液体金属沿着通道 6 经喷嘴 7 填充铸型 8;冷却后压射冲头回升,多余的液体 金属回流至压室中,然后打开铸型取出 铸件。 热室压铸机的特点是生产工序简 单、生产效率高、易实现自动化,金属 消耗少、工艺稳定、无氧化杂物、铸件 质量好;但由于压室和冲头长时间浸泡 在高温金属液中,影响使用寿命,常用 于锌合金压铸。 图 3-5 热室压铸机压铸过程示意图 1—金属液;2—坩埚;3—压射冲头;4—压室 5—进口;6—通道;7—喷嘴;8—铸模 1 图 3-6 热室压铸机结构示意图 1—金属液;2—坩埚;3—压射冲头;4—压射室;5—进口;6—通道;7—型腔; 8—返料冲头 3.4 压铸机的选择 实际生产中并不是每台压铸机都能满足压铸各种产品的需要,而必须根据具 体情况进行选用,一般应从下述两方面进行考虑: (1)按不同品种及批量选择 在组织多品种,小批量生产时,一般要选用液压系统简单,适应性强,能够 快速进行调整的压铸机,在组织少品种大量生产时,要选用配各种机械化和自动 化控制机构的高效率压铸机;对单一品种大量生产的铸件可选用专用压铸机。 (2)按铸件结构及工艺参数选择 铸件外形尺寸,重量,、壁厚等参数对选用压铸机有重要影响。铸件重量(包 括浇注系统和溢流槽)不应超过压铸机压定的额定容量,但也不能过小,以免造 成压铸机功串的浪费。一般压铸机的额定容量可查说明书。 压铸机都有一定的和小型距离,所以压型厚度和铸件高度要有 一定限度,如果压铸型厚度或铸件高度太大就可能取不出铸件。 4 压力铸造技术新发展 压铸件的主要缺陷是气孔和疏松,通常不能进行热处理。为了解决此问题, 目前主要有两个途径:一是改进现有设;二是发展特殊压铸工艺,如真空压铸, 充氧压铸等,下面逐一介绍。 4.1 真空压铸 为了减少或避免压铸过程中气体随金属液高速卷入而使得铸件产生气孔和 疏松,压铸前采用对铸型抽真空压铸为普遍。根据压室和型腔的真空度大小又 可将真空压铸分为普通真空压铸和高线) 普通真空压铸 即采用机械泵抽空压铸模腔的空气,建立真空后注入金属液的压铸方法该方 法。该方法是在动模座和动模座之间用一个密封的真空罩连接,然后通过机械泵 将整个真空罩中的气体抽出。线—抽气孔; 7—弹簧垫衬 (2)高真空压铸 高真空压铸的关键是能在很短的时间获得高线 为吸入式高真空压 铸机的工作原理图,它采用真空吸入金属液至压室,然后进行快速压射,可获得 较高的压铸线 吸入式高真空压铸机的工作原理图 高真空压铸的原理:压铸工作前,先从抽真空管将整个压室和型腔中的空气 抽出,这个抽真空过程速度一定要尽可能快,使得坩埚中的金属液和压室产生较 大的压力差,从而使得坩埚中的金属液体沿着升液管进入压室,接着压射冲头开 始向右进行压射。 4.1.1 真空压铸法的优点 ① 真空压铸法可以消除或减少压铸件部的气孔,提高压铸件的机械性能 和表面质量,改善镀覆性能; ② 真空压铸法大大减少型腔的反压力,可使用较低的比压及铸造性能较 1 差的合金,有可能用小机器压铸较大的铸件; ③ 可以改善填充条件,可压铸较薄铸件; 4.1.2 真空压铸法的缺点 ① 密封结构复杂,制造及安装困难; ② 真空压铸法若控制不当,压铸效果不明显。 4.2 充氧压铸 充氧压铸是将干燥的氧气充入压室和压铸 模型腔,以取代其中的空气和其他气体。充氧压 铸工艺原理图如图 4-3 所示。 充氧压铸仅适用于铝合金。当铝合金液体压 入压室和压铸模型腔时与氧气发生化合反应,生 成 AL2O3,形成均匀分布的 AL2O3 小颗粒(直径在 1um 以下),从而减少或消除了气孔,提高了铸 件的致密性。这些小颗粒分散在铸件中,约占总 质量的 0.1%-0.2%,不影响机械加工。 图 4-3 充氧压铸工艺原理 4.2.1 充氧压铸的特点 消除或减少了铸件部的气孔,强度提高了 10%、伸长率增加了 1.5-2 倍,铸 件可进行热处理;AL2O3 有防腐蚀作用,充氧压铸件可在 200-300℃的环境中工作; 与真空压铸相比,充氧压铸的结构简单、操作方便、投资少。 局限性: 1.必须使用润滑剂或固体粉末脱模; 2.氧气置换和除去水分的时间稍长; 3.铸造合金中 Fe 和 Mn 的含量要适当; 4.熔液和氧气完全反应下的铸造条件优化比较难。 4.3 精、速、密压铸 精、速、密压铸(双压射冲头)时采用一种由两个套在一起的外压射冲头。 在开始压射时,两个压射冲头同时前进;当充填完毕,型腔达到一定压力后,限 时开关启动,压射冲头继续前进,补充压实铸件。 这种方法的基本特征是: 1)浇口较厚,一般为 3~5mm; 2)充填速度较低,一般为 4~6m/s; 3)压铸后用压射冲头补充加压。此时比压是 3500KN~10000KN,压射冲头 的行程为 50~150mm。 4)控制铸件的凝固。 4.4 定向、抽气、加氧压铸 定向、抽气、加氧压铸实质上是一种真空压铸和加氧压铸相结合的工艺。工 艺过程是,在液体金属充填型腔之前,先将气体沿液态金属填充的方向以超过充 填的速度抽空,使金属液顺利地充填;对有深凹或死角的复杂铸件,在抽气的同 1 时进行加氧,以达到更好的效果。 4.5 半固态压铸 半固态压铸是当液态金属在凝固时,进行强烈的搅拌,并在一定的冷却速率 下获得约 50%甚至更高的固体组分的浆料,用这种浆料进行压铸。 半固态压铸与全液态金属压铸相比有如下优点: 1)由于降低了浇注温度,而且半固态金属在搅拌时已有 50%的融化潜热散 失掉,所以大大减少了对压室、压铸型腔和压铸机组成部件的热冲击,因而可以 提高压铸模面得使用寿命。 2)由于半固态金属粘度比全液态金属大,浇口处流速较低,因而充填时少 喷溅,无湍流,卷入的空气少;由于半固态收缩小,所以铸件不易出现疏松、缩 孔,故提高了铸件质量。 5.典型压铸零件举例 压铸是进的金属成型方法之一,是实现少切屑,无切屑的有效途径,应 用很广,发展很快。目前压铸广泛用于有色金属如锌、铝、镁和铜等合金。压铸 制品主要有车辆零部件,以齿轮盖及箱盖为主,还有各种电子产品。下面介绍几 种典型的压铸零件,如图 5-1 所示。 机车配件 方向盘 齿轮箱盖体 图 5.1 典型压铸零件 电子产品 1 参考文献 [1] 樊自田.先进材料成形技术与理论.化学工业,2006 [2] 徐光,常庆明等.现代材料成形技术.化学工业,2007 1
以上信息由江苏亚立特钢有限公司整理编辑,了解更多离心铸造信息请访问http://www.jsyltg.com